PCB Footprint and Pad Design for Soldering
One of the most important aspects of designing a PCB for soldering is creating appropriate footprints and pads for each component. The footprint is the arrangement of pads and holes on the PCB that match up with the leads or contacts on the electronic component. Pads need to be the right size, shape, and spacing to allow for proper soldering.
Pad Size and Spacing
Pads should be sized based on the component lead/contact dimensions as well as the soldering process to be used (e.g. wave, reflow, hand soldering). A good guideline is to make the pad 25-50% larger than the component lead or contact. This provides sufficient area for solder to form a strong joint.
Pad-to-Pad spacing is another key consideration. Pads need to be spaced far enough apart to prevent solder bridges from forming between adjacent pads. The minimum spacing depends on factors like the soldering method, solder paste properties, and PCB manufacturability. A typical minimum pad spacing for standard surface mount components is around 0.2-0.25 mm.
Pad Shape
The most common pad shapes are rectangular and rounded rectangular. Rounded rectangular pads, also called oblong or oval pads, can improve solder joint strength and self-centering of components during reflow. However, they require more precise control of solder paste volume. The table below summarizes pros and cons of rectangular vs rounded pads:
Pad Shape | Pros | Cons |
---|---|---|
Rectangular | Easier to control solder paste volume | Lower joint strength |
Rounded | Higher joint strength, self-centering | Requires tighter paste volume control |
Solder Mask Openings
Solder mask is a polymer coating applied to the PCB that covers areas where soldering is not desired. Openings in the solder mask, called solder mask clearance, are needed around component pads to allow soldering to those pads.
The size of solder mask openings impacts how well solder flows onto the pads. Openings that are too small can cause Insufficient Soldering and weak joints. Openings that are too large may allow solder to spread onto unintended areas. Typically, solder mask openings should be 0.05-0.1 mm larger than the pad size on all sides.
PCB Layout for Soldering
Beyond individual footprints and pads, the overall PCB layout and arrangement of components play a big role in soldering quality and reliability. Good PCB layout practices help ensure manufacturability, ease of assembly, and long-term reliability.
Component Placement
Components should be placed in a logical arrangement that minimizes crossing of leads/contacts and allows for efficient soldering. Some guidelines for component placement include:
- Place components on a grid to allow for automated assembly
- Align components in the same orientation for easier visual inspection
- Group similar components together
- Provide adequate spacing between components for soldering and rework
- Avoid placing large/tall components near the edge of the board
Thermal Design
During soldering, heat is applied to melt the solder and form joints. However, excessive heat can damage components or cause reliability issues. PCB Designs need to manage heat flow and dissipation during soldering.
One way to improve thermal performance is by using thermal relief pads. These are pads with narrower connections to the rest of the copper plane, which restricts heat flow away from the pad. This helps the pad reach soldering temperature faster and prevents heat from spreading to nearby components.
Proper sizing of copper planes and traces also impacts thermal behavior. Larger copper features act as heat sinks and draw heat away from components during soldering. The table below shows recommended minimum trace widths for different copper thicknesses:
Copper Thickness (oz) | Minimum Trace Width (mm) |
---|---|
0.5 | 0.2 |
1 | 0.3 |
2 | 0.5 |
Panelization
Panelization is the process of arranging multiple PCBs into a larger panel for production. This allows for more efficient assembly since multiple boards can be soldered at once. However, panelization also introduces some additional design considerations.
Boards in a panel need to be spaced far enough apart to allow for component overhangs, tooling, and depanelization. A minimum spacing of 3-5 mm between boards is typical. Tooling holes and fiducials also need to be added to the panel to assist with alignment and assembly.
Depanelization methods, such as V-scoring or tab routing, impact the panelization design as well. The chosen depanelization method determines the spacing and arrangement of boards in the panel.
Soldering Process Considerations
In addition to PCB design, the soldering process itself can impact joint quality and reliability. Different soldering methods have different requirements and potential failure modes that need to be accounted for.
