What is Solder Paste and Why is it Essential?
Solder paste is a crucial component in the world of electronics manufacturing. It is a mixture of tiny solder particles suspended in a flux medium, which is applied to printed circuit boards (PCBs) before surface mount components are placed. The paste serves as both an adhesive to temporarily hold the components in place and a means to form reliable electrical and mechanical connections between the components and the PCB during the reflow soldering process.
Solder paste is essential because it enables the efficient and precise assembly of Surface Mount Devices (SMDs) onto PCBs. Without solder paste, it would be extremely challenging to manually place and solder tiny components, such as resistors, capacitors, and integrated circuits, onto the PCB’s pads. The paste’s unique properties allow for automated assembly processes, which are critical for high-volume production and ensuring consistent quality.
Key Properties of Solder Paste
Solder paste has several key properties that make it suitable for electronics assembly:
-
Solder Alloy Composition: The solder particles in the paste are typically made of a tin-lead (SnPb) or lead-free (e.g., SAC305) alloy. The alloy composition determines the melting point, wetting behavior, and mechanical strength of the solder joints.
-
Particle Size Distribution: The size and distribution of the solder particles in the paste affect its printing and reflow characteristics. Smaller particles allow for finer pitch components and more precise printing, while a narrow size distribution ensures consistent melting and joint formation.
-
Flux Medium: The flux medium in solder paste serves multiple purposes. It helps to suspend and disperse the solder particles, enables proper wetting of the surfaces during reflow, and removes oxides and contaminants from the metal surfaces to promote reliable solder joint formation.
-
Rheology: The rheological properties of solder paste, such as viscosity and thixotropy, determine its flow behavior and printability. A well-formulated paste should have a stable and consistent viscosity, allowing for clean and precise printing through stencils or screens.
Solder Paste Types and Classifications
Solder pastes are classified based on various criteria, such as alloy composition, particle size, and flux type. Understanding these classifications is important for selecting the appropriate paste for a given application.
Alloy Composition
Solder pastes are primarily categorized by their alloy composition. The most common types are:
-
Tin-Lead (SnPb): Traditional solder pastes contain a mixture of tin and lead, with typical ratios of 63Sn/37Pb or 60Sn/40Pb. These pastes have a relatively low melting point (183°C) and excellent wetting properties. However, due to environmental and health concerns, lead-based solders are being phased out in favor of lead-free alternatives.
-
Lead-Free: Lead-free solder pastes use alloys that do not contain lead, such as SAC (Tin-Silver-Copper) alloys. The most common lead-free alloy is SAC305 (96.5Sn/3.0Ag/0.5Cu), which has a higher melting point (217-220°C) compared to SnPb alloys. Other lead-free alloys include SnAg, SnCu, and SnBi.
Particle Size
Solder paste particle size is typically classified using a Type designation (e.g., Type 3, Type 4, Type 5). The table below shows the particle size ranges for common types:
Type | Particle Size Range (μm) |
---|---|
Type 3 | 25-45 |
Type 4 | 20-38 |
Type 5 | 15-25 |
Type 6 | 5-15 |
Smaller particle sizes allow for printing finer pitch components and more intricate PCB designs. However, they may also require more advanced printing equipment and process control.
Flux Type
Solder paste flux is classified according to its activity level and residue characteristics. The J-STD-004 standard defines four flux categories:
-
Rosin (RO): Rosin-based fluxes are derived from pine tree sap and are available in three activity levels: low (ROL0), moderate (ROM0), and high (ROH0). They provide good wetting and are suitable for most applications.
-
Resin (RE): Resin fluxes are synthetic and offer a cleaner residue compared to rosin fluxes. They are available in similar activity levels: low (REL0), moderate (REM0), and high (REH0).
-
Organic (OR): Organic fluxes are water-soluble and can be easily cleaned after reflow. They are also classified by activity level: low (ORL0), moderate (ORM0), and high (ORH0).
