Introduction
Printed circuit boards (PCBs) are essential components in nearly all modern electronics. PCBs provide the physical structure and electrical connections between various components like integrated circuits, resistors, capacitors, etc. Flex PCBs, also known as flex circuits, offer advantages over traditional rigid PCBs in many applications due to their flexibility and durability.
Wurth Elektronik is a leading manufacturer of flex PCBs, offering a wide range of products and services. In this detailed guide, we will explore Wurth’s flex PCB capabilities, applications, design considerations, and benefits.
Overview of Wurth Flex PCBs
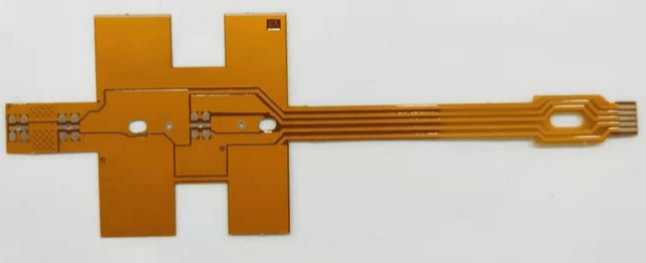
Wurth Elektronik produces single, double, and multilayer flex PCBs in various configurations. Their flex PCBs can integrate rigid sections, cover layers, shielding, and other features as needed by the application. Some key capabilities and options include:
- Flex stackups with 1 to 12 conductive layers
- Rigid-flex boards with rigid sections and flexible connectors
- Impedance controlled flex circuits from 25 ohms to 100 ohms
- Flexible dielectrics like polyimide and polyethylene
- Flexible soldermask and coverlayer coatings
- Shielding with aluminum, copper, or conductive polymers
- Gold plating over nickel for reliable connections
- Flex-to-board connectors like FFSD, SFSD, and HSD
- Various assembly and lamination options
Wurth utilizes advanced manufacturing techniques like laser direct imaging (LDI) for excellent repeatability and precision when producing complex flex PCB designs.
Typical Applications of Wurth Flex PCBs
Flex PCBs from Wurth Elektronik serve a diverse range of applications across consumer, industrial, automotive, aerospace, medical, and other markets. Here are some typical uses cases that benefit from flex circuits:
- Wearable devices – Flex PCBs can conform to curves and motion for wearable products like smart watches, fitness trackers, AR/VR headsets, etc.
- Medical devices – Flexible circuits work well in ultrasound transducers, hearing aids, patient monitoring systems, and other medical equipment where flexibility and space savings are needed.
- Automotive – Flex PCBs withstand vibration and temperature extremes, making them suitable for engine controls, sensors, lighting, seats, mirrors, and other automotive subsystems.
- Robotics – The dynamic bending and flexing requirements in robotics and automation are met by flexible PCB materials.
- Consumer electronics – Mobile phones, laptops, cameras, gaming systems, and appliances leverage flex PCBs for interconnects and internal wiring.
- Aerospace and defense – Rugged flex circuits perform reliably in the extreme conditions encountered in avionics, satellites, and missiles.
Design Considerations for Wurth Flex PCBs
Engineers should take into account several factors when designing flex PCBs to avoid issues and optimize the performance. Here are some key considerations:
Layer Stackup
Determining the right number of conductive layers is crucial based on complexity and cost targets. Signal layers should be balanced on both sides of the dielectric for stability. Wurth offers flex stackups from 1 to 12 layers.
Dielectric Material
Polyimide is most common, but polyethylene terephthalate (PET) and polyester are also options. The dielectric controls flexibility, temperature tolerance, and impedance.
Conductor Thickness
Thicker copper lowers resistance but reduces flexibility. Typical thicknesses are 1/2 oz (18 μm) to 2 oz (70 μm) copper. Thieving patterns can help optimize flexibility.
Bend Radius
Sharp bends can crack conductors or dielectrics. A minimum bend radius is required based on materials and stackup. Dynamic flexing also reduces flex life.
Stiffeners and Shielding
Adding protective covers, metal shields, and stiffener bars increases durability. But they also reduce flexibility in those regions.
Connectors
Specialized flex-to-board connectors like Flexi-Edge allow easy integration with rigid PCBs or cables. The connector style impacts durability.
Flex-to-Rigid Transition
Careful structural design is needed where flexible and rigid sections meet to avoid mechanical stresses.