Wave Soldering
Wave soldering involves passing the PCB over a wave of molten solder, which wets and forms joints on exposed pads and through-holes. Some key considerations for wave soldering include:
- Orientation of components and board travel direction
- Use of thermal reliefs to prevent heat damage
- Solder mask placement to prevent solder from spreading
- Placement of components to prevent shadowing
Reflow Soldering
Reflow soldering uses solder paste applied to pads, which is then heated to melt and form joints. Considerations for reflow soldering include:
- Solder paste selection and volume
- Stencil design for paste application
- Reflow temperature profile
- Component thermal limits
Hand Soldering
For low-volume assembly or rework, hand soldering may be used. Hand soldering requires more skill and attention to detail than automated methods. Some tips for successful hand soldering include:
- Use of appropriate soldering iron tip size and temperature
- Proper cleaning and tinning of the iron tip
- Adequate flux application
- Avoiding excessive heat or pressure on components
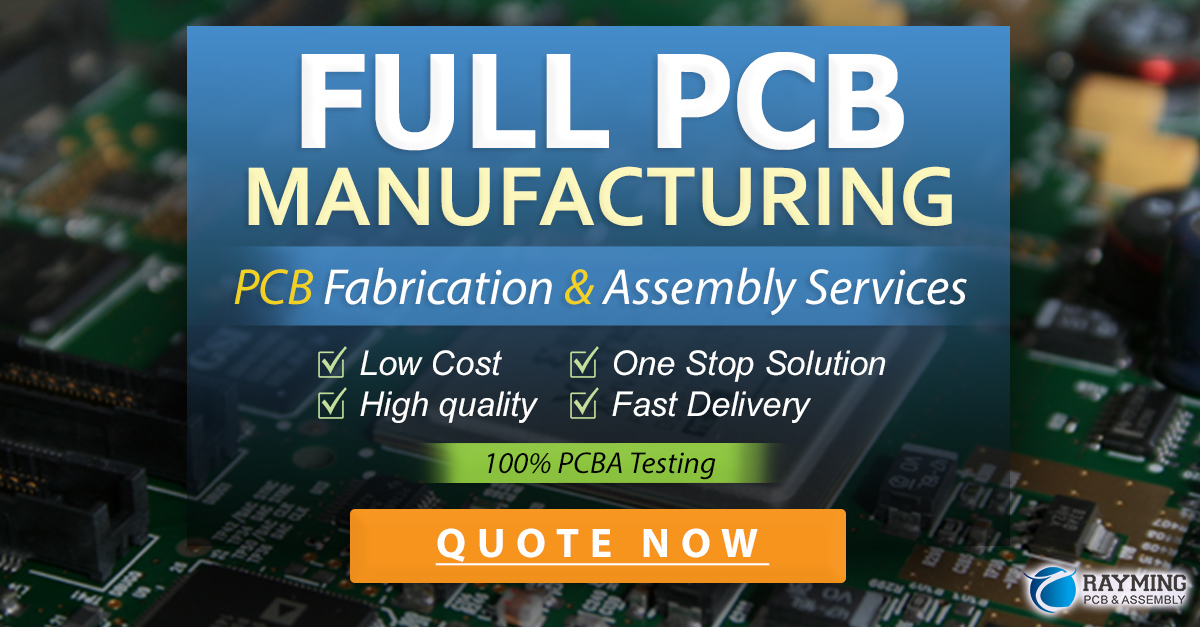
Common Soldering Defects
Even with proper PCB design and soldering process control, defects can still occur. Being aware of common soldering defects and their causes can help inform design decisions and troubleshooting.
Solder Bridges
Solder bridges are unintended connections between adjacent pads or pins, caused by excess solder. Solder bridges can be prevented by:
- Adequate pad spacing
- Precise control of solder paste volume
- Proper stencil design and alignment
- Sufficient solder mask clearance
Tombstoning
Tombstoning, also known as drawbridging, is when a component stands up on one end due to uneven heating or surface tension during reflow. Tombstoning can be minimized by:
- Ensuring even pad sizes on both sides of the component
- Controlling paste volume and placement
- Using a properly designed reflow profile
Cold Joints
Cold joints are weak, brittle solder joints that result from insufficient heat or poor wetting. Causes of cold joints include:
- Insufficient flux
- Contaminated pads or component leads
- Incorrect iron temperature
- Inadequate heat transfer to the joint
Voiding
Voids are cavities or bubbles that form within the solder joint, weakening it. Voids can be caused by:
- Outgassing of flux or contaminants
- Rapid cooling of the joint
- Incorrect reflow profile
- Inadequate paste volume
FAQ
What is the most important factor in designing a PCB for soldering?
Creating appropriate footprints and pad designs for each component is one of the most critical aspects of PCB design for soldering. Pads need to be the right size, shape, and spacing to ensure reliable solder joints and prevent defects.
How big should solder mask openings be?
Solder mask openings should typically be 0.05-0.1 mm larger than the pad size on all sides. This allows for sufficient solder wetting onto the pad while still preventing bridging or spreading.
What is the purpose of thermal relief pads?
Thermal relief pads have narrower connections to the rest of the copper plane, which restricts heat transfer away from the pad during soldering. This allows the pad to reach soldering temperature faster and prevents excess heat from spreading to nearby components.
What causes tombstoning of components during reflow soldering?
Tombstoning can occur due to uneven heating or surface tension forces on the component during reflow. It is often caused by unequal pad sizes on either side of the component or improper control of solder paste volume and placement.
How can voiding in solder joints be minimized?
To minimize voiding, the reflow profile should be optimized to allow sufficient time for flux and volatiles to outgas before solidification of the solder. Adequate solder paste volume and proper joint design also help reduce the risk of voiding.
Leave a Reply