Introduction to PCB Prototyping
Printed Circuit Board (PCB) prototyping is an essential part of the electronics design process. It involves creating a physical prototype of a PCB design to test its functionality, reliability, and manufacturability before mass production. PCB prototyping helps identify and fix design flaws early in the development cycle, saving time and money in the long run.
In this article, we will explore the fundamentals of PCB prototyping and the PCB design flow. We will cover topics such as PCB design software, PCB materials, PCB layout techniques, PCB manufacturing processes, and PCB testing methods. By the end of this article, you will have a solid understanding of the PCB prototyping process and how to create high-quality PCB Prototypes.
PCB Design Software
The first step in PCB prototyping is to create a digital design using PCB design software. There are many PCB design software options available, ranging from free open-source tools to professional-grade commercial software. Some popular PCB design software include:
Software | Vendor | Price |
---|---|---|
Eagle | Autodesk | Free for non-commercial use, paid plans available |
KiCad | KiCad | Free and open-source |
Altium Designer | Altium | Paid, starting at $2,950 per year |
OrCAD | Cadence | Paid, contact vendor for pricing |
When choosing PCB design software, consider factors such as ease of use, features, compatibility with other tools, and price. Many PCB design software offer free trials or limited versions, so you can try them out before committing to a purchase.
PCB Design Workflow
The PCB design workflow typically involves the following steps:
-
Schematic capture: Create a schematic diagram of the circuit using the PCB design software. The schematic shows the components and their interconnections.
-
Component placement: Place the components on the PCB layout, taking into account factors such as component size, pin spacing, and thermal considerations.
-
Routing: Connect the components using copper traces, following design rules such as minimum trace width, spacing, and via size.
-
Design rule check (DRC): Run a DRC to ensure the PCB layout meets the manufacturing specifications and design rules.
-
Output files generation: Generate the output files needed for PCB manufacturing, such as Gerber files, drill files, and bill of materials (BOM).
PCB Materials
The choice of PCB material depends on factors such as the application, operating environment, and cost. The most common PCB materials are:
Material | Description | Applications |
---|---|---|
FR-4 | A composite material made of fiberglass and epoxy resin | General-purpose PCBs |
Polyimide | A high-temperature material with excellent thermal stability | High-reliability aerospace and military applications |
Aluminum | A metal-core PCB with high thermal conductivity | High-power LED lighting and power electronics |
Flexible | A thin, flexible PCB made of polyimide or polyester | Wearable electronics and compact devices |
When selecting a PCB material, consider its electrical properties (such as dielectric constant and loss tangent), mechanical properties (such as strength and flexibility), and thermal properties (such as glass transition temperature and thermal conductivity).
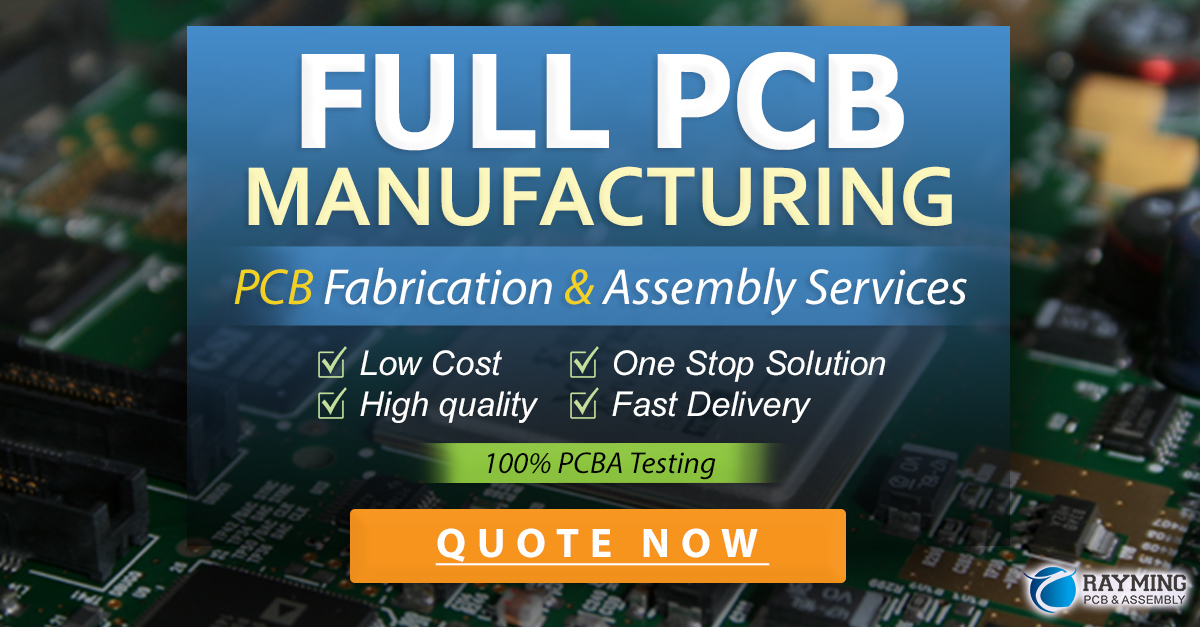
PCB Layout Techniques
Proper PCB layout techniques are critical for ensuring the functionality, reliability, and manufacturability of the PCB. Some important PCB layout techniques include:
Component Placement
- Place components in a logical order, following the signal flow from input to output.
