What is Circuit Board Blistering?
Circuit board blistering is a defect that occurs on the surface of printed circuit boards (PCBs) where small dome-shaped bumps or blisters form. These blisters can range in size from very tiny to several millimeters in diameter. Circuit board blistering is a serious issue that can compromise the integrity and functionality of the PCB.
Blistering typically occurs between the copper traces and the base laminate material of the PCB. The blisters form when gases or moisture trapped within the board expands due to heat exposure during the soldering process or other high-temperature operations. As the gases expand, they cause localized delamination of the copper from the underlying substrate, resulting in the characteristic dome-shaped blisters on the surface.
Causes of Circuit Board Blistering
There are several potential causes of blistering on PCBs:
1. Moisture Absorption
One of the primary causes of PCB blistering is moisture absorption by the board materials prior to high-temperature processes like soldering. PCB base materials are somewhat hygroscopic and can absorb moisture from the environment during storage or handling.
If a board has absorbed excessive moisture and is then subjected to high Soldering Temperatures, the moisture can vaporize and expand, causing localized delamination and blistering. Certain board materials are more susceptible to moisture absorption than others.
2. Insufficient Drying/Baking
To help prevent moisture-related blistering, PCBs need to be properly dried or baked prior to soldering or other high-temp processes. The baking process removes excess moisture from the board in a controlled way.
If the drying process is insufficient or skipped entirely, the board will retain too much moisture which can then cause blistering during soldering. Drying parameters like temperature, duration, and humidity levels must be carefully controlled for optimal results.
3. Incompatible Soldering Temperatures
Blistering can also occur if the soldering temperature is not compatible with the base materials and components used in the PCB construction. Excessively high soldering temperatures can scorch or damage the board substrate causing gases to form.
The leaded and lead-free soldering processes use different temperature profiles. The lead-free process requires higher temps. Using lead-free temps on a non-compatible board or vice versa can lead to blistering issues. The soldering temp must be matched to the board specs.
4. Contamination
Contamination of the PCB surface or base material can also potentially cause blistering in some cases. Ionic contaminants like sulfates and chlorides can weaken the bond between the copper traces and laminate.
If these contaminants are present in high concentrations, they can contribute to localized delamination and blistering, especially when combined with moisture and high-temp exposure. Thorough cleaning of boards prior to soldering is critical.
5. Improper Material Selection
Using improper or incompatible materials in the PCB construction can make blistering more likely to occur. The glass transition temperature (Tg) of the specific material is a key property to consider.
If the material’s Tg is too low for the processing temperature used, it can soften and expand excessively, making it more prone to blistering and delamination. Choosing high-Tg base materials matched to the expected processing and operating environment helps mitigate blistering risks.
Impact of Circuit Board Blistering
Blistering is a serious circuit board defect that can have major negative impacts on the reliability and functionality of the finished product. Some key impacts include:
Compromised Reliability
A PCB with blistering defects will have compromised reliability compared to a defect-free board. The blistered areas represent weakened spots in the copper to laminate bond. These blistered areas are prone to further delamination over time.
As the blister defects worsen and the copper delaminates further, it can lead to broken traces and circuit failures. This compromised reliability translates to a higher failure rate in the end use environment.
Damaged Components
In severe cases, blistering defects can also lead to damaged components. If the expanding blister breaks through the solder mask layer, it can lift or dislodge small surface mount components.
Damaged or missing components like resistors and capacitors can prevent the circuit from functioning properly. Rework to replace dislodged components takes extra time and expense and still may not restore full reliability.
Cosmetic Issues
Even if the blistering is relatively minor and does not cause immediate electrical issues, it still creates a cosmetic defect. In transparent products where the PCB is visible this cosmetic issue may be unacceptable to the customer.
Cosmetic flaws like blistering can hurt the perceived quality of the product. The blistered areas also represent latent defects which could worsen over time in the end use environment, impacting long-term reliability.
Scrap and Rework
Blistering defects caught during manufacturing will typically result in scrap or rework depending on the severity. Scrapped boards that have to be replaced represent an added expense and wasted material.
If the blistering is minor, technicians may be able to rework the affected areas. However, rework takes extra time and may not be feasible on boards with widespread blistering. Reworked areas may also have compromised appearance and reliability.