Benefits of Wurth Flex PCBs
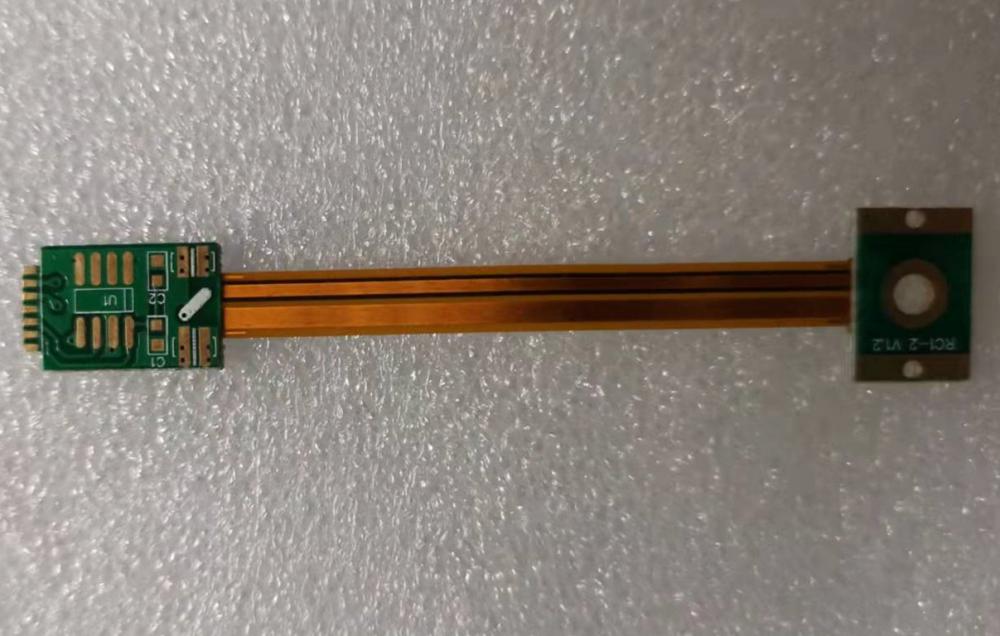
Compared to rigid boards, flex PCBs from Wurth offer a number of advantages:
- Flexibility – Can be bent, folded, twisted, and contorted to fit space constrained areas. Enables new packaging concepts.
- Lightweight – Weighs up to 75% less than rigid boards, important in portable and aerospace applications.
- Thin profile – Extremely thin cross-section down to 50 μm facilitates dense, compact electronics.
- Reliability – Dynamic flexing resisted with robust dielectric and conductor materials. Handles vibration and impacts.
- Simplified assembly – Integrated flex-to-board connectors eliminate soldering. Fewer separate components.
- Design freedom – Curved and three-dimensional conformal shapes open new possibilities for industrial design.
- Cost effectiveness – Reduces wiring, connectors, and manual assembly compared to discrete wires and cables.
For applications requiring thin, lightweight, and dynamically flexing interconnects, Wurth’s flex PCB capabilities deliver rugged and reliable performance. Their expertise in flex PCB design, materials, fabrication, and assembly ensures an optimized flex circuit solution.
Frequently Asked Questions
Here are some common questions about Wurth flex PCB technology and capabilities:
What are the minimum and maximum sizes for Wurth flex PCBs?
Wurth can produce extremely small flex PCBs with minimum line/space down to 25/25 μm (0.98/0.98 mil), enabling micro-circuits. Maximum panel size is 457 x 610 mm (18 x 24 inches). Complex designs are manufactured on smaller panels and assembled.
How many flex layer stackups does Wurth support?
Wurth supports stackups from 1 to 12 conductive layers. Typical configurations are 1, 2, and 4 layer. More layers allow complex rigid-flex designs but increase costs. Stackups balance dielectric materials on both sides of each signal layer.
What types of coatings and finishes are used on Wurth flex PCBs?
Standard soldermask, coverlayer, and legend inks are epoxy-based. These provide flex circuit protection and electrical insulation. Other options like polyurethane, acrylic, or urethane conformal coating can be applied. Finishes include immersion tin, gold, and ENIG.
Can Wurth perform DFM checks and pre-production prototypes of my flex PCB design?
Yes, Wurth offers design reviews and recommendations to identify any fabrication issues early. They can produce both functional and visual prototypes for design validation and testing before full production.
What is the typical lead time for production quantities of Wurth flex PCBs?
Lead times range from 2 to 8 weeks depending on order quantity, custom tooling, and materials sourcing. Prototypes can be delivered in 1 to 2 weeks. Expedited manufacturing may be possible for an additional fee. Contact Wurth sales to discuss target schedule.
Conclusion
Wurth Elektronik’s advanced flex PCB technology and solutions deliver valuable benefits across many industries. Their capabilities span single layer flex circuits to complex rigid-flex multilayer boards with integrated connectors. With stringent quality control and attention to detail, Wurth ensures reliable product performance even in challenging environments. For your next flex PCB project, the combination of innovation, expertise, and customer support from Wurth Elektronik merits strong consideration.
Leave a Reply