Introduction to PCB Vias
Printed Circuit Boards (PCBs) are essential components in modern electronics, providing a platform for interconnecting various electronic components. One crucial aspect of PCB design is the use of vias, which are conductive pathways that allow electrical signals to pass through different layers of the board. In this comprehensive guide, we will explore the eight types of PCB vias and their applications in PCB design.
What are PCB Vias?
PCB vias are small holes drilled through the layers of a PCB, which are then plated with a conductive material, typically copper. These conductive pathways enable electrical signals to travel between different layers of the board, allowing for more complex and compact circuit designs. Vias are essential for connecting components on different layers, as well as for providing ground and power connections.
The Importance of PCB Vias in PCB Design
PCB vias play a crucial role in PCB design for several reasons:
- Interconnectivity: Vias allow electrical signals to pass through different layers of the PCB, enabling the connection of components on different layers.
- Space Optimization: By utilizing vias, designers can create more compact and efficient PCB layouts, as components can be placed on different layers and connected through vias.
- Signal Integrity: Properly designed vias help maintain signal integrity by minimizing signal reflections and crosstalk.
- Thermal Management: Vias can also be used for thermal management, as they can help dissipate heat from components to other layers or to the outside of the board.
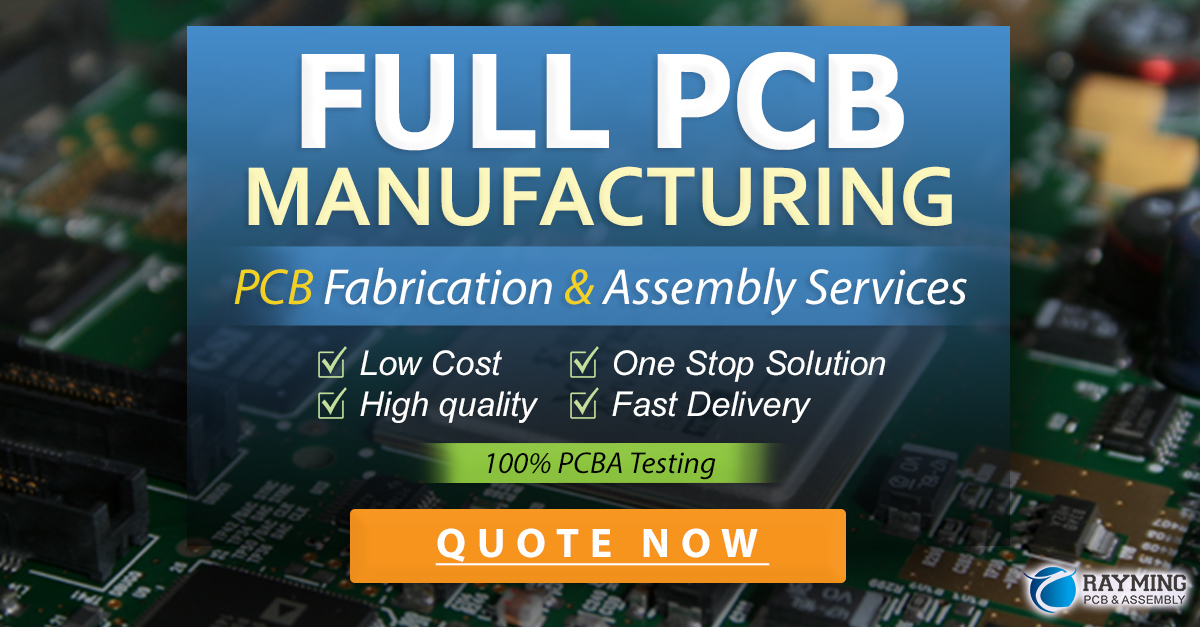
The 8 Types of PCB Vias
1. Through-Hole Vias
Through-hole vias are the most common type of via in PCB design. They are drilled through all layers of the PCB and are plated with a conductive material, typically copper. Through-hole vias provide a reliable and strong connection between layers, making them suitable for high-current applications and for connecting components that require mechanical stability.
