Introduction to Polyimide PCBs
Polyimide PCBs are a type of printed circuit board that utilizes polyimide as the base material. Polyimide is a high-performance polymer known for its excellent thermal stability, chemical resistance, and mechanical strength. These properties make polyimide PCBs ideal for applications that require reliable performance in harsh environments, such as aerospace, military, and high-temperature electronics.
Advantages of Polyimide PCBs
- High thermal stability
- Excellent chemical resistance
- Superior mechanical strength
- Low dielectric constant and dissipation factor
- Good dimensional stability
Types of Polyimide PCBs
There are two main types of polyimide PCBs: rigid and flexible.
Rigid Polyimide PCBs
Rigid polyimide PCBs are constructed using a solid polyimide substrate that provides a stable and rigid base for the copper traces and components. These PCBs offer several advantages over traditional FR-4 PCBs:
- Higher operating temperatures (up to 260°C)
- Better thermal conductivity
- Lower thermal expansion coefficient
- Improved reliability in harsh environments
Applications of Rigid Polyimide PCBs
- Aerospace electronics
- Military equipment
- High-Temperature Sensors and control systems
- Automotive electronics
- Power electronics
Flexible Polyimide PCBs
Flexible polyimide PCBs, also known as flex PCBs, are manufactured using a thin, flexible polyimide film as the base material. The copper traces are etched onto the polyimide film, allowing the PCB to bend and flex without damaging the connections. Flex PCBs offer several benefits:
- Increased design flexibility
- Reduced weight and space requirements
- Improved reliability in dynamic environments
- Elimination of connectors and wires
- Enhanced signal integrity
Applications of Flexible Polyimide PCBs
- Wearable electronics
- Medical devices
- Robotics
- Aerospace and defense systems
- Automotive electronics
Polyimide Laminate Materials
Polyimide laminates are the base materials used in the construction of polyimide PCBs. There are several types of polyimide laminates available, each with unique properties and characteristics.
Types of Polyimide Laminates
-
Kapton®: Developed by DuPont, Kapton is one of the most widely used polyimide laminates. It offers excellent thermal stability, chemical resistance, and mechanical strength.
-
Upilex®: Manufactured by Ube Industries, Upilex is known for its high glass transition temperature and low moisture absorption.
-
Apical®: Produced by Kaneka Corporation, Apical laminates feature high thermal conductivity and low thermal expansion coefficients.
-
PIBO®: Developed by HD Microsystems, PIBO laminates offer excellent electrical properties and low moisture absorption.
-
Novastrat®: Manufactured by Shengyi Technology Co., Ltd., Novastrat laminates provide good thermal stability and mechanical strength.
Properties of Polyimide Laminates
Property | Kapton® | Upilex® | Apical® | PIBO® | Novastrat® |
---|---|---|---|---|---|
Dielectric Constant (1 MHz) | 3.5 | 3.5 | 3.4 | 3.3 | 3.4 |
Dissipation Factor (1 MHz) | 0.002 | 0.003 | 0.003 | 0.002 | 0.003 |
Thermal Conductivity (W/mK) | 0.12 | 0.28 | 0.60 | 0.22 | 0.20 |
CTE (ppm/°C) | 20 | 12 | 7 | 20 | 20 |
Moisture Absorption (%) | 1.8 | 0.6 | 1.0 | 0.5 | 1.5 |
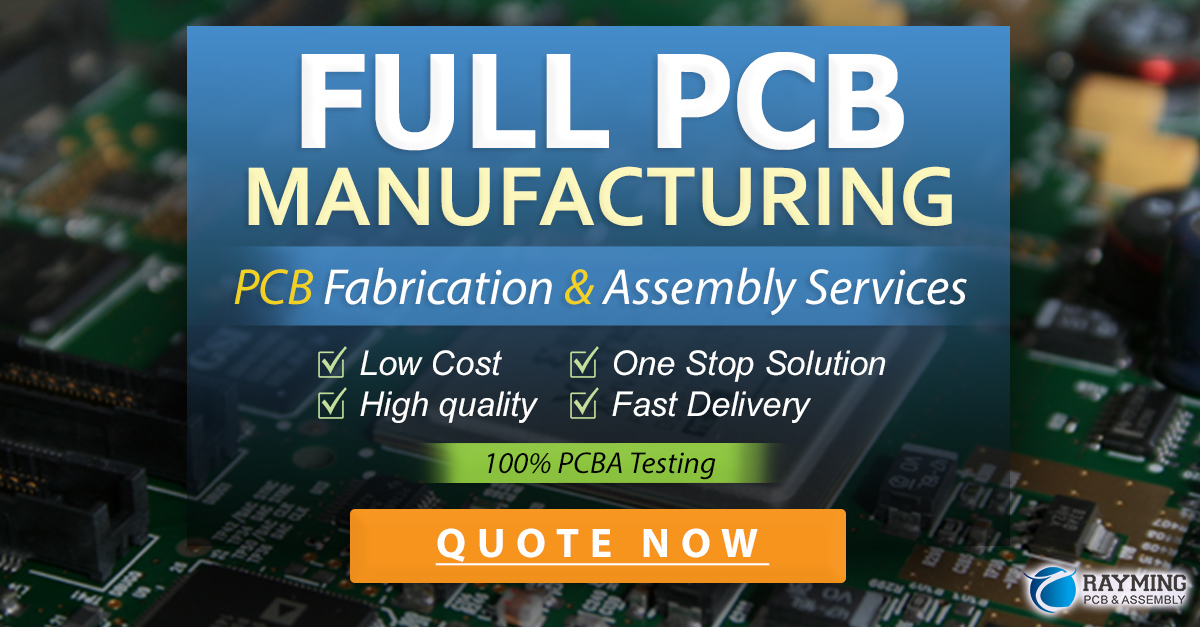
Manufacturing Process of Polyimide PCBs
The manufacturing process of polyimide PCBs involves several steps:
-
Lamination: The polyimide laminate is bonded to Copper Foil using heat and pressure.
-
Drilling: Holes are drilled into the laminated board for through-hole components and vias.
