Introduction to Quality Control
Quality control is a critical aspect of any business that aims to deliver high-quality products or services to its customers. It involves the systematic monitoring, evaluation, and maintenance of the quality of products or services to ensure that they meet the required standards and specifications. Quality control is particularly important for companies that rely on incoming materials or components from suppliers, as the quality of these inputs can significantly impact the quality of the final product.
In this article, we will explore the importance of an incoming quality control process for companies and how it can help them maintain the quality of their products, reduce costs, and improve customer satisfaction.
The Importance of Incoming Quality Control
Ensuring Product Quality
One of the primary reasons why a company needs an incoming quality control process is to ensure the quality of its products. By inspecting and testing incoming materials or components, companies can identify and reject any items that do not meet the required quality standards. This helps to prevent defective or substandard materials from entering the production process, which can lead to the manufacture of defective products.
Incoming Material | Inspection Method | Acceptance Criteria |
---|---|---|
Raw Materials | Visual Inspection | No visible defects |
Components | Dimensional Check | Within tolerances |
Packaging | Leak Test | No leaks detected |
Table 1: Example of an incoming quality control inspection plan
Reducing Costs
Another benefit of an incoming quality control process is that it can help companies reduce costs associated with defective products. When defective materials enter the production process, they can lead to the manufacture of defective products, which may need to be reworked or scrapped entirely. This can result in significant costs for the company, including the cost of materials, labor, and production downtime.
By implementing an incoming quality control process, companies can identify and reject defective materials before they enter the production process, thereby reducing the risk of manufacturing defective products and the associated costs.
Improving Customer Satisfaction
An incoming quality control process can also help companies improve customer satisfaction by ensuring that the products they deliver meet the required quality standards. When customers receive defective or substandard products, they are likely to be dissatisfied and may choose to take their business elsewhere. This can lead to a loss of revenue and damage to the company’s reputation.
By implementing an incoming quality control process, companies can ensure that the products they deliver to customers are of high quality and meet their expectations. This can help to improve customer satisfaction, build brand loyalty, and increase revenue over time.
Implementing an Incoming Quality Control Process
Establishing Quality Standards
The first step in implementing an incoming quality control process is to establish clear quality standards for incoming materials or components. These standards should be based on the specific requirements of the product or service being produced and should be communicated to suppliers to ensure that they understand what is expected of them.
Quality standards may include specifications for dimensions, tolerances, materials, and performance characteristics, among other things. They should be documented in a quality manual or other reference material and should be regularly reviewed and updated as necessary.
Developing Inspection and Testing Procedures
Once quality standards have been established, the next step is to develop inspection and testing procedures to ensure that incoming materials or components meet those standards. These procedures should be designed to identify any defects or non-conformances and should be carried out by trained and qualified personnel.
Inspection and testing procedures may include visual inspections, dimensional checks, functional tests, and other types of evaluations, depending on the nature of the product or service being produced. They should be documented in a quality control plan or other reference material and should be regularly reviewed and updated as necessary.
Implementing Corrective Actions
When defects or non-conformances are identified through the incoming quality control process, it is important to take corrective actions to prevent them from recurring in the future. This may involve working with suppliers to identify the root cause of the problem and implementing corrective actions to address it.
Corrective actions may include changes to the manufacturing process, modifications to the product design, or improvements to the supplier’s quality control processes. They should be documented in a corrective action report or other reference material and should be regularly reviewed and updated as necessary.
