Understanding PCB Tolerances and Their Importance
Printed Circuit Boards (PCBs) are the backbone of modern electronic devices, providing a platform for components to be mounted and interconnected. The performance and reliability of these devices heavily depend on the precision and accuracy of the PCB manufacturing process. This is where PCB tolerances come into play, as they define the acceptable variations in dimensions, materials, and processes during the fabrication of PCBs.
What are PCB Tolerances?
PCB tolerances refer to the acceptable range of variations in the physical and electrical properties of a printed circuit board. These tolerances are specified by designers and manufacturers to ensure that the PCB functions as intended, fits properly within the device enclosure, and meets the required quality standards.
Tolerances are applied to various aspects of a PCB, including:
- Board dimensions (length, width, thickness)
- Hole sizes and positions
- Conductor widths and spacing
- Solder mask and silkscreen registration
- Electrical properties (impedance, capacitance, resistance)
Why are PCB Tolerances Important?
Adhering to PCB tolerances is crucial for several reasons:
-
Functionality: Precise tolerances ensure that components fit correctly and the PCB functions as designed. Deviations beyond the specified tolerances can lead to issues such as signal integrity problems, electromagnetic interference, or mechanical failures.
-
Manufacturability: PCB manufacturers rely on tolerances to produce boards consistently and efficiently. Well-defined tolerances help optimize the production process, reduce defects, and improve yield rates.
-
Compatibility: Tolerances guarantee that the PCB is compatible with the components it hosts and the device it is intended for. Proper tolerances allow for smooth assembly and prevent issues like component misalignment or poor fit within the enclosure.
-
Reliability: Maintaining tight tolerances contributes to the overall reliability of the electronic device. Boards that meet the specified tolerances are less likely to experience failures or performance degradation over time.
-
Cost-effectiveness: Specifying appropriate tolerances helps strike a balance between quality and cost. Overly stringent tolerances can increase manufacturing costs, while loose tolerances may lead to subpar performance or higher rejection rates.
Types of PCB Tolerances
PCB tolerances can be categorized into several types based on the specific aspect of the board they control. Let’s explore some of the most common types of tolerances encountered in PCB design and manufacturing.
Dimensional Tolerances
Dimensional tolerances govern the physical dimensions of the PCB, including its length, width, and thickness. These tolerances are typically expressed as a plus/minus deviation from the nominal value. For example, a board dimension might be specified as 100mm ± 0.2mm, meaning the acceptable range is between 99.8mm and 100.2mm.
The specific dimensional tolerances required depend on factors such as:
- The size and complexity of the PCB
- The components to be mounted on the board
- The assembly process (e.g., through-hole, surface mount)
- The device enclosure and mechanical constraints
Tighter dimensional tolerances are often necessary for high-density designs or boards with strict mechanical requirements. However, achieving tighter tolerances may increase manufacturing costs and lead times.
Hole Size and Position Tolerances
Holes on a PCB serve various purposes, including accommodating through-hole components, providing mounting points, or enabling interconnections between layers. Tolerances for hole sizes and positions ensure that components fit properly and align correctly with the corresponding pads.
Hole size tolerances define the acceptable range for the diameter of drilled holes. They account for variations in the drilling process and the plating thickness applied to the hole walls. Common hole size tolerances range from ±0.05mm to ±0.1mm, depending on the hole diameter and the specific manufacturing capabilities.
Position tolerances, on the other hand, control the allowable deviation in the location of the holes relative to their intended coordinates. Precise positioning is critical for component alignment and board-to-board interconnections. Position tolerances are typically tighter than hole size tolerances, often in the range of ±0.05mm to ±0.1mm.
Hole Diameter | Size Tolerance | Position Tolerance |
---|---|---|
0.5mm – 1.0mm | ±0.05mm | ±0.05mm |
1.0mm – 2.0mm | ±0.08mm | ±0.08mm |
2.0mm – 5.0mm | ±0.10mm | ±0.10mm |
Table 1: Example hole size and position tolerances
Conductor Width and Spacing Tolerances
Conductor width and spacing tolerances are crucial for maintaining the electrical integrity of the PCB. These tolerances control the minimum and maximum allowable widths of copper traces and the spacing between them.
