Introduction to PCB Troubleshooting
Printed Circuit Boards (PCBs) are the backbone of modern electronics. They provide a stable and reliable platform for electronic components to be mounted and connected. However, despite the advancements in PCB Manufacturing technology, issues can still arise during the production process or during the use of the PCB. In this article, we will discuss four common issues that can occur in PCBs or PCB pads and how to troubleshoot and fix them.
The Importance of PCB Troubleshooting
PCB troubleshooting is an essential skill for anyone working with electronics. Whether you are a hobbyist or a professional, being able to identify and fix issues in PCBs can save you time and money. PCB issues can range from simple problems like a cold solder joint to more complex issues like signal integrity problems. Knowing how to troubleshoot these issues can help you get your projects back on track quickly.
Common Tools Used in PCB Troubleshooting
Before we dive into the common issues and how to fix them, let’s take a look at some of the tools you will need for PCB troubleshooting:
Tool | Description |
---|---|
Multimeter | Used to measure voltage, current, and resistance |
Oscilloscope | Used to visualize and analyze electrical signals |
Soldering Iron | Used for soldering and desoldering components |
Solder Wick | Used to remove excess solder from PCBs |
Flux | Used to improve the flow of solder and prevent oxidation |
Magnifying Glass | Used to inspect small components and solder joints |
With these tools in hand, let’s move on to the common issues and how to troubleshoot them.
Issue 1: Cold Solder Joints
What are Cold Solder Joints?
Cold solder joints occur when the solder does not melt completely and does not form a proper bond between the component lead and the PCB pad. This can happen due to a variety of reasons, such as insufficient heat, poor soldering technique, or contaminated solder.
Symptoms of Cold Solder Joints
Cold solder joints can cause a variety of problems in PCBs, such as:
- Intermittent connections
- High resistance
- Poor signal quality
- Components falling off the board
How to Identify Cold Solder Joints
Cold solder joints can be identified by their appearance. They often have a dull, grainy appearance and may not have a smooth, shiny surface like a properly soldered joint. They may also have a cracked or fractured appearance.
How to Fix Cold Solder Joints
To fix a cold solder joint, you will need to reheat the joint with a soldering iron and add more solder if necessary. Here are the steps:
- Clean the soldering iron tip with a damp sponge or brass wool.
- Apply a small amount of flux to the joint.
- Heat the joint with the soldering iron until the solder melts and flows smoothly.
- If necessary, add more solder to the joint.
- Remove the soldering iron and let the joint cool.
Issue 2: Lifted Pads
What are Lifted Pads?
Lifted pads occur when the copper pad on the PCB separates from the board material. This can happen due to a variety of reasons, such as mechanical stress, thermal stress, or poor adhesion between the copper and the board material.
Symptoms of Lifted Pads
Lifted pads can cause a variety of problems in PCBs, such as:
- Open circuits
- Intermittent connections
- Poor signal quality
- Components falling off the board
How to Identify Lifted Pads
Lifted pads can often be identified visually. The pad may appear to be raised or separated from the board material. In some cases, the pad may be completely missing from the board.
How to Fix Lifted Pads
Fixing lifted pads can be challenging and may require specialized equipment and techniques. Here are some options:
- Solder a small wire or component lead to the trace leading to the lifted pad.
- Use conductive epoxy or conductive ink to bridge the gap between the pad and the board.
- Scrape away some of the Solder mask around the lifted pad and solder directly to the exposed copper trace.
- As a last resort, remove the lifted pad completely and solder directly to the underlying trace.
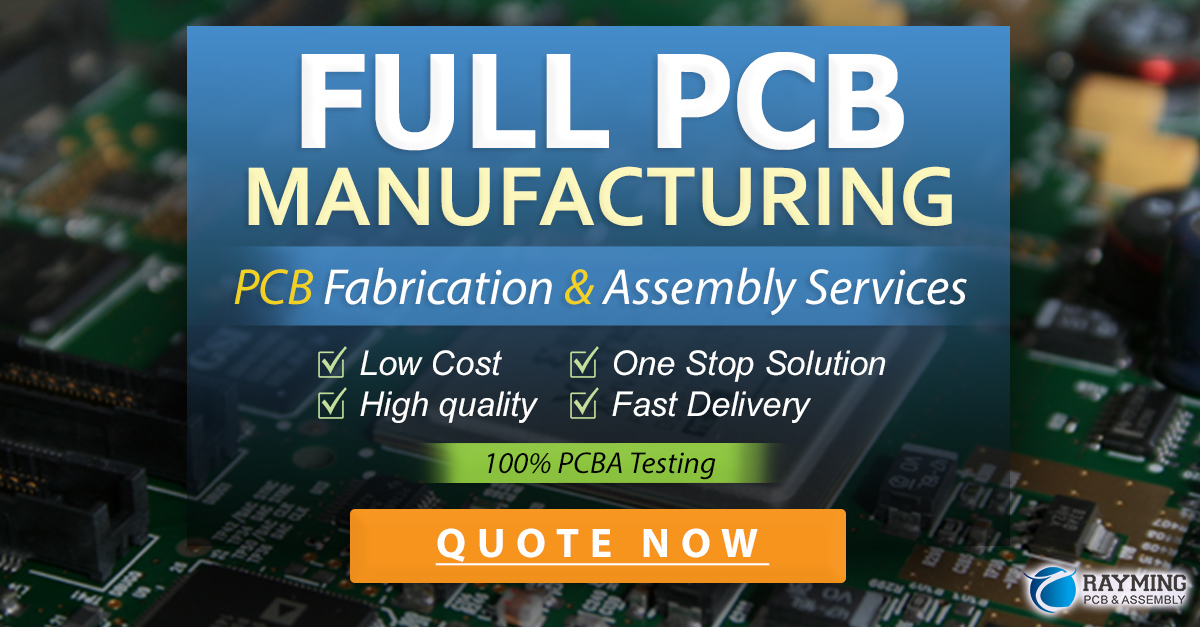
Issue 3: Solder Bridges
What are Solder Bridges?
