Understanding Lead Free Soldering
Lead-free soldering is the process of joining two or more metal surfaces using a lead-free solder alloy. The most common lead-free solder alloys are tin-silver-copper (SAC) alloys, with the most popular being SAC305 (96.5% tin, 3% silver, and 0.5% copper).
Advantages of Lead Free Soldering
- Environmentally friendly: Reduces the release of toxic lead into the environment.
- Compliance with regulations: Meets RoHS (Restriction of Hazardous Substances) and WEEE (Waste Electrical and Electronic Equipment) directives.
- Improved mechanical strength: Lead-free solder joints have higher shear strength and creep resistance compared to lead-based solder joints.
Challenges of Lead Free Soldering
- Higher melting point: Lead-free solder alloys have a higher melting point (217-227°C) compared to lead-based solders (183°C), requiring higher Soldering Temperatures.
- Wetting and spreading: Lead-free solders have inferior wetting and spreading properties, making it more challenging to achieve reliable solder joints.
- Thermal stress: The higher soldering temperatures can cause increased thermal stress on components and PCBs.
Lead Free Solder Alloys
Several lead-free solder alloys are available, each with unique properties and characteristics. The following table compares the most common lead-free solder alloys:
Alloy | Composition | Melting Point (°C) | Features |
---|---|---|---|
SAC305 | Sn96.5/Ag3.0/Cu0.5 | 217-220 | Most widely used, good mechanical and thermal properties |
SAC387 | Sn95.5/Ag3.8/Cu0.7 | 217-219 | Improved thermal cycling performance compared to SAC305 |
SN100C | Sn99.3/Cu0.7 + Ni | 227 | Excellent wetting and joint strength, contains nickel |
SnCuNiGe | Sn98.5/Cu0.8/Ni0.6/Ge0.1 | 227 | Good drop shock resistance, contains germanium |
Reflow Profile Considerations
A reflow profile is a time-temperature graph that specifies the thermal profile a PCB Assembly undergoes during the Reflow Soldering process. Proper reflow profile development is crucial for achieving reliable solder joints and minimizing defects.
Key Stages of a Reflow Profile
- Preheat: Gradually raises the temperature of the PCB assembly to activate the flux and evaporate solvents.
- Thermal soak: Maintains a stable temperature to ensure even heat distribution and minimize thermal gradients.
- Reflow: Raises the temperature above the solder’s melting point, allowing the solder to melt, wet, and form intermetallic bonds.
- Cooling: Gradually cools the PCB assembly to solidify the solder joints and minimize thermal stress.
Reflow Profile Parameters
The following table lists the key parameters to consider when developing a lead-free reflow profile:
Parameter | Typical Value Range |
---|---|
Preheat ramp rate | 0.5-2.0°C/s |
Preheat temperature | 150-180°C |
Thermal soak time | 60-120 s |
Thermal soak temperature | 180-200°C |
Peak temperature | 235-250°C |
Time above liquidus (TAL) | 30-90 s |
Cooling ramp rate | 1-6°C/s |
Reflow Profile Optimization
Optimizing the reflow profile is essential for achieving high-quality solder joints and minimizing defects such as tombstoning, bridging, and voiding. Consider the following tips when optimizing your lead-free reflow profile:
- Use a thermal profiler to monitor and record the actual temperature profile of the PCB assembly during reflow.
- Ensure the preheat stage is long enough to activate the flux and remove moisture, but not so long that it causes component damage or excessive oxidation.
- Maintain a consistent thermal soak temperature to minimize thermal gradients and ensure even heat distribution across the PCB.
- Adjust the peak temperature and time above liquidus (TAL) based on the specific solder alloy and component requirements.
- Control the cooling rate to minimize thermal stress and prevent the formation of large, brittle intermetallic compounds.
