Introduction to Multilayer PCB Manufacturing
Multilayer PCB manufacturing is a complex process that involves the fabrication of printed circuit boards with three or more conductive layers. These boards are essential components in modern electronic devices, as they allow for the efficient routing of electrical signals and the integration of multiple components in a compact space. With the increasing demand for high-performance electronics, multilayer PCB manufacturing has become a critical technology in the electronics industry.
The Need for Multilayer PCBs
As electronic devices become more advanced and compact, the need for multilayer PCBs has grown significantly. These boards offer several advantages over traditional single or double-layer PCBs, including:
- Increased circuit density
- Improved signal integrity
- Reduced electromagnetic interference (EMI)
- Better thermal management
- Enhanced mechanical stability
Applications of Multilayer PCBs
Multilayer PCBs find applications in a wide range of industries, including:
- Consumer electronics (smartphones, tablets, laptops)
- Automotive electronics (infotainment systems, advanced driver assistance systems)
- Medical devices (imaging equipment, patient monitoring systems)
- Aerospace and defense (avionics, radar systems)
- Telecommunications (routers, switches, base stations)
The Multilayer PCB Manufacturing Process
The manufacturing process for multilayer PCBs is a multi-step procedure that requires precision and attention to detail. The following sections outline the key steps involved in the fabrication of these complex boards.
1. Design and Layout
The first step in multilayer PCB manufacturing is the design and layout of the circuit. This process involves the use of specialized software tools to create a digital representation of the board, including the placement of components, the routing of traces, and the definition of layer stackups. The design must adhere to various industry standards and guidelines to ensure compatibility and reliability.
2. Material Selection
The choice of materials for multilayer PCBs is crucial, as it directly impacts the performance and reliability of the finished product. The most common base material for multilayer PCBs is FR-4, a glass-reinforced epoxy laminate. Other materials, such as polyimide or PTFE, may be used for high-frequency or high-temperature applications.
3. Inner Layer Fabrication
Once the design is finalized and the materials are selected, the inner layers of the multilayer PCB are fabricated. This process involves the following steps:
- Copper clad laminate is cut to size
- Photoresist is applied to the copper surface
- The circuit pattern is exposed onto the photoresist using UV light
- The exposed photoresist is developed, revealing the copper to be etched
- The unwanted copper is etched away, leaving the desired circuit pattern
- The remaining photoresist is stripped away
4. Lamination
After the inner layers are fabricated, they are stacked and aligned according to the design specifications. Pre-preg, a partially cured glass-reinforced epoxy material, is placed between the layers to act as an insulating and bonding agent. The stack is then subjected to high pressure and temperature in a lamination press, fusing the layers together to form a solid board.
5. Drilling
Once the board is laminated, holes are drilled through the board to accommodate component leads and vias. The drilling process is typically performed using computer-controlled drilling machines, which ensure precise hole placement and size.
6. Plating and Copper Deposition
After drilling, the holes are plated with copper to create electrical connections between layers. This process involves the following steps:
- The board is cleaned and activated to promote adhesion
- A thin layer of electroless copper is deposited onto the board and hole walls
- Additional copper is electroplated onto the board to achieve the desired thickness
7. Outer Layer Patterning
With the inner layers and plated holes complete, the outer layers of the multilayer PCB are patterned using a process similar to that used for the inner layers. This involves the application of photoresist, exposure, development, and etching of the copper.
8. Solder Mask Application
A solder mask, a protective coating that prevents solder bridging and short circuits, is applied to the outer layers of the board. The solder mask is typically a green or black epoxy-based material that is screen printed or photoimaged onto the board.
9. Surface Finishing
To enhance solderability and protect the exposed copper, a surface finish is applied to the multilayer PCB. Common surface finishes include:
- Hot Air Solder Leveling (HASL)
- Electroless Nickel Immersion Gold (ENIG)
- Immersion Silver
- Immersion Tin
- Organic Solderability Preservative (OSP)
10. Electrical Testing
Before the multilayer PCB is deemed ready for use, it undergoes rigorous electrical testing to ensure functionality and reliability. This includes tests for continuity, insulation resistance, and impedance control.
Challenges in Multilayer PCB Manufacturing
While multilayer PCB manufacturing offers numerous benefits, it also presents several challenges that must be addressed to ensure the production of high-quality boards.
Signal Integrity
As the number of layers in a multilayer PCB increases, so does the complexity of maintaining signal integrity. Factors such as crosstalk, impedance mismatch, and EMI can degrade signal quality and lead to performance issues. To mitigate these problems, careful design and layout techniques must be employed, such as the use of ground planes, shielding, and controlled impedance traces.
Thermal Management
Multilayer PCBs often have a higher component density than single or double-layer boards, which can lead to increased heat generation. Proper thermal management is essential to prevent overheating and ensure the longevity of the board and its components. This can be achieved through the use of thermal vias, heat sinks, and careful component placement.
Manufacturing Complexity
As the number of layers in a multilayer PCB increases, so does the manufacturing complexity. This can lead to longer lead times, higher costs, and a greater risk of defects. To minimize these issues, manufacturers must employ strict Quality Control measures and invest in advanced equipment and processes.
