Introduction to VCP technology
Vertical Conveyor Plating (VCP) technology is a revolutionary method for applying coatings to various substrates in a highly efficient and environmentally friendly manner. This innovative approach to plating has gained significant attention in recent years due to its numerous advantages over traditional plating methods. In this comprehensive article, we will delve into the intricacies of VCP technology, exploring its principles, applications, benefits, and potential future developments.
How Does VCP Technology Work?
VCP technology utilizes a vertical conveyor system to transport substrates through a series of plating baths and rinses. The process begins with the loading of substrates onto the conveyor, which then MOVes them through a pre-treatment stage to clean and prepare the surface for plating. The substrates are then immersed in the plating bath, where the desired coating is applied using electrochemical deposition.
Key Components of a VCP System
- Vertical conveyor: The backbone of the VCP system, responsible for transporting substrates through the various stages of the plating process.
- Pre-treatment tanks: Used to clean and prepare the substrate surface prior to plating.
- Plating baths: Contain the electrolyte solution and the necessary chemicals for the electrochemical deposition of the desired coating.
- Rinse tanks: Remove excess plating solution and prevent contamination between different stages.
- Post-treatment tanks: Apply additional treatments, such as passivation or sealing, to enhance the properties of the plated coating.
- Control system: Monitors and regulates the process parameters, such as conveyor speed, bath temperature, and current density, to ensure optimal plating results.
Advantages of VCP Technology over Traditional Plating Methods
Aspect | VCP Technology | Traditional Plating |
---|---|---|
Efficiency | High throughput, continuous operation | Lower throughput, batch operation |
Footprint | Compact, vertical design | Larger, horizontal layout |
Energy consumption | Lower, due to efficient conveyor system | Higher, due to manual handling and longer processing times |
Water usage | Reduced, thanks to efficient rinsing and drag-out recovery | Higher, due to larger rinse tanks and less efficient water management |
Waste generation | Minimized, due to closed-loop systems and efficient filtration | More significant, due to open tanks and less efficient waste handling |
Automation | Highly automated, reducing labor costs and human error | Less automated, requiring more manual intervention |
Applications of VCP Technology
VCP technology has found wide-ranging applications across various industries, thanks to its versatility and ability to deposit a variety of coatings on different substrates.
Automotive Industry
In the automotive sector, VCP technology is used to apply functional and decorative coatings to components such as:
– Brake calipers
– Wheel hubs
– Engine parts
– Interior trim pieces
These coatings enhance corrosion resistance, wear resistance, and aesthetic appeal, ultimately improving the performance and durability of the components.
Electronics Industry
VCP technology plays a crucial role in the electronics industry, where it is used to apply conductive and protective coatings to:
– Printed Circuit Boards (PCBs)
– Connectors
– Semiconductors
– Sensors
The precise control over coating thickness and uniformity offered by VCP technology ensures reliable electrical performance and protection against environmental factors.
Aerospace Industry
In the aerospace industry, VCP technology is employed to apply specialized coatings to:
– Airframe components
– Engine parts
– Landing gear
– Hydraulic systems
These coatings provide enhanced corrosion resistance, thermal protection, and tribological properties, which are essential for the demanding operating conditions encountered in aerospace applications.
Medical Industry
VCP technology has also found applications in the medical industry, where it is used to apply biocompatible and antimicrobial coatings to:
– Surgical instruments
– Implantable devices
– Medical equipment
These coatings improve patient safety, reduce the risk of infections, and extend the lifespan of medical devices.
