Introduction to PCB Tolerances
Printed Circuit Boards (PCBs) are essential components in modern electronic devices. They provide a platform for mounting and interconnecting electronic components, enabling the creation of complex circuits. However, the manufacturing process of PCBs is subject to various tolerances that can affect the performance and reliability of the final product. In this article, we will focus on two critical aspects of PCB tolerances: track width and isolation gap tolerances.
What are PCB Tolerances?
PCB tolerances refer to the acceptable variations in the dimensions and properties of a PCB during the manufacturing process. These tolerances are necessary because it is impossible to manufacture a PCB with perfect precision. Tolerances are specified by the PCB designer and must be adhered to by the manufacturer to ensure the proper functioning of the circuit.
Why are PCB Tolerances Important?
PCB tolerances play a crucial role in determining the performance, reliability, and manufacturability of a PCB. If the tolerances are too tight, it can lead to increased manufacturing costs and lower yields. On the other hand, if the tolerances are too loose, it can result in poor electrical performance, signal integrity issues, and even short circuits.
Track Width Tolerances
Track width refers to the width of the copper traces on a PCB. It is a critical parameter that affects the electrical characteristics of the circuit, such as resistance, inductance, and current-carrying capacity.
Factors Affecting Track Width Tolerances
Several factors can influence the track width tolerances on a PCB:
- Manufacturing Process: The type of manufacturing process used, such as etching or plating, can affect the achievable track width tolerances.
- PCB Material: The choice of PCB material, such as FR-4 or high-frequency laminates, can impact the track width tolerances due to differences in thermal expansion and mechanical properties.
- Copper Thickness: The thickness of the copper layer on the PCB can affect the track width tolerances, as thicker copper allows for wider tolerances.
- PCB Complexity: The complexity of the PCB design, including the number of layers and the density of components, can influence the achievable track width tolerances.
Calculating Track Width Tolerances
Track width tolerances are typically specified as a percentage of the nominal track width. For example, a track with a nominal width of 0.2 mm and a tolerance of ±10% would have an acceptable range of 0.18 mm to 0.22 mm.
The following table provides a general guideline for track width tolerances based on the nominal track width:
Nominal Track Width (mm) | Tolerance (±%) |
---|---|
0.1 – 0.2 | 20% |
0.2 – 0.5 | 15% |
0.5 – 1.0 | 10% |
1.0 – 2.0 | 5% |
> 2.0 | 3% |
It is important to note that these values are just a rough guideline, and the actual tolerances achievable may vary depending on the specific manufacturing process and PCB requirements.
Isolation Gap Tolerances
Isolation gaps, also known as clearances, refer to the minimum distance between two adjacent copper features on a PCB. They are essential for preventing short circuits and ensuring proper electrical isolation between different signals.
Factors Affecting Isolation Gap Tolerances
Several factors can influence the isolation gap tolerances on a PCB:
- Manufacturing Process: The capabilities of the manufacturing process, such as the minimum achievable feature size, can affect the isolation gap tolerances.
- PCB Material: The dielectric properties of the PCB material can impact the isolation gap tolerances, as materials with higher dielectric constants require larger isolation gaps.
- Voltage Requirements: The voltage levels of the signals on the PCB can dictate the minimum required isolation gaps to prevent electrical breakdown.
- Environmental Factors: The operating environment of the PCB, such as temperature and humidity, can affect the isolation gap tolerances due to changes in the dielectric properties of the PCB material.
Calculating Isolation Gap Tolerances
Isolation gap tolerances are typically specified as a minimum distance between copper features. The required isolation gap depends on various factors, including the PCB material, the voltage levels of the signals, and the applicable industry standards.
The following table provides a general guideline for minimum isolation gaps based on the voltage level:
Voltage Level (V) | Minimum Isolation Gap (mm) |
---|---|
< 50 | 0.1 |
50 – 100 | 0.2 |
100 – 150 | 0.3 |
150 – 300 | 0.5 |
> 300 | 1.0 |
It is important to consult the relevant industry standards, such as IPC-2221, for specific isolation gap requirements based on the PCB application and voltage levels.
