What Does PCB Stand For?
PCB stands for Printed Circuit Board. A PCB File contains all the data needed to design and manufacture a printed circuit board, including the schematic, component layout, trace routing, drill holes, and other specifications.
PCB files allow designers to digitally create and share Circuit Board Designs that can then be fabricated into physical boards. Understanding PCB files is essential for anyone involved in electronic product development.
Common PCB File Formats
There are several common file formats used for PCB design. Here are some of the most popular:
Format | Description |
---|---|
Gerber (GBR) | The standard format for PCB Fabrication data. Includes copper layers, solder mask, silk screen, and drill data as individual files. |
ODB++ | A unified, intelligent CAD-to-CAM data exchange format that contains all PCB fabrication data in a single file structure. |
IPC-2581 | An open, neutral format for exchanging PCB design data. Replaces multiple Gerber files with a single XML file. |
Eagle (.BRD) | The PCB design file format used by Autodesk Eagle, a popular PCB design tool. |
Altium (.PcbDoc) | The PCB design file format used by Altium Designer, a professional PCB Design Software. |
Each format has its own advantages and use cases. Gerber is the most widely supported by manufacturers, while newer formats like ODB++ and IPC-2581 provide more intelligent data packaging. Eagle and Altium’s formats are specific to those design tools.
Anatomy of a PCB File
So what exactly is contained in a PCB file? Let’s break down the key elements:
Schematic Data
The schematic shows the electrical connections between components in the circuit. This is typically drawn first before laying out the physical board. The schematic data includes:
- Component symbols and properties
- Net (connection) information
- Pin mappings to physical components
- Hierarchical blocks for multi-sheet designs
Board Outline and Layer Stackup
The board outline defines the physical shape and size of the PCB. The layer stackup specifies the arrangement of copper, insulating, and masking layers that make up the board. This includes:
- Board dimensions (length, width, thickness)
- Cutouts and holes
- Copper pour and keepout areas
- Layer types (signal, plane, mask, paste, silk)
- Layer thicknesses and materials
Component Placement
Component placement data specifies the physical location, orientation, and properties of parts on the board. This includes:
- Reference designators (e.g. R1, C2, U1)
- Footprints (land patterns)
- 3D models
- Assembly variants
- Placement coordinates and rotation
Copper Traces and Vias
Copper traces are the conductive paths that connect components together according to the schematic. Vias are holes that allow traces to pass between layers. Trace and via data includes:
- Trace widths, lengths, and layer assignments
- Via types (thru-hole, blind, buried)
- Via spans (layers connected) and drill sizes
- Teardrops, trace smoothing, and other optimizations
Drill Data
Drill data specifies all the holes that need to be drilled in the board, including:
- Plated holes for vias and thru-hole component pins
- Non-plated holes for mounting or other mechanical purposes
- Hole sizes, types (round, square, slotted), and locations
Silkscreen and Fabrication Notes
The silkscreen is the text and graphics printed on the PCB for assembly and identification purposes. Fabrication notes provide additional instructions for the manufacturer. These include:
- Reference designators
- Polarity and pin 1 indicators
- Assembly instructions
- Tooling marks and fiducials
- Parametric data (e.g. Track Width, clearances)
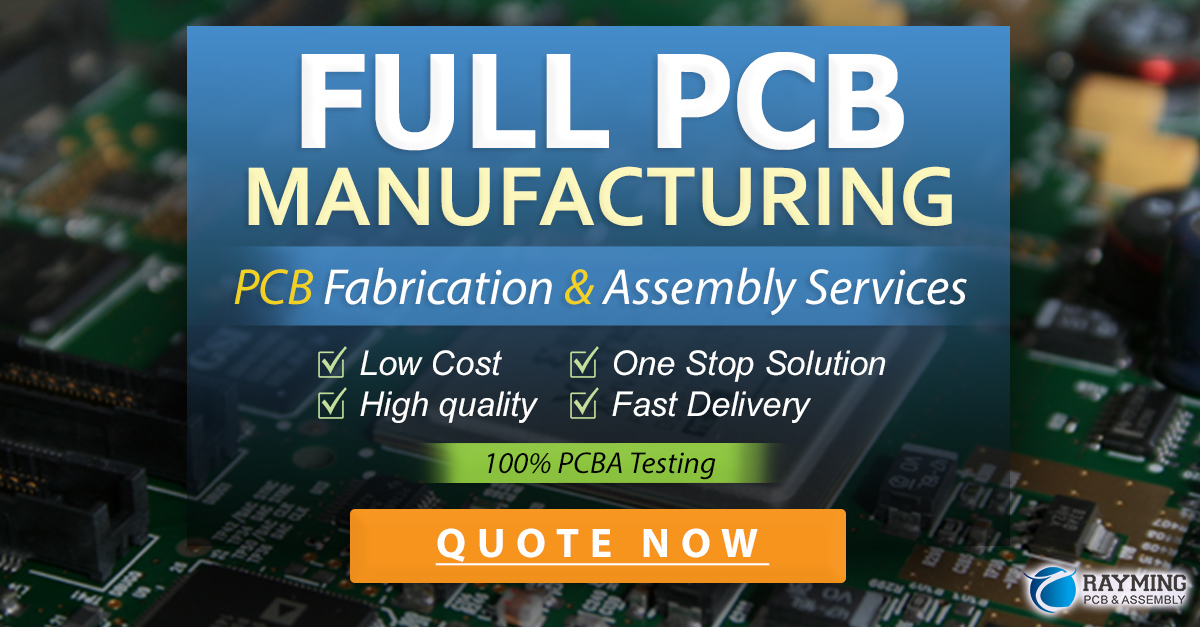
PCB Design Rules and Constraints
Creating a manufacturable PCB file requires adhering to various design rules and constraints. These ensure the board can be reliably fabricated and assembled. Key considerations include:
Electrical Rules
- Schematic connectivity – ensuring all nets are complete and properly connected
- Electrical clearances – minimum spacing between traces, pads, and planes to prevent short circuits
- Controlled impedance – maintaining consistent trace impedance for high-speed signals
Physical Rules
- Trace width and spacing – minimum trace sizes and clearances based on the fabrication process
- Via and pad sizes – minimum drill hole and annular ring dimensions
- Copper-to-edge clearance – preventing traces from being too close to the board edge
Manufacturing Rules
- Minimum feature sizes – the smallest traces, spaces, and drill holes a fabricator can reliably produce
- Aspect ratio – the ratio of a drilled hole’s depth to its diameter
- Solder mask and silkscreen clearances – preventing overlap between copper, mask, and legend layers
Following these rules helps ensure your PCB file will result in a board that functions as intended and can be efficiently manufactured.