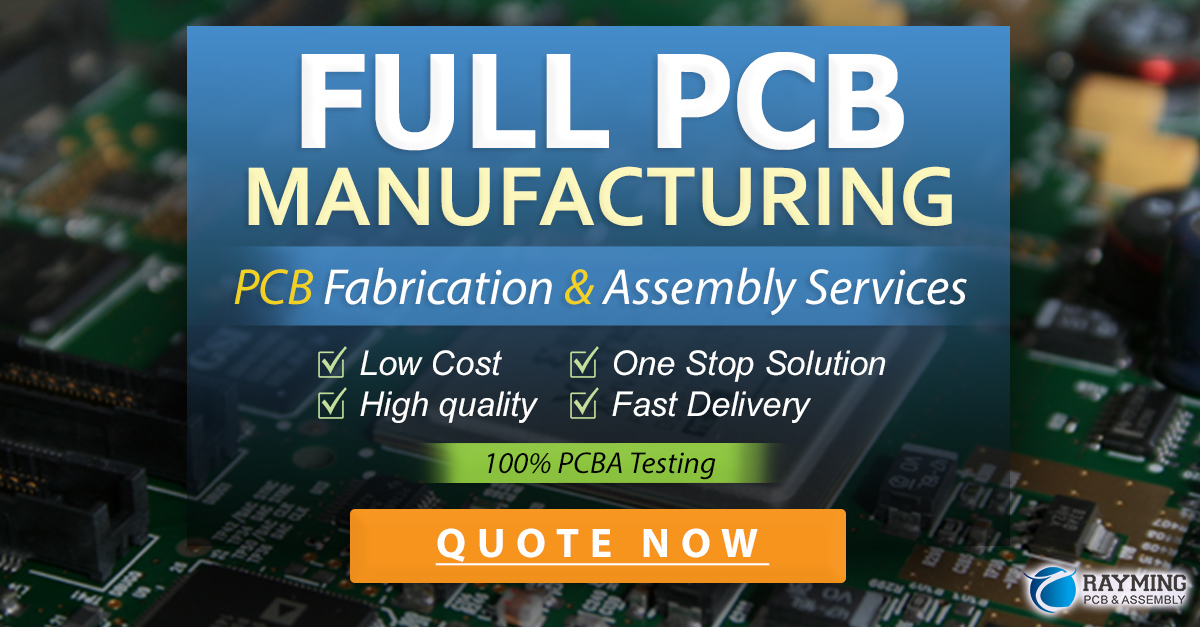
Soldering Techniques
Proper soldering techniques are essential for achieving reliable solder joints and minimizing defects. The following table compares the most common soldering techniques for lead-free soldering:
Technique | Description | Advantages | Disadvantages |
---|---|---|---|
Hand soldering | Manual soldering using a soldering iron | Flexibility, low cost, suitable for rework | Time-consuming, operator dependent, inconsistent |
Wave soldering | Automated soldering using a molten solder wave | High throughput, consistent, suitable for THT | Limited to simple PCB designs, higher defect rate |
Reflow soldering | Automated soldering using a reflow oven | High throughput, consistent, suitable for SMT | Higher equipment cost, requires profile optimization |
Selective Soldering | Automated soldering of specific areas or components | Combines advantages of wave and reflow soldering | Higher equipment cost, requires process optimization |
Hand Soldering Tips
- Use a temperature-controlled soldering iron with a suitable tip size and shape for the component being soldered.
- Apply a small amount of lead-free solder wire to the tip of the iron to improve heat transfer and wetting.
- Preheat the component and PCB pad using the soldering iron, then apply the solder wire to the joint, allowing it to melt and flow around the connection.
- Remove the soldering iron and allow the joint to cool naturally, avoiding any movement until the solder has solidified.
Wave Soldering Considerations
- Ensure the PCB design is suitable for wave soldering, with appropriate component spacing and orientation.
- Adjust the wave height, conveyor speed, and preheat settings to achieve optimal solder joint formation and minimize defects such as bridging or insufficient filleting.
- Use a nitrogen atmosphere to reduce oxidation and improve solder joint quality.
Reflow Soldering Guidelines
- Follow the recommended reflow profile for the specific solder alloy and PCB assembly.
- Ensure proper solder paste application using a stencil or syringe, with the appropriate aperture size and thickness.
- Use a reflow oven with accurate temperature control and uniform heat distribution across the PCB.
- Monitor the reflow process using a thermal profiler to ensure the actual temperature profile matches the desired profile.
Frequently Asked Questions (FAQ)
-
Q: What is the main difference between lead-based and lead-free soldering?
A: Lead-free soldering uses solder alloys that do not contain lead, typically consisting of tin, silver, and copper (SAC alloys). Lead-free solders have a higher melting point and require different soldering techniques and temperature profiles compared to lead-based solders. -
Q: Why is lead-free soldering important?
A: Lead-free soldering is important because it reduces the environmental and health risks associated with lead exposure. It also ensures compliance with regulations such as the RoHS (Restriction of Hazardous Substances) directive, which restricts the use of lead in electronic products. -
Q: What are the most common lead-free solder alloys?
A: The most common lead-free solder alloys are tin-silver-copper (SAC) alloys, with the most popular being SAC305 (96.5% tin, 3% silver, and 0.5% copper). Other lead-free alloys include SAC387, SN100C, and SnCuNiGe, each with unique properties and characteristics. -
Q: How do I develop an optimal reflow profile for lead-free soldering?
A: Developing an optimal reflow profile involves considering factors such as the specific solder alloy, PCB design, and component requirements. Key stages of a reflow profile include preheat, thermal soak, reflow, and cooling. Use a thermal profiler to monitor and optimize the actual temperature profile, ensuring it matches the desired profile and minimizes defects. -
Q: What are some tips for achieving reliable lead-free solder joints?
A: Tips for achieving reliable lead-free solder joints include: - Using a suitable solder alloy and soldering technique for the application
- Following the recommended reflow profile and temperature parameters
- Ensuring proper PCB design and component placement
- Applying an appropriate amount of solder paste or wire
- Maintaining a clean and oxide-free soldering environment
- Inspecting and testing solder joints for quality and reliability
By understanding the principles of lead-free soldering, developing optimal reflow profiles, and applying proper soldering techniques, you can achieve high-quality, reliable solder joints in your electronic assemblies.
Leave a Reply