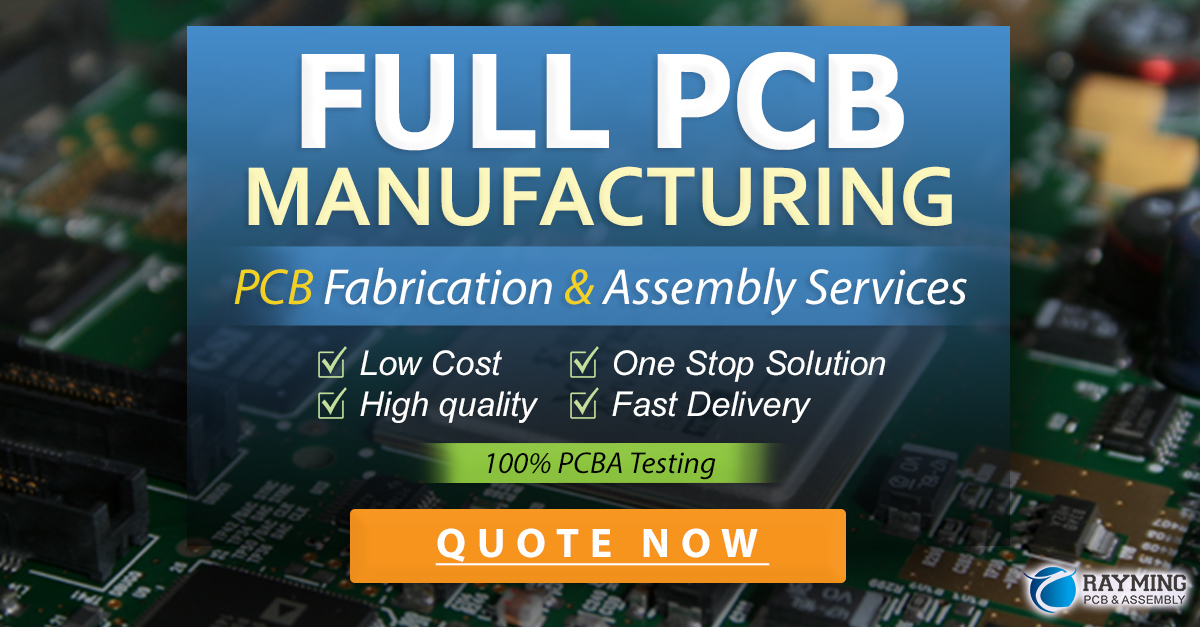
Prevention of Circuit Board Blistering
Preventing blistering defects is far more effective than trying to address the issue after the fact through rework or scrap. There are several best practices for minimizing the risk of blistering:
Proper Storage and Handling
Proper storage and handling of PCBs and base materials is critical for preventing moisture absorption that can lead to blistering. Bare Boards should be stored in a dry environment with controlled humidity levels.
The use of moisture barrier bags (MBBs) and desiccants can help protect moisture sensitive boards during storage and transport. Baking prior to soldering is still required if the boards are exposed to moisture before use.
Sufficient Prebaking
Prebaking PCBs before soldering or other high-temp processes is a must for preventing moisture-related blistering. The exact time and temperature parameters will vary based on board thickness and material.
In general, thicker boards will require longer baking times to fully dry. Following the manufacturer’s recommended baking guidelines for the specific board material is advised. Under-baking is a common mistake that leads to issues.
Soldering Profile Optimization
The reflow soldering profile should be optimized based on the PCB materials and components to minimize the risk of damage and blistering. Excessively high peak temperatures can scorch the board and cause blistering.
The ramp rate, time above liquidus, and cooling rate all need to be dialed in and kept consistent. For lead-free soldering especially, it’s critical that the profile does not exceed the documented maximum temperatures for the board material.
Contamination Control
Proper cleaning and contamination control during PCB fabrication and assembly can help minimize the risk of blistering defects. Keeping boards free of ionic contaminants will help maintain better copper to laminate adhesion.
Using clean, high quality base materials is also important. Contaminated Copper Clad laminate will be more prone to delaminating and blistering during reflow. Quality control checks of incoming materials can help screen out contaminated lots.
FAQ
What does blistering look like on a circuit board?
Blistering on a PCB appears as small dome-shaped bumps or protrusions on the surface of the board. These blisters can range in size from less than a millimeter to several millimeters in diameter. The size, number, and location of the blisters can vary depending on the root cause and severity of the defect.
Can you repair a blistered circuit board?
In some cases, minor blistering can be repaired through careful rework. This involves using a hot air pencil or soldering iron to carefully reflow and flatten the affected area. However, rework is not always feasible for severe or widespread blistering. Rework can also further compromise the integrity and appearance of the board. Scrapping and replacement is often required.
How can you tell if a PCB has absorbed too much moisture?
Moisture absorption is not always readily apparent by visual inspection alone. One method to check moisture levels is to bake a sample board and measure the weight before and after. If the weight loss exceeds 0.1% or so, the boards were likely too wet. Special moisture analyzers can also be used to directly measure the moisture content of board materials but this requires destructive testing.
Why is lead-free soldering more likely to cause blistering?
The lead-free soldering process requires higher temperatures compared to traditional leaded soldering. These higher temps can exacerbate other blistering risk factors like moisture absorption and material instability. The peak soldering temperature is often very close to the maximum limit for the board material which leaves little room for error. Even a small deviation can result in blistering.
What are the best base materials for preventing blistering?
In general, high-Tg materials like polyimide and certain ceramic compounds will have the best blister resistance. These materials can tolerate higher soldering temperatures without softening or expanding. The trade-off is that high-Tg materials also tend to be more brittle and expensive. Lower-Tg FR-4 materials can still be used successfully but the soldering parameters and moisture protection becomes more critical.
Cause | Prevention |
---|---|
Moisture absorption | Proper storage and handling with humidity control and moisture barrier bags |
Insufficient drying | Following manufacturer’s recommended prebaking guidelines for time and temp |
Incompatible soldering profile | Optimizing the reflow profile to stay within the documented tolerances for the specific board materials |
Contamination | Thorough cleaning, high quality base materials, and ionic contamination screening |
Improper material selection | Choosing high-Tg base materials that are compatible with the expected processing and operating conditions |
By understanding the causes of circuit board blistering and following industry best practices, manufacturers can greatly reduce the occurrence of this serious defect. Paying close attention to material storage, prebaking, soldering profiles, and contamination control will go a long way in ensuring a high quality, blister free product.
While some blistering issues can be corrected through careful rework, prevention is always the better approach. The rework process is time consuming and does not always fully restore the board. Blistered boards that cannot be reworked will need to be scrapped and replaced, adding to the production time and expense.
Ultimately, taking a proactive and comprehensive approach to blister prevention will yield the best results in terms of cost, cosmetics, and long-term reliability. Open communication between the PCB designer, fabricator, and assembler is also key to ensure that the material specs and processing parameters are fully optimized for the specific project.
Leave a Reply