Conductor width tolerances ensure that traces have the appropriate cross-sectional area to carry the required current without excessive resistance or heat generation. The specific width tolerances depend on the desired trace impedance, current carrying capacity, and the manufacturing process capabilities. Common conductor width tolerances range from ±0.05mm to ±0.1mm.
Spacing tolerances, also known as clearance or isolation tolerances, define the minimum distance between adjacent conductors to prevent short circuits or signal crosstalk. The spacing requirements vary based on factors such as the operating voltage, signal frequency, and the PCB material. Typical spacing tolerances range from ±0.05mm to ±0.1mm.
Copper Thickness | Conductor Width Tolerance | Spacing Tolerance |
---|---|---|
18μm (0.5 oz/ft²) | ±0.05mm | ±0.05mm |
35μm (1.0 oz/ft²) | ±0.08mm | ±0.08mm |
70μm (2.0 oz/ft²) | ±0.10mm | ±0.10mm |
Table 2: Example conductor width and spacing tolerances
Solder Mask and Silkscreen Tolerances
Solder mask and silkscreen are two important layers on a PCB that serve distinct purposes. Solder mask is a protective coating applied over the copper traces, leaving only the exposed pads for component soldering. Silkscreen, on the other hand, is a printed layer that provides text, symbols, and markings for component identification and assembly guidance.
Tolerances for solder mask and silkscreen ensure proper registration and alignment with the underlying copper features. Solder mask tolerances control the allowable deviation in the size and position of the solder mask openings relative to the pads. Typical solder mask tolerances range from ±0.05mm to ±0.1mm, depending on the pad size and spacing.
Silkscreen tolerances define the acceptable registration and clarity of the printed markings. They ensure that the silkscreen aligns correctly with the components and does not overlap with the solder mask openings. Common silkscreen tolerances range from ±0.1mm to ±0.2mm.
Feature | Tolerance |
---|---|
Solder Mask Opening | ±0.05mm |
Silkscreen Registration | ±0.1mm |
Silkscreen Line Width | ±0.1mm |
Table 3: Example solder mask and silkscreen tolerances
Electrical Tolerances
In addition to physical dimensions, PCBs also have electrical tolerances that govern the allowable variations in electrical properties. These tolerances are critical for ensuring signal integrity, controlling impedance, and maintaining the overall performance of the circuit.
Some common electrical tolerances include:
-
Impedance Tolerance: Specifies the allowable deviation in the characteristic impedance of controlled impedance traces. Typical impedance tolerances range from ±5% to ±10%.
-
Capacitance Tolerance: Controls the acceptable variation in the capacitance of embedded capacitors or the parasitic capacitance between traces. Capacitance tolerances are usually expressed as a percentage, such as ±10% or ±20%.
-
Resistance Tolerance: Defines the allowable range for the resistance of copper traces or embedded resistors. Resistance tolerances are typically specified as a percentage, such as ±5% or ±10%.
Electrical tolerances are achieved through careful control of the PCB material properties, trace geometries, and manufacturing processes. Meeting these tolerances often requires specialized materials, precise fabrication techniques, and rigorous testing and measurement procedures.
Factors Affecting PCB Tolerances
Several factors influence the achievable tolerances in PCB manufacturing. Understanding these factors helps designers and manufacturers set realistic expectations and make informed decisions during the design and production phases.
Manufacturing Process Capabilities
The capabilities of the PCB manufacturing process play a significant role in determining the achievable tolerances. Different fabrication techniques, such as etching, drilling, plating, and lamination, have their own inherent limitations and variability.
For example, the minimum feature size and spacing that can be reliably produced depend on the resolution and accuracy of the imaging and etching processes. Similarly, the hole size and position tolerances are influenced by the precision of the drilling equipment and the stability of the drill bits.
Manufacturers invest in advanced equipment, process control systems, and skilled personnel to push the boundaries of their capabilities and offer tighter tolerances. However, it’s important to recognize that achieving extremely tight tolerances may require specialized processes or materials, which can increase costs and lead times.
Material Selection
The choice of PCB materials also affects the achievable tolerances. Different substrate materials, such as FR-4, high-frequency laminates, or flexible substrates, have varying dimensional stability, thermal expansion coefficients, and electrical properties.
For instance, some high-performance materials may offer better dimensional stability and tighter tolerances compared to standard FR-4. However, these materials often come at a higher cost and may require specific processing conditions.