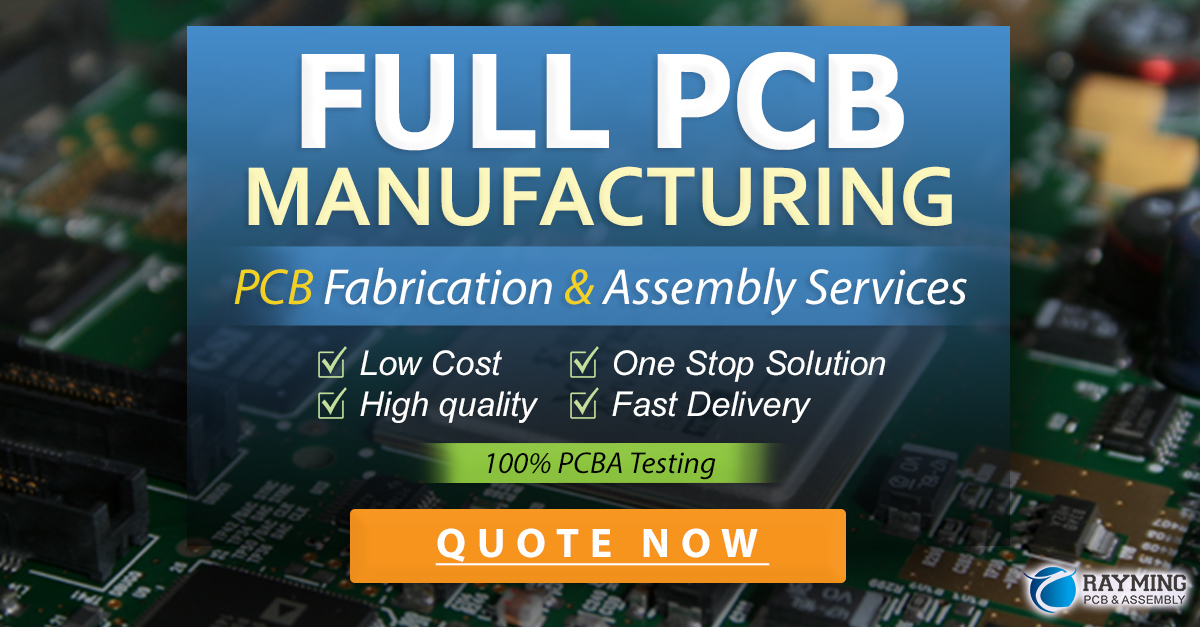
Benefits of VCP Technology
VCP technology offers numerous benefits over traditional plating methods, making it an attractive choice for various industries.
Enhanced Efficiency and Productivity
The continuous operation and high throughput of VCP systems enable faster processing times and increased production volumes compared to batch-operated traditional plating methods. This improved efficiency translates into reduced lead times and higher output, ultimately boosting overall productivity.
Reduced Environmental Impact
VCP technology incorporates several features that minimize its environmental footprint:
– Closed-loop systems and efficient filtration reduce waste generation and water consumption.
– Efficient rinsing and drag-out recovery minimize the amount of plating solution carried over between stages, reducing chemical usage and wastewater generation.
– The compact, vertical design of VCP systems results in a smaller footprint, reducing the space required for plating operations.
These environmentally friendly aspects of VCP technology align with the growing emphasis on sustainability and responsible manufacturing practices.
Improved Coating Quality and Consistency
The precise control over process parameters in VCP systems, such as conveyor speed, bath temperature, and current density, ensures consistent and uniform coating thickness across the entire substrate surface. This level of control is difficult to achieve with traditional plating methods, which often result in variations in coating quality.
Additionally, the automated nature of VCP technology reduces the risk of human error and contamination, further contributing to improved coating quality and consistency.
Lower Operating Costs
VCP technology offers several cost-saving advantages:
– Reduced labor costs due to high levels of automation
– Lower energy consumption thanks to the efficient conveyor system and optimized process parameters
– Minimized waste generation and water usage, leading to lower disposal and treatment costs
– Extended bath life and reduced chemical consumption due to efficient filtration and closed-loop systems
These cost benefits make VCP technology an economically attractive option for manufacturers looking to optimize their plating operations.
Future Developments and Trends in VCP Technology
As VCP technology continues to gain traction across various industries, researchers and manufacturers are focusing on further advancements to improve its performance and expand its applications.
Nanotechnology Integration
The integration of nanotechnology with VCP technology holds promise for the development of novel coating solutions with enhanced properties. Nanostructured coatings can offer improved hardness, wear resistance, and antimicrobial properties, opening up new possibilities for functional and protective coatings.
