Introduction to PCB Manufacture
Printed Circuit Boards (PCBs) are the backbone of modern electronic devices. They provide a platform for electronic components to be mounted and interconnected, enabling the creation of complex circuits in a compact and efficient manner. PCB manufacture is a multi-step process that involves various techniques and technologies to transform a circuit design into a physical board. In this article, we will explore the PCB manufacture process step-by-step, from design to final assembly.
PCB Design and Preparation
Circuit Design and Schematic Creation
The first step in PCB manufacture is to create a circuit design and schematic. This involves defining the electronic components, their connections, and the overall circuit functionality. Engineers use specialized software tools, such as Electronic Design Automation (EDA) software, to create the schematic diagram. The schematic captures the logical connections between components and serves as a blueprint for the PCB layout.
PCB Layout and Routing
Once the schematic is complete, the next step is to create the PCB layout. The layout determines the physical placement of components on the board and the routing of the copper traces that connect them. PCB designers use layout software to arrange the components and route the traces while adhering to design rules and constraints. The layout must consider factors such as signal integrity, electromagnetic compatibility (EMC), and manufacturing limitations.
Design Rule Check (DRC) and Gerber File Generation
After the PCB layout is finalized, it undergoes a Design Rule Check (DRC) to ensure that it meets the manufacturing requirements and design rules. The DRC verifies aspects such as minimum trace widths, clearances, and hole sizes. Once the design passes the DRC, Gerber files are generated. Gerber files are industry-standard files that contain the necessary information for PCB manufacturing, including the copper layers, solder mask, silkscreen, and drill data.
PCB Fabrication Process
PCB Material Selection
The choice of PCB material depends on the specific requirements of the application, such as electrical properties, thermal characteristics, and mechanical strength. Common PCB materials include FR-4, which is a glass-reinforced epoxy laminate, and high-frequency materials like Rogers or Teflon for RF applications. The thickness of the PCB and the number of layers are also determined based on the design requirements.
Copper Clad Laminate Preparation
The PCB fabrication process begins with the preparation of the copper clad laminate. The laminate consists of a dielectric substrate, typically FR-4, with a thin layer of copper foil bonded to one or both sides. The copper foil thickness can vary depending on the desired current carrying capacity and signal integrity requirements. The laminate is cut to the desired size and cleaned to remove any contaminants.
Drilling and Hole Plating
Holes are drilled into the PCB laminate to accommodate through-hole components and provide interconnections between layers. The drilling process is performed using high-speed CNC drilling machines equipped with small diameter drill bits. After drilling, the holes are plated with copper to create electrical connections between the layers. This is done through a process called electroless copper plating, followed by electrolytic copper plating to achieve the desired thickness.
Patterning and Etching
The next step is to transfer the PCB layout pattern onto the copper surface. This is typically done using a photolithography process. A photoresist layer is applied to the copper surface and exposed to UV light through a photomask that contains the PCB pattern. The exposed areas of the photoresist become soluble and are removed during development, leaving the desired copper pattern protected.
The unprotected copper areas are then etched away using a chemical etching process, typically with an acidic solution like ferric chloride or cupric chloride. The etching process removes the unwanted copper, leaving only the desired copper traces and pads. After etching, the remaining photoresist is stripped away, revealing the final copper pattern.
Solder Mask Application
A solder mask is applied to the PCB to protect the copper traces and prevent solder bridging during the assembly process. The solder mask is a thin layer of polymer that covers the copper, leaving only the exposed pads and areas where components will be soldered. The solder mask is typically green in color but can be available in other colors for specific applications. The solder mask is applied using a screen printing or photoimaging process and then cured to achieve the desired properties.
Silkscreen Printing
Silkscreen printing is used to add text, labels, and logos to the PCB surface. The silkscreen is a layer of ink that is applied on top of the solder mask using a screen printing process. The silkscreen provides visual information for component placement, orientation, and identification. It is typically white in color but can be available in other colors as well.
Surface Finish Application
The exposed copper pads on the PCB require a surface finish to protect them from oxidation and enhance solderability. There are various surface finish options available, each with its own advantages and disadvantages. Some common surface finishes include:
- Hot Air Solder Leveling (HASL): A tin-lead alloy is applied to the pads and then leveled using hot air to create a flat surface.
