Introduction to PCB Simulation
Printed Circuit Board (PCB) simulation is a critical step in the design process of electronic systems. It involves using specialized software to model and analyze the behavior of a PCB before it is manufactured. The goal of PCB simulation is to identify and resolve any potential issues that may affect the performance, reliability, or manufacturability of the board.
There are two main types of PCB simulation: pre-layout and post-layout. Pre-layout simulation is performed before the physical layout of the board is created, while post-layout simulation takes place after the layout is complete. Each type of simulation has its own set of advantages and limitations, and understanding the differences between them is crucial for designers to make informed decisions throughout the design process.
Pre-Layout PCB Simulation
Pre-layout simulation, also known as schematic-level simulation, is the process of analyzing the electrical behavior of a circuit based on its schematic diagram. This type of simulation is typically performed using SPICE (Simulation Program with Integrated Circuit Emphasis) or similar tools.
Advantages of Pre-Layout Simulation
-
Early detection of design issues: Pre-layout simulation allows designers to identify and correct problems with the circuit’s functionality, performance, and power consumption early in the design process, before investing time and resources into the physical layout.
-
Faster iterations: Since pre-layout simulation does not require a complete physical layout, designers can quickly make changes to the schematic and re-simulate the circuit to assess the impact of those changes.
-
Reduced design time and cost: By catching and fixing issues early, pre-layout simulation can help reduce the overall design time and cost associated with PCB development.
Limitations of Pre-Layout Simulation
-
Idealized component models: Pre-layout simulation relies on idealized models of components, which may not accurately represent their real-world behavior, especially at high frequencies or under extreme operating conditions.
-
Lack of physical layout effects: Pre-layout simulation does not account for the effects of the physical layout, such as trace impedance, coupling, and parasitic elements, which can significantly impact the circuit’s performance.
-
Limited signal integrity analysis: While pre-layout simulation can provide some insight into signal integrity issues, it may not be able to fully capture the complex interactions between signals and the PCB environment.
Post-Layout PCB Simulation
Post-layout simulation, also known as layout-level simulation, is the process of analyzing the electrical behavior of a circuit based on its physical layout. This type of simulation takes into account the effects of the PCB layout, including trace geometry, layer stackup, and component placement.
Advantages of Post-Layout Simulation
-
Accurate representation of physical effects: Post-layout simulation provides a more realistic representation of the circuit’s behavior by incorporating the effects of the physical layout, such as trace impedance, coupling, and parasitic elements.
-
Comprehensive signal integrity analysis: With post-layout simulation, designers can perform in-depth signal integrity analysis, including crosstalk, reflections, and power integrity, to ensure the circuit will perform as expected in the real world.
-
Manufacturability assessment: Post-layout simulation can help identify potential manufacturability issues, such as signal integrity problems caused by improper trace routing or component placement, allowing designers to make necessary adjustments before sending the board for fabrication.
Limitations of Post-Layout Simulation
-
Longer simulation times: Post-layout simulation requires more computational resources and time compared to pre-layout simulation, due to the increased complexity of the model and the need to account for physical layout effects.
-
Late-stage design changes: If issues are discovered during post-layout simulation, making changes to the physical layout can be more time-consuming and costly compared to making changes at the schematic level.
-
Dependence on layout accuracy: The accuracy of post-layout simulation heavily relies on the accuracy of the physical layout model. Any discrepancies between the model and the actual layout can lead to inaccurate simulation results.
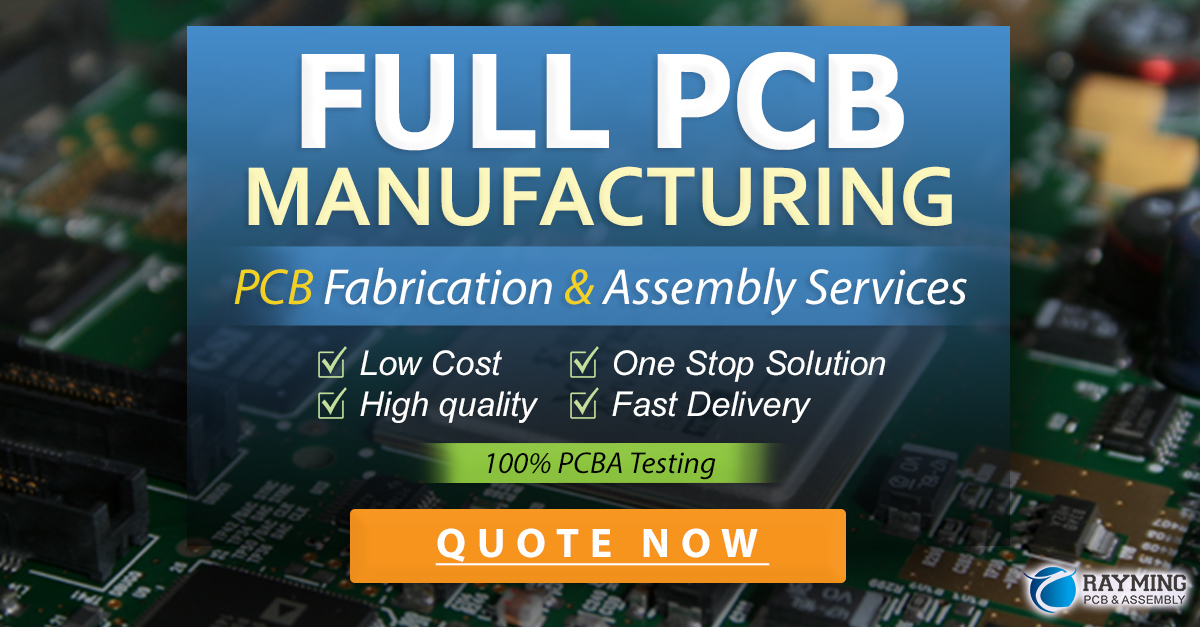
Comparing Pre-Layout and Post-Layout Simulation
The following table summarizes the key differences between pre-layout and post-layout PCB simulation:
Aspect | Pre-Layout Simulation | Post-Layout Simulation |
---|---|---|
Circuit Representation | Schematic diagram | Physical layout |
Component Models | Idealized models | Detailed models |
Physical Layout Effects | Not considered | Included |
Signal Integrity Analysis | Limited | Comprehensive |
