What is Nitrogen Reflow Soldering?
Nitrogen Reflow Soldering is a process used in printed circuit board (PCB) assembly where components are attached to the PCB using solder paste, and then the entire board is heated in a controlled manner inside a nitrogen-rich oven environment to melt and flow the solder, creating permanent electrical connections.
The key difference compared to conventional reflow soldering is the use of nitrogen gas in the oven. Nitrogen displaces oxygen during the reflow process, preventing oxidation of the solder paste and components. This results in shinier, cleaner solder joints with improved wetting and fewer defects.
Advantages of Nitrogen Reflow Soldering
There are several advantages to using nitrogen reflow soldering for PCB Assembly:
-
Reduced Oxidation: The nitrogen atmosphere prevents oxygen from reacting with the molten solder, flux, and component surfaces during reflow. This greatly reduces oxidation, dross formation, and solder balling.
-
Improved Wetting: With less oxidation, the molten solder can flow and wet to the surfaces more effectively. This results in shinier, smoother, and more consistent solder joints with better mechanical strength and reliability.
-
Fewer Defects: Nitrogen reflow helps prevent common soldering defects such as bridging, tombstoning, voiding, and incomplete joints. The cleaner process produces higher first-pass yield.
-
wider process window: Using nitrogen allows for a wider range of acceptable reflow profiles and peak temperatures. This provides more flexibility and forgiveness in the process.
-
Longer Shelf Life: PCBs soldered in a nitrogen environment have slower oxidation rates even after assembly. This extends the shelf life and storage time before components start to tarnish or corrode.
How Does Nitrogen Reflow Soldering Work?
The nitrogen reflow soldering process follows the same basic steps as conventional reflow soldering, with the addition of nitrogen gas:
-
Solder Paste Printing: Solder paste, a mixture of tiny solder spheres and flux, is applied to the PCB pads through a stencil using a screen printer or dispensing system.
-
Component Placement: The surface mount components are placed onto their respective pads with the solder paste acting as a temporary adhesive. This is typically done by automated Pick-and-Place machines.
-
Nitrogen Reflow: The populated PCB is run through a reflow oven with multiple heating zones. Nitrogen gas is pumped into the oven, purging out most of the oxygen. The PCB is gradually heated according to a predetermined temperature profile, activating the flux and melting the solder particles. The molten solder then flows and wets to the component leads and pads, forming solid interconnections as it cools.
-
Inspection: After exiting the reflow oven, the assembLED PCBs are inspected, either manually or using automated optical inspection (AOI) systems, to check for any soldering defects or missing components.
Nitrogen Reflow Oven designs
Reflow ovens used for nitrogen soldering have several key features and design considerations:
-
Convection Heating: Most reflow ovens use forced convection heating, with multiple zones and fans to circulate the hot gas evenly across the PCB surface. This provides more consistent heating compared to infrared (IR) radiation.
-
Nitrogen Supply: The oven has a nitrogen inlet port connected to a supply tank or generator. Nitrogen flow rate and concentration are controlled to maintain a low oxygen level inside the oven chamber.
-
Exhaust Management: To prevent a positive pressure buildup, the oven has exhaust outlets to vent out the air displaced by nitrogen. The exhausted gas is either released into the room or captured for disposal.
-
Oxygen Analyzer: A oxygen analyzer, usually a zirconia sensor, is integrated to continuously monitor the oxygen concentration inside the oven. This provides closed-loop control to maintain a stable ppm O2 level.
-
Cooling Zone: After the reflow zone, the oven has a cooling section that uses air or nitrogen to quickly bring the PCB temperature down in a controlled manner. This helps solidify the solder joints and prevents thermal shock.
There are two main configurations of nitrogen reflow ovens:
-
Standalone Ovens: These are batch-type ovens that process one PCB array at a time. They have a front-loading door and a removable PCB tray or rack. Standalone ovens offer easier maintenance but lower throughput.
-
In-Line Ovens: For high-volume production, in-line ovens are used. PCBs are automatically transferred in and out of the heating zones on a conveyor belt. Multiple PCBs can be processed in a continuous flow. In-line ovens are faster but require more floor space.
Process Parameters and Optimization
To achieve high-quality soldering results, several key process parameters need to be controlled and optimized:
Reflow Profile
The reflow profile defines the temperature gradient experienced by the PCB over time as it passes through the oven. It is divided into four main stages:
-
Preheat: The PCB is gradually heated at a controlled ramp rate, typically 0.5-2°C/sec, to activate the flux and dry out the solder paste. This stage usually peaks at 150-180°C.