- Electroless Nickel Immersion Gold (ENIG): A layer of nickel is deposited on the copper, followed by a thin layer of gold. ENIG provides excellent solderability and flatness.
- Immersion Silver (IAg): A thin layer of silver is deposited on the copper pads, providing good solderability and cost-effectiveness.
- Organic Solderability Preservative (OSP): A thin organic coating is applied to the copper pads to prevent oxidation and enhance solderability.
The choice of surface finish depends on factors such as the intended application, soldering process, and cost considerations.
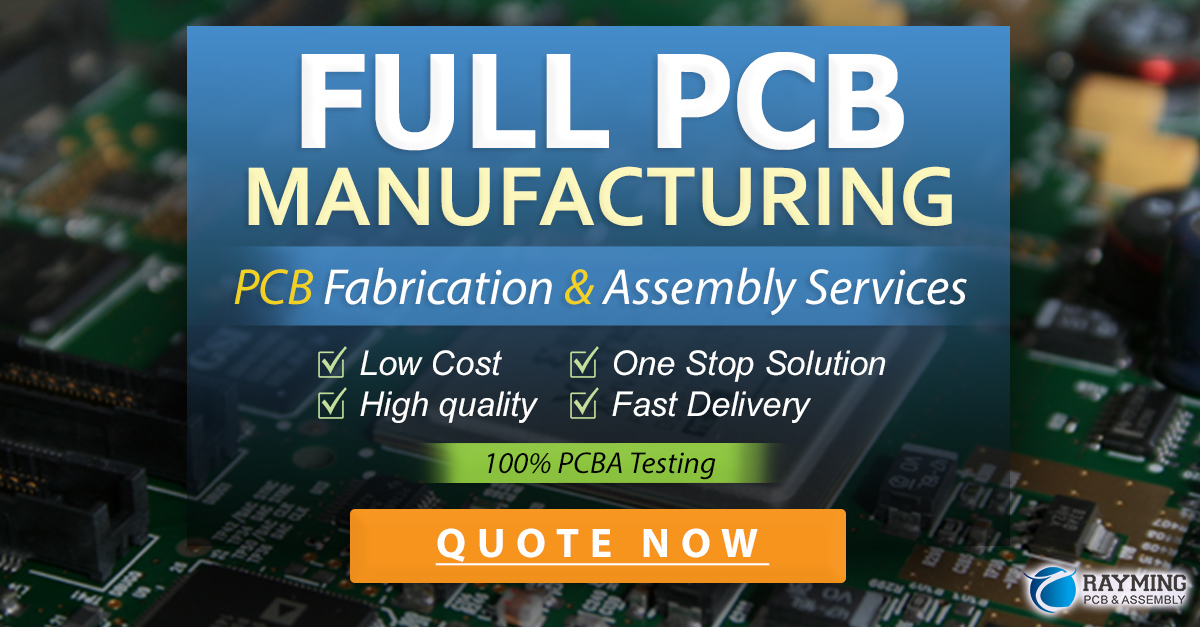
PCB Assembly
Component Placement
Once the PCB fabrication is complete, the next step is to assemble the electronic components onto the board. The component placement process involves placing the components on the designated pads and locations as per the PCB layout. This can be done manually for low-volume production or using automated pick-and-place machines for high-volume manufacturing. The components are typically supplied in reels or trays and are picked up by the machine’s nozzle, aligned, and placed on the PCB with high precision.
Soldering
After component placement, the PCB undergoes the soldering process to establish electrical connections between the components and the PCB pads. There are two main soldering techniques used in PCB assembly:
-
Through-Hole Soldering: For through-hole components, the leads are inserted into the drilled holes, and the soldering is done on the opposite side of the board. This can be done manually using a soldering iron or using a wave soldering machine for automated soldering.
-
Surface Mount Soldering: Surface mount components are soldered directly onto the pads on the PCB surface. The soldering is typically done using a reflow soldering process, where solder paste is applied to the pads, and the components are placed on top. The PCB then goes through a reflow oven, where the solder paste melts and forms a reliable electrical and mechanical connection.
Inspection and Testing
After soldering, the assembled PCBs undergo thorough inspection and testing to ensure quality and functionality. Visual inspection is performed to check for any soldering defects, component placement accuracy, and overall PCB Quality. Automated optical inspection (AOI) systems can be used for high-volume production to detect any soldering or placement issues.