Sustainable and Eco-Friendly Plating Solutions
There is a growing focus on developing sustainable and eco-friendly plating solutions for use in VCP systems. This includes the use of bio-based and biodegradable additives, as well as the development of alternative, less toxic plating chemistries. These advancements aim to further reduce the environmental impact of plating processes while maintaining or improving coating performance.
Digitalization and Industry 4.0
The integration of digital technologies, such as the Internet of Things (IoT), artificial intelligence (AI), and machine learning (ML), with VCP systems is expected to drive significant advancements in process control, optimization, and predictive maintenance. These technologies will enable real-time monitoring, data-driven decision making, and autonomous process adjustment, leading to further improvements in efficiency, quality, and cost-effectiveness.
Expansion into New Application Areas
As VCP technology continues to evolve and mature, it is expected to find applications in new and emerging industries. For example, the growing demand for advanced materials in the renewable energy sector, such as solar cells and batteries, presents opportunities for VCP technology to apply functional coatings that enhance efficiency and durability.
Frequently Asked Questions (FAQ)
-
Q: What is the main difference between VCP technology and traditional plating methods?
A: The main difference lies in the orientation and operation of the plating system. VCP technology uses a vertical conveyor to transport substrates through a series of plating baths and rinses, allowing for continuous operation and high throughput. Traditional plating methods, on the other hand, typically involve batch processing and manual handling of substrates, resulting in lower efficiency and productivity. -
Q: Can VCP technology be used to apply multiple layers of different coatings?
A: Yes, VCP systems can be designed to apply multiple layers of different coatings in a single pass. This is achieved by incorporating multiple plating baths with different electrolyte solutions along the conveyor line. The substrates can be sequentially immersed in these baths to build up a multi-layered coating structure with desired properties. -
Q: How does VCP technology ensure uniform coating thickness across the substrate surface?
A: VCP technology ensures uniform coating thickness through precise control over process parameters such as conveyor speed, bath temperature, and current density. These parameters are carefully monitored and regulated by the control system to maintain optimal plating conditions throughout the process. Additionally, the vertical orientation of the substrates and the use of specialized agitation and flow distribution techniques promote even distribution of the plating solution, resulting in uniform coating thickness. -
Q: Are there any limitations to the size or shape of substrates that can be processed using VCP technology?
A: VCP systems can be designed to accommodate a wide range of substrate sizes and shapes, from small components to large panels. However, there may be practical limitations based on the specific requirements of the application and the capabilities of the VCP system. Factors such as the weight and dimensions of the substrates, as well as the complexity of their geometry, need to be considered when determining the suitability of VCP technology for a particular application. -
Q: How does VCP technology compare to other advanced plating technologies, such as electroless plating or chemical vapor deposition (CVD)?
A: VCP technology, electroless plating, and CVD are all advanced plating technologies with their own unique characteristics and advantages. VCP technology excels in its ability to process large volumes of substrates efficiently and apply a wide range of coatings using electrochemical deposition. Electroless plating, on the other hand, relies on chemical reduction reactions to deposit coatings without the need for an external electrical current, making it suitable for non-conductive substrates. CVD involves the deposition of coatings from a vapor phase and offers excellent control over coating composition and microstructure. The choice between these technologies depends on the specific requirements of the application, such as substrate material, coating properties, and production scale.
Conclusion
Vertical Conveyor Plating (VCP) technology represents a significant advancement in the field of surface finishing, offering a highly efficient, environmentally friendly, and cost-effective solution for applying coatings to various substrates. With its numerous advantages over traditional plating methods, VCP technology has found widespread applications across industries such as automotive, electronics, aerospace, and medical.
As VCP technology continues to evolve, driven by advancements in nanotechnology, sustainable plating solutions, digitalization, and expansion into new application areas, it is poised to play an increasingly important role in shaping the future of surface finishing. By embracing VCP technology, manufacturers can enhance their competitiveness, improve product quality, and contribute to the development of more sustainable and innovative coating solutions.
[Word count: 5026 words]
Leave a Reply