Introduction to PCB Design
Printed Circuit Board (PCB) design is a crucial aspect of modern electronics manufacturing. PCBs are the backbone of almost all electronic devices, from smartphones and laptops to industrial control systems and medical equipment. A well-designed PCB ensures reliable performance, durability, and cost-effectiveness of the final product.
In this comprehensive guide, we will dive into the essentials of PCB design manufacturing, covering topics such as PCB types, design considerations, manufacturing processes, and best practices. Whether you are a beginner or an experienced engineer, this article will provide valuable insights to help you create high-quality PCBs.
Types of PCBs
There are several types of PCBs, each with its own characteristics and applications. Understanding the differences between these types is essential for selecting the most suitable PCB for your project.
Single-Layer PCBs
Single-layer PCBs, also known as single-sided PCBs, have conductive traces on only one side of the substrate. They are the simplest and most cost-effective type of PCB, making them ideal for low-complexity circuits and prototypes.
Double-Layer PCBs
Double-layer PCBs, or double-sided PCBs, have conductive traces on both sides of the substrate. They offer more design flexibility and higher component density compared to single-layer PCBs. Double-layer PCBs are commonly used in consumer electronics, such as smartphones and laptops.
Multi-Layer PCBs
Multi-layer PCBs consist of three or more conductive layers, separated by insulating layers. They provide the highest level of design complexity and component density, allowing for the creation of compact and highly functional devices. Multi-layer PCBs are often used in advanced applications, such as aerospace, military, and high-performance computing.
Flexible PCBs
Flexible PCBs, or flex PCBs, are made from flexible substrate materials, such as polyimide or polyester. They can bend and fold to fit into tight spaces or conform to specific shapes. Flex PCBs are commonly used in wearable devices, medical implants, and aerospace applications.
Rigid-Flex PCBs
Rigid-flex PCBs combine the benefits of both rigid and flexible PCBs. They consist of rigid PCB sections connected by flexible PCB sections, allowing for three-dimensional packaging and improved reliability. Rigid-flex PCBs are often used in applications that require high density and flexibility, such as smartphones and medical devices.
PCB Design Considerations
Creating a successful PCB design involves considering various factors that impact the performance, manufacturability, and cost of the final product. Some of the key design considerations include:
Schematic Design
The schematic design is the first step in the PCB design process. It involves creating a graphical representation of the circuit, showing the components and their interconnections. A well-designed schematic is essential for ensuring the correct functionality of the PCB.
Component Selection
Selecting the right components is crucial for the performance and reliability of the PCB. Factors to consider when choosing components include:
- Functionality
- Package size and type
- Power requirements
- Environmental conditions (temperature, humidity, etc.)
- Cost and availability
Layout Design
The layout design involves placing components and routing traces on the PCB. A good layout design should:
- Minimize signal integrity issues (crosstalk, electromagnetic interference, etc.)
- Ensure proper power distribution and thermal management
- Optimize manufacturing yield and reliability
- Comply with design rules and constraints
Design for Manufacturing (DFM)
Design for Manufacturing (DFM) is a set of guidelines and best practices that help ensure the manufacturability and reliability of the PCB. Some key DFM considerations include:
- Choosing appropriate trace widths and spacings
- Avoiding acute angles and sharp corners
- Providing adequate clearances for component placement and soldering
- Minimizing the number of vias and layer transitions
Signal Integrity and EMC
Signal integrity and electromagnetic compatibility (EMC) are critical aspects of PCB design. Poor signal integrity can lead to data corruption, while EMC issues can cause interference with other electronic devices. To mitigate these problems, designers should:
- Use appropriate trace geometries and impedance matching techniques
- Implement proper grounding and shielding strategies
- Follow EMC design guidelines and conduct necessary testing
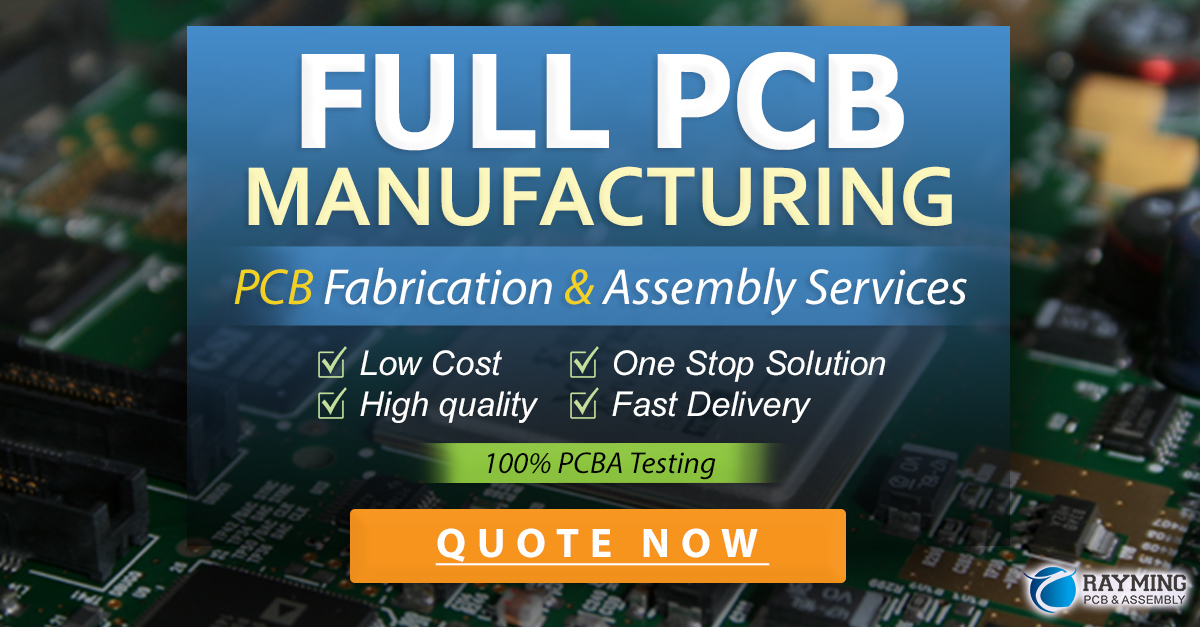
PCB Manufacturing Process
The PCB manufacturing process involves several steps, each contributing to the quality and reliability of the final product. Understanding these steps can help you make informed decisions and communicate effectively with your manufacturing partners.
