Introduction to Aluminum PCB
Aluminum PCBs, also known as metal core PCBs (MCPCBs), are a type of printed circuit board that uses an aluminum substrate instead of the traditional FR-4 material. This unique structure provides excellent Thermal Conductivity, making aluminum PCBs ideal for applications that generate significant heat, such as high-power LEDs, power electronics, and automotive systems.
Advantages of Aluminum PCB
- Enhanced thermal management
- Improved electrical performance
- Increased durability and reliability
- Lightweight and compact design
- Cost-effective solution for heat dissipation
Structure of Aluminum PCB
Layers of an Aluminum PCB
An aluminum PCB consists of several layers:
- Dielectric layer
- Copper foil
- Thermal insulation layer
- Aluminum substrate
Dielectric Layer
The dielectric layer is an electrically insulating material that separates the copper foil from the aluminum substrate. Common dielectric materials include:
- Polyimide
- Epoxy
- Ceramic
The dielectric layer’s thickness and thermal conductivity play a crucial role in the overall thermal performance of the aluminum PCB.
Copper Foil
The copper foil layer is where the electrical circuit is etched. The thickness of the copper foil can vary depending on the application’s requirements, with typical thicknesses ranging from 0.5 oz to 10 oz per square foot.
Thermal Insulation Layer
The thermal insulation layer, also known as the thermal interface material (TIM), is placed between the dielectric layer and the aluminum substrate. This layer helps to minimize thermal resistance and improve heat transfer from the copper foil to the aluminum substrate.
Aluminum Substrate
The aluminum substrate serves as the foundation of the PCB and provides excellent thermal conductivity. The most common aluminum alloys used in PCBs are:
- 6061
- 5052
- 1100
The thickness of the aluminum substrate can range from 0.5 mm to 3 mm, depending on the application’s requirements.
Comparison of Aluminum PCB vs. Traditional FR-4 PCB
Property | Aluminum PCB | FR-4 PCB |
---|---|---|
Thermal Conductivity | High | Low |
Electrical Insulation | Low | High |
Weight | Low | High |
Mechanical Strength | High | Moderate |
Cost | High | Low |
Heat Conductivity of Aluminum PCB
Thermal Conductivity of Aluminum
Aluminum is an excellent thermal conductor, with a thermal conductivity of approximately 205 W/(m·K). This high thermal conductivity allows aluminum PCBs to efficiently dissipate heat from the electrical components to the environment.
Factors Affecting Heat Conductivity
Several factors can influence the heat conductivity of an aluminum PCB:
- Dielectric material properties
- Thickness of the dielectric layer
- Thermal interface material (TIM) properties
- Aluminum alloy composition
- Surface finish and roughness
Dielectric Material Properties
The dielectric material’s thermal conductivity directly impacts the overall thermal performance of the aluminum PCB. Materials with higher thermal conductivity, such as ceramic or epoxy-based dielectrics, can improve heat transfer from the copper foil to the aluminum substrate.
Thickness of the Dielectric Layer
A thinner dielectric layer reduces thermal resistance and improves heat transfer. However, the dielectric layer must be thick enough to provide adequate electrical insulation between the copper foil and the aluminum substrate.
Thermal Interface Material (TIM) Properties
The thermal interface material fills the gaps between the dielectric layer and the aluminum substrate, helping to minimize thermal resistance. TIMs with high thermal conductivity and low thermal resistance can significantly improve the aluminum PCB’s heat dissipation capabilities.
Aluminum Alloy Composition
Different aluminum alloys have varying thermal conductivities. For example, 6061 aluminum has a thermal conductivity of 167 W/(m·K), while 1100 aluminum has a thermal conductivity of 222 W/(m·K). Choosing the appropriate aluminum alloy can optimize the PCB’s thermal performance.
Surface Finish and Roughness
The surface finish and roughness of the aluminum substrate can affect its ability to dissipate heat. A smooth surface finish promotes better contact with the thermal interface material, reducing thermal resistance. Additionally, surface treatments such as anodization or plasma electrolytic oxidation (PEO) can enhance the aluminum substrate’s thermal properties.
Thermal Management Techniques for Aluminum PCB
To further improve the thermal performance of aluminum PCBs, several thermal management techniques can be employed:
- Heatsinks
- Thermal vias
- Thermal pads
- Forced air cooling
- Liquid cooling
Heatsinks
Heatsinks are passive cooling devices that increase the surface area for heat dissipation. They can be attached to the aluminum substrate using thermal adhesive or mechanical fasteners.
Thermal Vias
Thermal vias are plated-through holes that transfer heat from the copper foil to the aluminum substrate. They provide a low-resistance thermal path and can be strategically placed near high-heat-generating components.
