Introduction to Printed Circuit Boards (PCBs)
A Printed Circuit Board (PCB) is a fundamental component in modern electronics. It serves as the backbone of almost all electronic devices, from simple gadgets like calculators to complex systems such as computers and smartphones. PCBs provide a platform for electrical components to be mounted and interconnected, enabling the efficient functioning of electronic circuits.
What is a PCB?
A PCB is a flat board made of insulating materials, such as fiberglass or composite epoxy, with conductive pathways etched or printed onto its surface. These conductive pathways, known as traces or tracks, are typically made of copper and serve to electrically connect the various components mounted on the board.
The Importance of PCBs in Electronics
PCBs have revolutionized the electronics industry by providing a reliable and efficient means of assembling electronic circuits. They offer several advantages over traditional point-to-point wiring:
- Compact size: PCBs allow for the miniaturization of electronic devices by providing a dense layout for components.
- Reliability: The structured layout and robust construction of PCBs ensure better electrical connections and reduced chances of short circuits or loose connections.
- Mass production: PCBs can be easily designed and manufactured in large quantities, making them cost-effective for mass production.
- Reproducibility: PCB designs can be easily replicated, ensuring consistency across multiple units of the same device.
PCB Manufacturing Process
The manufacturing process of PCBs involves several stages, each requiring precision and attention to detail. The following are the main steps involved in PCB manufacturing:
1. PCB Design
The first step in creating a PCB is designing the circuit schematic and layout using specialized software such as Altium Designer, Eagle, or KiCad. The design process involves the following sub-steps:
a. Schematic capture: The electronic circuit is created as a schematic diagram, representing the components and their interconnections.
b. Component placement: The components are positioned on the virtual board layout, considering factors such as size, shape, and proximity to other components.
c. Routing: The conductive traces are designed to connect the components according to the schematic, while adhering to design rules and constraints.
d. Design verification: The design is checked for errors, such as short circuits, incomplete connections, or violations of manufacturing constraints.
2. PCB Fabrication
Once the PCB design is finalized, the physical board is fabricated using the following steps:
a. Printing: The PCB design is printed onto a photosensitive film or directly onto the copper-clad board using a plotter or laser printer.
b. Exposure: The photosensitive film or board is exposed to UV light, hardening the areas that will form the conductive traces.
c. Etching: The unexposed areas of the copper layer are chemically etched away, leaving behind the desired conductive traces.
d. Drilling: Holes are drilled through the board to accommodate through-hole components and provide interconnections between layers in multi-layer PCBs.
e. Plating: The holes are plated with copper to ensure electrical continuity between layers.
f. Solder mask application: A protective layer, known as the solder mask, is applied to the board, exposing only the areas where components will be soldered.
g. Silkscreen printing: Text, symbols, and logos are printed onto the board using a silkscreen process for identification and assembly purposes.
3. PCB Assembly
After the bare PCB is fabricated, the electronic components are mounted onto the board using either through-hole or surface-mount technology (SMT).
a. Through-hole assembly: Components with long leads are inserted through the holes in the PCB and soldered onto the opposite side.
b. Surface-mount assembly: Components with small leads or contact pads are placed directly onto the surface of the PCB and soldered in place.
c. Reflow soldering: For SMT assembly, the board is heated in a reflow oven, melting the solder paste and creating a permanent connection between the components and the board.
d. Inspection: The assembled PCB is inspected for quality control, ensuring proper component placement, soldering, and functionality.
Types of PCBs
PCBs can be categorized based on various factors, such as the number of layers, material, and assembly technology. The following are some common types of PCBs:
1. Single-Layer PCBs
Single-layer PCBs have conductive traces on only one side of the insulating substrate. They are the simplest and most cost-effective type of PCB, suitable for low-complexity circuits.
2. Double-layer PCBs
Double-layer PCBs have conductive traces on both sides of the insulating substrate, allowing for more complex circuits and higher component density compared to single-layer PCBs.
3. Multi-layer PCBs
Multi-layer PCBs consist of three or more conductive layers separated by insulating layers. They offer the highest component density and are used in complex electronic devices, such as smartphones, computers, and aerospace systems.
Number of Layers | Advantages | Disadvantages |
---|---|---|
Single-layer | – Low cost – Simple design – Quick fabrication |
– Limited circuit complexity – Low component density |
Double-layer | – Increased circuit complexity – Higher component density |
– Higher cost than single-layer – More design effort |
Multi-layer | – High circuit complexity – Highest component density – Compact size |
– Highest cost – Complex design and fabrication process |
4. Rigid PCBs
Rigid PCBs are made using a solid, non-flexible insulating substrate, such as fiberglass-reinforced epoxy. They are the most common type of PCB and are used in a wide range of electronic devices.
5. Flexible PCBs
Flexible PCBs (FPCBs) are made using a flexible insulating substrate, such as polyimide or polyester. They can bend and conform to various shapes, making them suitable for applications with limited space or moving parts, such as cameras, wearable devices, and automotive electronics.
6. Rigid-Flex PCBs
Rigid-Flex PCBs combine the features of rigid and flexible PCBs, consisting of both rigid and flexible sections. They offer the benefits of both types, allowing for compact and complex designs with improved reliability and reduced assembly costs.