-
Inorganic (IN): Inorganic fluxes contain inorganic acids and are highly active. They require thorough cleaning after reflow and are only used in specific applications.
Solder Paste Printing Process
Solder paste printing is the process of applying solder paste onto the PCB’s pads through a stencil or screen. The goal is to deposit a precise amount of paste on each pad, ensuring consistent and reliable solder joints after reflow.
Stencil Design
The stencil is a thin metal sheet (usually stainless steel) with laser-cut or chemically etched apertures that correspond to the PCB’s pads. The aperture size and shape are critical for achieving the correct paste volume and profile on each pad. Factors to consider when designing a stencil include:
-
Aperture Size: The aperture size should be slightly larger than the pad size to allow for proper paste release and to accommodate any misalignment during printing.
-
Aperture Shape: Apertures can be square, rectangular, or circular, depending on the pad geometry and the desired paste profile. Rounded corners help to prevent paste from sticking to the aperture walls.
-
Stencil Thickness: The stencil thickness determines the volume of paste deposited on each pad. Thicker stencils deposit more paste, which may be necessary for larger components or higher-reliability applications. Common stencil thicknesses range from 0.1 mm to 0.2 mm.
Printing Equipment and Process
Solder paste printing is typically performed using automated stencil printers. These machines align the stencil with the PCB, dispense the paste onto the stencil, and use a squeegee blade to spread the paste across the stencil and force it through the apertures onto the pads.
Key factors in the printing process include:
-
Printer Setup: The printer must be properly set up, with the stencil aligned to the PCB and the squeegee pressure, speed, and angle optimized for the paste and stencil being used.
-
Paste Dispensing: The paste should be dispensed in a controlled manner, with the right amount applied to the stencil. Too little paste can result in incomplete prints, while too much paste can cause bridging or slumping.
-
Print Inspection: After printing, the PCB should be inspected to ensure that the paste has been deposited correctly on all pads. Automated vision systems can check for print quality, alignment, and any defects such as bridging or insufficient paste.
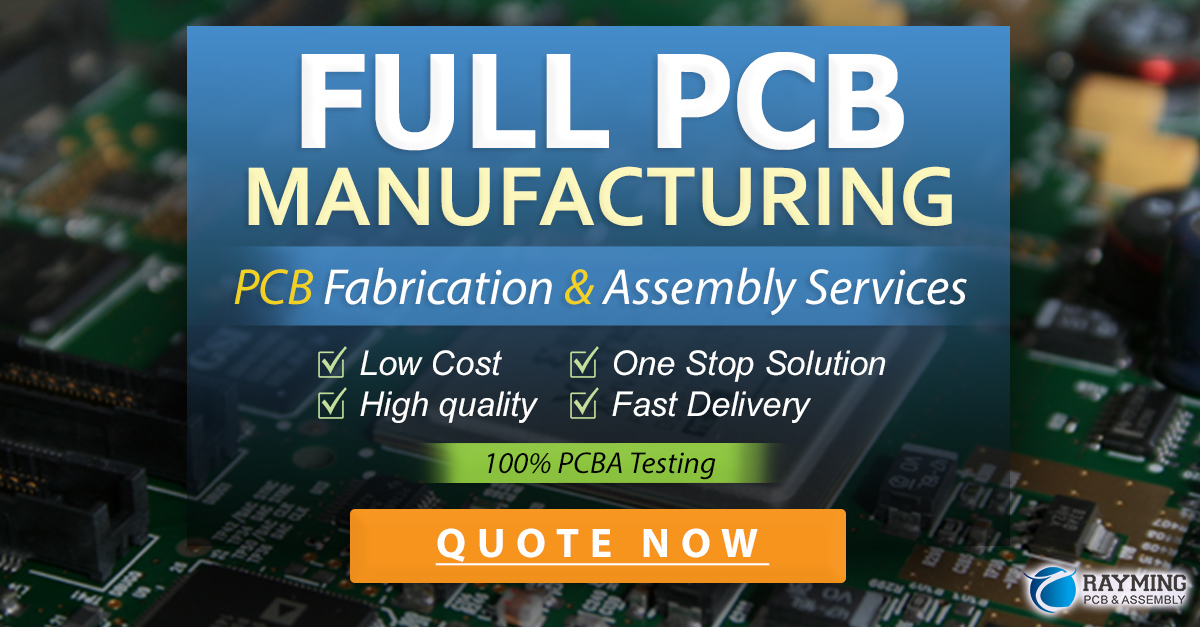
Solder Paste Reflow Profile
Once the components have been placed on the printed solder paste, the PCB undergoes a reflow process to melt the solder and form permanent connections. The reflow profile is a critical factor in achieving high-quality solder joints and reliable PCB Assembly.