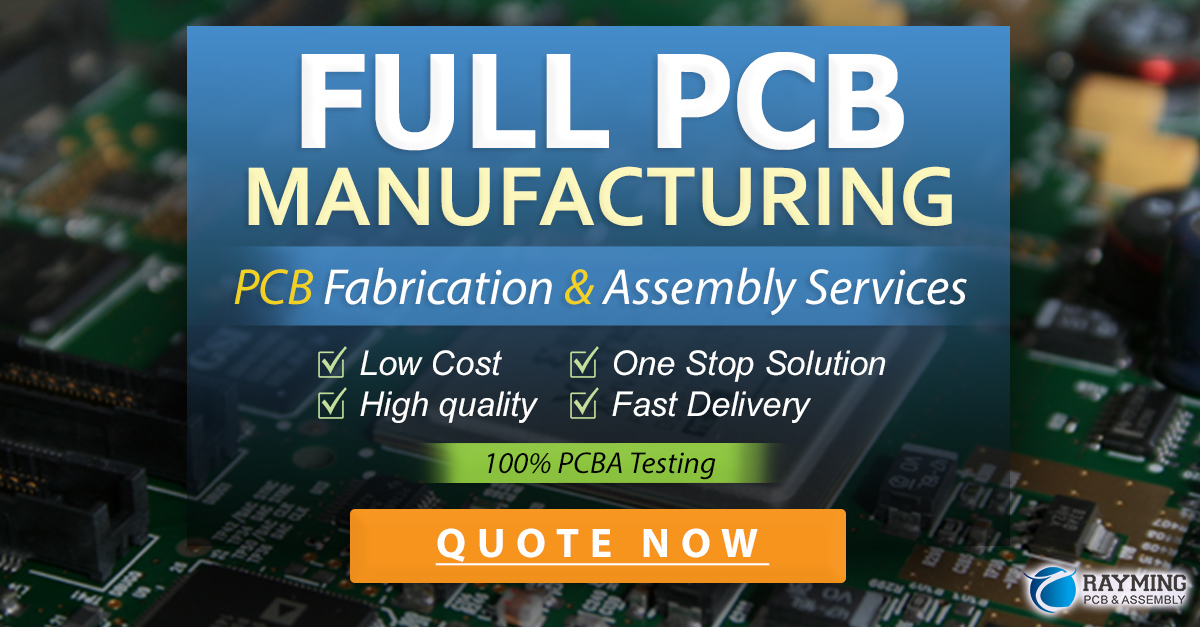
Design Considerations for PCB Tolerances
When designing a PCB, it is crucial to consider the manufacturing tolerances to ensure the manufacturability and reliability of the final product. Here are some design considerations related to track width and isolation gap tolerances:
- Design for Manufacturability: Choose track widths and isolation gaps that are within the capabilities of the intended manufacturing process. Consult with the PCB manufacturer to understand their specific tolerances and design rules.
- Use Appropriate Trace Widths: Select trace widths that are appropriate for the current-carrying requirements of the circuit. Wider traces can handle higher currents but may increase the overall PCB size and cost.
- Provide Adequate Clearances: Ensure that the isolation gaps between copper features are sufficient to prevent short circuits and maintain signal integrity. Consider the voltage levels and the PCB material when determining the required clearances.
- Utilize Design Rule Checks (DRC): Use DRC tools in your PCB design software to verify that your design meets the specified tolerances and design rules. DRC helps identify potential issues before sending the design for manufacturing.
- Communicate with the Manufacturer: Clearly communicate your tolerance requirements to the PCB manufacturer. Provide detailed documentation, including drawings and specifications, to ensure that the manufacturer understands and adheres to your requirements.
Frequently Asked Questions (FAQ)
-
What happens if the track width tolerances are not met during PCB manufacturing?
If the track width tolerances are not met, it can lead to various issues, such as increased resistance, current crowding, and potential open circuits. This can affect the electrical performance and reliability of the PCB. -
Can I use tighter tolerances to improve the performance of my PCB?
While using tighter tolerances can potentially improve the performance of your PCB, it also increases the manufacturing cost and complexity. It is important to strike a balance between performance requirements and manufacturability. Consult with your PCB manufacturer to determine the optimal tolerances for your specific application. -
What are the consequences of insufficient isolation gaps on a PCB?
Insufficient isolation gaps can lead to short circuits between adjacent copper features, causing electrical failures and potentially damaging the connected components. It can also compromise the signal integrity and electromagnetic compatibility (EMC) of the PCB. -
How can I ensure that my PCB design meets the required tolerances?
To ensure that your PCB design meets the required tolerances, follow these steps: - Familiarize yourself with the capabilities and limitations of the intended manufacturing process.
- Use appropriate design tools and techniques, such as Design Rule Checks (DRC), to verify your design against the specified tolerances.
- Clearly communicate your tolerance requirements to the PCB manufacturer and provide detailed documentation.
-
Work closely with the manufacturer throughout the design and fabrication process to address any issues or concerns.
-
Are there any industry standards that govern PCB tolerances?
Yes, there are several industry standards that provide guidelines and requirements for PCB tolerances. Some of the commonly used standards include: - IPC-2221: Generic Standard on Printed Board Design
- IPC-6012: Qualification and Performance Specification for Rigid Printed Boards
- IPC-A-600: Acceptability of Printed Boards
- IPC-A-610: Acceptability of Electronic Assemblies
It is important to refer to the relevant standards based on your specific PCB application and industry requirements.
Conclusion
Understanding and properly specifying manufacturing tolerances is crucial for ensuring the performance, reliability, and manufacturability of PCBs. Track width and isolation gap tolerances are two key aspects that designers must consider when creating PCB layouts.
By taking into account factors such as manufacturing processes, PCB materials, voltage requirements, and industry standards, designers can make informed decisions about the appropriate tolerances for their PCB designs. Effective communication with PCB manufacturers and the use of design tools and techniques, such as DRC, can help ensure that the final product meets the required tolerances.
By following best practices and considering the design considerations outlined in this article, PCB designers can create robust and manufacturable designs that meet the demands of modern electronic applications.
Leave a Reply