Thermal Pads
Thermal pads are compressible materials that can be placed between the aluminum substrate and a heatsink or cooling device. They help to fill any air gaps and improve thermal contact.
Forced Air Cooling
Forced air cooling involves using fans or blowers to actively circulate air over the aluminum PCB, enhancing convective heat transfer.
Liquid Cooling
Liquid cooling systems use a coolant to absorb and transport heat away from the aluminum PCB. This technique is typically reserved for high-performance applications with extreme heat dissipation requirements.
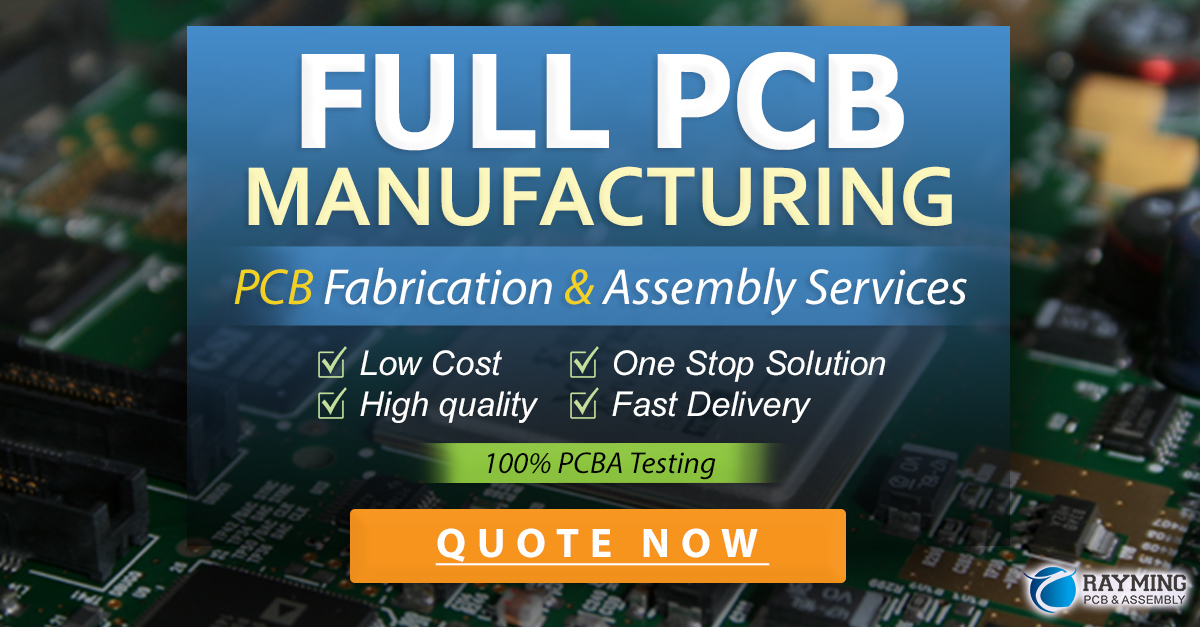
Applications of Aluminum PCB
Aluminum PCBs are used in various industries and applications where thermal management is critical:
- LED Lighting
- Power electronics
- Automotive systems
- Telecommunications
- Aerospace and defense
LED Lighting
Aluminum PCBs are widely used in LED lighting applications due to their ability to efficiently dissipate heat generated by high-power LEDs. By maintaining lower operating temperatures, aluminum PCBs can improve LED efficiency, color consistency, and longevity.
Power Electronics
Power electronic devices, such as motor drives, inverters, and power supplies, generate significant heat during operation. Aluminum PCBs can help to manage this heat, ensuring reliable performance and preventing premature component failure.
Automotive Systems
In the automotive industry, aluminum PCBs are used in various applications, including engine control units (ECUs), LED headlights, and power distribution systems. The increased thermal conductivity of aluminum PCBs helps to ensure reliable operation in the harsh automotive environment.
Telecommunications
Telecommunications equipment, such as base stations and routers, require efficient thermal management to maintain optimal performance. Aluminum PCBs can help to dissipate heat generated by high-frequency components, improving system reliability and reducing maintenance costs.
Aerospace and Defense
Aerospace and defense applications often demand high-performance electronics that can operate in extreme conditions. Aluminum PCBs offer a lightweight and thermally efficient solution for managing heat in systems such as radar, avionics, and satellite communications.
Design Considerations for Aluminum PCB
When designing an aluminum PCB, several key factors must be considered to ensure optimal performance and reliability:
- Dielectric material selection
- Copper foil thickness
- Thermal via placement and size
- Aluminum substrate thickness and alloy
- Surface finish and treatment
Dielectric Material Selection
Choosing the appropriate dielectric material is crucial for achieving the desired balance between thermal conductivity and electrical insulation. Factors to consider include the material’s thermal conductivity, dielectric strength, and compatibility with the aluminum substrate.
