Understanding Soldering Flux
Before diving into the methods of Removing PCB Flux, it is crucial to understand what soldering flux is and why it is used.
What is Soldering Flux?
Soldering flux is a chemical cleaning agent that is applied to the surfaces of the components and PCB pads prior to soldering. It serves several purposes:
- Removes oxidation and contamination from the surfaces to be soldered
- Prevents re-oxidation during the soldering process
- Improves the wetting ability of the solder, allowing it to flow more easily and create a stronger bond
Types of Soldering Flux
There are three main types of soldering flux:
Flux Type | Composition | Residue | Cleaning |
---|---|---|---|
Rosin | Natural or synthetic resins | Non-corrosive, can be left on PCB | Optional |
Water-Soluble | Organic acids and bases | Corrosive, must be cleaned | Required |
No-Clean | Synthetic resins, low solid content | Minimal, non-corrosive | Optional |
Methods for Removing PCB Soldering Flux
There are several methods for removing PCB soldering flux, each with its own advantages and disadvantages. The choice of method depends on the type of flux used, the size and complexity of the PCB, and the available resources.
Manual Cleaning
Manual cleaning involves using a brush, swab, or wipe to apply a cleaning solution to the PCB and remove the flux residue. This method is suitable for small PCBs or localized cleaning.
Materials Needed
- Cleaning solution (isopropyl alcohol, flux remover, or other solvents)
- Brushes, swabs, or lint-free wipes
- Protective gloves and eyewear
Procedure
- Put on protective gloves and eyewear.
- Apply the cleaning solution to the brush, swab, or wipe.
- Gently scrub the affected areas of the PCB, focusing on the solder joints and surrounding areas.
- Repeat the process until all visible flux residue is removed.
- Allow the PCB to dry completely before further handling or use.
Ultrasonic Cleaning
Ultrasonic cleaning uses high-frequency sound waves to agitate a cleaning solution, creating tiny bubbles that implode and release energy, effectively removing flux residue from the PCB. This method is suitable for larger PCBs or batch cleaning.
Materials Needed
- Ultrasonic cleaner
- Cleaning solution (water-based or solvent-based, depending on flux type)
- Protective gloves and eyewear
Procedure
- Fill the ultrasonic cleaner with the appropriate cleaning solution.
- Place the PCB into the cleaner, ensuring it is fully submerged.
- Set the cleaner to the recommended temperature and time settings for your specific flux type and PCB size.
- Start the cleaning cycle and wait for it to complete.
- Remove the PCB from the cleaner and rinse it with deionized water.
- Allow the PCB to dry completely before further handling or use.
Spray Cleaning
Spray cleaning involves using a pressurized spray of cleaning solution to remove flux residue from the PCB. This method is suitable for larger PCBs or hard-to-reach areas.
Materials Needed
- Pressurized spray cleaner (aerosol or pump-based)
- Cleaning solution (flux remover or other solvents)
- Protective gloves, eyewear, and respiratory protection
Procedure
- Put on protective gloves, eyewear, and respiratory protection.
- Place the PCB in a well-ventilated area, preferably with a fume extractor.
- Shake the pressurized spray cleaner well before use.
- Hold the spray nozzle 15-20 cm away from the PCB and apply the cleaning solution in a sweeping motion, covering all affected areas.
- Allow the cleaning solution to penetrate and dissolve the flux residue for the recommended time.
- Rinse the PCB with deionized water or use a clean, lint-free wipe to remove any remaining residue.
- Allow the PCB to dry completely before further handling or use.
Vapor Degreasing
Vapor degreasing is a highly effective method for removing PCB flux residue, using a closed-loop system with a boiling solvent. The PCB is exposed to the solvent vapors, which condense on the board and dissolve the flux residue.
Materials Needed
- Vapor degreaser
- Solvent (e.g., perchloroethylene, trichloroethylene, or methylene chloride)
- Protective gloves and eyewear
Procedure
- Fill the vapor degreaser with the appropriate solvent.
- Heat the solvent to its boiling point, creating a vapor zone above the liquid.
- Place the PCB into the vapor zone, allowing the solvent vapors to condense on the board and dissolve the flux residue.
- Remove the PCB from the vapor zone and allow it to drain and cool.
- Rinse the PCB with deionized water, if required.
- Allow the PCB to dry completely before further handling or use.
Choosing the Right Cleaning Solution
Selecting the appropriate cleaning solution is crucial for effectively removing PCB flux residue without damaging the board or components. The choice of cleaning solution depends on the type of flux used and the specific requirements of your PCB.
Isopropyl Alcohol (IPA)
Isopropyl alcohol is a common and effective cleaning solution for removing rosin-based and no-clean flux residues. It is relatively safe, inexpensive, and easily available. IPA can be used for manual cleaning or in ultrasonic cleaners.
Flux Removers
Flux removers are specialized cleaning solutions designed to dissolve and remove specific types of flux residue. They are available in both water-based and solvent-based formulations. When choosing a flux remover, ensure that it is compatible with your PCB materials and flux type.
Other Solvents
Other solvents, such as acetone, methyl ethyl ketone (MEK), and terpenes, can be used for removing PCB flux residue. However, these solvents may be more aggressive and can potentially damage certain PCB materials or components. Always test the solvent on a small, inconspicuous area of the PCB before using it for cleaning.
