What is FR4 Material and Why is Yellowness a Concern?
FR4 (Flame Retardant 4) is a commonly used material for printed circuit boards (PCBs) due to its excellent mechanical, electrical, and thermal properties. It is a composite material made of woven fiberglass cloth impregnated with an epoxy resin binder. FR4 provides a stable and reliable base for mounting electronic components and interconnecting them through conductive copper traces.
However, one aesthetic concern with FR4 material is its tendency to appear yellow, especially when exposed to high temperatures during the manufacturing process or in certain operating environments. This yellowness can be visually unappealing and may raise questions about the quality or reliability of the PCB.
Factors Contributing to FR4 yellowness
Several factors can contribute to the yellowness of FR4 material in PCBs:
-
Resin Formulation: The epoxy resin used in FR4 can have a natural yellow tint, which can become more pronounced under certain conditions.
-
Manufacturing Process: High temperatures during the lamination and soldering processes can accelerate the yellowing of FR4.
-
Exposure to UV Light: Prolonged exposure to ultraviolet (UV) light can cause the epoxy resin in FR4 to degrade and yellow over time.
-
Chemical Exposure: Exposure to certain chemicals, such as strong acids or bases, can also contribute to the yellowing of FR4.
Strategies for Minimizing FR4 Yellowness
To minimize the yellowness of FR4 material in PCBs, several strategies can be employed:
1. Resin Formulation Optimization
One approach to reduce FR4 yellowness is to optimize the epoxy resin formulation. Resin manufacturers can develop special formulations that have reduced yellowing tendencies while maintaining the desired mechanical and electrical properties.
Resin Type | Yellowing Tendency | Mechanical Strength | Thermal Stability |
---|---|---|---|
Standard FR4 Resin | High | High | High |
Low-Yellowing FR4 Resin | Medium | High | High |
Ultra-Low Yellowing FR4 Resin | Low | Medium | Medium |
2. Manufacturing Process Control
Careful control of the manufacturing process can help minimize FR4 yellowness. This includes:
- Optimizing lamination temperature and duration
- Controlling the soldering process to avoid excessive heat exposure
- Implementing proper cooling techniques to minimize thermal stress
3. UV Protection
To prevent yellowing caused by UV exposure, various techniques can be employed:
- Applying UV-resistant coatings or solder masks to the PCB surface
- Using UV-blocking additives in the FR4 resin formulation
- Implementing UV-resistant packaging or storage solutions
4. Chemical Resistance
Selecting FR4 materials with enhanced chemical resistance can help prevent yellowing caused by exposure to harsh chemicals. This may involve using specialized resin formulations or protective coatings that provide a barrier against chemical attack.
Impact of FR4 Yellowness on PCB Performance
While the yellowness of FR4 material is primarily an aesthetic concern, it can also have some impact on PCB performance:
-
Visual Inspection: Yellowed PCBs can make visual inspection more challenging, as defects or anomalies may be harder to detect against a yellow background.
-
Optical Sensors: In applications involving optical sensors or light-sensitive components, excessive yellowness of the PCB substrate may interfere with the desired optical properties.
-
Customer Perception: In some cases, customers may perceive yellowed PCBs as being of lower quality or reliability, even if the yellowness does not directly affect the PCB’s performance.