Advantages of Through-Hole Vias
- Strong mechanical connection
- High current carrying capacity
- Easy to manufacture and inspect
Disadvantages of Through-Hole Vias
- Occupy more space on the PCB
- Limited routing flexibility
- Higher manufacturing costs compared to other via types
2. Blind Vias
Blind vias are drilled from one side of the PCB and terminate at a specific inner layer, without passing through the entire board. These vias are typically used to connect an outer layer to an inner layer, allowing for more efficient use of space on the PCB.
Advantages of Blind Vias
- Space-saving design
- Improved routing flexibility
- Reduced signal path length
Disadvantages of Blind Vias
- Higher manufacturing costs compared to through-hole vias
- Limited to connecting outer layers to inner layers
- More difficult to inspect and repair
3. Buried vias
Buried vias are drilled between two inner layers of the PCB and do not extend to either outer layer. These vias are used to connect two or more inner layers, allowing for even more efficient use of space and improved signal routing.
Advantages of Buried Vias
- Maximizes board space utilization
- Enhances signal routing flexibility
- Reduces signal path length
Disadvantages of Buried Vias
- Higher manufacturing costs compared to through-hole and blind vias
- Limited to connecting inner layers only
- More difficult to inspect and repair
4. Micro Vias
Micro vias are small, laser-drilled vias with diameters typically less than 0.15mm (6 mils). These vias are used for high-density interconnects (HDI) and are commonly found in advanced PCB designs, such as those used in smartphones and other compact electronic devices.
Advantages of Micro Vias
- Enable high-density interconnects
- Minimize signal path length
- Suitable for high-frequency applications
Disadvantages of Micro Vias
- Higher manufacturing costs due to specialized equipment
- Limited current carrying capacity
- More susceptible to manufacturing defects
5. Stacked Vias
Stacked vias are a combination of blind or buried vias that are aligned vertically, forming a continuous conductive path through multiple layers of the PCB. Stacked vias are used to create connections between non-adjacent layers, improving routing flexibility and signal integrity.
Advantages of Stacked Vias
- Enable connections between non-adjacent layers
- Improve routing flexibility
- Enhance signal integrity
Disadvantages of Stacked Vias
- Higher manufacturing costs due to multiple drilling and plating steps
- Increased Board Thickness
- More difficult to inspect and repair
6. Staggered Vias
Staggered vias are similar to stacked vias but are offset horizontally, rather than being aligned vertically. This arrangement helps minimize the impact of signal reflections and crosstalk, making staggered vias suitable for high-speed and high-frequency applications.
Advantages of Staggered Vias
- Reduce signal reflections and crosstalk
- Suitable for high-speed and high-frequency applications
- Improve signal integrity
Disadvantages of Staggered Vias
- Higher manufacturing costs due to precise drilling requirements
- Increased board space consumption
- More complex design and layout process
7. Via-in-Pad
Via-in-pad is a design technique where a via is placed directly on a component pad, allowing for a more compact PCB layout. This technique is commonly used in high-density designs and for connecting ball grid array (BGA) components.
Advantages of Via-in-Pad
- Enables more compact PCB layouts
- Reduces signal path length
- Suitable for high-density designs and BGA components
Disadvantages of Via-in-Pad
- Requires precise manufacturing processes
- Potential for solder wicking into the via during component assembly
- More susceptible to manufacturing defects
8. Thermal Vias
Thermal vias are used for heat dissipation, helping to transfer heat from components to other layers or to the outside of the PCB. These vias are typically placed near power-intensive components, such as voltage regulators or high-speed processors, to prevent overheating and ensure proper operation.
Advantages of Thermal Vias
- Improve heat dissipation
- Help prevent component overheating
- Enhance overall system reliability
Disadvantages of Thermal Vias
- Occupy additional board space
- May increase manufacturing costs
- Require careful design and placement for optimal performance
Choosing the Right Type of Via for Your PCB Design
When selecting the appropriate type of via for your PCB design, consider the following factors:
-
Board Complexity: The complexity of your PCB design will influence the type of vias required. Simple designs may only require through-hole vias, while more complex designs may benefit from blind, buried, or stacked vias.
-
Signal Integrity: For high-speed and high-frequency applications, consider using staggered vias or micro vias to minimize signal reflections and crosstalk.
-
Manufacturing Constraints: Some via types, such as micro vias and stacked vias, require specialized manufacturing processes and may increase production costs. Ensure that your chosen via type aligns with your manufacturing capabilities and budget.