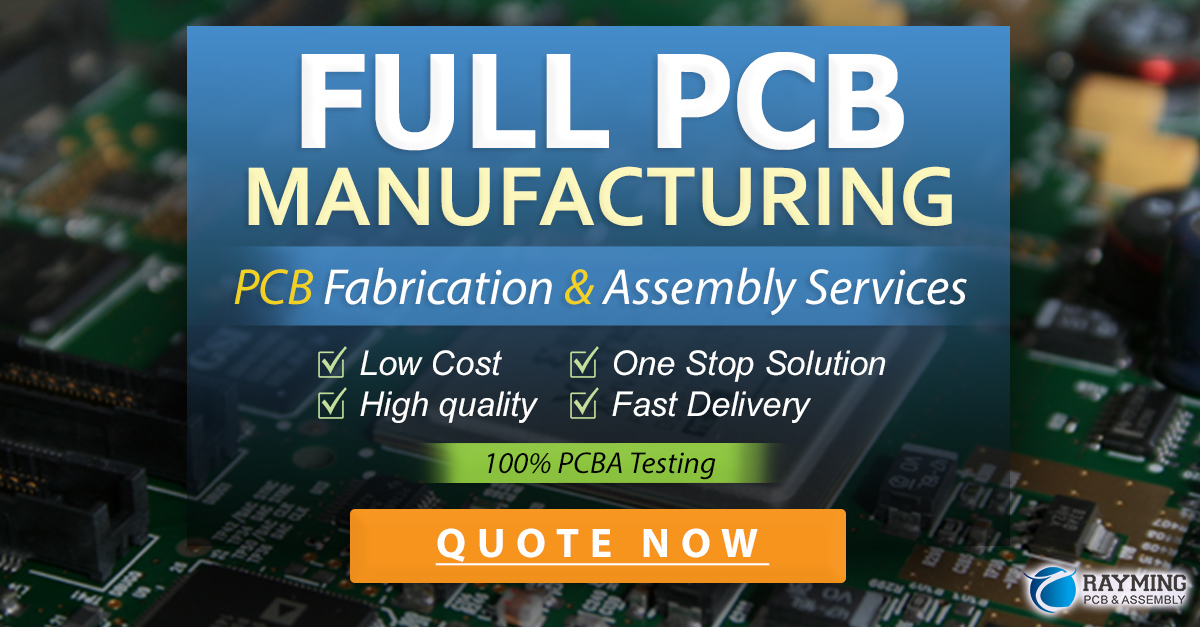
Tips for Effective PCB Flux Removal
- Always wear appropriate personal protective equipment (PPE) when handling cleaning solutions and solvents.
- Work in a well-ventilated area to avoid inhaling fumes from cleaning solutions.
- Follow the manufacturer’s instructions for the cleaning solution and equipment.
- Test the cleaning method and solution on a small, non-critical area of the PCB before applying it to the entire board.
- Be gentle when manually scrubbing the PCB to avoid damaging components or solder joints.
- Ensure that the PCB is completely dry before powering it on or subjecting it to further assembly or testing.
FAQ
1. Is it necessary to remove flux residue from PCBs?
Yes, it is important to remove flux residue from PCBs to prevent corrosion, improve the board’s appearance, and ensure optimal performance. Some types of flux, such as water-soluble flux, are corrosive and must be removed to prevent damage to the PCB and components.
2. Can I use household cleaners to remove PCB flux?
It is not recommended to use household cleaners for removing PCB flux, as they may contain ingredients that can damage the PCB or leave unwanted residues. Always use cleaning solutions specifically designed for electronic applications.
3. How do I know which cleaning method is best for my PCB?
The best cleaning method for your PCB depends on factors such as the size and complexity of the board, the type of flux used, and the available resources. For small PCBs or localized cleaning, manual methods may suffice. For larger boards or batch cleaning, ultrasonic or spray cleaning may be more efficient. If you have access to a vapor degreaser and require a highly effective cleaning process, vapor degreasing may be the best option.
4. Can I reuse the cleaning solution?
The reusability of cleaning solutions depends on the specific solution and the level of contamination. Some solutions, such as isopropyl alcohol, can be reused until they become visibly contaminated or lose their effectiveness. Other solutions, such as water-based cleaners in ultrasonic tanks, may need to be replaced more frequently. Always follow the manufacturer’s guidelines for the reuse and disposal of cleaning solutions.
5. How long should I wait for the PCB to dry after cleaning?
The drying time for a PCB after cleaning depends on the cleaning method and the environment. In general, allow the PCB to air dry for at least 30 minutes to an hour before handling or using it. If you require faster drying, you can use compressed air or a low-temperature oven (below 60°C) to speed up the process. Ensure that the PCB is completely dry before powering it on or subjecting it to further assembly or testing.
Conclusion
Removing PCB soldering flux is a critical step in the PCB manufacturing and assembly process. By understanding the different types of flux and the various cleaning methods available, you can effectively remove flux residue and ensure the optimal performance and longevity of your PCBs. Always choose the appropriate cleaning solution and method for your specific PCB and flux type, and follow proper safety precautions when handling cleaning solutions and solvents. With these tips and techniques, you can maintain the quality and reliability of your PCBs and electronic devices.
Leave a Reply