A typical reflow profile consists of four stages:
-
Preheat: The PCB is gradually heated to a temperature below the solder paste’s melting point. This stage activates the flux, removes solvents, and prepares the surfaces for soldering.
-
Thermal Soak: The PCB is held at a stable temperature to ensure that all components and the board reach a uniform temperature. This stage also allows the flux to further clean the surfaces and promote wetting.
-
Reflow: The temperature is rapidly increased above the solder paste’s melting point, causing the solder to melt and wet the surfaces of the pads and component leads. The peak temperature and time above liquidus (TAL) are critical parameters in this stage.
-
Cooling: The PCB is cooled at a controlled rate to allow the molten solder to solidify and form strong, reliable solder joints. Rapid cooling can cause thermal shock and lead to joint defects, while slow cooling may result in excessive intermetallic compound (IMC) growth.
The specific temperatures, ramp rates, and dwell times for each stage depend on factors such as the solder paste alloy, PCB design, and component thermal requirements. Solder paste manufacturers provide recommended reflow profiles for their products, which serve as a starting point for developing a profile tailored to the specific application.
Monitoring and controlling the reflow profile is essential for ensuring consistent and reliable solder joint formation. This can be done using thermocouples attached to the PCB or by employing profiling systems that use thermal sensors to measure the actual temperatures experienced by the board during reflow.
Solder Paste Storage and Handling
Proper storage and handling of solder paste are critical for maintaining its quality and performance. Solder paste is a perishable material that can degrade over time due to factors such as oxidation, moisture absorption, and separation of the solder particles from the flux.
Storage Conditions
Solder paste should be stored under controlled conditions to maximize its shelf life:
-
Temperature: Most solder pastes should be stored at refrigerated temperatures between 2-10°C to slow down the rate of oxidation and degradation. Some pastes may require storage at sub-zero temperatures.
-
Humidity: Solder paste should be stored in a low-humidity environment to prevent moisture absorption, which can affect the rheology and printability of the paste. A relative humidity of less than 40% is typically recommended.
-
Container: Solder paste should be stored in airtight containers to minimize exposure to air and moisture. Syringes or jars with tightly sealed lids are commonly used.
Handling Guidelines
When handling solder paste, it is important to follow guidelines to ensure its quality and usability:
-
Thawing: Before use, refrigerated solder paste must be allowed to thaw and reach room temperature. This process should be done gradually to prevent condensation and moisture absorption. Thawing times can range from 2-8 hours, depending on the container size and paste volume.
-
Mixing: After thawing, the solder paste should be thoroughly mixed to redistribute the solder particles and flux components that may have separated during storage. This can be done using a mechanical mixer or by hand-stirring with a spatula.
-
Expiration: Solder paste has a limited shelf life, typically ranging from 3-6 months when stored under proper conditions. The expiration date should be tracked, and expired paste should be discarded to avoid quality issues.
-
Contamination: Care should be taken to avoid contaminating the solder paste with foreign materials or debris. Clean, lint-free gloves should be worn when handling paste containers, and any tools or surfaces that come into contact with the paste should be properly cleaned.