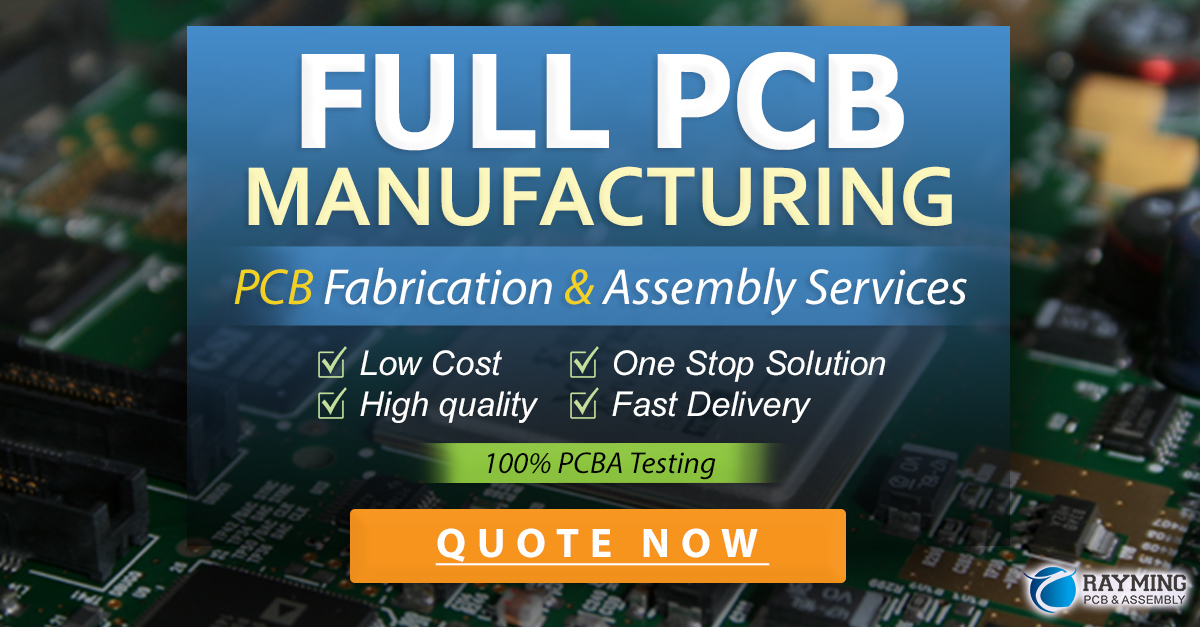
Benefits of an Incoming Quality Control Process
Improved Product Quality
One of the primary benefits of an incoming quality control process is that it can help companies improve the quality of their products. By identifying and rejecting defective materials or components before they enter the production process, companies can prevent the manufacture of defective products and ensure that the products they deliver to customers meet the required quality standards.
Product | Defect Rate (Before QC) | Defect Rate (After QC) |
---|---|---|
A | 5% | 1% |
B | 7% | 2% |
C | 10% | 3% |
Table 2: Example of the impact of an incoming quality control process on product defect rates
Reduced Costs
Another benefit of an incoming quality control process is that it can help companies reduce costs associated with defective products. By identifying and rejecting defective materials or components before they enter the production process, companies can avoid the costs associated with reworking or scrapping defective products.
In addition, an incoming quality control process can help companies identify opportunities for cost savings by working with suppliers to improve the quality of their materials or components. This can lead to reduced costs for the company over time.
Increased Customer Satisfaction
An incoming quality control process can also help companies increase customer satisfaction by ensuring that the products they deliver meet the required quality standards. When customers receive high-quality products that meet their expectations, they are more likely to be satisfied and to continue doing business with the company in the future.
In addition, an incoming quality control process can help companies identify and address quality issues before they impact customers, which can help to prevent customer complaints and improve the company’s reputation.
Frequently Asked Questions (FAQ)
1. What is incoming quality control?
Incoming quality control is the process of inspecting and testing incoming materials or components to ensure that they meet the required quality standards before they enter the production process.
2. Why is incoming quality control important?
Incoming quality control is important because it helps companies ensure the quality of their products, reduce costs associated with defective products, and improve customer satisfaction.
3. How can a company implement an incoming quality control process?
To implement an incoming quality control process, a company should establish clear quality standards for incoming materials or components, develop inspection and testing procedures to ensure that those standards are met, and implement corrective actions when defects or non-conformances are identified.
4. What are some common inspection and testing procedures used in incoming quality control?
Common inspection and testing procedures used in incoming quality control may include visual inspections, dimensional checks, functional tests, and other types of evaluations, depending on the nature of the product or service being produced.
5. What are the benefits of an incoming quality control process?
The benefits of an incoming quality control process include improved product quality, reduced costs associated with defective products, and increased customer satisfaction. An incoming quality control process can also help companies identify opportunities for cost savings and prevent customer complaints.
Conclusion
In conclusion, an incoming quality control process is a critical component of any company that aims to deliver high-quality products or services to its customers. By establishing clear quality standards, developing inspection and testing procedures, and implementing corrective actions when necessary, companies can ensure that the materials or components they receive from suppliers meet the required quality standards and are suitable for use in the production process.
Implementing an incoming quality control process can help companies improve product quality, reduce costs associated with defective products, and increase customer satisfaction. It can also help companies identify opportunities for cost savings and prevent customer complaints, which can lead to increased revenue and improved profitability over time.
While implementing an incoming quality control process may require an initial investment of time and resources, the long-term benefits far outweigh the costs. By making quality control a priority, companies can differentiate themselves from their competitors, build a strong reputation for quality, and position themselves for long-term success in their industry.
Leave a Reply