Introduction to PCBA Box Build Assembly
PCBA (Printed Circuit Board Assembly) box build is a comprehensive manufacturing process that involves the assembly of electronic components onto a printed circuit board (PCB) and the subsequent integration of the PCB into a complete electronic device or system, often housed within a protective enclosure or box. This process combines the expertise of PCB Assembly with the final product assembly, resulting in a fully functional, ready-to-use electronic product.
Key Components of PCBA Box Build Assembly
- PCB Assembly
- Component sourcing and procurement
- SMT (Surface Mount Technology) and THT (Through-Hole Technology) assembly
- Soldering and inspection
- Enclosure Design and Fabrication
- Custom enclosure design
- Material selection (e.g., plastic, metal, or composite)
- Fabrication techniques (e.g., injection molding, CNC machining, or 3D printing)
- Integration and Final Assembly
- PCB integration into the enclosure
- Wiring and interconnections
- Installation of additional components (e.g., displays, buttons, or connectors)
- Testing and Quality Control
- Functional testing
- Environmental testing (e.g., temperature, humidity, or vibration)
- Quality assurance and compliance with industry standards
Benefits of PCBA Box Build Assembly
Cost Efficiency
PCBA box build assembly offers several cost advantages compared to separate PCB assembly and final product assembly processes:
- Reduced logistics costs: By combining PCB assembly and final product assembly under one roof, transportation costs and lead times are minimized.
- Volume discounts: Purchasing components and materials in larger quantities for the entire box build process can result in significant cost savings.
- Optimized inventory management: Consolidated inventory for both PCB and final product assembly reduces the risk of overstock or shortages.
Streamlined Supply Chain
A streamlined supply chain is another key benefit of PCBA box build assembly:
- Single-source responsibility: With a single contract manufacturer handling both PCB assembly and box build, communication and coordination are simplified, reducing the risk of errors and delays.
- Faster time-to-market: Concurrent engineering and parallel processes accelerate the overall production timeline, enabling quicker product launches.
- Improved quality control: Integrated quality control measures throughout the entire process ensure consistent and reliable product quality.
Customization and Flexibility
PCBA box build assembly allows for greater customization and flexibility in product design and manufacturing:
- Custom enclosure design: Tailored enclosures can be designed and fabricated to meet specific product requirements and brand identity.
- Rapid prototyping: 3D printing and other rapid prototyping techniques enable quick iterations and design optimizations.
- Agile manufacturing: Box build assembly lines can be quickly reconfigured to accommodate product variations or new product introductions.
PCBA Box Build Assembly Process
Step 1: PCB Design and Fabrication
The PCBA box build process begins with the design and fabrication of the printed circuit board:
- Schematic design: Creating a schematic diagram that represents the electrical connections and components of the circuit.
- PCB layout: Translating the schematic into a physical layout, determining the placement of components and routing of traces.
- PCB fabrication: Manufacturing the bare PCB according to the layout, typically using a combination of etching, drilling, and plating processes.
Step 2: Component Sourcing and Procurement
Once the PCB design is finalized, the necessary components are sourced and procured:
- Bill of Materials (BOM) creation: Generating a comprehensive list of all required components, including part numbers, quantities, and specifications.
- Vendor selection: Identifying reliable suppliers for each component, considering factors such as cost, quality, and lead time.
- Component procurement: Placing orders for the required components and ensuring timely delivery to the assembly facility.
Step 3: PCB Assembly
With the bare PCB and components ready, the assembly process begins:
- Solder Paste application: Applying a precise amount of solder paste onto the PCB pads using a stencil or screen printing process.
- Component placement: Placing the components onto the PCB, either manually or using automated pick-and-place machines.
- Soldering: Melting the solder paste to create electrical and mechanical connections between the components and the PCB, typically using reflow ovens.
- Inspection and testing: Visually inspecting the assembLED PCB for defects and conducting electrical tests to verify functionality.
Step 4: Enclosure Design and Fabrication
Concurrent with the PCB assembly process, the enclosure design and fabrication take place:
- Enclosure design: Creating a 3D model of the enclosure based on the product requirements, considering factors such as size, shape, material, and aesthetics.
