Introduction to Vapor Phase Reflow
Vapor phase reflow is a soldering process that has gained popularity in recent years due to its ability to produce high-quality solder joints consistently. This technology uses a heated vapor to transfer heat to the printed circuit board (PCB) and components, allowing for a more uniform and controlled soldering process compared to traditional convection reflow methods.
What is Vapor Phase Reflow?
Vapor phase reflow is a soldering process that involves the use of a special fluid, typically a perfluoropolyether (PFPE), which is heated to its boiling point. The PCB and components are then placed in the vapor above the boiling fluid, where the latent heat of the vapor is transferred to the assembly, causing the solder to melt and form a connection between the components and the PCB.
Advantages of Vapor Phase Reflow
-
Uniform heat transfer: The vapor surrounds the PCB and components, providing a uniform heat transfer across the entire assembly. This results in consistent solder joint formation and reduces the risk of thermal damage to sensitive components.
-
Reduced void formation: The vapor environment minimizes the formation of voids in the solder joints, as the vapor displaces any trapped air or gases during the soldering process.
-
Improved wetting: The uniform heat transfer and controlled environment of vapor phase reflow promote better wetting of the solder, resulting in stronger and more reliable solder joints.
-
Lower peak temperatures: Vapor phase reflow typically operates at lower peak temperatures compared to convection reflow, reducing the risk of thermal damage to components and the PCB.
The Need for Vapor Phase Reflow Technology
Increasing Complexity of PCB Assemblies
As electronic devices become more advanced and compact, the complexity of PCB assemblies continues to increase. This complexity presents several challenges for the soldering process, including:
-
Higher component density: Modern PCBs often feature a high density of components, making it difficult to achieve uniform heat distribution using traditional convection reflow methods.
-
Varied component sizes and thermal mass: PCBs may contain components of different sizes and thermal mass, which can lead to uneven heating and cooling rates during the soldering process.
-
Temperature-sensitive components: Some components, such as certain sensors and optical devices, are particularly sensitive to high temperatures and may be damaged during the soldering process if not handled properly.
Vapor phase reflow addresses these challenges by providing a uniform and controlled heat transfer, ensuring that all components are soldered consistently and with minimal risk of thermal damage.
Demand for High-Quality Solder Joints
The reliability and performance of electronic devices depend heavily on the quality of the solder joints. Poor solder joint formation can lead to various issues, such as:
-
Intermittent connections: Weak or incomplete solder joints may result in intermittent electrical connections, causing device malfunctions or failures.
-
Reduced mechanical strength: Poor solder joints may not provide adequate mechanical support for components, making the assembly more susceptible to damage from vibration or physical stress.
-
Increased resistance: Improperly formed solder joints can have higher electrical resistance, leading to power loss and reduced device efficiency.
Vapor phase reflow technology helps to ensure the formation of high-quality solder joints by providing a controlled and uniform soldering environment, minimizing the risk of defects and improving the overall reliability of the electronic assembly.
Environmental and Health Considerations
Traditional soldering processes, such as hand soldering and convection reflow, often involve the use of lead-based solders and flux materials that can have negative environmental and health impacts. Lead is a toxic substance that can accumulate in the environment and pose risks to human health if not handled properly.
Vapor phase reflow technology supports the use of lead-free solders and reduces the need for aggressive flux materials, making it a more environmentally friendly and safer soldering process. The closed-loop nature of the vapor phase reflow system also minimizes the release of harmful fumes and particulates into the work environment, further reducing potential health risks for operators.
Implementing Vapor Phase Reflow Technology
Equipment and Setup
To implement vapor phase reflow technology, the following equipment and setup are required:
-
Vapor phase reflow oven: A specialized oven that contains the heated PFPE fluid and provides a controlled environment for the soldering process.
-
PCB carrier: A device used to hold and transport the PCB and components through the vapor phase reflow oven.
-
Solder paste and stencil: A solder paste suitable for vapor phase reflow is applied to the PCB using a stencil to ensure precise and consistent solder deposition.
-
Profiling and monitoring equipment: Tools used to measure and monitor the temperature profile of the PCB during the soldering process, ensuring that the desired profile is achieved.
Process Optimization
To achieve the best results with vapor phase reflow technology, it is essential to optimize the soldering process for each specific PCB assembly. This involves:
-
Developing a suitable temperature profile: The temperature profile should be designed to ensure that the solder melts and flows properly without causing thermal damage to the components or PCB.
-
Selecting the appropriate solder paste: The solder paste should be compatible with the vapor phase reflow process and the specific requirements of the PCB assembly, such as the desired alloy composition and particle size.