-
thermal soak: The PCB temperature is held steady for 60-120 seconds to allow all areas to reach an even temperature and let the flux fully activate and clean the surfaces. Soaking is done between 150-200°C.
-
Reflow: The temperature is rapidly ramped up, >2°C/sec, to a peak above the solder’s melting point. For lead-free solder, peak reflow is around 240-250°C and lasts for 30-90 seconds. This is when the solder fully melts, flows, and wets the surfaces to form the joints.
-
Cool Down: The PCB is cooled, <4°C/sec, to solidify the molten solder and prevent thermal shock. Cooling is done until around 100°C.
The exact temperatures and durations depend on the solder paste composition, PCB design, and component types. The reflow profile needs to be optimized to fit within the process window specified by the paste and component datasheets.
Stage | Temp (°C) | Time (sec) | Ramp (°C/sec) |
---|---|---|---|
Preheat | 150-180 | 60-150 | 0.5-2 |
Soak | 150-200 | 60-120 | 0-1 |
Reflow | 230-250 | 30-90 | >2 |
Cool Down | Peak to 100 | 30-90 | <4 |
Nitrogen Concentration
The nitrogen concentration inside the oven affects the level of oxidation protection. It is typically measured in parts per million (ppm) of oxygen remaining.
For effective nitrogen reflow soldering, the oxygen level is maintained at below 1000 ppm, with 500 ppm and 100 ppm being common setpoints. The lower the oxygen, the cleaner the process, but it comes at a higher nitrogen consumption cost.
The nitrogen flow rate needed depends on the oven size and conveyor speed. Typical flow rates range from 5-20 cubic meters per hour.
O2 Level (ppm) | Nitrogen Quality | Flow Rate (m3/hr) |
---|---|---|
1000 | Minimal | 5-10 |
500 | Good | 10-15 |
100 | Best | 15-20 |
Solder Paste
The selection of solder paste also influences the nitrogen reflow process. Lead-free pastes with higher melting points benefit more from nitrogen than leaded pastes.
Some key solder paste parameters to consider:
-
Alloy Composition: Tin-silver-copper (SAC) alloys like SAC305 and SAC405 are common lead-free choices. The exact composition affects melting behavior.
-
Paste Particle Size: Smaller solder powder sizes, like Type 3 and Type 4, are used for fine-pitch components. They require lower profiles.
-
Flux Activity Level: Higher activity fluxes are better at oxide removal but leave more residue. Nitrogen reduces the need for highly active fluxes.
Alloy | Melting Point (°C) | Powder Size | Flux Type |
---|---|---|---|
SAC305 | 217-220 | Type 3 | ROL0 |
SAC405 | 217-225 | Type 4 | ROL1 |
SnPb63 | 183 | Type 3 | ROL0 |
PCB Design
The PCB design also affects the nitrogen reflow process. Some guidelines to follow:
-
Thermal Mass: Avoid large copper pours and thick boards that increase thermal mass and require higher temperatures.
-
Component Mix: Use components with similar reflow profiles to avoid overheating some while underheating others.
-
Solder Mask: Have a solder mask clearance around pads to prevent solder wicking and bridging.
-
Nitrogen Venting: Include vent holes in the PCB to allow nitrogen to reach bottom-side components for more uniform protection.