- Prototyping: Producing rapid prototypes of the enclosure using 3D printing or CNC machining to validate the design and make necessary adjustments.
- Tooling and fabrication: Creating the necessary molds, dies, or fixtures for mass production of the enclosure, and manufacturing the enclosure components using the chosen fabrication method.
Step 5: Integration and Final Assembly
The assembled PCB and fabricated enclosure are brought together for final integration and assembly:
- PCB integration: Mounting the assembled PCB into the enclosure, ensuring proper alignment and secure fastening.
- Wiring and interconnections: Connecting any additional wires, cables, or harnesses required for the product’s functionality.
- Component installation: Installing any additional components, such as displays, buttons, sensors, or connectors, into the enclosure.
- Sealing and labeling: Applying any necessary gaskets, seals, or adhesives to protect the product from environmental factors, and affixing labels or branding elements.
Step 6: Testing and Quality Control
Rigorous testing and quality control measures are implemented throughout the PCBA box build process:
- In-circuit testing (ICT): Verifying the functionality and performance of individual components and circuits on the PCB using automated test equipment.
- Functional testing: Validating the overall functionality of the assembled product, ensuring it meets the specified requirements and performs as intended.
- Environmental testing: Subjecting the product to various environmental conditions, such as temperature extremes, humidity, vibration, or shock, to assess its durability and reliability.
- Quality assurance: Implementing quality control checks at each stage of the process to identify and correct any defects or inconsistencies.
Step 7: Packaging and Shipping
The final step in the PCBA box build process is packaging and shipping the completed products:
- Packaging design: Developing protective packaging that ensures the product’s safety during transportation and storage, while also promoting brand identity.
- Packaging and labeling: Placing the finished products into the designed packaging, along with any necessary accessories, manuals, or documentation, and applying appropriate labels and markings.
- Shipping and logistics: Coordinating the transportation of the packaged products to their final destination, whether it be a distribution center, retail store, or end customer.
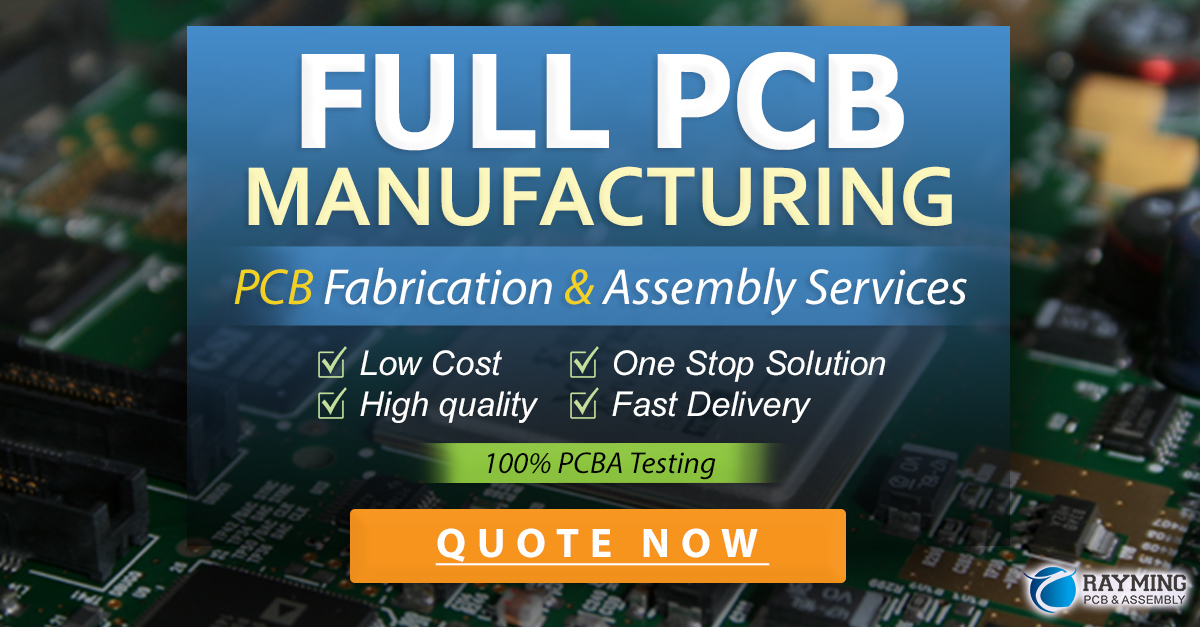
Challenges in PCBA Box Build Assembly
Despite the many benefits of PCBA box build assembly, there are several challenges that manufacturers must navigate:
- Supply chain management: Ensuring a reliable and consistent supply of components and materials, particularly during times of market volatility or disruption.
