What is an LED PCB Board?
An LED PCB (printed circuit board) is a specialized type of circuit board designed to power and control LEDs (light-emitting diodes). LED PCBs provide the electrical connections and heat dissipation necessary for LEDs to function optimally in various lighting applications.
LEDs offer many advantages over traditional lighting sources such as incandescent and fluorescent bulbs. They are more energy-efficient, have a longer lifespan, generate less heat, and can produce a wide range of colors. However, LEDs require specific driving circuits and thermal management to operate reliably. This is where LED PCBs come in.
LED PCBs are manufactured using materials and techniques that cater to the unique requirements of LEDs. They typically feature a conductive layer of copper traces for electrical connections, along with a dielectric substrate for insulation and mechanical support. Additional layers and components may be added depending on the complexity of the circuit design.
The layout and construction of an LED PCB can greatly impact the performance, efficiency, and longevity of the LED system. Factors such as trace width, copper thickness, thermal vias, and component placement all play a role in optimizing the circuit for its intended application.
Types of LED PCB Boards
There are several types of LED PCB boards, each with its own characteristics and uses. The following table summarizes the main types:
Type | Description | Common Applications |
---|---|---|
Rigid LED PCB | Standard, non-Flexible PCB | General lighting, signage |
Flexible LED PCB | Thin, bendable PCB made of flexible materials | Wearables, automotive lighting |
Metal Core LED PCB | PCB with a metal core for enhanced heat dissipation | High-power LEDs, spotlights |
Aluminum LED PCB | PCB with an aluminum substrate for heat dissipation | LED displays, grow lights |
High-Density Interconnect (HDI) LED PCB | PCB with fine-pitch traces and vias for compact designs | Miniature LED devices, portable electronics |
Ceramic LED PCB | PCB with a ceramic substrate for high-temperature resistance | Harsh environments, industrial lighting |
Let’s dive deeper into each type of LED PCB and explore their features, benefits, and applications.
1. Rigid LED PCB
Rigid LED PCBs are the most common type of LED circuit board. They are made of a solid, non-flexible substrate material such as FR-4 (a flame-retardant fiberglass-reinforced epoxy laminate). Rigid PCBs offer good mechanical stability, making them suitable for a wide range of LED lighting applications.
Key features of rigid LED PCBs include:
– Sturdy construction for reliable operation
– Excellent electrical insulation properties
– Cost-effective for high-volume production
– Available in single-layer or multi-layer configurations
Rigid LED PCBs are widely used in general lighting fixtures, signage, automotive rear lights, and LED displays. They provide a stable platform for mounting LEDs and associated components, ensuring consistent performance over time.
2. Flexible LED PCB
Flexible LED PCBs, also known as flex PCBs or FPCBs, are made of thin, bendable materials such as polyimide or polyester. These materials allow the PCB to conform to curved surfaces or fold into compact spaces, making them ideal for applications where flexibility is required.
Advantages of flexible LED PCBs include:
– Lightweight and thin profile for space-constrained designs
– Ability to bend, fold, or twist without damaging the circuit
– Resistance to vibration and shock
– Reduced assembly time and costs compared to rigid PCBs in certain applications
Flexible LED PCBs are commonly used in wearable electronics, automotive interior lighting, and compact LED devices. They enable designers to create unique form factors and integrate LEDs into previously impossible spaces.
3. Metal Core LED PCB
Metal Core PCBs (MCPCBs) are designed to address the thermal management challenges associated with high-power LEDs. These PCBs feature a metal core, typically made of aluminum, which acts as a heat sink to quickly dissipate heat away from the LEDs.
Benefits of metal core LED PCBs include:
– Excellent thermal conductivity for efficient heat dissipation
– Improved LED performance and longevity due to lower operating temperatures
– Ability to handle higher power densities compared to standard PCBs
– Reduced need for external heat sinks, saving space and cost
Metal core LED PCBs are used in applications that demand high luminous flux, such as high-bay lighting, spotlights, and outdoor floodlights. They ensure that the LEDs remain within their safe operating temperature range, preventing premature failure and maintaining optimal light output.