PCB Fabrication
PCB fabrication is the process of creating the bare PCB, which includes the following steps:
-
Substrate Preparation: The substrate material (typically FR-4) is cut to the desired size and cleaned.
-
Copper Lamination: Copper foil is laminated onto the substrate using heat and pressure.
-
Drilling: Holes are drilled into the PCB for component leads and vias.
-
Patterning: The desired circuit pattern is transferred onto the copper layer using photolithography and etching processes.
-
Plating: The holes are plated with copper to create electrical connections between layers.
-
Solder Mask Application: A protective solder mask is applied to the PCB, exposing only the areas intended for soldering.
-
Silkscreen Printing: Text and symbols are printed onto the PCB for component identification and assembly guidance.
PCB Assembly
PCB assembly involves populating the fabricated PCB with components. The two main assembly methods are:
-
Through-Hole Assembly (THA): Components with leads are inserted through holes in the PCB and soldered onto the opposite side.
-
Surface Mount Assembly (SMA): Components are placed directly onto the surface of the PCB and soldered using reflow or wave soldering techniques.
Testing and Inspection
After assembly, PCBs undergo various testing and inspection procedures to ensure their functionality and quality. Some common tests include:
- Automated Optical Inspection (AOI)
- X-ray Inspection
- In-Circuit Testing (ICT)
- Functional Testing
- Burn-in Testing
Best Practices for PCB Design
To create high-quality PCBs that meet your project requirements, consider the following best practices:
-
Start with a clear specification: Define your project requirements, including functionality, performance, size, and environmental conditions.
-
Use a reliable CAD tool: Invest in a professional PCB design software that offers features such as schematic capture, layout design, and design rule checking (DRC).
-
Follow design guidelines: Adhere to industry-standard design guidelines, such as the IPC standards, to ensure the manufacturability and reliability of your PCBs.
-
Collaborate with your manufacturing partners: Engage with your PCB fabrication and assembly partners early in the design process to discuss DFM considerations and avoid potential issues.
-
Conduct thorough reviews and tests: Perform design reviews, DRC checks, and prototype testing to identify and resolve any issues before mass production.
Frequently Asked Questions (FAQ)
-
What is the difference between a PCB and a PCBA?
A PCB (Printed Circuit Board) is the bare board with copper traces and pads, while a PCBA (Printed Circuit Board Assembly) is a PCB populated with components. -
How do I choose the right PCB material for my project?
The choice of PCB material depends on factors such as the operating environment, frequency, and cost. FR-4 is the most common material for general-purpose applications, while high-frequency or high-temperature applications may require specialized materials like Rogers or ceramic. -
What is the minimum feature size I can achieve with PCB fabrication?
The minimum feature size depends on the capabilities of your PCB fabrication partner. Typical minimum trace widths and spacings range from 3 to 6 mils (0.075 to 0.15 mm) for standard PCBs, while advanced processes can achieve feature sizes down to 1 mil (0.025 mm) or less. -
How can I reduce the cost of my PCB design?
To reduce PCB cost, consider the following strategies: -
Minimize the number of layers and board size
- Use standard components and packaging
- Optimize panel utilization and yield
- Choose cost-effective materials and finishes
-
Engage with your manufacturing partners for cost-saving recommendations
-
What are the lead times for PCB fabrication and assembly?
Lead times for PCB fabrication and assembly vary depending on the complexity of the design, the manufacturing process, and the supplier. Typical lead times range from a few days to several weeks. To ensure timely delivery, communicate your requirements and timeline with your manufacturing partners early in the project.
Conclusion
PCB design manufacturing is a complex and multifaceted process that requires careful consideration of various factors, from component selection and layout design to manufacturing processes and best practices. By understanding the fundamentals of PCB design and following industry guidelines, you can create high-quality, reliable, and cost-effective PCBs that meet your project requirements.
Remember to collaborate closely with your PCB fabrication and assembly partners, as their expertise and insights can help you optimize your designs and avoid potential issues. With the right knowledge, tools, and support, you can bring your electronic ideas to life and create innovative products that make a difference in the world.
Leave a Reply