Why is Pad to Pad Spacing Important?
Pad-to-Pad spacing plays a crucial role in several aspects of PCB design and manufacturing:
1. Component Placement
The pad-to-pad distance directly affects the placement of components on the PCB. It determines how closely components can be placed next to each other without causing interference or soldering issues. Adequate pad-to-pad spacing allows for optimal component density while maintaining manufacturability and reliability.
2. Soldering Process
Proper pad-to-pad spacing is essential for the soldering process. If the pads are too close together, there is a risk of solder bridges forming between adjacent pads, leading to short circuits. On the other hand, if the pads are too far apart, it can be challenging to achieve reliable solder joints. The pad-to-pad distance must be carefully considered to ensure that the soldering process can be carried out effectively.
3. Manufacturing Capability
The pad-to-pad spacing also depends on the manufacturing capabilities of the PCB fabrication and assembly facilities. Different manufacturing processes and equipment have varying limitations in terms of the minimum pad-to-pad distance they can handle. It is essential to consider these capabilities when designing the PCB to ensure that it can be manufactured reliably and cost-effectively.
4. Signal Integrity
In high-speed and high-frequency PCB designs, pad-to-pad spacing can impact signal integrity. Closely spaced pads can introduce capacitive coupling and crosstalk between adjacent signals, leading to signal distortion and interference. Proper pad-to-pad spacing, along with other design techniques such as ground planes and shielding, helps to mitigate these issues and maintain signal integrity.
Factors Affecting Pad to Pad Spacing
Several factors influence the determination of appropriate pad-to-pad spacing:
1. Component Package
The component package type and size play a significant role in determining the pad-to-pad spacing. Different package types, such as QFP (Quad Flat Pack), BGA (Ball Grid Array), or CSP (Chip Scale Package), have specific requirements for pad size and spacing. The pad-to-pad distance must accommodate the dimensions of the component package while allowing for reliable soldering and assembly.
2. PCB Manufacturing Process
The PCB manufacturing process and the capabilities of the fabrication facility impact the achievable pad-to-pad spacing. Different manufacturing processes, such as etching, plating, or solder mask application, have their own tolerances and limitations. The pad-to-pad spacing must be designed to meet the capabilities of the chosen manufacturing process to ensure successful fabrication.
3. Assembly Process
The assembly process, including soldering techniques and equipment, also influences pad-to-pad spacing. For example, wave soldering or reflow soldering may have different requirements for pad spacing compared to manual soldering. The pad-to-pad distance must be compatible with the assembly process to ensure reliable and efficient component attachment.
4. Industry Standards and Guidelines
Various industry standards and guidelines provide recommendations for pad-to-pad spacing based on component packages, PCB materials, and manufacturing processes. These standards, such as IPC (Institute of Printed Circuits) or JEDEC (Joint Electron Device Engineering Council), offer guidelines to ensure compatibility and reliability in PCB design and manufacturing.
Pad to Pad Spacing Guidelines
To determine appropriate pad-to-pad spacing, designers can refer to industry standards, component manufacturer recommendations, and PCB fabrication and assembly guidelines. Here are some general guidelines for pad-to-pad spacing based on common component packages:
Component Package | Minimum Pad-to-Pad Spacing |
---|---|
QFP (Quad Flat Pack) | 0.5mm – 0.8mm |
BGA (Ball Grid Array) | 0.5mm – 0.8mm |
CSP (Chip Scale Package) | 0.3mm – 0.5mm |
SOIC (Small Outline Integrated Circuit) | 0.5mm – 0.8mm |
TSSOP (Thin Shrink Small Outline Package) | 0.3mm – 0.5mm |
It is important to note that these are general guidelines, and specific component packages may have different requirements. Always refer to the component manufacturer’s datasheet and the PCB fabrication and assembly guidelines for accurate pad-to-pad spacing information.
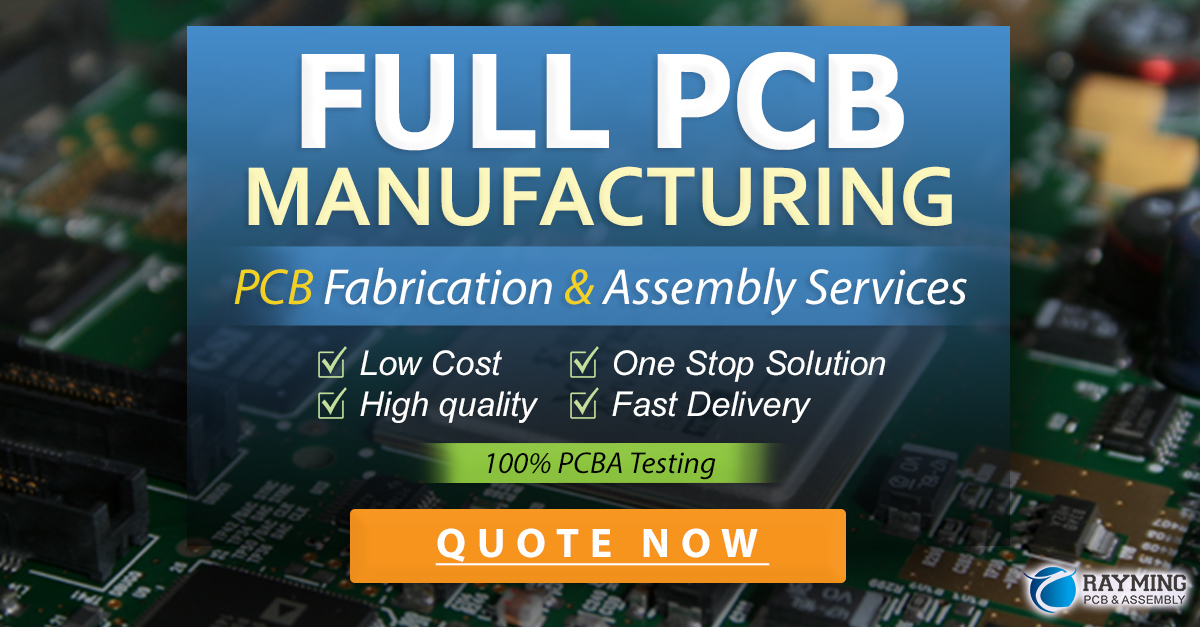
Designing for Optimal Pad to Pad Spacing
When designing a PCB, consider the following best practices to optimize pad-to-pad spacing:
- Consult component datasheets and application notes for recommended pad sizes and spacing.