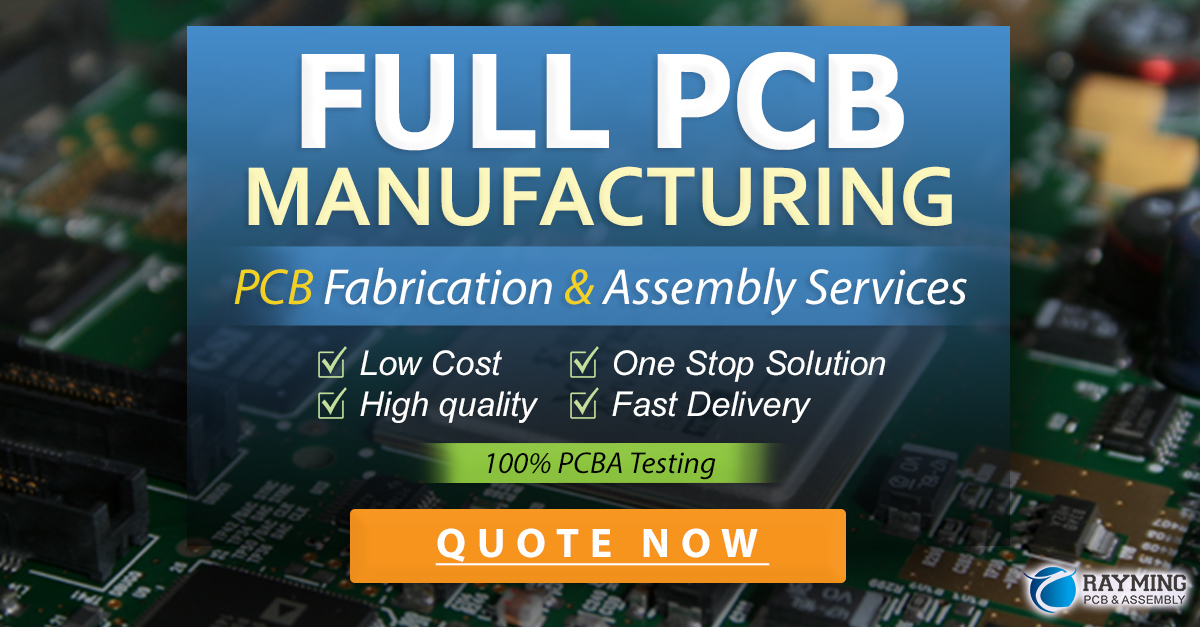
PCB Design Considerations
Designing a PCB involves various considerations to ensure optimal performance, reliability, and manufacturability. Some key factors to consider when designing a PCB include:
1. Component Selection
Choosing the right components for a PCB is crucial for its functionality and reliability. Factors to consider when selecting components include:
a. Functionality: Ensure that the chosen components meet the requirements of the circuit and are compatible with each other.
b. Package size: Consider the physical size of the components and their compatibility with the available space on the PCB.
c. Power requirements: Ensure that the power supply and power management components are adequate for the circuit’s needs.
d. Environmental factors: Select components that can withstand the expected operating conditions, such as temperature, humidity, and vibration.
2. Signal Integrity
Maintaining signal integrity is essential for ensuring reliable communication between components on a PCB. Some techniques for improving signal integrity include:
a. Proper trace routing: Minimize the length of traces and avoid sharp bends or corners to reduce signal reflections and crosstalk.
b. Impedance matching: Ensure that the impedance of traces matches the impedance of the components and connectors to minimize signal reflections.
c. Ground and power planes: Use solid ground and power planes to provide a low-impedance return path for signals and minimize noise.
d. Shielding: Use shielding techniques, such as grounded copper pours or shielded cables, to reduce electromagnetic interference (EMI) and crosstalk.
3. Thermal Management
Effective thermal management is crucial for preventing overheating and ensuring the long-term reliability of a PCB. Some techniques for managing heat on a PCB include:
a. Component placement: Position heat-generating components away from sensitive components and provide adequate spacing for heat dissipation.
b. Copper pours: Use large copper pours connected to ground or power planes to spread heat evenly across the board.
c. Thermal vias: Use thermal vias to transfer heat from components to the opposite side of the board or to internal layers in multi-layer PCBs.
d. Heatsinks and fans: Use heatsinks and fans to dissipate heat from high-power components, such as processors or power transistors.
4. Manufacturing Constraints
Designing a PCB that is easy to manufacture helps reduce costs and improve reliability. Some manufacturing constraints to consider include:
a. Minimum trace width and spacing: Adhere to the minimum trace width and spacing specifications provided by the PCB manufacturer to ensure reliable fabrication.
b. Drill hole size: Ensure that the drill hole sizes for through-hole components and vias are compatible with the manufacturer’s capabilities.
c. Solder mask and silkscreen: Provide adequate clearance between components, traces, and solder mask openings to ensure proper solder mask application and legibility of silkscreen markings.
d. Panelization: Consider panelizing multiple PCBs on a single panel to reduce fabrication costs, but ensure proper spacing and routing between individual boards.