-
Component Requirements: The type of components used in your design may dictate the use of specific via types. For example, BGA components often require via-in-pad techniques for proper connection.
-
Board Size and Space Constraints: If board space is limited, consider using blind, buried, or micro vias to maximize space utilization and routing flexibility.
PCB Via Design Best Practices
To ensure optimal performance and manufacturability of your PCB design, follow these best practices when incorporating vias:
-
Minimize Via Count: Use the minimum number of vias necessary to achieve the desired interconnectivity and signal integrity. Excessive via usage can increase manufacturing costs and decrease reliability.
-
Adhere to Manufacturing Constraints: Ensure that your via design adheres to your manufacturer’s specifications, such as minimum via diameter, drill size, and spacing requirements.
-
Consider Signal Integrity: When routing high-speed or high-frequency signals, use appropriate via types and placement techniques to minimize signal reflections, crosstalk, and impedance mismatches.
-
Optimize Via Placement: Place vias strategically to minimize signal path lengths, reduce EMI, and improve overall signal integrity. Avoid placing vias too close to component pads or in areas that may cause manufacturing issues.
-
Use Thermal Relief: When placing vias near large copper planes, such as ground or power planes, use thermal relief patterns to prevent solder wicking and ensure proper soldering of components.
Frequently Asked Questions (FAQ)
- What is the difference between a through-hole via and a blind via?
-
A through-hole via passes through all layers of the PCB, while a blind via only connects an outer layer to an inner layer without passing through the entire board.
-
When should I use micro vias in my PCB design?
-
Micro vias are typically used in high-density PCB designs, such as those found in smartphones and other compact electronic devices, where space is limited, and high-density interconnects are required.
-
How do staggered vias improve signal integrity?
-
Staggered vias are offset horizontally, which helps minimize signal reflections and crosstalk. This arrangement makes staggered vias suitable for high-speed and high-frequency applications.
-
What are thermal vias, and why are they used?
-
Thermal vias are used for heat dissipation, helping to transfer heat from components to other layers or to the outside of the PCB. They are typically placed near power-intensive components to prevent overheating and ensure proper operation.
-
How can I determine the appropriate via type for my PCB design?
- When choosing the appropriate via type, consider factors such as board complexity, signal integrity requirements, manufacturing constraints, component requirements, and board size and space constraints. Consult with your PCB Manufacturer for guidance on selecting the most suitable via type for your specific design.
Conclusion
PCB vias are essential elements in PCB design, enabling interconnectivity between layers and components while optimizing board space and signal integrity. Understanding the different types of vias and their applications is crucial for creating efficient, reliable, and high-performance PCB designs. By following best practices and carefully considering the specific requirements of your design, you can effectively incorporate vias into your PCB layout, ensuring optimal functionality and manufacturability.
Via Type | Description | Advantages | Disadvantages |
---|---|---|---|
Through-Hole | Drilled through all layers, plated with conductive material | Strong connection, high current capacity | Occupy more space, limited routing flexibility |
Blind | Drilled from one side, terminate at inner layer | Space-saving, improved routing flexibility | Higher cost, limited to outer-to-inner layer connection |
Buried | Drilled between inner layers, do not extend to outer layers | Maximizes space utilization, enhances routing | Higher cost, limited to inner layer connection |
Micro | Small, laser-drilled, diameters < 0.15mm | Enable high-density interconnects, minimize length | Higher cost, limited current capacity, more defects |
Stacked | Combination of blind/buried vias, aligned vertically | Connect non-adjacent layers, improve routing | Higher cost, increased thickness, difficult to inspect |
Staggered | Similar to stacked, offset horizontally | Reduce reflections and crosstalk, improve integrity | Higher cost, increased space, complex design |
Via-in-Pad | Via placed directly on component pad | Compact layouts, reduces signal length | Precise manufacturing, potential for solder wicking |
Thermal | Used for heat dissipation, placed near power-intensive components | Improve heat dissipation, prevent overheating | Occupy additional space, may increase cost |
As PCB designs continue to evolve and become more complex, staying informed about the various types of vias and their applications will be essential for engineers and designers. By leveraging the appropriate via types and following best practices, you can create PCBs that are efficient, reliable, and capable of meeting the ever-increasing demands of modern electronics.
Leave a Reply