Understanding Ferric Chloride
Ferric chloride (FeCl3) is an acidic salt commonly used in PCB Etching due to its ability to dissolve copper. When exposed to ferric chloride, the copper on the PCB surface that is not protected by a resist layer is chemically removed, creating the desired circuit pattern.
Chemical Reaction
The chemical reaction between ferric chloride and copper can be represented as follows:
2 FeCl3 + Cu → 2 FeCl2 + CuCl2
In this reaction, ferric chloride is reduced to ferrous chloride (FeCl2), while copper is oxidized to copper(II) chloride (CuCl2). This process continues until all the exposed copper is removed from the PCB surface.
Factors Affecting Etching Performance
Several factors can influence the performance of ferric chloride in the PCB etching process:
-
Concentration: A higher concentration of ferric chloride leads to faster etching rates. However, overly concentrated solutions can cause excessive etching and undercut the resist layer.
-
Temperature: Increasing the temperature of the ferric chloride solution accelerates the etching process. Typically, a temperature range of 30°C to 50°C is recommended for optimal results.
-
Agitation: Agitating the solution during etching helps to remove the dissolved copper and ensures a more uniform etch. This can be achieved through manual stirring, air bubbling, or using a magnetic stirrer.
-
Age and Contamination: As ferric chloride is used, it becomes saturated with dissolved copper, reducing its etching efficiency. Regularly replacing or regenerating the solution is necessary to maintain consistent results.
Preparing the PCB for Etching
Before etching your PCB with ferric chloride, it is essential to properly prepare the board to ensure the best possible results.
Cleaning the PCB
-
Remove any dirt, grease, or oxidation from the copper surface using a mild abrasive, such as fine steel wool or a green Scotch-Brite pad.
-
Clean the board with isopropyl alcohol or a dedicated PCB cleaner to remove any residue.
-
Ensure the board is completely dry before proceeding to the next step.
Applying the Resist
- Choose a suitable resist method, such as:
- Photoresist (positive or negative)
- Toner transfer (using a laser printer and glossy paper)
-
Permanent marker (for simple, low-resolution designs)
-
Apply the resist according to the chosen method, ensuring complete coverage of the areas you want to protect from etching.
-
Inspect the resist for any defects, such as bubbles, scratches, or incomplete coverage. Make necessary repairs before etching.
Etching Process
Once your PCB is prepared with the resist, you can begin the etching process using ferric chloride.
Equipment and Safety
-
Use a non-reactive container, such as a glass or plastic tray, to hold the ferric chloride solution.
-
Wear appropriate personal protective equipment (PPE), including gloves, safety goggles, and an apron, to prevent skin contact and eye irritation.
-
Work in a well-ventilated area to minimize exposure to fumes.
Etching Steps
-
Heat the ferric chloride solution to the desired temperature (30°C to 50°C) using a water bath or a dedicated etching tank with temperature control.
-
Immerse the prepared PCB in the heated ferric chloride solution.
-
Agitate the solution gently to ensure even etching and remove dissolved copper. This can be done by manually rocking the container, using an air bubbler, or a magnetic stirrer.
-
Monitor the etching progress closely. The time required for complete etching depends on factors such as solution concentration, temperature, and copper thickness.
-
Remove the PCB from the solution once all the unwanted copper has been etched away. Rinse the board thoroughly with water to stop the etching process.
Post-Etching Cleaning
- Remove the resist layer using the appropriate method:
- For photoresist, use a dedicated resist stripper or a strong alkaline solution, such as sodium hydroxide (NaOH).
-
For toner transfer or permanent marker, use acetone or isopropyl alcohol.
-
Clean the PCB with water and dry it completely.
-
Inspect the etched PCB for any defects, such as over-etching, undercut, or incomplete etching. Make necessary corrections or repairs.
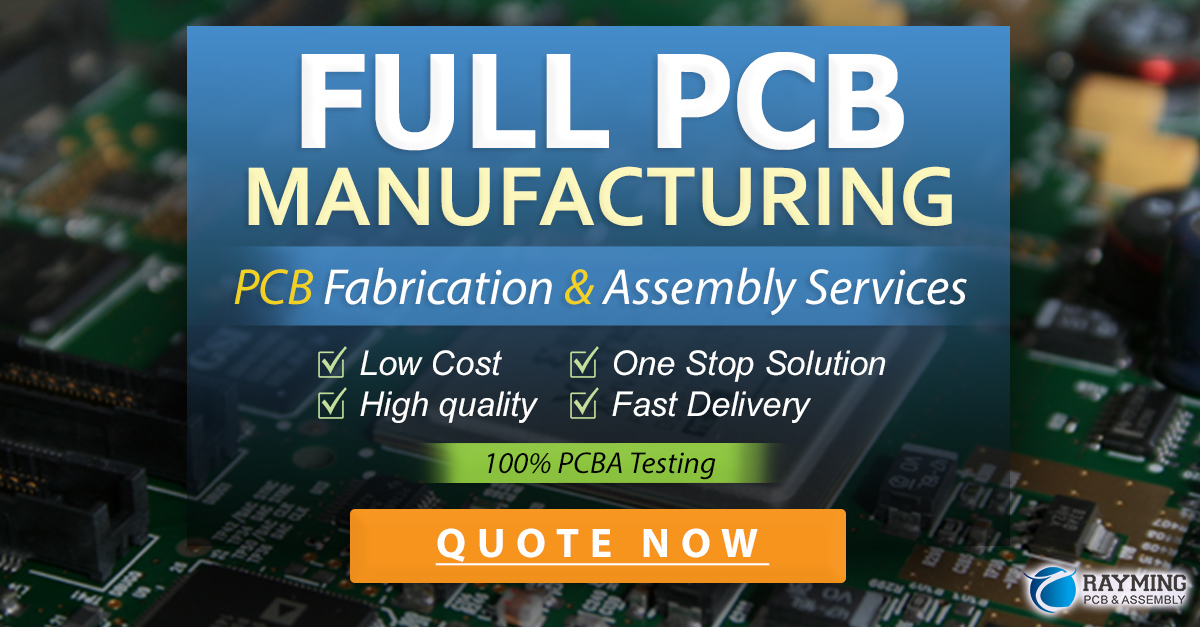
Optimizing the Etching Process
To achieve the best results and minimize issues during PCB etching with ferric chloride, consider the following tips:
Maintain Solution Quality
-
Regularly check the specific gravity of the ferric chloride solution using a hydrometer. A specific gravity of 1.35 to 1.45 is generally recommended for optimal etching performance.