-
Adjusting the vapor phase reflow oven settings: The oven settings, such as the temperature and duration of the preheat and reflow stages, should be optimized based on the characteristics of the PCB assembly and the temperature profile.
-
Conducting regular maintenance: Regular maintenance of the vapor phase reflow oven, including cleaning and replacing the PFPE fluid as needed, helps to ensure consistent performance and prevent contamination of the soldering environment.
Integration with Other Manufacturing Processes
Vapor phase reflow technology can be integrated with other manufacturing processes to create a streamlined and efficient production line. This integration may involve:
-
Automated component placement: The use of automated pick-and-place machines to populate the PCB with components prior to the vapor phase reflow process.
-
Inline inspection: Incorporating automated optical inspection (AOI) or X-ray inspection systems to detect any soldering defects or component placement issues after the vapor phase reflow process.
-
Traceability and data management: Implementing systems to track and record process parameters and inspection results throughout the manufacturing process, enabling better quality control and continuous improvement.
By integrating vapor phase reflow technology with other manufacturing processes, companies can achieve higher levels of automation, consistency, and quality in their PCB assembly operations.
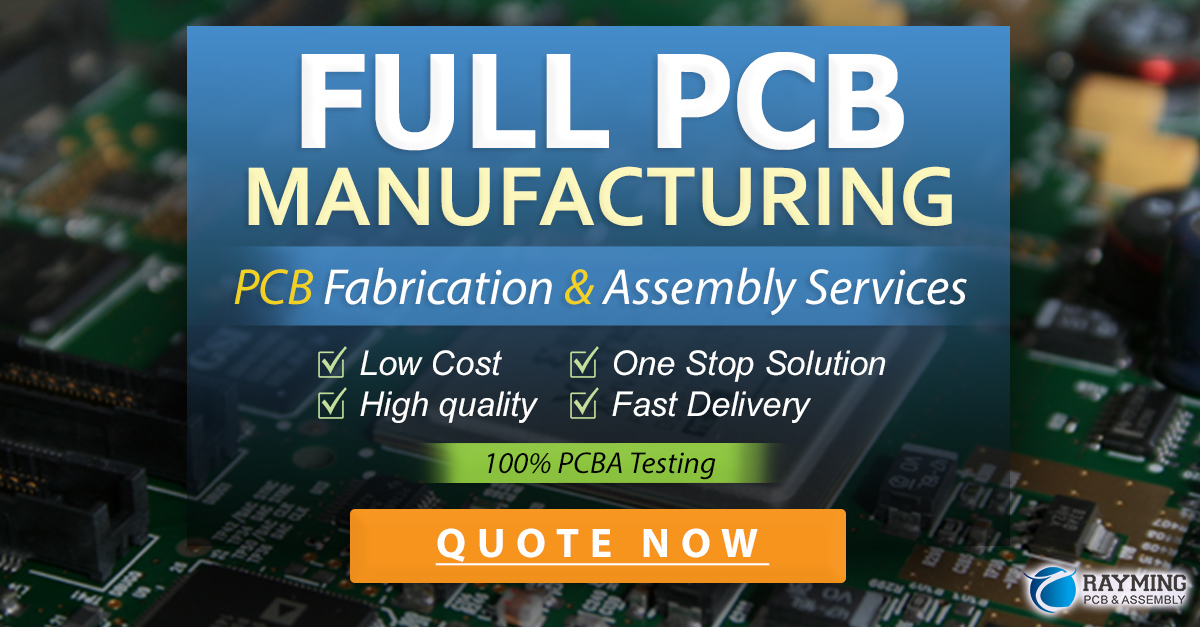
Case Studies and Applications
Automotive Electronics
Vapor phase reflow technology has found significant application in the automotive electronics industry, where the reliability and durability of electronic components are critical. Some examples include:
-
Engine control units (ECUs): These complex electronic modules require high-quality solder joints to withstand the harsh operating conditions and vibrations present in the automotive environment.
-
Sensors and actuators: Various sensors and actuators, such as temperature sensors and fuel injectors, rely on robust solder connections to ensure accurate and reliable performance.
-
Infotainment systems: The increasing complexity of automotive infotainment systems, including displays, audio systems, and navigation units, demands a soldering process that can handle high component density and varying thermal requirements.
Vapor phase reflow technology helps automotive electronics manufacturers to produce consistently high-quality solder joints, reducing the risk of failures and improving the overall reliability of their products.