The copper foil thickness used for the conductive layers also influences the tolerances. Thinner copper foils allow for finer trace widths and spacings but may be more susceptible to variations in etching and plating processes.
Design Complexity
The complexity of the PCB design itself can impact the achievable tolerances. Boards with high component density, fine-pitch devices, or complex routing patterns may require tighter tolerances to ensure proper assembly and functionality.
Designers need to consider factors such as trace widths, spacings, pad sizes, and hole diameters when defining the tolerances for a specific design. Striking a balance between design requirements and manufacturing feasibility is crucial to avoid unnecessary costs or production issues.
Environmental Factors
Environmental factors, such as temperature and humidity, can affect the dimensional stability of PCBs during manufacturing and operation. Changes in temperature can cause the board material to expand or contract, leading to variations in dimensions and feature positions.
To mitigate the impact of environmental factors, designers need to consider the operating conditions of the device and specify appropriate tolerances. Using materials with low thermal expansion coefficients or incorporating design techniques like symmetric layup and balanced copper distribution can help reduce the sensitivity to environmental changes.
Quality Control and Inspection
Maintaining tight tolerances requires robust quality control and inspection processes throughout the PCB manufacturing flow. Manufacturers employ various techniques, such as automated optical inspection (AOI), X-ray inspection, and electrical testing, to verify that the boards meet the specified tolerances.
Implementing statistical process control (SPC) methods helps monitor and control the manufacturing processes, identifying trends or deviations early on. Regular calibration and maintenance of equipment, along with operator training, contribute to achieving consistent and reliable results.
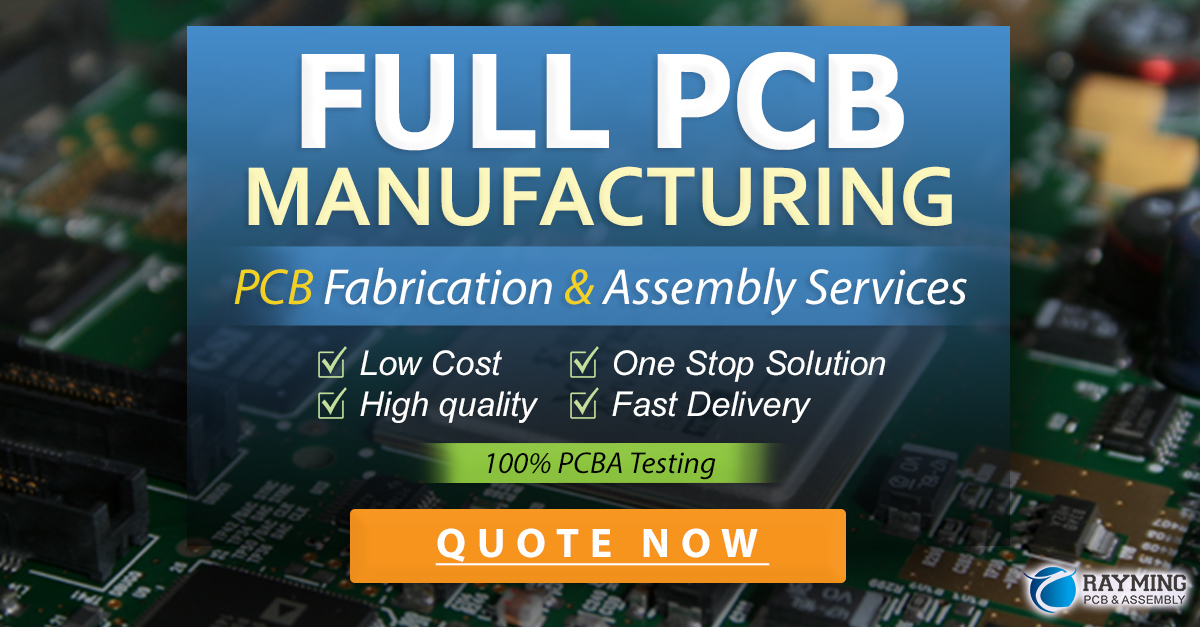
Specifying and Communicating PCB Tolerances
Clearly specifying and communicating PCB tolerances is essential for ensuring a smooth and successful manufacturing process. Designers and manufacturers need to work together to establish realistic and achievable tolerances based on the specific requirements of the project.
