Introduction to Flexible PCBs
Flexible printed circuit boards (PCBs) are a versatile and increasingly popular choice for electronics applications that require a lightweight, compact, or bendable design. Flexible PCBs use a thin, flexible substrate material like polyimide instead of the rigid fiberglass material used in standard PCBs. This allows flexible PCBs to be bent, folded, twisted, and contoured to fit into tight spaces or conform to the shape of a product enclosure.
The growing demand for wearable devices, IoT products, and compact electronics is driving strong growth in the flexible PCB market. According to research firm Mordor Intelligence, the global flexible PCB market was valued at USD 15.2 billion in 2020 and is expected to reach USD 27.7 billion by 2026, registering a CAGR of 10.5% during the forecast period (2021-2026).
With this rising demand, many PCB manufacturers are now offering flexible PCB fabrication services. But with so many options on the market, how do you choose the right flexible PCB supplier for your project? In this article, we’ll compare some of the top flexible PCB manufacturers and examine key factors to consider when making your selection.
Leading Flexible PCB Manufacturers
Here are profiles of five well-known flexible PCB manufacturers:
NOK
NOK is a Japanese manufacturer that has been producing flexible PCBs for over 30 years. They offer a wide range of flex and Rigid-Flex PCB solutions for consumer electronics, automotive, medical, and industrial applications. NOK operates several manufacturing facilities in Japan and Thailand.
Nippon Mektron
Another major Japanese flexible PCB supplier, Nippon Mektron is a subsidiary of Nitto Denko Corporation. They have deep experience manufacturing flex PCBs for smartphones, wearables, hard disk drives, and Automotive Electronics. Nippon Mektron has factories in Japan, South Korea, Taiwan, and China.
Career Technology
Career Technology is a Taiwan-based manufacturer specializing in flexible PCBs and FPCB Assembly. Founded in 1989, they have become a key supplier to the consumer electronics and automotive industries. Career has multiple manufacturing sites in Taiwan and China.
Flexium Interconnect
Also headquartered in Taiwan, Flexium Interconnect produces high-end flexible PCBs, rigid-flex PCBs, and FPCB assemblies for consumer electronics and automotive applications. Their manufacturing footprint spans Taiwan and China. Flexium is known for their expertise in fine-pitch circuitry and HDI flexible PCBs.
Zhen Ding Technology
Zhen Ding Technology (ZDT) is a leading Taiwanese flex PCB manufacturer with a focus on the consumer electronics and automotive markets. They offer a variety of flexible circuit technologies, including multilayer, rigid-flex, and high-frequency materials. ZDT has several large-scale factories in Taiwan and China.
Comparison of Key Factors
When evaluating flexible PCB suppliers, here are some of the most important criteria to consider:
Manufacturing Capabilities
One of the first things to assess is whether a manufacturer has the right capabilities for your project. Some key manufacturing capabilities to look at include:
- Supported flex circuit types (single-sided, double-sided, multilayer, rigid-flex, etc.)
- Minimum feature sizes (line width/spacing, via sizes, etc.)
- Supported materials (polyimide, adhesiveless laminates, etc.)
- Surface finishes (ENIG, OSP, immersion silver, etc.)
- Maximum panel sizes and layer counts
- Special processes (controlled impedance, microvias, embedded components, etc.)
Here’s a comparison of some key capabilities for the five manufacturers profiled above:
Manufacturer | Flex Circuit Types | Min. Line Width/Spacing (μm) | Max. Layers | Finishes |
---|---|---|---|---|
NOK | Single-sided, double-sided, multilayer, rigid-flex | 30/30 | 30 | ENIG, OSP, immersion tin, immersion silver |
Nippon Mektron | Single-sided, double-sided, multilayer, rigid-flex | 20/20 | 12 | ENIG, OSP |
Career Technology | Single-sided, double-sided, multilayer, rigid-flex | 30/30 | 16 | ENIG, OSP, hard gold, immersion silver |
Flexium Interconnect | Single-sided, double-sided, multilayer, rigid-flex | 20/20 | 16 | ENIG, OSP, hard gold, immersion silver |
Zhen Ding Technology | Single-sided, double-sided, multilayer, rigid-flex | 20/20 | 30 | ENIG, OSP, immersion silver |
Quality Systems
When it comes to medical devices, aerospace systems, automotive electronics, and other critical applications, quality and reliability are paramount. Make sure your flexible PCB manufacturer has robust quality systems in place. Some key certifications and standards to look for include:
- ISO 9001
- IATF 16949 (automotive)
- ISO 13485 (medical devices)
- AS9100 (aerospace)
- IPC-6013 (performance spec for flexible PCBs)
- UL certification
- REACH and RoHS Compliance
All five of the manufacturers covered in this article hold ISO 9001 certification. Here’s how they compare on some other key quality standards:
Manufacturer | IATF 16949 | ISO 13485 | AS9100 | IPC-6013 | UL |
---|---|---|---|---|---|
NOK | Yes | Yes | Yes | Yes | Yes |
Nippon Mektron | Yes | No | No | Yes | Yes |
Career Technology | Yes | Yes | No | Yes | Yes |
Flexium Interconnect | Yes | Yes | No | Yes | Yes |
Zhen Ding Technology | Yes | Yes | No | Yes | Yes |
Engineering Support
Access to knowledgeable engineering support is critical when designing flexible circuits, which are typically more complex than rigid PCBs. Look for a manufacturer that can provide design reviews, DFM feedback, and technical guidance to help optimize your design for manufacturability, reliability, and cost.
