Introduction to BOM
A Bill of Materials (BOM) is a comprehensive list of components, parts, and materials required to manufacture a product. In the context of Printed Circuit Board (PCB) assembly, a BOM is a crucial document that provides a detailed list of all the components needed to assemble a PCB. It serves as a guide for the PCB Assembly process, ensuring that all necessary components are available and correctly specified.
Importance of BOM in PCB Assembly
The BOM plays a vital role in the PCB assembly process for several reasons:
- Accuracy: A well-prepared BOM ensures that the correct components are used during the assembly process, minimizing the risk of errors and rework.
- Efficiency: By providing a clear and organized list of components, a BOM streamlines the assembly process, reducing the time and effort required to gather and manage components.
- Cost control: An accurate BOM helps in estimating the cost of the PCB assembly project, allowing for better budgeting and cost control.
- Supply chain management: The BOM facilitates effective communication between the PCB designer, the assembly team, and the component suppliers, ensuring that all parties have a clear understanding of the required components.
Types of BOM
There are several types of BOMs used in the PCB assembly process, each serving a specific purpose:
1. Engineering BOM (EBOM)
An Engineering BOM, also known as a Design BOM, is created by the PCB designer during the design phase. It includes all the components and their specifications as per the design requirements. The EBOM is typically used for prototyping and testing purposes.
2. Manufacturing BOM (MBOM)
A Manufacturing BOM, also called a Production BOM, is derived from the EBOM and is tailored for the manufacturing process. It includes additional information such as part numbers, suppliers, and assembly instructions. The MBOM is used by the assembly team to procure components and assemble the PCB.
3. Configurable BOM (CBOM)
A Configurable BOM is used for products that have multiple configurations or variants. It allows for the creation of different BOMs based on the specific configuration of the product. CBOMs are commonly used in industries where customization is prevalent, such as in the automotive or telecommunications sectors.
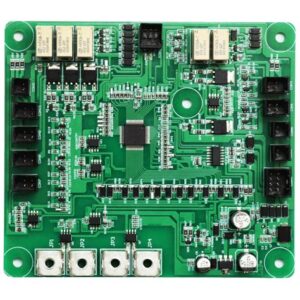
Essential Elements of a BOM
A comprehensive BOM should include the following essential elements:
- Part Number: A unique identifier for each component, usually assigned by the manufacturer.
- Description: A brief description of the component, including its function and key characteristics.
- Quantity: The number of each component required for the assembly of one PCB.
- Manufacturer: The name of the component manufacturer.
- Manufacturer Part Number: The manufacturer’s unique identifier for the component.
- Reference Designator: The reference designator assigned to the component on the PCB Schematic and layout.
- Footprint: The physical dimensions and shape of the component, which determines how it will be mounted on the PCB.
- Value: The electrical value of the component, such as resistance, capacitance, or voltage rating.
- Tolerance: The acceptable range of variation in the component’s value.
- Supplier: The name of the supplier from whom the component will be procured.
- Supplier Part Number: The supplier’s unique identifier for the component.
Here’s an example of a BOM table:
Part Number | Description | Quantity | Manufacturer | Manufacturer Part Number | Reference Designator | Footprint | Value | Tolerance | Supplier | Supplier Part Number |
---|---|---|---|---|---|---|---|---|---|---|
1 | Resistor | 10 | ABC Inc. | ABC-123 | R1, R2, R3 | 0805 | 10K | 1% | XYZ Corp | XYZ-10K-0805 |
2 | Capacitor | 5 | DEF Co. | DEF-456 | C1, C2 | 1206 | 10uF | 10% | UVW Ltd | UVW-10uF-1206 |
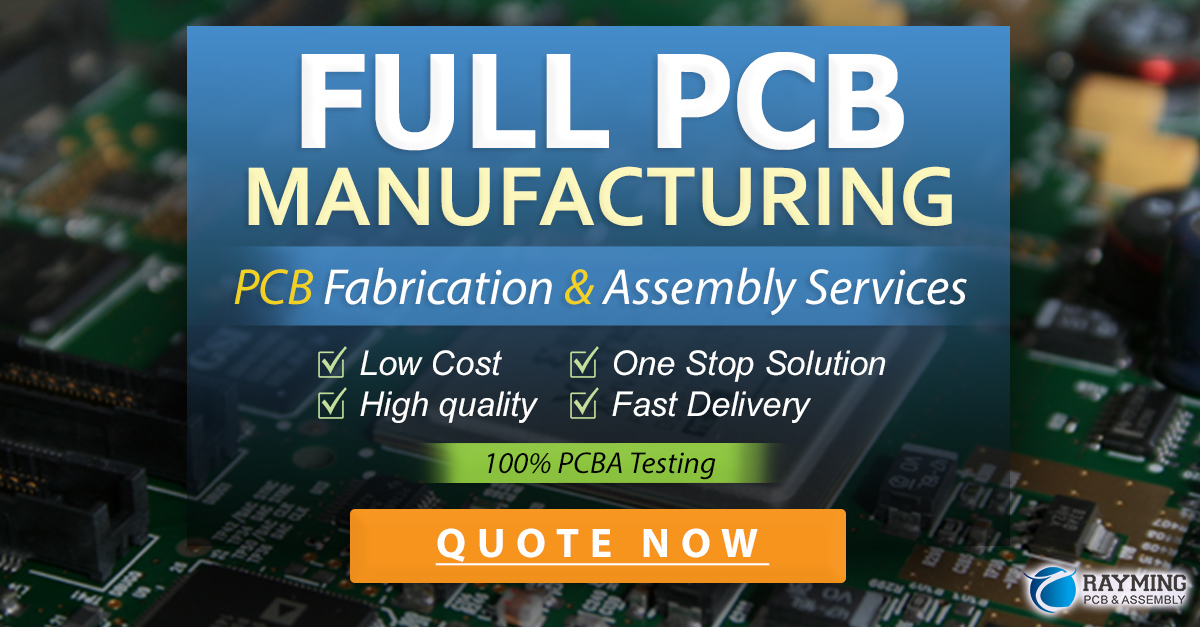
BOM Management Best Practices
To ensure an efficient and accurate PCB assembly process, follow these best practices for BOM management:
- Use a consistent format: Establish a standard format for your BOM and use it consistently across all projects. This helps in maintaining clarity and reducing confusion.
- Keep it updated: Regularly update the BOM as the design evolves or component information changes. An outdated BOM can lead to delays and errors in the assembly process.
- Collaborate with stakeholders: Involve all relevant stakeholders, such as the design team, procurement team, and assembly team, in the BOM creation and review process. This ensures that all necessary information is included and validated.
- Verify component availability: Before finalizing the BOM, check the availability of components with suppliers. This helps in identifying potential supply chain issues and allows for timely resolution.
- Use automated tools: Consider using BOM management software or tools that integrate with your PCB Design Software. These tools can help in automating the BOM creation process, reducing manual errors, and ensuring consistency.
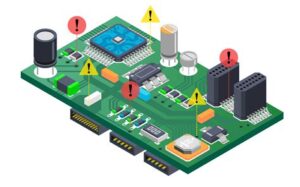
Common BOM Mistakes to Avoid
To minimize issues during the PCB assembly process, avoid these common BOM mistakes:
- Incomplete or inaccurate information: Ensure that all necessary information, such as part numbers, quantities, and specifications, is included and accurate in the BOM.
- Inconsistent formatting: Maintain a consistent format throughout the BOM to avoid confusion and misinterpretation.
- Using obsolete or end-of-life components: Verify that the components specified in the BOM are currently available and not obsolete or nearing end-of-life. Using obsolete components can lead to supply chain issues and delays.
- Lack of version control: Implement a version control system for your BOM to track changes and ensure that all team members are working with the latest version.
- Not considering alternative components: Include alternative or substitute components in the BOM, especially for critical or hard-to-source components. This helps in mitigating supply chain risks and ensuring timely assembly.
Conclusion
A well-prepared and managed BOM is essential for a successful PCB assembly project. By understanding the different types of BOMs, including essential elements, and following best practices, you can ensure that your PCB assembly process is efficient, accurate, and cost-effective. Remember to collaborate with all stakeholders, keep the BOM updated, and use automated tools to streamline the BOM management process.
Frequently Asked Questions (FAQ)
- What is the difference between an EBOM and an MBOM?
An Engineering BOM (EBOM) is created during the design phase and includes all the components as per the design requirements. A Manufacturing BOM (MBOM) is derived from the EBOM and includes additional information specific to the manufacturing process, such as part numbers and supplier information. - How often should I update my BOM?
It is recommended to update your BOM whenever there are changes in the design, component specifications, or supplier information. Regularly updating the BOM ensures that all team members have access to the latest information and helps in avoiding assembly errors and delays. - What is the purpose of a reference designator in a BOM?
A reference designator is a unique identifier assigned to each component on the PCB schematic and layout. It helps in locating the component on the PCB and is used in the assembly process to ensure that the correct component is placed in the correct position. - How can I ensure the availability of components specified in the BOM?
To ensure component availability, it is important to verify the availability with suppliers before finalizing the BOM. Additionally, consider including alternative or substitute components in the BOM to mitigate supply chain risks. - What are the benefits of using BOM management software?
BOM management software helps in automating the BOM creation process, reducing manual errors, and ensuring consistency. It also facilitates collaboration among team members, enables version control, and integrates with other tools used in the PCB design and assembly process.
Leave a Reply