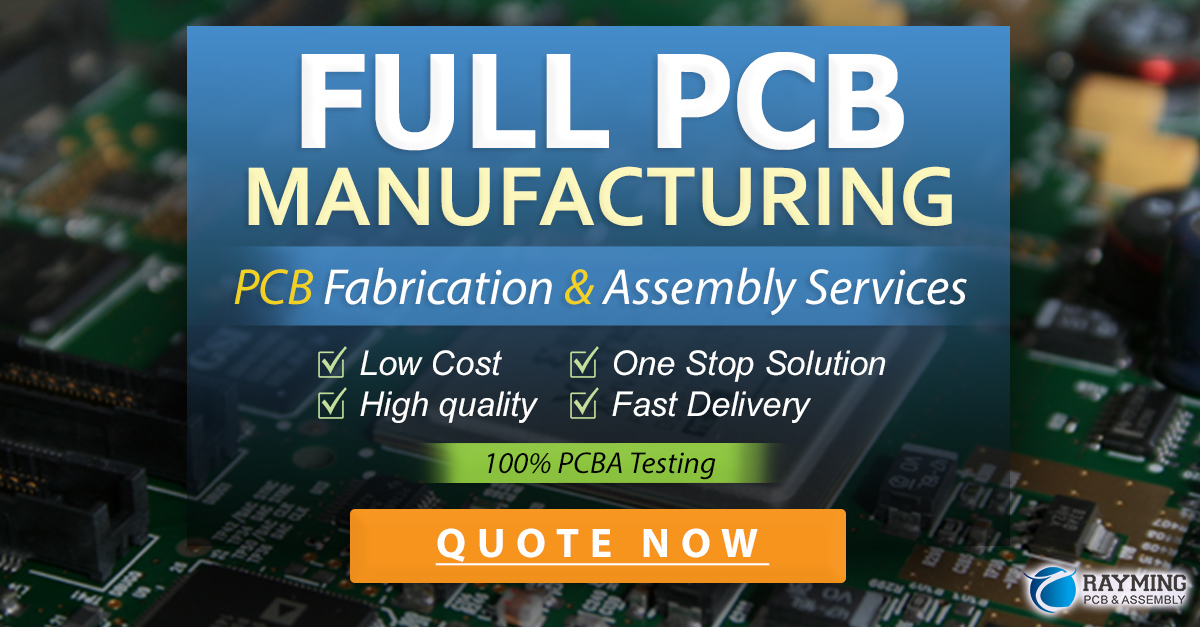
Alternatives to FR4 for Reduced Yellowness
While strategies can be employed to minimize FR4 yellowness, there are also alternative PCB materials that inherently have less yellowing tendency:
1. Polyimide (PI)
Polyimide is a high-performance polymer that offers excellent thermal stability, chemical resistance, and low yellowing characteristics. It is often used in applications requiring high reliability and resistance to harsh environments.
2. High Tg FR4
High Tg (glass transition temperature) FR4 materials are formulated to withstand higher temperatures without significant yellowing. These materials have a higher Tg value compared to standard FR4, typically above 170°C.
3. Halogen-Free Materials
Some Halogen-Free PCB materials, such as those based on polyphenylene oxide (PPO) or bismaleimide triazine (BT), exhibit lower yellowing tendencies compared to traditional FR4. These materials are increasingly used in environmentally friendly and low-yellowing applications.
Conclusion
FR4 yellowness is a common concern in PCB manufacturing, primarily due to its impact on aesthetics and visual perception. While the yellowing of FR4 does not necessarily affect the electrical performance of the PCB, it can raise questions about quality and reliability.
To minimize FR4 yellowness, strategies such as optimizing resin formulation, controlling the manufacturing process, implementing UV protection, and enhancing chemical resistance can be employed. Additionally, alternative PCB materials like polyimide, high Tg FR4, and halogen-free options can be considered for applications where low yellowing is a critical requirement.
By understanding the factors contributing to FR4 yellowness and implementing appropriate mitigation strategies, PCB manufacturers can produce boards with improved visual appearance while maintaining the desired electrical and mechanical properties.
Frequently Asked Questions (FAQ)
-
What causes FR4 material to yellow in PCBs?
FR4 yellowing can be caused by factors such as the natural yellow tint of the epoxy resin, exposure to high temperatures during manufacturing, prolonged UV light exposure, and chemical exposure. -
Does FR4 yellowing affect the electrical performance of PCBs?
In most cases, FR4 yellowing does not directly impact the electrical performance of PCBs. However, it can make visual inspection more challenging and may affect customer perception of quality. -
How can FR4 yellowness be minimized during PCB manufacturing?
Strategies to minimize FR4 yellowness include optimizing the resin formulation, controlling the manufacturing process parameters (e.g., lamination temperature and duration), implementing UV protection measures, and enhancing chemical resistance. -
Are there alternative materials to FR4 that have lower yellowing tendency?
Yes, alternative PCB materials such as polyimide (PI), high Tg FR4, and halogen-free materials like polyphenylene oxide (PPO) or bismaleimide triazine (BT) exhibit lower yellowing tendencies compared to standard FR4. -
Is FR4 yellowness a purely aesthetic concern, or can it have other implications?
While FR4 yellowness is primarily an aesthetic concern, it can also impact visual inspection processes, interfere with optical sensors in certain applications, and influence customer perception of PCB Quality and reliability.
Leave a Reply