All five manufacturers offer engineering support to their customers, but the level of service and expertise can vary. It’s a good idea to discuss your technical support needs with each potential supplier.
Lead Times
For time-sensitive projects, production lead times are a key consideration. Flexible PCBs typically have slightly longer lead times than rigid PCBs due to their more complex manufacturing processes. That said, many flex PCB manufacturers offer expedited production options for a premium.
Standard lead times for the profiled manufacturers range from 2-4 weeks, depending on the complexity of the design and order volume. Expedited turns of 1-2 weeks may be available. Always confirm current lead times with each supplier based on your specific requirements.
Pricing
Of course, price is always an important factor when choosing a PCB supplier. But be careful about focusing solely on the lowest price. Very low quotes can be a red flag for quality issues or inexperienced suppliers. It’s best to evaluate pricing in the context of the manufacturer’s overall capabilities, quality, and service.
Flex PCB pricing can vary widely depending on the specific design requirements, materials, order volume, and other factors. In general, flexible circuits are more expensive than rigid PCBs due to their specialized materials, more complex manufacturing processes, and lower volumes.
If your project is very cost-sensitive, it’s a good idea to get quotes from multiple suppliers based on your specific design and volume requirements. Be sure to also factor in any additional costs for engineering support, testing, or expedited production.
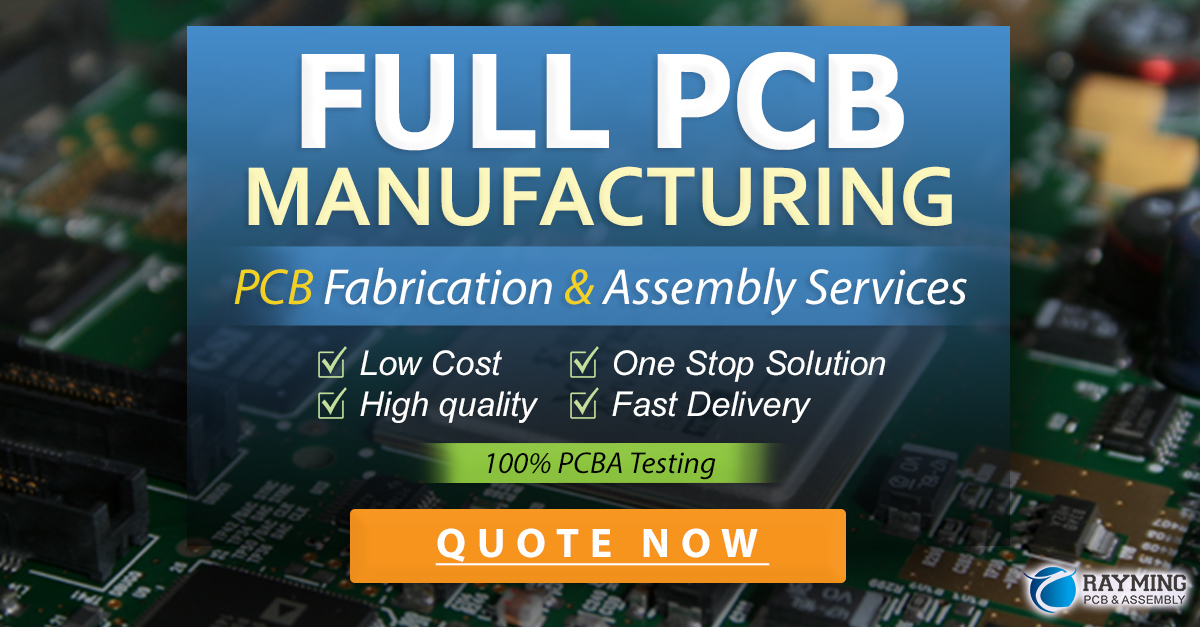
Other Factors to Consider
Beyond the key criteria outlined above, here are a few other factors that can influence your choice of flex PCB supplier:
Location and Logistics
The location of your manufacturer’s facilities can impact lead times, shipping costs, and ease of communication. Working with a local supplier may offer advantages like faster delivery times, lower shipping costs, and easier site visits or face-to-face meetings.