- Follow industry standards and guidelines, such as IPC or JEDEC, for pad-to-pad spacing recommendations based on component packages and PCB materials.
- Communicate with the PCB fabrication and assembly facilities to understand their capabilities and limitations regarding pad-to-pad spacing.
- Use PCB design software that provides design rule checks (DRC) to ensure compliance with pad-to-pad spacing requirements.
- Consider the impact of pad-to-pad spacing on signal integrity, especially in high-speed and high-frequency designs. Use appropriate design techniques, such as ground planes and shielding, to mitigate crosstalk and interference.
- Perform thorough testing and prototyping to validate the pad-to-pad spacing and ensure reliable soldering and assembly.
Frequently Asked Questions (FAQ)
1. What happens if the pad-to-pad spacing is too small?
If the pad-to-pad spacing is too small, it can lead to several issues:
– Solder bridges may form between adjacent pads, causing short circuits.
– Difficulty in achieving reliable solder joints due to insufficient space for solder fillets.
– Increased risk of component misalignment during assembly.
– Potential signal integrity issues due to capacitive coupling and crosstalk between closely spaced pads.
2. Can the pad-to-pad spacing be different for different layers of the PCB?
Yes, the pad-to-pad spacing can vary between different layers of the PCB. For example, the spacing on the outer layers may be different from the inner layers due to different manufacturing processes or signal requirements. It is important to consider the specific requirements of each layer and ensure compatibility with the manufacturing capabilities.
3. How does the PCB material affect pad-to-pad spacing?
The choice of PCB material can impact the pad-to-pad spacing. Different materials have varying dielectric constants, which affect the electrical characteristics of the PCB. Materials with higher dielectric constants may require larger pad-to-pad spacing to maintain signal integrity and prevent crosstalk. Additionally, the thickness and thermal properties of the PCB material can influence the pad-to-pad spacing requirements.
4. What is the relationship between pad-to-pad spacing and PCB trace width?
Pad-to-pad spacing and PCB trace width are interconnected. The trace width determines the current-carrying capacity and impedance of the signal traces on the PCB. Wider traces generally require larger pad-to-pad spacing to accommodate the trace width and maintain appropriate clearances. The pad-to-pad spacing should be designed in conjunction with the trace width to ensure compatibility and signal integrity.
5. How can I determine the appropriate pad-to-pad spacing for a specific component?
To determine the appropriate pad-to-pad spacing for a specific component, follow these steps:
1. Consult the component manufacturer’s datasheet or application notes for recommended pad sizes and spacing.
2. Refer to industry standards and guidelines, such as IPC or JEDEC, for pad-to-pad spacing recommendations based on the component package and PCB materials.
3. Communicate with the PCB fabrication and assembly facilities to understand their capabilities and limitations regarding pad-to-pad spacing.
4. Use PCB design software that provides design rule checks (DRC) to ensure compliance with pad-to-pad spacing requirements.
5. Perform thorough testing and prototyping to validate the pad-to-pad spacing and ensure reliable soldering and assembly.
Conclusion
Pad to Pad (PP) spacing is a critical aspect of PCB design and manufacturing. It directly impacts component placement, soldering reliability, manufacturing capability, and signal integrity. Proper pad-to-pad spacing ensures that components can be reliably soldered and assembled on the PCB while maintaining optimal performance.
When designing a PCB, it is essential to consider factors such as component packages, PCB manufacturing processes, assembly techniques, and industry standards to determine appropriate pad-to-pad spacing. By following best practices and guidelines, designers can optimize pad-to-pad spacing to achieve reliable and manufacturable PCBs.
Effective communication between designers, component manufacturers, and PCB fabrication and assembly facilities is crucial to ensure compatibility and successful implementation of pad-to-pad spacing requirements. Through careful consideration and attention to detail, designers can create PCBs that meet the required functionality, reliability, and manufacturability standards.
Leave a Reply