Introduction to BGA Assembly
Ball Grid Array (BGA) assembly is a critical process in the manufacturing of modern electronic devices. BGA packages offer numerous advantages over traditional through-hole and surface-mount packages, including higher pin density, better thermal and electrical performance, and reduced package size. As electronic devices continue to shrink in size and increase in functionality, BGA assembly has become an essential capability for electronics manufacturers.
What is BGA?
BGA (Ball Grid Array) is a surface-mount packaging technology that uses a grid of solder balls to connect the package to the printed circuit board (PCB). The solder balls are arranged in a matrix on the bottom side of the package, allowing for a high density of interconnects in a small package size. BGA packages can have hundreds or even thousands of solder balls, depending on the size and complexity of the device.
Advantages of BGA Packaging
BGA packaging offers several advantages over other packaging technologies, including:
- High pin density: BGA packages can accommodate a large number of interconnects in a small package size, making them ideal for complex devices with high I/O counts.
- Improved thermal performance: The solder balls in a BGA package provide a low-resistance thermal path between the device and the PCB, allowing for better heat dissipation.
- Better electrical performance: The short interconnects in a BGA package reduce inductance and improve signal integrity, resulting in better electrical performance.
- Reduced package size: BGA packages are typically smaller than equivalent throughole or surface-mount packages, allowing for more compact device designs.
BGA Assembly Process
The BGA assembly process involves several steps, including PCB preparation, solder paste printing, component placement, and reflow soldering. Each step requires precise control and specialized equipment to ensure reliable and consistent results.
PCB Preparation
Before the BGA assembly process can begin, the PCB must be properly prepared. This includes:
- Cleaning: The PCB surface must be clean and free of contaminants that could interfere with the solder joint formation.
- Solder Mask application: A solder mask is applied to the PCB to protect the copper traces and prevent solder bridging.
- Pad finishing: The pads on the PCB must be finished with a suitable surface finish, such as Organic Solderability Preservative (OSP) or Electroless Nickel Immersion Gold (ENIG), to ensure good solder joint formation.
Solder Paste Printing
Solder paste is a mixture of tiny solder spheres suspended in a flux matrix. The solder paste is applied to the PCB using a stencil printing process, which deposits a precise amount of solder paste onto each pad. The stencil is a thin metal sheet with apertures that match the pad layout on the PCB. The solder paste is forced through the apertures onto the pads using a squeegee blade.
Component Placement
After the solder paste has been applied, the BGA component is placed onto the PCB using a pick-and-place machine. The machine uses vision systems to align the component with the pads on the PCB and place it with high accuracy. The component is held in place by the tackiness of the solder paste.
Reflow Soldering
Once the component has been placed, the PCB is transferred to a reflow oven for soldering. The reflow oven applies a carefully controlled temperature profile to the PCB, which melts the solder paste and forms a metallurgical bond between the component and the PCB. The temperature profile must be carefully optimized to ensure good solder joint formation without damaging the components or the PCB.
BGA Assembly Challenges
While BGA assembly offers many advantages, it also presents several challenges that must be overcome to ensure reliable and consistent results.
Thermal Management
One of the main challenges in BGA assembly is managing the heat generated by the device. The high pin density of BGA packages can result in high power densities, which can lead to thermal issues if not properly managed. Proper thermal management requires careful design of the PCB Layout, selection of materials with appropriate thermal properties, and use of heat sinks or other cooling solutions where necessary.
Solder Joint Reliability
Another challenge in BGA assembly is ensuring the reliability of the solder joints. The small size and close spacing of the solder balls in a BGA package can make it difficult to achieve consistent and reliable solder joints. Factors that can affect solder joint reliability include:
- Solder paste quality: The solder paste must have the appropriate composition and particle size distribution to ensure good solder joint formation.
- Stencil design: The stencil apertures must be properly sized and shaped to deposit the correct amount of solder paste onto each pad.
- Reflow profile: The reflow temperature profile must be carefully optimized to ensure complete melting and wetting of the solder paste without damaging the components or the PCB.
- PCB and component warpage: Warpage of the PCB or component can lead to open or inadequate solder joints.
Rework and Repair
Reworking or repairing BGA assemblies can be challenging due to the small size and close spacing of the solder balls. Special tools and techniques are required to remove and replace BGA Components without damaging the PCB or adjacent components. Proper training and experience are essential for successful BGA Rework and repair.