Simulation Time | Faster | Slower |
Design Changes | Easier to implement | More time-consuming |
Manufacturability Assessment | Limited | Detailed |
Best Practices for PCB Simulation
To maximize the benefits of PCB simulation and ensure a successful design process, consider the following best practices:
-
Start with pre-layout simulation: Begin by performing pre-layout simulation to validate the circuit’s functionality and identify any initial design issues. This will help minimize the need for costly and time-consuming changes later in the design process.
-
Use accurate component models: Ensure that the component models used in both pre-layout and post-layout simulations are accurate and up-to-date. This may require obtaining models from component manufacturers or measuring the characteristics of critical components.
-
Collaborate with layout designers: Maintain open communication between circuit designers and layout designers to ensure that the physical layout meets the electrical requirements of the circuit. This collaboration can help identify and resolve potential issues early in the design process.
-
Perform iterative simulations: As the design progresses, perform multiple rounds of pre-layout and post-layout simulations to validate the circuit’s performance and identify any new issues that may arise due to layout changes or component substitutions.
-
Validate simulation results: Compare simulation results with real-world measurements to validate the accuracy of the models and identify any discrepancies. This will help refine the simulation process and improve the overall design quality.
FAQ
1. What software tools are used for PCB simulation?
There are several software tools available for PCB simulation, including:
- SPICE-based simulators: LTspice, PSpice, HSPICE, and Xyce
- Electronic design automation (EDA) tools: Altium Designer, Cadence OrCAD, Mentor Graphics PADS, and KiCad
- Electromagnetic field solvers: Ansys HFSS, CST Studio Suite, and Keysight ADS
2. Can PCB simulation completely replace physical prototyping?
While PCB simulation can significantly reduce the need for physical prototyping, it cannot completely replace it. Simulation results should be validated against real-world measurements to ensure the accuracy of the models and to identify any unforeseen issues that may not be captured in the simulation.
3. How do I choose between pre-layout and post-layout simulation?
The choice between pre-layout and post-layout simulation depends on the stage of the design process and the specific requirements of the project. In general, pre-layout simulation is useful for early-stage design validation, while post-layout simulation is essential for ensuring the manufacturability and real-world performance of the final design.
4. What are the main challenges in performing accurate PCB simulations?
Some of the main challenges in performing accurate PCB simulations include:
- Obtaining accurate component models, especially for high-frequency or non-linear devices
- Modeling complex physical phenomena, such as thermal effects, mechanical stress, and electromagnetic interference
- Managing the computational resources and time required for large and complex simulations
- Ensuring the accuracy and consistency of the simulation setup across different tools and platforms
5. How can I improve the efficiency of my PCB simulation workflow?
To improve the efficiency of your PCB simulation workflow, consider the following tips:
- Automate repetitive tasks, such as model creation and simulation setup, using scripts or templates
- Use a consistent and organized naming convention for components, nets, and simulation files
- Leverage the capabilities of your simulation tools, such as distributed computing and result visualization
- Regularly review and update your simulation models and libraries to ensure they are accurate and up-to-date
- Collaborate with colleagues and share best practices to streamline the simulation process and avoid duplication of effort
Conclusion
PCB simulation is an essential part of the electronic design process, allowing designers to validate the functionality, performance, and manufacturability of their circuits before committing to physical prototypes. By understanding the differences between pre-layout and post-layout simulation, and by following best practices for simulation setup and execution, designers can optimize their simulation workflow and achieve better design outcomes.
As PCB designs continue to increase in complexity and speed, the role of simulation in the design process will only become more critical. By staying up-to-date with the latest simulation tools and techniques, and by continuously refining their simulation skills, PCB designers can stay ahead of the curve and deliver high-quality, reliable, and manufacturable designs.
Leave a Reply