Medical Devices
Medical devices often require exceptional levels of reliability and performance, as any malfunction can have serious consequences for patient health and safety. Vapor phase reflow technology is well-suited for the production of medical electronic assemblies, such as:
-
Implantable devices: Pacemakers, defibrillators, and neurostimulators require extremely reliable solder connections to ensure long-term functionality within the human body.
-
Diagnostic equipment: Medical imaging systems, such as X-ray machines and ultrasound devices, rely on high-quality electronic assemblies to produce accurate and detailed results.
-
Monitoring systems: Patient monitoring devices, such as ECG and EEG machines, must have robust and reliable electronic components to provide continuous and precise measurements.
By using vapor phase reflow technology, medical device manufacturers can achieve the necessary level of soldering quality and consistency to meet the stringent requirements of the healthcare industry.
Aerospace and Defense
The aerospace and defense industries have some of the most demanding requirements for electronic assemblies, as these components must operate reliably in extreme conditions, including high altitudes, temperature fluctuations, and intense vibrations. Vapor phase reflow technology is well-suited for the production of aerospace and defense electronics, such as:
-
Avionics systems: Flight control systems, communication equipment, and navigation devices require high-quality solder joints to ensure safe and reliable operation in the challenging aerospace environment.
-
Satellite components: Electronic components used in satellites must withstand the harsh conditions of space, including extreme temperature variations and radiation exposure.
-
Military equipment: Electronic systems used in military applications, such as tactical communication devices and weapon control systems, must be able to function reliably in demanding operational environments.
Vapor phase reflow technology provides the necessary soldering quality and consistency to meet the stringent requirements of the aerospace and defense industries, ensuring the reliability and performance of critical electronic systems.
FAQ
1. What is the main difference between vapor phase reflow and convection reflow soldering?
The main difference between vapor phase reflow and convection reflow soldering is the method of heat transfer. In vapor phase reflow, the heat is transferred to the PCB and components through a heated vapor, providing a uniform and controlled soldering environment. In convection reflow, the heat is transferred through hot air convection, which can result in less uniform heating and a higher risk of thermal damage to sensitive components.
2. Can vapor phase reflow technology be used with lead-free solders?
Yes, vapor phase reflow technology is compatible with lead-free solders and is often used in conjunction with these materials to create a more environmentally friendly and safer soldering process. The uniform heat transfer and controlled environment of vapor phase reflow help to ensure the formation of high-quality solder joints when using lead-free solders.
3. How does vapor phase reflow technology compare to hand soldering in terms of quality and efficiency?
Vapor phase reflow technology offers several advantages over hand soldering in terms of quality and efficiency. The uniform heat transfer and controlled environment of vapor phase reflow ensure consistent solder joint formation across the entire PCB, reducing the risk of defects and improving overall reliability. Additionally, vapor phase reflow is a highly automated process, allowing for faster and more efficient production compared to manual hand soldering.
4. What type of maintenance is required for a vapor phase reflow oven?
Maintenance for a vapor phase reflow oven typically involves regular cleaning to remove any flux residue or contaminants that may accumulate over time. The PFPE fluid used in the oven also needs to be periodically replaced to maintain its purity and ensure optimal performance. Additionally, the oven’s heating elements and control systems should be inspected and calibrated as needed to ensure accurate and consistent operation.
5. Can vapor phase reflow technology be used for both prototyping and high-volume production?
Yes, vapor phase reflow technology can be used for both prototyping and high-volume production. In prototyping applications, vapor phase reflow offers the advantage of consistent and high-quality solder joints, even for complex or sensitive assemblies. For high-volume production, vapor phase reflow can be integrated with automated component placement and inspection systems to create a streamlined and efficient manufacturing process, ensuring consistent quality and throughput.
Conclusion
Vapor phase reflow technology offers a superior alternative to traditional soldering methods, providing a uniform and controlled soldering environment that ensures the formation of high-quality solder joints. As electronic devices become increasingly complex and the demand for reliability and performance grows, the need for vapor phase reflow technology becomes more apparent.
By implementing vapor phase reflow in their manufacturing processes, companies can address the challenges posed by high component density, varied thermal requirements, and sensitive components. The technology also supports the use of lead-free solders and reduces the environmental and health risks associated with traditional soldering methods.
Across various industries, such as automotive electronics, medical devices, and aerospace and defense, vapor phase reflow technology has proven its value in producing reliable and high-performance electronic assemblies. As the electronics industry continues to evolve, the adoption of vapor phase reflow technology is likely to grow, driving innovation and improvement in PCB assembly processes.
Leave a Reply