On the other hand, overseas manufacturers may offer lower pricing and the ability to scale to very high volumes. If you choose an offshore supplier, be sure to carefully evaluate their quality systems, communication practices, and logistics capabilities to ensure a smooth working relationship.
Financial Stability
When choosing a manufacturing partner, it’s important to evaluate their financial health and stability. You don’t want to risk working with a supplier that may go out of business or experience financial problems that could disrupt your supply chain.
Research each potential manufacturer’s ownership structure, years in business, revenue growth, and profitability. Look for red flags like recent layoffs, facility closures, or legal problems.
References and Track Record
Finally, don’t hesitate to ask each supplier for references from existing customers, especially those in your industry or with similar applications. Talking to real customers can give you valuable insights into the manufacturer’s quality, reliability, service, and engineering support.
It’s also a good idea to research each supplier’s track record and reputation online. Look for customer reviews, news articles, and other information that can help you gauge their experience and credibility.
Frequently Asked Questions
What’s the difference between flex and rigid-flex PCBs?
Flex PCBs are made entirely of flexible substrate materials like polyimide, allowing the entire circuit to bend and flex. Rigid-flex PCBs combine rigid and flexible substrates, with the rigid areas providing mechanical support and the flexible portions allowing the circuit to be bent or folded. Rigid-flex designs are often used to replace wired connections between rigid PCB sections.
How do I choose the right flex PCB material?
The most common base material for flex PCBs is polyimide (PI), which offers excellent flexibility, heat resistance, and electrical properties. Other specialized materials like polyester (PET) or liquid crystal polymer (LCP) may be used for applications that require unique properties like ultra-thinness, transparency, or low moisture absorption. Your flex PCB manufacturer can help you select the best material for your design based on your specific requirements.
What are the most common applications for flex PCBs?
Flex PCBs are widely used in applications that require compact packaging, light weight, or the ability to fit into tight spaces. Some of the most common applications include:
- Consumer electronics (smartphones, wearables, laptops)
- Medical devices (hearing aids, insulin pumps, patient monitors)
- Automotive electronics (displays, sensors, control modules)
- Aerospace and defense systems
- Industrial equipment
- Internet of Things (IoT) devices
What are some key design considerations for flex PCBs?
Designing flexible circuits requires careful attention to material selection, mechanical stress, and manufacturing constraints. Some key design considerations include:
- Choosing the right base material and copper thickness
- Defining appropriate bend radii and bend zones
- Adding strain relief features like stiffeners and coverlay
- Following manufacturer’s design rules for trace width/spacing, pad sizes, and via placement
- Defining appropriate plated through-hole (PTH) or via structures
- Specifying the right surface finish for the application environment
- Planning for the assembly process and required access points
It’s important to involve your flex PCB supplier early in the design process to ensure your design is optimized for manufacturability, reliability, and cost.
Are there any special testing or quality requirements for flex PCBs?
In addition to standard electrical testing and visual inspection, flex PCBs typically require additional testing to ensure they can withstand the expected mechanical stresses and environmental conditions. Common tests for flex PCBs include:
- Bend testing to verify the circuit can withstand repeated flexing without damage
- Thermal cycling to ensure reliable operation across the expected temperature range
- Humidity testing to evaluate moisture resistance
- Tensile testing to measure the amount of force required to pull the circuit apart
- Accelerated life testing to assess long-term durability
Work with your flex PCB supplier to define the right testing and quality assurance plan for your specific application and reliability requirements.
Conclusion
Choosing the right flexible PCB manufacturer is critical to the success of your project. By carefully evaluating each supplier’s capabilities, quality systems, engineering support, lead times, and pricing, you can find the best fit for your specific needs.
The five manufacturers profiled in this article – NOK, Nippon Mektron, Career Technology, Flexium Interconnect, and Zhen Ding Technology – are all well-established suppliers with strong track records in the flex PCB industry. However, there are many other excellent flex PCB manufacturers around the world that may be a good fit for your project.
Ultimately, the right flex PCB supplier for you will depend on your unique requirements, budget, and location. By doing your due diligence and asking the right questions, you can find a manufacturing partner that will help you bring your flexible circuit designs to life.
Leave a Reply