4. Aluminum LED PCB
Aluminum LED PCBs are a specific type of metal core PCB that uses an aluminum substrate instead of the traditional FR-4 material. The aluminum substrate offers several advantages over other PCB materials when it comes to thermal management and mechanical stability.
Key features of aluminum LED PCBs include:
– High thermal conductivity for efficient heat dissipation
– Excellent mechanical strength and rigidity
– Resistance to thermal expansion and contraction
– Compatibility with standard PCB manufacturing processes
Aluminum LED PCBs are commonly used in LED displays, grow lights, and industrial lighting applications. They provide a reliable and cost-effective solution for managing the heat generated by high-power LEDs, ensuring consistent performance and extended lifespan.
5. High-Density Interconnect (HDI) LED PCB
HDI LED PCBs are designed to accommodate the increasing demand for miniaturization and high-density component integration in LED devices. These PCBs feature fine-pitch traces and vias, allowing for more compact and complex circuit layouts.
Advantages of HDI LED PCBs include:
– Increased circuit density for smaller form factors
– Improved signal integrity due to shorter trace lengths
– Reduced power consumption and EMI (electromagnetic interference)
– Enhanced reliability and functionality
HDI LED PCBs are used in applications such as miniature LED devices, portable electronics, and high-resolution LED displays. They enable designers to create compact, feature-rich LED products that meet the ever-growing demands of the market.
6. Ceramic LED PCB
Ceramic LED PCBs are made using a ceramic substrate, typically alumina (aluminum oxide) or aluminum nitride. These materials offer exceptional thermal conductivity and high-temperature resistance, making them suitable for LED applications in harsh environments.
Benefits of ceramic LED PCBs include:
– Excellent thermal management properties for high-power LEDs
– High electrical insulation and low dielectric loss
– Resistance to thermal shock and mechanical stress
– Compatibility with high-temperature soldering processes
Ceramic LED PCBs are used in industrial lighting, automotive lighting, and outdoor applications where the LEDs are exposed to extreme temperatures or demanding environmental conditions. They ensure reliable operation and extended service life in these challenging settings.
FAQ
1. What are the advantages of using LED PCBs over traditional lighting PCBs?
LED PCBs offer several advantages over traditional lighting PCBs:
– Improved energy efficiency and lower power consumption
– Longer lifespan and reduced maintenance costs
– Compact size and flexibility in design
– Faster switching and dynamic control capabilities
– Environmentally friendly and recyclable materials
2. How do I choose the right type of LED PCB for my application?
Choosing the right type of LED PCB depends on several factors:
– Power requirements and thermal management needs
– Mechanical constraints and flexibility requirements
– Environmental conditions and operating temperature range
– Budget and production volume
– Required features and functionality
Consider consulting with an experienced LED PCB manufacturer or designer to determine the best option for your specific application.
3. Can LED PCBs be customized to meet specific design requirements?
Yes, LED PCBs can be customized to meet specific design requirements. Manufacturers offer a range of customization options, including:
– Custom board shapes and sizes
– Specific copper weights and trace widths
– Different substrate materials and thicknesses
– Additional features such as thermal vias, reflective coatings, or embedded components
Work closely with your chosen LED PCB manufacturer to discuss your custom design needs and ensure they can accommodate your requirements.
4. How do I ensure proper thermal management for my LED PCB?
Proper thermal management is crucial for LED PCBs to ensure optimal performance and longevity. Consider the following strategies:
– Use a metal core or aluminum PCB for enhanced heat dissipation
– Incorporate thermal vias to transfer heat from the LED pads to the PCB substrate
– Use thick copper traces to improve thermal conductivity
– Implement adequate spacing between LEDs to prevent thermal crosstalk
– Consider using external heat sinks or active cooling solutions for high-power applications
Conduct thorough thermal simulations and testing to validate your LED PCB Design and ensure it meets the required thermal performance criteria.