Copper Foil Thickness
The thickness of the copper foil should be selected based on the electrical and thermal requirements of the application. Thicker copper foil can improve current-carrying capacity and heat spreading, but may increase the overall cost of the PCB.
Thermal Via Placement and Size
Thermal vias should be strategically placed near high-heat-generating components to provide a low-resistance thermal path to the aluminum substrate. The size and number of thermal vias will depend on the specific heat dissipation requirements of the application.
Aluminum Substrate Thickness and Alloy
The thickness and alloy of the aluminum substrate should be chosen based on the mechanical and thermal requirements of the application. Thicker substrates can provide better heat spreading and mechanical stability, while different alloys offer varying thermal conductivities and mechanical properties.
Surface Finish and Treatment
The surface finish and treatment of the aluminum substrate can impact its thermal performance and compatibility with the dielectric material. Common surface finishes include anodization and plasma electrolytic oxidation (PEO), which can improve the substrate’s thermal properties and adhesion to the dielectric layer.
Manufacturing Process of Aluminum PCB
The manufacturing process for aluminum PCBs involves several key steps:
- Substrate preparation
- Dielectric layer application
- Copper foil lamination
- Circuit etching
- Surface finish application
- Inspection and testing
Substrate Preparation
The aluminum substrate is cleaned and treated to ensure good adhesion with the dielectric layer. This may involve surface roughening, degreasing, and anodization or PEO treatment.
Dielectric Layer Application
The dielectric layer is applied to the aluminum substrate using techniques such as screen printing, curtain coating, or lamination. The dielectric material must be evenly distributed and free of defects to ensure proper electrical insulation.
Copper Foil Lamination
The copper foil is laminated to the dielectric layer using heat and pressure. The lamination process must ensure good adhesion between the copper foil and the dielectric material to prevent delamination during subsequent processing steps.
Circuit Etching
The desired circuit pattern is etched into the copper foil using photolithography and chemical etching processes. The etching process must be carefully controlled to ensure accurate feature sizes and minimize undercut.
Surface Finish Application
A surface finish, such as HASL (Hot Air Solder Leveling), ENIG (Electroless Nickel Immersion Gold), or OSP (Organic Solderability Preservative), is applied to the copper traces to protect them from oxidation and improve solderability.
Inspection and Testing
The completed aluminum PCB undergoes visual inspection and electrical testing to ensure that it meets the required specifications. This may include continuity testing, insulation resistance testing, and thermal imaging to verify proper heat dissipation.
Frequently Asked Questions (FAQ)
- What is the main advantage of using an aluminum PCB over a traditional FR-4 PCB?
-
The main advantage of using an aluminum PCB is its superior thermal conductivity, which allows for better heat dissipation and thermal management of electronic components.
-
Can aluminum PCBs be used in high-voltage applications?
-
Yes, aluminum PCBs can be used in high-voltage applications, provided that the dielectric layer is properly designed to provide adequate electrical insulation between the copper foil and the aluminum substrate.
-
Are aluminum PCBs more expensive than traditional FR-4 PCBs?
-
Yes, aluminum PCBs are typically more expensive than FR-4 PCBs due to the higher cost of the aluminum substrate and the specialized manufacturing processes required.
-
How does the choice of dielectric material affect the thermal performance of an aluminum PCB?
-
The dielectric material’s thermal conductivity directly impacts the overall thermal performance of the aluminum PCB. Materials with higher thermal conductivity, such as ceramic or epoxy-based dielectrics, can improve heat transfer from the copper foil to the aluminum substrate.
-
Can aluminum PCBs be used in flexible applications?
- While aluminum PCBs are generally more rigid than traditional FR-4 PCBs, they can be used in some flexible applications. However, special considerations must be made in the design and manufacturing process to ensure the reliability and durability of the flexible aluminum PCB.
Conclusion
Aluminum PCBs offer a highly effective solution for thermal management in electronic applications. By combining the excellent thermal conductivity of aluminum with a multi-layer structure, these PCBs can efficiently dissipate heat from high-power components, ensuring reliable performance and extended product life.
When designing an aluminum PCB, it is crucial to consider factors such as dielectric material selection, copper foil thickness, thermal via placement, and aluminum substrate properties. By optimizing these design elements and employing appropriate thermal management techniques, engineers can create aluminum PCBs that meet the demanding requirements of various industries, from LED lighting and power electronics to automotive systems and aerospace applications.
As electronic devices continue to become more compact and powerful, the need for efficient thermal management solutions will only grow. Aluminum PCBs are well-positioned to meet this challenge, offering a proven, cost-effective, and versatile approach to managing heat in a wide range of applications.
Leave a Reply