Electrical testing is also conducted to verify the functionality of the assembled PCB. This can include in-circuit testing (ICT), where the PCB is tested for short circuits, open circuits, and component functionality using a bed-of-nails test fixture. Functional testing is performed to validate the overall operation of the PCB in its intended application.
Conformal Coating and Potting
In some cases, additional protection measures are applied to the assembled PCB to enhance its durability and reliability. Conformal coating involves applying a thin layer of protective material, such as acrylic, silicone, or polyurethane, over the PCB surface. This coating protects the PCB from moisture, dust, and other environmental factors. Potting is another technique where the PCB is encapsulated in a resin or epoxy material to provide mechanical strength and environmental protection.
PCB Inspection and Quality Control
Throughout the PCB manufacture process, various inspection and quality control measures are implemented to ensure the highest quality and reliability of the final product. Some key inspection and quality control steps include:
- Incoming Material Inspection: The raw materials used in PCB fabrication, such as copper clad laminates and solder masks, are inspected for quality and conformance to specifications.
- In-Process Inspection: During the PCB fabrication process, intermittent inspections are performed to check for any defects or deviations from the desired specifications. This can include visual inspections, electrical testing, and dimensional measurements.
- Final Inspection: Before packaging and shipping, the assembled PCBs undergo a final inspection to ensure they meet all the required quality standards. This includes visual inspection, electrical testing, and functional testing as per the customer’s requirements.
- Quality Management Systems: PCB manufacturers often adhere to quality management systems such as ISO 9001 or IPC Standards to ensure consistent quality and continuous improvement in their processes.
Packaging and Shipping
After the PCBs have passed the final inspection, they are packaged and prepared for shipping. The packaging method depends on the quantity, size, and fragility of the PCBs. Anti-statIC Packaging materials are used to protect the PCBs from electrostatic discharge (ESD) damage during transportation. The packaged PCBs are then shipped to the customer or the next stage of the manufacturing process, such as final product assembly.
Frequently Asked Questions (FAQ)
-
What is the typical turnaround time for PCB manufacture?
The turnaround time for PCB manufacture varies depending on the complexity of the design, the quantity ordered, and the manufacturer’s capacity. Typically, simple PCBs can be manufactured within a few days, while complex designs or high-volume orders may take several weeks. -
What are the different types of PCBs based on the number of layers?
PCBs can be categorized based on the number of layers: - Single-sided PCBs: These have components and copper traces on only one side of the board.
- Double-sided PCBs: These have components and copper traces on both sides of the board.
-
Multi-layer PCBs: These have multiple layers of copper traces separated by insulating layers. Common multi-layer PCBs include 4-layer, 6-layer, 8-layer, and more.
-
What is the minimum feature size that can be achieved in PCB manufacture?
The minimum feature size in PCB manufacture depends on the capabilities of the manufacturer and the fabrication technology used. Typically, the minimum trace width and spacing that can be reliably manufactured is around 3-4 mils (0.003-0.004 inches or 0.075-0.1 mm). However, advanced manufacturing techniques can achieve even smaller feature sizes for high-density designs. -
What is the difference between through-hole and surface mount components?
Through-hole components have leads that are inserted into drilled holes in the PCB and soldered on the opposite side. Surface mount components, on the other hand, are soldered directly onto the pads on the PCB surface without requiring holes. Surface mount components are smaller and allow for higher component density compared to through-hole components. -
What are the advantages of using a solder mask on a PCB?
A solder mask offers several advantages in PCB manufacture: - It protects the copper traces from oxidation and prevents solder bridging during the assembly process.
- It provides insulation between adjacent traces and components, reducing the risk of short circuits.
- It improves the aesthetics of the PCB by covering the exposed copper and providing a uniform appearance.
- It aids in the soldering process by defining the solderable areas and preventing solder from spreading to undesired locations.
Conclusion
PCB manufacture is a complex process that involves multiple steps and technologies to transform a circuit design into a functional physical board. From design and fabrication to assembly and inspection, each step plays a crucial role in ensuring the quality, reliability, and performance of the final PCB. Understanding the PCB manufacture process enables designers, engineers, and project managers to make informed decisions, optimize designs, and collaborate effectively with PCB manufacturers. As technology advances and electronic devices become more sophisticated, the PCB manufacture industry continues to evolve, offering new materials, techniques, and capabilities to meet the ever-growing demands of the electronics industry.
Leave a Reply