5. What are the key considerations when designing an LED PCB layout?
When designing an LED PCB layout, consider the following key factors:
– Proper component placement for optimal thermal management and light distribution
– Adequate trace width and copper thickness to handle the required current
– Minimizing trace lengths to reduce voltage drop and improve efficiency
– Implementing appropriate grounding and shielding techniques to minimize EMI
– Ensuring sufficient space for mounting holes, connectors, and other mechanical features
– Adhering to the manufacturer’s recommended footprints and design guidelines for the chosen LEDs
Follow best practices for PCB layout design and work with experienced engineers to ensure your LED PCB layout is optimized for performance, reliability, and manufacturability.
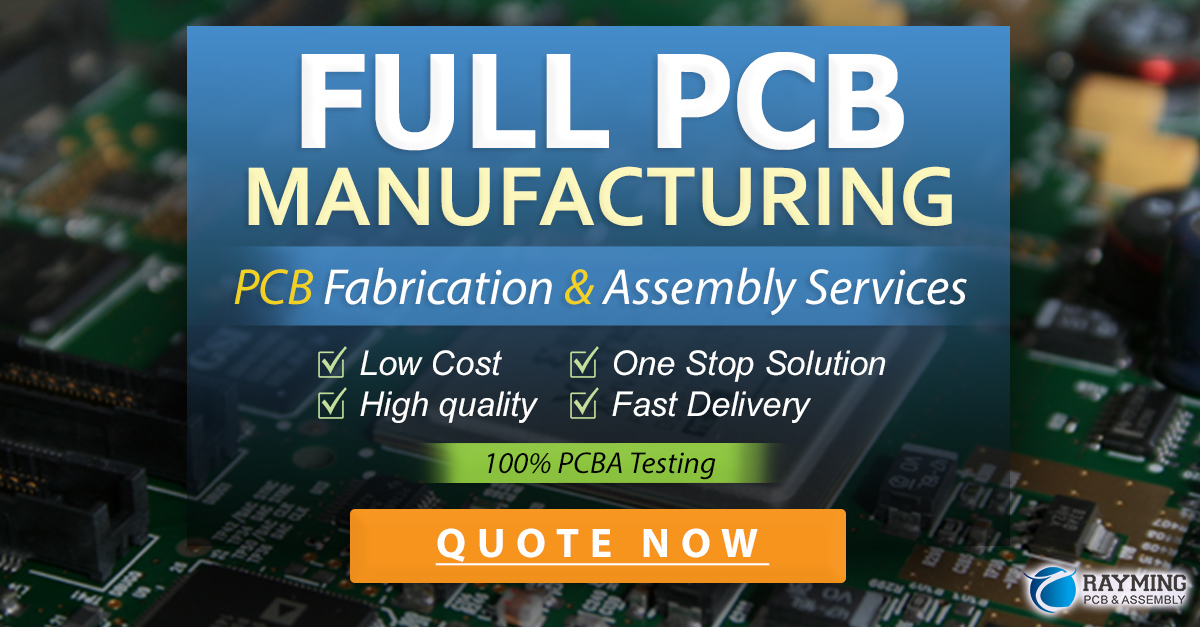
Conclusion
LED PCBs play a crucial role in the development of modern lighting solutions, offering improved efficiency, flexibility, and functionality compared to traditional lighting PCBs. Understanding the different types of LED PCBs and their unique characteristics is essential for selecting the right option for your application.
From rigid and flexible PCBs to metal core and ceramic substrates, each type of LED PCB offers specific advantages in terms of thermal management, mechanical stability, and design flexibility. By carefully considering your requirements and working with experienced LED PCB manufacturers, you can create custom LED lighting solutions that meet the demands of your application.
As LED technology continues to evolve, so too will the capabilities of LED PCBs. Advancements in materials, manufacturing processes, and design tools will enable even more compact, efficient, and intelligent LED lighting systems in the future. By staying informed about the latest developments in LED PCB technology, designers and engineers can continue to push the boundaries of what is possible with LED lighting.
Leave a Reply