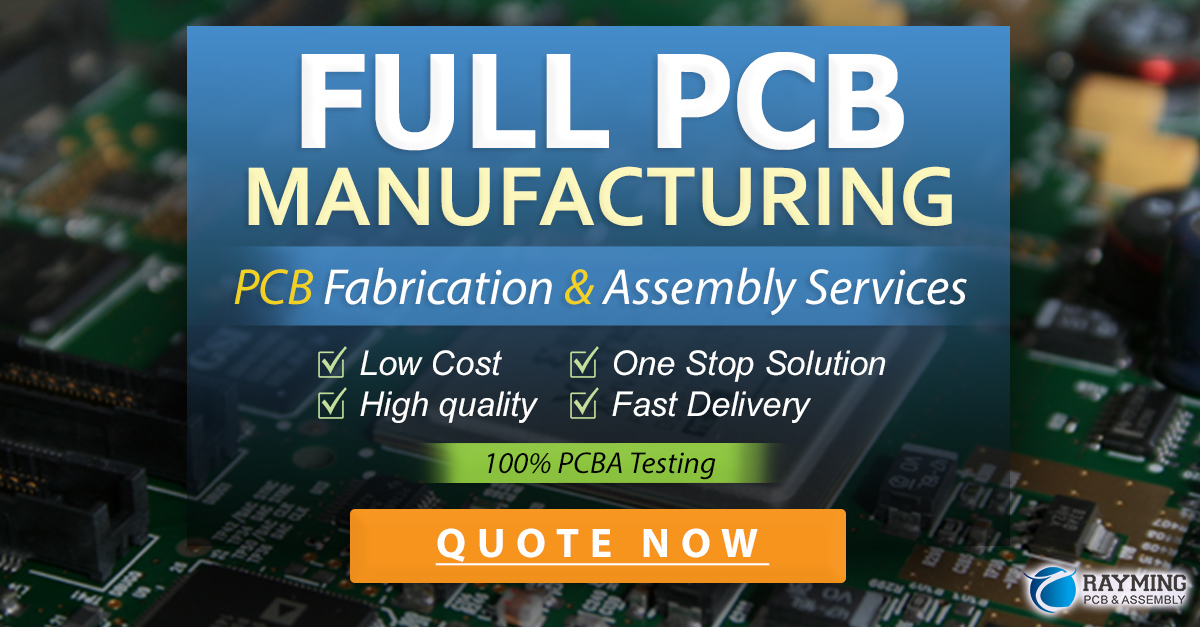
BGA Assembly Equipment
BGA assembly requires specialized equipment to ensure precise and consistent results. Some of the key pieces of equipment used in BGA assembly include:
Solder Paste Printer
A solder paste printer is used to apply solder paste to the PCB through a stencil. The printer must be capable of precise alignment and pressure control to ensure consistent solder paste deposits.
Pick-and-Place Machine
A pick-and-place machine is used to place the BGA component onto the PCB with high accuracy. The machine must have a vision system capable of aligning the component with the pads on the PCB and a placement head capable of handling the small and delicate BGA components.
Reflow Oven
A reflow oven is used to apply the controlled temperature profile required to melt the solder paste and form the solder joints. The oven must be capable of precise temperature control and uniform heating to ensure consistent solder joint formation.
Inspection Equipment
Inspection equipment is used to verify the quality of the solder joints after reflow. Automated optical inspection (AOI) systems and X-ray inspection systems are commonly used for BGA assembly inspection.
BGA Assembly Best Practices
To ensure reliable and consistent BGA assembly results, several best practices should be followed:
- Use high-quality materials: Use high-quality solder paste, PCBs, and components to ensure good solder joint formation and reliability.
- Follow manufacturer’s recommendations: Follow the manufacturer’s recommendations for solder paste printing, component placement, and reflow soldering to ensure optimal results.
- Use appropriate stencil design: Use a stencil with properly sized and shaped apertures to ensure consistent solder paste deposits.
- Optimize reflow profile: Carefully optimize the reflow temperature profile to ensure complete melting and wetting of the solder paste without damaging the components or the PCB.
- Perform regular maintenance: Regularly clean and maintain the solder paste printer, pick-and-place machine, and reflow oven to ensure consistent performance.
- Provide proper training: Provide proper training to operators and technicians to ensure they have the skills and knowledge necessary for successful BGA assembly.
Conclusion
BGA assembly is a critical capability for electronics manufacturers looking to produce high-density, high-performance devices. While BGA assembly presents several challenges, including thermal management, solder joint reliability, and rework and repair, these challenges can be overcome with the right equipment, materials, and processes. By following best practices and investing in the necessary equipment and training, electronics manufacturers can achieve reliable and consistent BGA assembly results.
Frequently Asked Questions (FAQ)
-
What is BGA assembly?
BGA (Ball Grid Array) assembly is the process of attaching a BGA component to a printed circuit board (PCB) using a grid of solder balls to form the electrical and mechanical connection. -
What are the advantages of BGA packaging?
BGA packaging offers several advantages, including high pin density, improved thermal and electrical performance, and reduced package size compared to other packaging technologies. -
What equipment is used in BGA assembly?
BGA assembly requires specialized equipment, including a solder paste printer, pick-and-place machine, reflow oven, and inspection equipment such as automated optical inspection (AOI) and X-ray systems. -
What are some of the challenges in BGA assembly?
Some of the challenges in BGA assembly include thermal management, solder joint reliability, and rework and repair. Proper design, materials selection, and process control are necessary to overcome these challenges. -
What are some best practices for BGA assembly?
Some best practices for BGA assembly include using high-quality materials, following manufacturer’s recommendations, using appropriate stencil design, optimizing the reflow profile, performing regular maintenance, and providing proper training to operators and technicians.
Advantage | Description |
---|---|
High pin density | BGA packages can accommodate a large number of interconnects in a small package size |
Improved thermal performance | The solder balls provide a low-resistance thermal path for better heat dissipation |
Better electrical performance | Short interconnects reduce inductance and improve signal integrity |
Reduced package size | BGA packages are typically smaller than equivalent through-hole or surface-mount packages |
Challenge | Description |
---|---|
Thermal management | High power densities in BGA packages can lead to thermal issues if not properly managed |
Solder joint reliability | Small size and close spacing of solder balls can make it difficult to achieve consistent and reliable solder joints |
Rework and repair | Special tools and techniques are required to remove and replace BGA components without damaging the PCB or adjacent components |
Leave a Reply