What are Rigid-Flex PCBs?
Rigid-flex PCBs are a type of printed circuit board that combines both rigid and flexible substrates into a single board. The rigid sections provide structural support and house most of the components, while the flexible sections allow for bending and folding of the board, enabling 3D configurations and space-saving designs.
Rigid-Flex Benefits
1. Space Savings and Miniaturization
One of the primary advantages of rigid-flex PCBs is their ability to save space and enable miniaturization of electronic devices. By combining rigid and flexible sections, designers can create compact, three-dimensional configurations that would be impossible with traditional rigid boards.
Feature | Rigid PCBs | Rigid-Flex PCBs |
---|---|---|
Board Thickness | Thicker | Thinner |
Component Density | Lower | Higher |
3D Configurations | Limited | Extensive |
2. Increased Reliability
Rigid-flex PCBs offer increased reliability compared to traditional PCBs with separate rigid and flexible sections connected by cables or connectors. By eliminating these interconnects, rigid-flex boards reduce the risk of connection failures and improve overall system reliability.
3. Improved Signal Integrity
The elimination of connectors and cables in rigid-flex PCBs also leads to improved signal integrity. With fewer interconnects, there is less opportunity for signal degradation, reflections, and noise, resulting in better signal quality and higher-speed performance.
4. Weight Reduction
Rigid-flex PCBs can help reduce the overall weight of electronic devices by eliminating the need for separate boards, connectors, and cables. This weight reduction is particularly important in applications such as aerospace and portable devices, where every gram counts.
5. Enhanced Durability
The flexible sections of rigid-flex PCBs allow for repeated bending and folding without compromising the board’s integrity. This enhanced durability makes rigid-flex PCBs ideal for applications that require frequent motion or are subjected to vibration and shock.
6. Simplified Assembly
Rigid-flex PCBs can simplify the assembly process by reducing the number of separate components and interconnects. This streamlined assembly leads to shorter production times, lower assembly costs, and improved overall manufacturing efficiency.
Assembly Step | Rigid PCBs | Rigid-Flex PCBs |
---|---|---|
Board Mounting | Multiple boards | Single board |
Interconnects | Cables and connectors | Integrated |
Testing | Multiple points | Fewer points |
7. Design Flexibility
The combination of rigid and flexible sections in rigid-flex PCBs allows for greater design flexibility. Designers can create complex, three-dimensional configurations that conform to the available space within a device, enabling innovative and compact product designs.
8. Cost Savings
While rigid-flex PCBs may have a higher initial cost compared to traditional rigid boards, they can lead to overall cost savings in the long run. By reducing the number of separate components, simplifying assembly, and improving reliability, rigid-flex PCBs can help lower production and maintenance costs.
Frequently Asked Questions (FAQ)
1. What industries commonly use rigid-flex PCBs?
Rigid-flex PCBs are used in a wide range of industries, including:
– Aerospace and defense
– Medical devices
– Automotive electronics
– Consumer electronics
– Industrial automation
2. Can rigid-flex PCBs be repaired?
Yes, rigid-flex PCBs can be repaired, but the process is more complex compared to traditional rigid boards. Specialized equipment and expertise are required to repair the flexible sections without causing further damage.
3. How do rigid-flex PCBs handle heat dissipation?
Heat dissipation in rigid-flex PCBs is primarily managed through the rigid sections, which can incorporate heat sinks and other thermal management features. The flexible sections are typically not used for heat dissipation due to their thin profile.
4. What materials are used in rigid-flex PCBs?
Rigid-flex PCBs typically use a combination of materials, including:
– Rigid substrate: FR-4, polyimide, or high-temperature materials
– Flexible substrate: Polyimide or polyester
– Copper Foil for conductive layers
– Adhesives and cover layers for bonding and protection
5. Are there any limitations to designing with rigid-flex PCBs?
While rigid-flex PCBs offer numerous advantages, there are some limitations to consider:
– Higher initial design complexity and cost
– Limited flexibility in component placement on flexible sections
– Reduced heat dissipation in flexible areas
– More complex assembly and repair processes
Despite these limitations, the benefits of rigid-flex PCBs often outweigh the drawbacks, making them an attractive option for many applications.
In conclusion, rigid-flex PCBs offer a range of advantages over traditional rigid boards, including space savings, increased reliability, improved signal integrity, weight reduction, enhanced durability, simplified assembly, design flexibility, and potential cost savings. As technology continues to advance and the demand for compact, reliable electronic devices grows, rigid-flex PCBs will likely play an increasingly important role in the electronics industry.
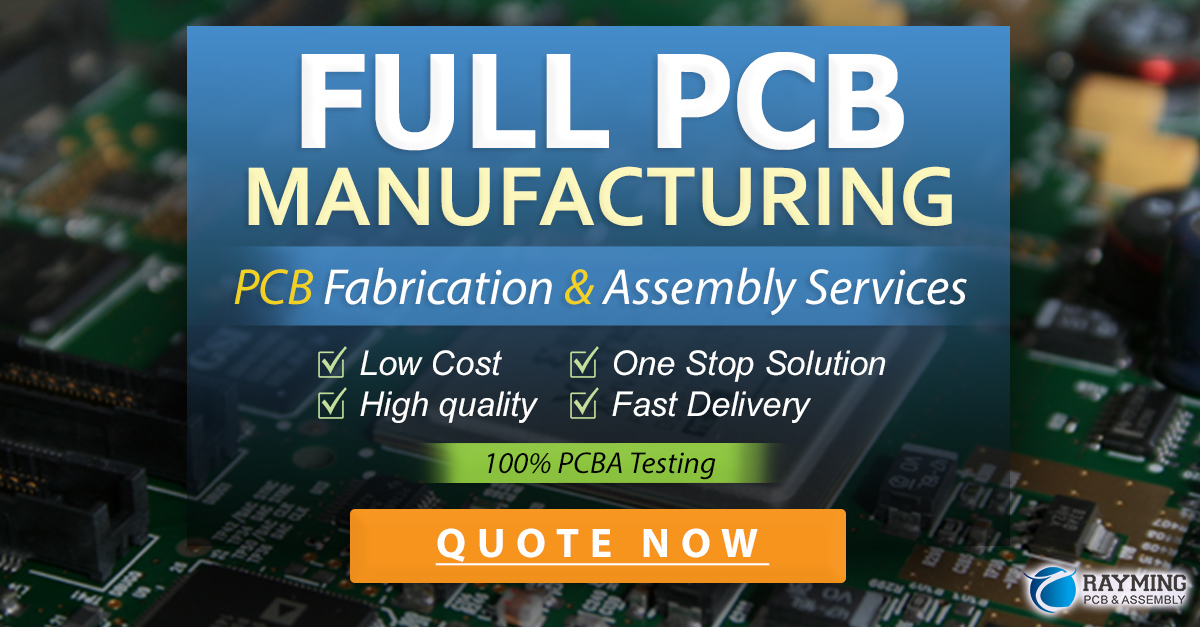
Leave a Reply