-
Replace or regenerate the solution when it becomes saturated with copper and the etching rate slows down significantly.
-
Filter the solution periodically to remove any debris or resist particles that may contaminate the etchant.
Control Etching Parameters
-
Adjust the temperature, agitation, and duration of etching based on the specific requirements of your PCB design and the resist method used.
-
Monitor the etching progress closely to avoid over-etching, which can lead to unwanted undercuts and damage to fine features.
-
Use a test piece or a small sample PCB to determine the optimal etching parameters before processing the actual board.
Improve Resist Quality
-
Ensure the resist layer is applied evenly and without defects, such as bubbles, scratches, or incomplete coverage.
-
For photoresist, use high-quality, high-resolution transparency films and ensure proper exposure and development times.
-
For toner transfer, use a laser printer with high toner density and a glossy paper designed for PCB toner transfer.
Prevent Undercut
-
Minimize the time the PCB is exposed to the ferric chloride solution to reduce the risk of undercutting.
-
Use a double-sided resist or a tin-plating process to protect the edges of the copper traces from excessive etching.
-
Experiment with different resist methods and thicknesses to find the optimal balance between etch resistance and ease of application.
Troubleshooting Common Issues
Despite careful preparation and process control, issues may arise during PCB etching with ferric chloride. Here are some common problems and potential solutions:
Issue | Possible Causes | Solutions |
---|---|---|
Incomplete etching | – Low ferric chloride concentration – Insufficient etching time – Low temperature |
– Increase solution concentration – Extend etching time – Raise solution temperature |
Over-etching / undercut | – Excessive etching time – High ferric chloride concentration – Insufficient resist coverage |
– Reduce etching time – Dilute the solution – Improve resist application |
Resist lifting or damage | – Incompatible resist material – Improper resist application – Excessive agitation |
– Choose a suitable resist method – Ensure proper application techniques – Reduce agitation intensity |
Uneven etching | – Poor solution agitation – Non-uniform temperature – Uneven resist coverage |
– Improve agitation method – Ensure consistent temperature – Apply resist evenly |
Environmental and Safety Considerations
When working with ferric chloride for PCB etching, it is crucial to prioritize safety and minimize environmental impact.
Safe Handling and Storage
-
Always wear appropriate PPE, including gloves, safety goggles, and an apron, when handling ferric chloride.
-
Store ferric chloride in a cool, dry place, away from direct sunlight and incompatible materials, such as strong bases and oxidizing agents.
-
Keep ferric chloride containers tightly closed when not in use to prevent spills and minimize exposure to air and moisture.
Proper Disposal
-
Never pour used ferric chloride solution down the drain or dispose of it in regular trash.
-
Contact your local waste management authority for guidance on proper disposal methods for ferric chloride and copper-saturated solutions.
-
Some localities may require neutralization of the solution before disposal, using methods such as sodium hydroxide treatment or electrowinning to remove copper.
Ventilation and Spill Control
-
Always work with ferric chloride in a well-ventilated area to minimize exposure to fumes.
-
Keep a spill kit nearby, including absorbent materials (e.g., sand, vermiculite), a neutralizing agent (e.g., sodium carbonate), and a plastic scoop and container for clean-up.
-
In case of a spill, neutralize the ferric chloride with the neutralizing agent, absorb it with the absorbent material, and dispose of the waste according to local regulations.
FAQs
-
Q: Can I reuse ferric chloride solution?
A: Yes, ferric chloride solution can be reused multiple times until it becomes saturated with copper and loses its etching efficiency. To extend the life of the solution, you can regenerate it using methods like aeration, electrolysis, or chemical treatment. -
Q: How do I know when the ferric chloride solution is exhausted?
A: You can monitor the specific gravity of the solution using a hydrometer. When the specific gravity drops below 1.25, the solution is considered exhausted and should be replaced or regenerated. -
Q: Can I use ferric chloride for etching other metals besides copper?
A: Ferric chloride is primarily used for etching copper, but it can also be used to etch other metals, such as brass, nickel, and steel. However, the etching process may require different parameters and resist materials. -
Q: How can I speed up the etching process?
A: To speed up the etching process, you can increase the temperature of the ferric chloride solution (up to 50°C), use a more concentrated solution, or improve agitation. However, be cautious as these changes can also increase the risk of over-etching and undercutting. -
Q: Is ferric chloride etching environmentally friendly?
A: While ferric chloride is less hazardous compared to some other etching chemicals, it still poses environmental risks if not handled and disposed of properly. Always follow local regulations for safe disposal and consider alternative, more eco-friendly etching methods, such as citric acid or electrochemical etching, when possible.
By following these tips and techniques, you can optimize your PCB etching process using ferric chloride, achieving high-quality results and minimizing potential issues. Remember to prioritize safety, maintain solution quality, and control etching parameters for the best possible outcomes.
Leave a Reply