PCB Testing and Inspection
After a PCB is manufactured and assembled, it must undergo various tests and inspections to ensure its functionality, reliability, and conformance to specifications. Some common testing and inspection methods include:
1. Visual Inspection
Visual inspection is the first step in assessing the quality of a PCB. It involves examining the board for visible defects, such as:
a. Component placement: Check for missing, misaligned, or incorrect components.
b. Soldering: Look for poor soldering, bridging, or insufficient solder coverage.
c. Trace integrity: Check for broken, shorted, or incomplete traces.
d. Cleanliness: Ensure the board is free from contaminants, such as flux residue or foreign particles.
2. Automated Optical Inspection (AOI)
AOI uses computer vision and image processing techniques to automatically inspect PCBs for defects. It can detect a wide range of issues, such as component placement errors, solder defects, and trace anomalies, with high speed and accuracy.
3. X-ray Inspection
X-ray inspection is used to examine the internal structure of a PCB, particularly for defects in ball grid array (BGA) packages or multi-layer boards. It can detect issues such as voids in solder joints, broken wire bonds, or misaligned components.
4. In-Circuit Testing (ICT)
ICT involves using a bed-of-nails fixture to make electrical contact with specific points on the PCB and testing the functionality of individual components and circuits. It can detect issues such as incorrect component values, short circuits, or open connections.
5. Functional Testing
Functional testing involves powering up the PCB and testing its overall functionality and performance. It may include:
a. Boundary scan testing: Using built-in test access ports (TAPs) to test the interconnections between components.
b. Firmware testing: Loading and running the device’s firmware to ensure proper operation.
c. Environmental testing: Subjecting the PCB to various environmental conditions, such as temperature, humidity, or vibration, to assess its reliability and durability.
Future Trends in PCB Technology
As electronic devices continue to advance, so do the technologies and techniques used in PCB design and manufacturing. Some emerging trends in PCB technology include:
1. High-Density Interconnect (HDI) PCBs
HDI PCBs feature finer trace widths, smaller vias, and higher component density than traditional PCBs. They enable the creation of more compact and complex electronic devices, such as smartphones, wearables, and IoT devices.
2. Embedded Components
Embedded components, such as resistors, capacitors, and even active components, are integrated directly into the layers of a PCB. This technique saves space, reduces the number of solder joints, and improves signal integrity.
3. 3D Printing
3D printing technology is being explored for the fabrication of PCBs, allowing for the creation of complex, three-dimensional structures and the integration of electronics into non-planar surfaces.
4. Flexible and Stretchable Electronics
Advances in materials science and manufacturing techniques are enabling the development of flexible and stretchable PCBs that can conform to various shapes and withstand repeated bending or stretching. These PCBs have applications in wearable devices, medical implants, and soft robotics.
5. Sustainable and Eco-Friendly Materials
There is a growing focus on developing sustainable and eco-friendly materials for PCB manufacturing, such as biodegradable substrates, lead-free solders, and halogen-free flame retardants. These materials aim to reduce the environmental impact of electronic waste and comply with evolving regulations.
Frequently Asked Questions (FAQ)
1. What is the difference between a PCB and a breadboard?
A breadboard is a temporary prototyping tool used to quickly assemble and test electronic circuits without soldering. In contrast, a PCB is a permanent, custom-designed board that provides a reliable and compact platform for electronic components.
2. Can I design my own PCB?
Yes, with the help of PCB design software and some basic knowledge of electronic circuits, you can design your own PCB. However, it is essential to adhere to design guidelines and manufacturing constraints to ensure a successful outcome.
3. How long does it take to manufacture a PCB?
The manufacturing time for a PCB depends on various factors, such as the complexity of the design, the chosen fabrication house, and the required quantity. Typically, the turnaround time ranges from a few days to several weeks.
4. What is the minimum trace width and spacing for a PCB?
The minimum trace width and spacing depend on the PCB manufacturer’s capabilities and the chosen fabrication technology. Common minimum trace widths range from 0.1 mm to 0.2 mm, while minimum spacing ranges from 0.1 mm to 0.15 mm. However, these values can vary depending on the specific requirements of the project.
5. How can I reduce the cost of PCB manufacturing?
Some ways to reduce the cost of PCB manufacturing include:
– Minimizing the board size and layer count
– Using standard materials and components
– Adhering to the manufacturer’s design guidelines
– Ordering larger quantities to benefit from economies of scale
– Choosing a cost-effective fabrication house with good reputation
Conclusion
Printed Circuit Boards (PCBs) are the foundation of modern electronics, providing a reliable and efficient means of interconnecting electronic components. Understanding the fundamentals of PCBs, including their manufacturing process, types, design considerations, and testing methods, is crucial for anyone involved in electronic product development.
As PCB technology continues to evolve, it is essential to stay updated with the latest trends and techniques, such as HDI PCBs, embedded components, and flexible electronics. By leveraging these advancements and following best practices in PCB design and manufacturing, engineers and hobbyists can create innovative, reliable, and cost-effective electronic devices that shape our future.
Leave a Reply