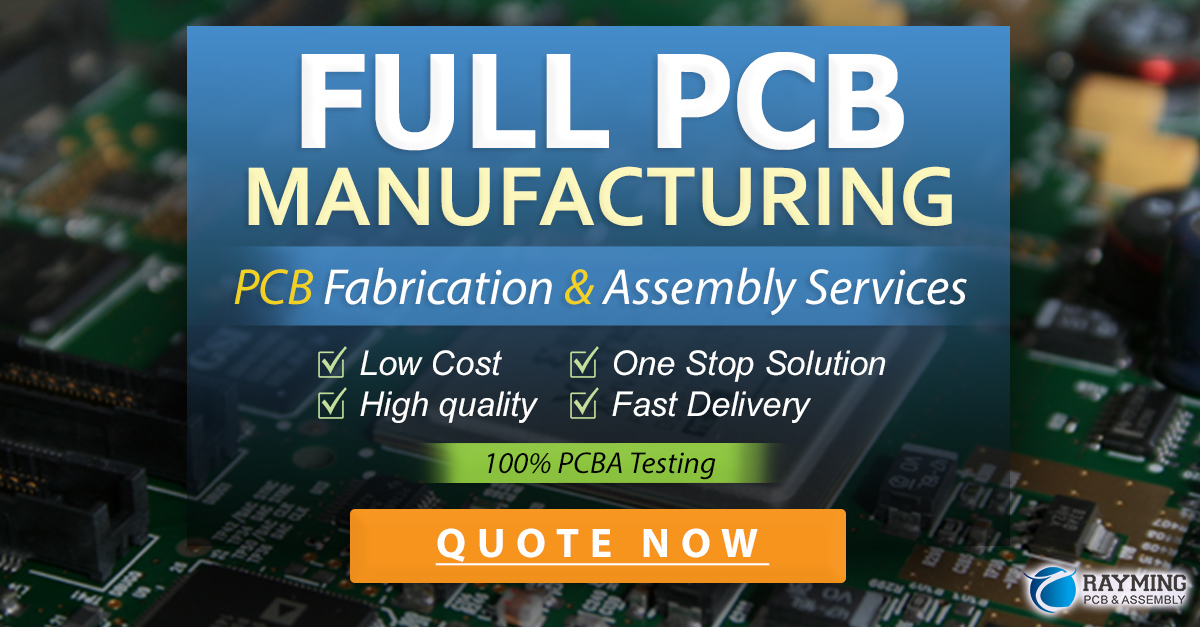
One-Stop Multilayer PCB Manufacturing Solutions
To address the challenges associated with multilayer PCB manufacturing, many companies now offer one-stop solutions that streamline the entire process from design to production.
Benefits of One-Stop Multilayer PCB Manufacturing
One-stop multilayer PCB manufacturing offers several advantages, including:
- Reduced lead times
- Lower costs
- Improved quality control
- Enhanced communication and collaboration
- Access to specialized expertise and equipment
Services Offered by One-Stop Multilayer PCB Manufacturers
One-stop multilayer PCB manufacturers typically offer a comprehensive range of services, including:
- PCB Design and layout
- Material selection and sourcing
- Prototyping and small-batch production
- High-volume manufacturing
- Electrical testing and quality control
- Assembly and packaging
By working with a one-stop manufacturer, companies can streamline their supply chain, reduce costs, and ensure the timely delivery of high-quality multilayer PCBs.
Frequently Asked Questions (FAQ)
- What is the maximum number of layers that can be achieved in multilayer PCB manufacturing?
-
Most multilayer PCB manufacturers can produce boards with up to 64 layers. However, the maximum number of layers achievable depends on the specific manufacturer’s capabilities and the design requirements of the board.
-
What is the typical turnaround time for multilayer PCB manufacturing?
-
The turnaround time for multilayer PCB manufacturing varies depending on the complexity of the board, the number of layers, and the manufacturer’s workload. Typical lead times range from 2-3 weeks for standard designs to 4-6 weeks for more complex boards.
-
How does the cost of multilayer PCBs compare to single or double-layer boards?
-
Multilayer PCBs are generally more expensive than single or double-layer boards due to the increased complexity of the manufacturing process and the cost of materials. However, the cost per unit decreases as the order quantity increases, making multilayer PCBs more cost-effective for high-volume production.
-
What are the most common materials used in multilayer PCB manufacturing?
-
The most common base material for multilayer PCBs is FR-4, a glass-reinforced epoxy laminate. Other materials, such as polyimide or PTFE, may be used for high-frequency or high-temperature applications.
-
What are the key considerations when designing a multilayer PCB?
- When designing a multilayer PCB, key considerations include signal integrity, thermal management, manufacturability, and cost. Designers must carefully plan the layer stackup, component placement, and routing to ensure optimal performance and reliability while adhering to industry standards and guidelines.
Conclusion
Multilayer PCB manufacturing is a complex process that requires expertise, precision, and advanced equipment. By understanding the key steps involved in the manufacturing process, the challenges associated with multilayer PCBs, and the benefits of one-stop manufacturing solutions, companies can make informed decisions when sourcing these critical components for their electronic devices. As the demand for high-performance electronics continues to grow, multilayer PCB manufacturing will remain a vital technology in the industry, driving innovation and enabling the development of ever more advanced and compact devices.
Number of Layers | Typical Applications | Relative Cost |
---|---|---|
3-4 | Simple consumer electronics, basic industrial devices | Low |
6-8 | Advanced consumer electronics, automotive, medical | Medium |
10-12 | High-performance computing, telecommunications | High |
14+ | Aerospace, defense, specialized applications | Very High |
Leave a Reply