- Group related components together to minimize trace lengths and improve signal integrity.
- Consider the mechanical constraints, such as component height and clearance.
Routing
- Use the appropriate trace width for the current carrying capacity and impedance requirements.
- Avoid sharp corners and use 45-degree angles for trace routing to reduce signal reflections.
- Provide adequate spacing between traces to minimize crosstalk and electromagnetic interference (EMI).
Grounding and Power Distribution
- Use a solid ground plane to provide a low-impedance return path for signals.
- Decouple power supplies with capacitors close to the power pins of ICs.
- Use power planes or wide traces for power distribution to minimize voltage drops.
Signal Integrity
- Match trace lengths for differential pairs and critical signals.
- Use termination resistors to minimize signal reflections.
- Avoid crossing split planes with signals to prevent discontinuities.
PCB Manufacturing Processes
Once the PCB design is complete, the next step is to manufacture the physical PCB prototype. The PCB manufacturing process involves several steps:
-
PCB fabrication: The PCB is fabricated using a process called photolithography. The copper layers are selectively etched away to create the desired trace patterns.
-
Solder mask application: A protective solder mask is applied to the PCB to insulate the copper traces and prevent short circuits.
-
Silkscreen printing: The component labels and other markings are printed on the PCB using silkscreen printing.
-
Surface finish application: A surface finish, such as HASL (Hot Air Solder Leveling) or ENIG (Electroless Nickel Immersion Gold), is applied to the exposed copper pads to prevent oxidation and improve solderability.
-
PCB assembly: The components are soldered onto the PCB using automated pick-and-place machines and reflow ovens.
PCB Testing Methods
After the PCB prototype is manufactured, it must be thoroughly tested to ensure it functions as intended. Some common PCB testing methods include:
Visual Inspection
- Check for obvious defects such as missing components, solder bridges, or damaged traces.
- Use a magnifying glass or microscope to inspect fine details.
Continuity Testing
- Use a multimeter to check for continuity between points that should be connected.
- Check for short circuits between adjacent traces or pins.
Functional Testing
- Apply power to the PCB and test its functionality using test equipment such as oscilloscopes, logic analyzers, or signal generators.
- Verify that the PCB performs as expected under various operating conditions.
Boundary Scan Testing
- Use JTAG (Joint Test Action Group) boundary scan testing to test the interconnections between ICs on the PCB.
- Boundary scan testing can help identify manufacturing defects such as open or short circuits.
PCB Design for Manufacturability (DFM)
To ensure that the PCB prototype can be easily and reliably manufactured, it is important to follow Design for Manufacturability (DFM) guidelines. Some key DFM considerations include:
- Adhere to the manufacturer’s design rules and specifications, such as minimum trace width and spacing, hole size, and copper thickness.
- Avoid using non-standard components or packaging that may be difficult to source or assemble.
- Provide adequate clearance around components for automated assembly machines.
- Include fiducial marks and tooling holes to aid in PCB registration and alignment during manufacturing.
Conclusion
PCB prototyping is a critical step in the electronics design process that helps validate the functionality and manufacturability of a PCB design. By following best practices in PCB design, material selection, layout techniques, manufacturing processes, and testing methods, you can create high-quality PCB prototypes that meet your design requirements and exceed customer expectations.
Frequently Asked Questions (FAQ)
-
What is the difference between a PCB prototype and a production PCB?
A PCB prototype is a small batch of PCBs manufactured for testing and validation purposes, while a production PCB is a large volume of PCBs manufactured for end-use applications. PCB prototypes may have looser tolerances and use different manufacturing processes than production PCBs. -
How long does it take to get a PCB prototype?
The turnaround time for a PCB prototype depends on factors such as the complexity of the design, the PCB material, and the manufacturer’s workload. Typical turnaround times range from a few days to a few weeks. -
How much does a PCB prototype cost?
The cost of a PCB prototype depends on factors such as the PCB size, layer count, material, and quantity. Small, simple PCB prototypes may cost a few dollars each, while large, complex PCB prototypes may cost hundreds of dollars each. Many PCB manufacturers offer discounts for larger quantities. -
Can I assemble the PCB prototype myself?
Yes, you can assemble the PCB prototype yourself using hand soldering techniques. However, for complex designs or high-volume production, it is recommended to use automated assembly processes to ensure consistency and reliability. -
What should I do if my PCB prototype doesn’t work as expected?
If your PCB prototype doesn’t work as expected, first perform visual inspection and continuity testing to identify any obvious defects. If the problem persists, use functional testing and boundary scan testing to isolate the issue. If necessary, modify the PCB design and fabricate a new prototype. It may also be helpful to consult with experienced PCB designers or engineers for guidance.
Leave a Reply