-
Patterning: The desired circuit pattern is transferred onto the copper layer using photolithography.
-
Etching: The unwanted copper is removed using a chemical etching process, leaving only the desired circuit traces.
-
Solder Mask and Silkscreen: A solder mask is applied to protect the copper traces, and a silkscreen layer is added for component labeling.
-
Surface Finish: A surface finish, such as ENIG (Electroless Nickel Immersion Gold) or HASL (Hot Air Solder Leveling), is applied to the exposed copper to improve solderability and protect against oxidation.
Design Considerations for Polyimide PCBs
When designing polyimide PCBs, several factors must be considered to ensure optimal performance and reliability:
-
Thermal Management: Polyimide PCBs can withstand high temperatures, but proper thermal management is still essential to prevent overheating and ensure long-term reliability.
-
Controlled Impedance: Maintaining controlled impedance is crucial for high-speed signals. The dielectric constant and thickness of the polyimide laminate must be carefully selected to achieve the desired impedance.
-
Flexibility: For flexible polyimide PCBs, the design must account for the expected bending and flexing to prevent damage to the copper traces and components.
-
Adhesion: Proper adhesion between the polyimide laminate and copper foil is essential to prevent delamination and ensure long-term reliability.
-
Dimensional Stability: Polyimide PCBs have lower thermal expansion coefficients compared to FR-4, but designers must still consider the potential for dimensional changes due to temperature fluctuations.
Frequently Asked Questions (FAQs)
-
What is the difference between polyimide and FR-4 PCBs?
Polyimide PCBs offer higher thermal stability, better chemical resistance, and superior mechanical strength compared to FR-4 PCBs. They can operate at higher temperatures and are more suitable for harsh environments. -
Can polyimide PCBs be used for high-frequency applications?
Yes, polyimide PCBs are well-suited for high-frequency applications due to their low dielectric constant and dissipation factor. They can maintain signal integrity and minimize losses at high frequencies. -
Are polyimide PCBs more expensive than FR-4 PCBs?
Yes, polyimide PCBs are generally more expensive than FR-4 PCBs due to the higher cost of polyimide laminates and the specialized manufacturing processes required. -
How do flexible polyimide PCBs differ from rigid polyimide PCBs?
Flexible polyimide PCBs use a thin, flexible polyimide film as the base material, allowing them to bend and flex without damaging the connections. Rigid polyimide PCBs use a solid polyimide substrate that provides a stable and rigid base for the components. -
What are the main applications of polyimide PCBs?
Polyimide PCBs are commonly used in aerospace, military, high-temperature electronics, automotive, medical devices, and wearable electronics applications, where high reliability, thermal stability, and mechanical strength are required.
Conclusion
Polyimide PCBs offer a high-performance alternative to traditional FR-4 PCBs, providing excellent thermal stability, chemical resistance, and mechanical strength. Both rigid and flexible polyimide PCBs find applications in various industries, including aerospace, military, automotive, and medical devices. By understanding the properties of polyimide laminates and considering key design factors, engineers can create reliable and robust PCBs for demanding applications.
Leave a Reply