Tolerance Stackup Analysis
Tolerance stackup analysis is a method used to assess the cumulative effect of individual tolerances on the overall dimensions and performance of the PCB. It involves considering the worst-case scenario where all tolerances are at their extreme limits and evaluating the impact on the final assembly.
Designers perform tolerance stackup analysis to identify potential issues, such as component misalignment, insufficient clearances, or excessive variations in electrical properties. By understanding the tolerance stackup, designers can make informed decisions on specifying appropriate tolerances and adjust the design if necessary.
Tolerance Callouts on Drawings
PCB design files and fabrication drawings should clearly specify the required tolerances for each critical dimension or feature. Tolerance callouts typically include the nominal value, the plus/minus deviation, and any applicable standards or references.
For example, a hole diameter tolerance might be specified as:
Hole Diameter: 1.00mm ±0.05mm
Reference: IPC-6012 Class 2
Including clear and unambiguous tolerance callouts helps communicate the requirements to the manufacturer and reduces the risk of misinterpretation or errors.
Communication and Collaboration
Effective communication and collaboration between the design team and the PCB manufacturer are vital for successfully managing tolerances. Designers should engage with the manufacturer early in the design process to discuss the feasibility of the proposed tolerances and identify any potential challenges or limitations.
Manufacturers can provide valuable insights and recommendations based on their experience and capabilities. They can suggest alternative materials, processes, or design modifications to achieve the desired tolerances more efficiently or cost-effectively.
Regular communication throughout the manufacturing process, including design reviews, prototyping, and production runs, helps ensure that the tolerances are consistently met and any issues are promptly addressed.
Frequently Asked Questions (FAQ)
-
What happens if the PCB tolerances are not met?
If the PCB tolerances are not met, it can lead to various problems, such as component misalignment, poor solderability, signal integrity issues, or even complete failure of the device. Non-conforming boards may need to be reworked or scrapped, resulting in additional costs and delays. -
How can I ensure that my PCB design is within the manufacturer’s capabilities?
To ensure that your PCB design is within the manufacturer’s capabilities, it’s important to communicate with them early in the design process. Share your design files, discuss your requirements, and seek their feedback on the feasibility of your tolerances. Refer to the manufacturer’s design guidelines and capabilities document to align your design with their processes. -
Can I achieve tighter tolerances than the industry standards?
In some cases, it may be possible to achieve tighter tolerances than the industry standards, but it often comes at a higher cost and may require specialized manufacturing processes or materials. It’s important to discuss your specific requirements with the PCB manufacturer and evaluate the trade-offs between tolerance, cost, and lead time. -
How do I specify tolerances for complex or non-standard features?
For complex or non-standard features, it’s best to provide detailed drawings or 3D models that clearly define the geometry and dimensions. Include tolerance callouts for critical dimensions and engage with the manufacturer to discuss the feasibility and any specific requirements. In some cases, you may need to provide additional information, such as cross-sectional views or assembly instructions. -
What are the common industry standards for PCB tolerances?
There are several industry standards that provide guidelines for PCB tolerances, such as IPC (Association Connecting Electronics Industries) standards. Some commonly referenced standards include: - IPC-6012: Qualification and Performance Specification for Rigid Printed Boards
- IPC-6013: Qualification and Performance Specification for Flexible Printed Boards
- IPC-2221: Generic Standard on Printed Board Design
These standards define different classes of tolerances based on the intended application and the level of quality required. Manufacturers often specify their capabilities in terms of these industry standards.
Conclusion
PCB tolerances play a crucial role in ensuring the functionality, reliability, and manufacturability of electronic devices. Understanding the types of tolerances, the factors affecting them, and the importance of clear specification and communication is essential for designers and manufacturers alike.
By setting realistic tolerances, performing thorough analysis, and collaborating closely with manufacturing partners, designers can optimize their PCB designs for successful production and performance. Investing in advanced manufacturing processes, quality control systems, and skilled personnel enables manufacturers to meet tight tolerances consistently and efficiently.
As technology advances and device complexity increases, the need for precise and well-managed PCB tolerances becomes even more critical. By staying informed about industry standards, best practices, and emerging technologies, designers and manufacturers can navigate the challenges and opportunities presented by PCB tolerances in the ever-evolving world of electronics.
Leave a Reply