Solder Paste Quality Control and Inspection
Ensuring the quality of solder paste is critical for achieving reliable and consistent PCB assembly. Various tests and inspection methods are used to assess the paste’s properties and performance.
Solder Paste Tests
-
Viscosity: The viscosity of solder paste is measured using a rheometer or viscometer to ensure that it meets the specified range for the desired printability and slump resistance. Changes in viscosity can indicate issues with the paste’s formulation or storage conditions.
-
Thixotropy: Thixotropy is the paste’s ability to thin when sheared (during printing) and then thicken again when at rest (after printing). This property is important for achieving good print definition and preventing slumping or bridging. Thixotropy is typically measured using a rheometer with a specific test profile.
-
Tack: Tack refers to the paste’s ability to hold components in place after placement and before reflow. Tack is influenced by factors such as the flux composition and the solder particle size and shape. Tack tests measure the force required to remove a component from the printed paste.
-
Solder Ball: Solder ball tests assess the paste’s tendency to form small solder balls or satellites during reflow. These balls can cause short circuits or other defects. The test involves reflowing a printed paste sample and inspecting it under a microscope for the presence and size of solder balls.
-
Wetting: Wetting tests evaluate the ability of the molten solder to spread and adhere to the surfaces of the pads and component leads. Good wetting is essential for forming strong and reliable solder joints. Wetting tests can be performed using a wetting balance or by assessing the spread of solder on a test coupon.
Solder Paste Inspection
In addition to testing the paste’s properties, inline inspection techniques are used to monitor the quality of the printed solder paste on the PCB:
-
2D Inspection: 2D solder paste inspection (SPI) systems use cameras to capture images of the printed paste and analyze them for defects such as insufficient paste, bridging, or misalignment. These systems can provide real-time feedback to the printing process, allowing for quick identification and correction of issues.
-
3D Inspection: 3D SPI systems use techniques such as laser triangulation or structured light to measure the height and volume of the printed paste deposits. This information can be used to assess the paste’s consistency and conformance to the desired profile, helping to ensure reliable solder joint formation during reflow.
Regular quality control and inspection of solder paste are essential for maintaining a high-yield and reliable PCB assembly process. By monitoring the paste’s properties and printed quality, manufacturers can identify and address issues early, reducing the risk of defects and rework.
Frequently Asked Questions
- What is the shelf life of solder paste?
The shelf life of solder paste depends on the specific formulation and storage conditions but typically ranges from 3-6 months when stored at refrigerated temperatures (2-10°C) and low humidity (< 40% RH). It is important to check the manufacturer’s recommendations and expiration date for each paste.
- Can expired solder paste be used?
Using expired solder paste is not recommended, as it may have degraded properties that can affect its printability, reflow behavior, and solder joint quality. Expired paste may have reduced viscosity, poor wetting, or excessive solder balling, leading to defects and reliability issues.
- How long can solder paste be left at room temperature?
Solder paste can typically be left at room temperature for 8-12 hours, depending on the specific formulation and ambient conditions. Beyond this time, the paste may start to degrade and lose its optimal properties. It is important to consult the manufacturer’s guidelines for the maximum allowable time at room temperature.
- What happens if solder paste is not mixed properly?
If solder paste is not mixed properly after thawing, the solder particles and flux components may remain separated, leading to inconsistent printing and reflow behavior. Poorly mixed paste may have variations in viscosity, tack, and wetting, resulting in defects such as insufficient solder, bridging, or poor joint formation.
- Can solder paste be reused after printing?
In general, solder paste should not be reused after printing, as it may have been exposed to air, moisture, or contaminants that can degrade its properties. Additionally, the paste may have started to partially cure or thicken, affecting its printability and reflow characteristics. It is best practice to discard any unused paste after a printing session and use fresh paste for the next run.
By understanding the essentials of solder paste, including its composition, properties, handling requirements, and quality control methods, PCB assembly manufacturers can optimize their processes and ensure the production of high-quality, reliable electronic products.
Leave a Reply