PCB File Generators
Most PCB design software includes tools for generating the various output files needed for fabrication and assembly. These file generators take the board layout data and export it into standard formats like Gerber, drill, and pick-and-place files.
Here are some key file types produced by PCB file generators:
File Type | Description |
---|---|
Gerber (RS-274X) | Individual files for each copper, mask, and legend layer, plus drill data. |
NC Drill | Numeric control (NC) files specifying drill locations, sizes, and plunge depths. |
IPC-D-356 | A netlist format associating component pins with their corresponding nets and vias. |
Pick and Place | A file specifying the placement locations and rotations of components for automated assembly. |
BOM | Bill of Materials file listing all components used in the design, along with quantities and suppliers. |
Most generators allow you to customize file output settings, like selecting which layers to export, choosing drill data formats, and specifying file naming conventions. It’s important to communicate with your manufacturer to ensure you’re providing the file types and formats they require.
Best Practices for Creating PCB Files
To create high-quality, manufacturable PCB files, follow these best practices:
-
Start with a clean schematic – Ensure your schematic is complete, accurate, and follows good design practices before starting the PCB layout.
-
Use a consistent grid – Set up a grid that aligns with your manufacturer’s capabilities and stick to it for component placement and routing.
-
Keep it simple – Avoid unnecessary complexity in your layout. Use the fewest number of layers possible and minimize the use of blind and buried vias.
-
Plan for manufacturing – Communicate with your manufacturer early and often to understand their capabilities and constraints. Design with their process in mind.
-
Follow design rules – Use your CAD tool’s design rule checking (DRC) features to catch violations early. Regularly run batch DRCs and address warnings promptly.
-
Verify your outputs – Carefully review your generated output files to ensure they match your design intent. Use a Gerber viewer to check copper, mask, and drill layers.
-
Communicate clearly – Provide your manufacturer with clear, complete documentation including drawings, specifications, and any special instructions. Err on the side of over-communication.
By following these guidelines, you’ll be well on your way to creating robust, reliable PCB files that result in successful boards.
FAQ
What software is used to create PCB files?
There are many PCB design software options available, ranging from free, open-source tools to professional, high-end CAD packages. Some popular choices include:
- KiCad (free and open-source)
- Eagle (affordable, widely used for hobbyists and small businesses)
- Altium Designer (professional-grade, feature-rich)
- OrCAD (professional, part of the Cadence design suite)
The right choice depends on your budget, experience level, and the complexity of your designs.
How do I choose the right PCB file format?
When deciding on a PCB file format, consider:
- Your design software’s native file format and export options
- Your manufacturer’s accepted and preferred file formats
- The complexity of your design (e.g. whether you need intelligent data formats)
- Compatibility with other tools and processes in your workflow
When in doubt, Gerber RS-274X is the safest choice, as it is the most widely accepted industry standard. But more intelligent formats like ODB++ and IPC-2581 are gaining traction and offer advantages for more complex designs.
What is a Gerber file?
A Gerber file is a standard file format used to describe the printed circuit board images copper layers, solder mask, legend, etc.) It is the most common data input format for PCB fabrication.
Gerber files are typically produced as RS-274X files. In a typical PCB design, a separate Gerber file will be produced for each layer of the board. These individual files are then bundled together into a single archive file (e.g. ZIP) for transfer to the manufacturer.
What are the most common PCB file errors?
Some of the most common errors found in PCB files include:
-
Incorrect or missing Gerber files – Not all necessary layer files are included, or files are incorrectly named/formatted.
-
Drill errors – Drill files are missing, incorrectly formatted, or contain invalid drill sizes/locations.
-
Clearance violations – Traces or components are placed too close together, violating manufacturing constraints.
-
Incomplete or inaccurate BOM – Bill of Materials files are missing components or contain incorrect part numbers or quantities.
-
Silkscreen issues – Silkscreen text overlaps with pads or violates clearance rules.
Many of these errors can be caught and corrected by carefully reviewing your design and running DRCs before generating output files. It’s also a good idea to use a Gerber viewer to visually inspect your files before sending them to your manufacturer.
How can I ensure my PCB files are manufacturable?
To create manufacturable PCB files:
-
Communicate early and often with your manufacturer to understand their capabilities and constraints.
-
Design with the manufacturing process in mind, adhering to your manufacturer’s design rules and guidelines.
-
Use your CAD tools’ DRC and rule-checking features to verify your design and catch errors.
-
Generate complete, accurate output files in the formats required by your manufacturer.
-
Carefully review your design and output files, using Gerber viewers and other tools to visually inspect them.
-
Provide your manufacturer with clear, complete documentation and instructions.
By working closely with your manufacturer and following best practices for PCB design and file generation, you can ensure your files will result in a successful, manufacturable board.
Leave a Reply