Solder bridges occur when excess solder forms an unintended connection between two or more pads or traces on the PCB. This can happen due to a variety of reasons, such as using too much solder, poor soldering technique, or inadequate pad spacing.
Symptoms of Solder Bridges
Solder bridges can cause a variety of problems in PCBs, such as:
- Short circuits
- Incorrect signal routing
- Overheating of components
- Damage to the PCB or components
How to Identify Solder Bridges
Solder bridges can often be identified visually. The excess solder will form a visible connection between the pads or traces. In some cases, a multimeter can be used to check for continuity between the pads or traces.
How to Fix Solder Bridges
To fix a solder bridge, you will need to remove the excess solder. Here are the steps:
- Apply flux to the affected area.
- Use a soldering iron to heat the bridge until the solder melts.
- Use a solder wick or a desoldering pump to remove the excess solder.
- Clean the area with isopropyl alcohol to remove any remaining flux.
Issue 4: Damaged Traces
What are Damaged Traces?
Damaged traces occur when the copper traces on the PCB are accidentally cut, scratched, or otherwise damaged. This can happen due to a variety of reasons, such as improper handling, mechanical stress, or exposure to harsh chemicals.
Symptoms of Damaged Traces
Damaged traces can cause a variety of problems in PCBs, such as:
- Open circuits
- Intermittent connections
- Poor signal quality
- Overheating of components
How to Identify Damaged Traces
Damaged traces can often be identified visually. The trace may appear to be cut or scratched, or there may be visible damage to the surrounding board material.
How to Fix Damaged Traces
Fixing damaged traces can be challenging and may require specialized equipment and techniques. Here are some options:
- Use conductive epoxy or conductive ink to bridge the gap in the damaged trace.
- Solder a small wire or component lead across the damaged section of the trace.
- Scrape away some of the solder mask around the damaged area and solder directly to the exposed copper.
- As a last resort, remove the damaged section of the trace completely and route a new trace around it.
FAQ
Q1: Can I use a regular soldering iron for PCB troubleshooting?
A1: While a regular soldering iron can be used for some PCB troubleshooting tasks, it is recommended to use a temperature-controlled soldering iron for more precise and reliable results. Temperature-controlled soldering irons allow you to set the exact temperature needed for the specific task, reducing the risk of damaging the PCB or components.
Q2: How can I prevent lifted pads from occurring?
A2: To prevent lifted pads from occurring, it is important to follow proper PCB Design and manufacturing guidelines. This includes using the appropriate pad size and shape for the component, ensuring adequate adhesion between the copper and the board material, and avoiding excessive mechanical or thermal stress on the board.
Q3: Can I use a multimeter to test for solder bridges?
A3: Yes, a multimeter can be used to test for solder bridges. To do this, set the multimeter to the continuity or resistance mode and touch the probes to the pads or traces that you suspect may be bridged. If the multimeter beeps or shows a low resistance reading, there is likely a solder bridge present.
Q4: Is it possible to repair a damaged trace without replacing the entire PCB?
A4: In many cases, it is possible to repair a damaged trace without replacing the entire PCB. The specific repair method will depend on the extent and location of the damage, but options include using conductive epoxy or ink, soldering a wire or component lead across the damaged area, or routing a new trace around the damage.
Q5: How can I improve my PCB troubleshooting skills?
A5: To improve your PCB troubleshooting skills, it is important to practice regularly and stay up-to-date with the latest techniques and tools. Some ways to do this include:
- Building and troubleshooting your own projects
- Attending workshops or courses on PCB design and troubleshooting
- Reading technical articles and forums
- Collaborating with other engineers or hobbyists
- Investing in quality tools and equipment
By following these tips and techniques, you can become a skilLED PCB troubleshooter and tackle even the most challenging issues with confidence.
Conclusion
PCB troubleshooting is an essential skill for anyone working with electronics. By understanding the common issues that can occur in PCBs and how to identify and fix them, you can save time and money and ensure the reliability and performance of your projects. Whether you are dealing with cold solder joints, lifted pads, solder bridges, or damaged traces, there are tools and techniques available to help you get your PCBs back up and running. So don’t be afraid to dive in and start troubleshooting – with practice and perseverance, you’ll be a PCB pro in no time!
Leave a Reply