- Skilled labor: Attracting and retaining skilled technicians and engineers with expertise in both PCB assembly and final product assembly.
- Quality control: Implementing robust quality control measures throughout the entire process to minimize defects and ensure consistent product quality.
- Regulatory compliance: Navigating the complex landscape of industry standards and regulations, such as RoHS, REACH, or UL, to ensure products meet all necessary requirements.
- Intellectual property protection: Safeguarding sensitive product designs and proprietary information from potential infringement or theft.
Future Trends in PCBA Box Build Assembly
As technology continues to advance and market demands evolve, PCBA box build assembly is poised for several key trends:
- Miniaturization: The increasing demand for smaller, more compact electronic devices will drive the need for advanced PCB assembly techniques and high-density interconnect (HDI) technologies.
- Internet of Things (IoT): The proliferation of connected devices and IoT applications will fuel the growth of PCBA box build services, as these products often require custom enclosures and integrated electronics.
- Sustainable manufacturing: A growing emphasis on environmental sustainability will push manufacturers to adopt eco-friendly materials, processes, and packaging solutions in their PCBA box build operations.
- Automation and Industry 4.0: The integration of advanced automation, robotics, and data analytics will enable smarter, more efficient PCBA box build processes, improving quality, throughput, and flexibility.
- Regionalization of supply chains: Geopolitical factors and the need for greater supply chain resilience may lead to a shift towards more localized or regionalized PCBA box build services, reducing reliance on global supply networks.
Conclusion
PCBA box build assembly is a comprehensive and efficient approach to electronic product manufacturing, combining the expertise of PCB assembly with the final product assembly process. By streamlining the supply chain, enabling greater customization and flexibility, and offering cost advantages, PCBA box build services provide a compelling solution for bringing electronic products to market quickly and reliably.
As the electronics industry continues to evolve, with trends such as miniaturization, IoT, and sustainable manufacturing shaping the landscape, PCBA box build assembly will play an increasingly critical role in meeting the demands of a dynamic and competitive market. By staying at the forefront of technological advancements and adapting to the challenges and opportunities that arise, PCBA box build manufacturers can position themselves as valuable partners in the development and production of innovative electronic products.
Frequently Asked Questions (FAQ)
1. What is the difference between PCBA and PCB?
A printed circuit board (PCB) is the bare board with copper traces and pads, while a printed circuit board assembly (PCBA) is a PCB that has been populated with electronic components and soldered, making it a functional Electronic Assembly.
2. What are the advantages of using PCBA box build services?
PCBA box build services offer several advantages, including cost efficiency through combined PCB and final product assembly, a streamlined supply chain with single-source responsibility, faster time-to-market, and greater customization and flexibility in product design and manufacturing.
3. What types of testing are performed during the PCBA box build process?
Testing during the PCBA box build process typically includes in-circuit testing (ICT) to verify individual component and circuit functionality, functional testing to validate overall product performance, and environmental testing to assess durability and reliability under various conditions.
4. How do PCBA box build manufacturers ensure product quality?
PCBA box build manufacturers ensure product quality by implementing robust quality control measures throughout the entire process, including visual inspections, automated testing, and adherence to industry standards and best practices. Regular audits and continuous improvement initiatives also contribute to maintaining high quality standards.
5. What factors should be considered when choosing a PCBA box build partner?
When selecting a PCBA box build partner, consider factors such as their technical capabilities, experience with similar products or industries, quality control processes, supply chain management, and ability to scale production to meet your needs. Additionally, evaluate their communication and collaboration processes, as well as their commitment to customer service and support.
Leave a Reply