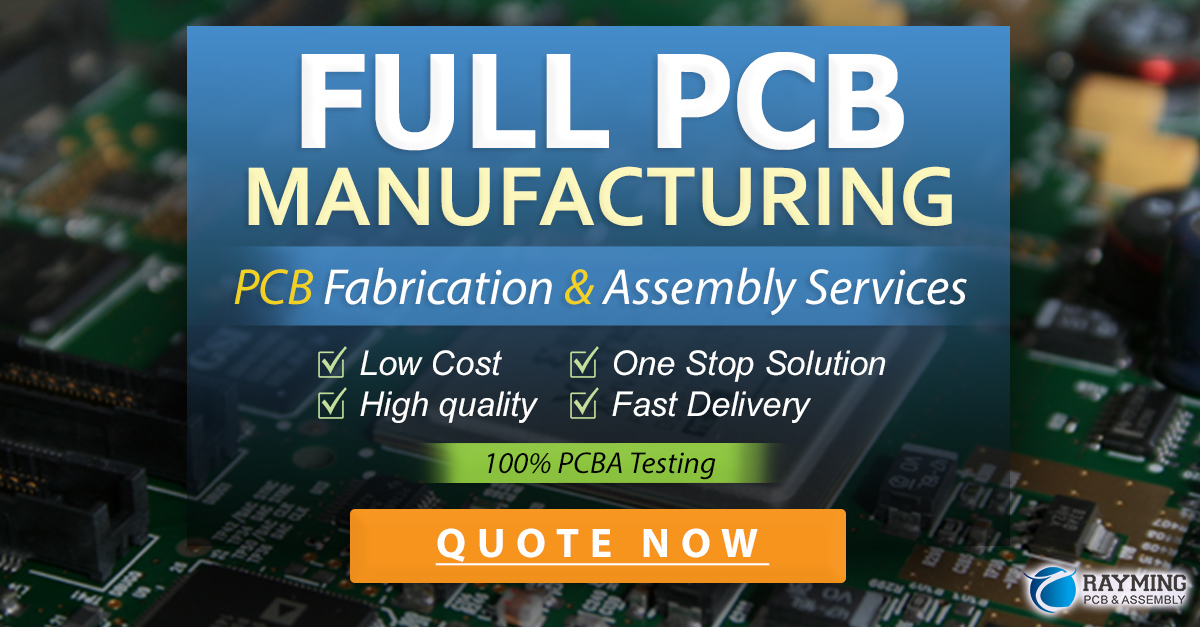
Defect Troubleshooting
Even with nitrogen reflow, some soldering defects can still occur due to improper process settings, design issues, or material problems. Here are some common defects and their potential causes:
Solder Bridging
Solder bridging is when solder inadvertently connects adjacent pads, creating a short circuit. Causes include:
- Excessive solder paste volume
- Insufficient solder mask clearance
- Incorrect reflow profile
- Inadequate nitrogen flow
Tombstoning
Tombstoning, also known as drawbridging, is when a component stands up on one end, lifting off the pad. It is caused by an imbalance in solder surface tension. Contributing factors are:
- Uneven solder paste volume
- Misaligned component placement
- Improper pad design
- Incorrect reflow profile
Voiding
Voids are hollow cavities within the solder joint that weaken its mechanical and electrical properties. Voids form due to:
- Outgassing of flux volatiles
- Trapped moisture in the PCB or components
- Rapid cooling that doesn’t allow enough time for gas bubbles to escape
- Oxidation reactions releasing CO2
Head-in-Pillow
Head-in-pillow (HIP) defects occur when the solder paste on the PCB pad melts but doesn’t fully coalesce with the solder ball on the component, resulting in a partial connection. HIP is caused by:
- Poor wetting due to surface oxidation
- Insufficient flux activity
- Incorrect solder paste volume
- Improper placement pressure
Troubleshooting these defects involves a combination of adjusting the reflow profile, optimizing the nitrogen settings, improving the PCB and stencil designs, and ensuring the paste and components are properly stored and handled.
Frequently Asked questions
1. Is nitrogen reflow soldering necessary for all PCB assemblies?
No, nitrogen reflow is not always necessary. It is most beneficial for lead-free processes, high-reliability applications, and fine-pitch components. Simpler PCBs with larger components and leaded solder may not require nitrogen.
2. Can existing reflow ovens be converted to use nitrogen?
Yes, many conventional reflow ovens can be retrofitted with a nitrogen supply system and oxygen analyzer. However, the oven chamber must be sufficiently sealed to maintain a low oxygen level, and exhaust ports may need to be added.
3. How much does nitrogen reflow soldering cost compared to conventional reflow?
The main additional costs for nitrogen reflow are the nitrogen consumption and the oven modifications. Nitrogen can be supplied by gas cylinders or generated on-site. The cost is offset by higher yields, fewer defects, and longer shelf life.
4. What is the typical nitrogen usage for reflow soldering?
Nitrogen consumption depends on the oven size, conveyor speed, and target oxygen level. Typical flow rates range from 5 to 20 cubic meters per hour. A 100 cubic meter liquid nitrogen tank can last for several weeks of continuous operation.
5. Are there any safety concerns with using nitrogen in reflow ovens?
Nitrogen gas itself is not toxic, but it can displace oxygen in confined spaces and cause asphyxiation. Reflow ovens should be operated in well-ventilated areas, and the exhaust gases should be properly vented. Personnel should be trained on the hazards and proper handling of nitrogen.
Leave a Reply