Introduction to PCBs
A printed circuit board (PCB) is the board base for physically supporting and wiring the surface-mounted and socketed components in most electronics. PCBs provide mechanical support and electrical connectivity, and help connect components together with conductive copper pathways, or traces. They are essential to the functioning of electronic devices.
PCBs are made from a variety of materials, providing insulation between layers of copper and serving as the structural base. The properties of these insulating materials determine much of the characteristics and performance capabilities of the PCBs. The most common base materials include:
FR-4
FR-4 glass epoxy is the most common PCB material used today. It consists of woven fiberglass cloth with an epoxy resin binder that is flame resistant (hence the FR designation). FR-4 offers a good balance of mechanical strength, dielectric properties, heat resistance, cost, and ease of manufacture.
CEM-1
Cellulose paper reinforced with phenolic resin. It has good dielectric properties but lower mechanical strength than FR-4. It is less common but still used for some low-cost consumer electronics.
CEI-Grade Paper
The CEI grade denotes prime grade cellulose paper bonded with thermoset adhesive. It is an inexpensive material used mainly for low density consumer products. It has poorer moisture absorption and chemical resistance compared to FR-4.
PTFE
Polytetrafluoroethylene (PTFE), commonly known by the brand name Teflon, has excellent electrical insulating ability and heat resistance. It is more expensive than FR-4 but needed for high performance circuit boards able to withstand very high temperatures.
CEM-3
This material consists of woven fiberglass cloth reinforced with an epoxy resin binder. It has excellent thermal performance suitable for auto-soldering processes. It has very low water absorption and improved mechanical characteristics over FR-4.
GETEK
GETEK is a cotton paper base laminated with an epoxy resin, typically used for cost-sensitive consumer electronics. It has good electrical properties but has limitations on heat resistance and structural strength compared to fiberglass-based PCBs. The material is fairly moisture absorbent.
Polyimide
Polyimide film provides superior heat resistance, chemical resistance and mechanical characteristics. Because of its high relative cost it is typically found in advanced electronics like aerospace systems that require rugged circuit boards. Common brands include Kapton and Vespel.
Some examples comparing select properties for common PCB substrate materials:
Material | Dielectric Constant | Dielectric Strength (kV/mm) | Water Absorption (%) | Glass Transition Temperature (°C) |
---|---|---|---|---|
FR-4 | 4.2-4.6 | 45-60 | 0.2-0.4 | 130-140 |
CEM-1 | 4-4.7 | 40-50 | 1-2 | 120-130 |
GETEK | 4-4.7 | 10-30 | 0.7-1 | 105-125 |
PTFE | 2.1 | 30-100 | 0 | 250-260 |
Polyimide | 3.4-3.6 | 200-400 | 0.3 | 360-410 |
Table 1: Dielectric and physical properties of select PCB substrate materials
But what are these PCB materials made out of, really? What are the key constituent components, and what gives the materials their unique characteristics? The rest of this article explores what the common PCB substrate materials introduced above are composed of.
What is FR-4 PCB made from?
FR-4 glass epoxy is composed of woven fiberglass cloth fabric “prepreg” sheets that are impregnated with an epoxy resin binder formulated for the lamination process. The components of FR-4 are:
Fiberglass Fabric
Fiberglass, or glass fiber, serves as the mechanically strong base reinforcement material. The glass fiber is extruded into very fine filaments, which are woven together into a cloth fabric. This gives sheets of fiberglass cloth with robust tensile strength, tear resistance, and dimensional stability.
The fiberglass is composed from silica sand (SiO2), limestone and soda ash as basic raw materials. These are melted together at very high temperature into glass, which is the drawn and woven into fine microfiber filaments. The fiberglass contributes the mechanical strength and ensures dimensional stability, preventing the PCB from warping or cracking.
The weave styles (e.g. plain, twilled, satin) impacts resin adhesion properties and ease of punching through holes. A tighter weave has more fiberglass by volume by area resulting in a stronger material. 106 style with around 106 threads per inch is common for standard consumer PCBs, while 7628 style with over 250 threads per inch provides high strength for cutting-edge electronics. Multilayer boards may use random chopped strand mat instead for uniform resin flow and adhesion between layers.
Epoxy Resin Binder
Epoxy is the primary polymer resin system impregnating and bounding the woven fiberglass layers together into an integrated composite material. Different formulations of epoxy resins and blends are used, often containing:
Bisphenol A Diglycidyl Ether – provides good adhesion, chemical resistance, and electrical insulation.
Bisphenol F Diglycidyl Ether – improves moisture absorption and alkali resistance.
Hardener or Curing Agents – typically aliphatic and aromatic amines to facilitate curing of epoxy into thermoset polymer with heat application and crosslinking of polymer chains. They enhance chemical bonding and mechanical strength.
Flame Retardants – restrict extent and speed of fire spreading. Most FR-4 includes tetrabromobisphenol-A type retardants meeting UL flammability standards. Some eco-friendly FR-4 is made without halogenated retardants.
Filler particles – inert particles like silica improve thermal and mechanical performance at reduced cost. Too much filler can make material brittle.
Additional epoxy components like flexibilizers, accelerators, and surfactants help tune resin viscosity, reactivity, and wetting action with fiber component.
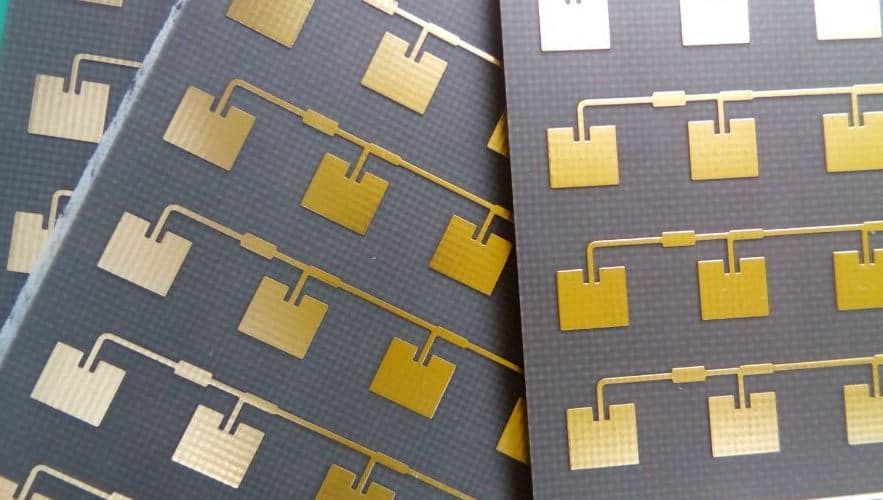
Composition of CEM-1 and CEI Laminates
CEM-1
Instead of fiberglass cloth, CEM-1 uses cellulose paper bonded with phenolic resin system as the core substrate:
Cellulose Paper – the cellulose paper, made from plant fiber, provides the base structural foundation with reasonable strength at low cost.
Phenolic Resin – the phenolic resin, consisting of phenol and formaldehyde components, penetrates and coats the cellulose fibers bonding them together. Heat application polymerizes the resin into crosslinked thermoset adhesive. The resin contributes mechanical support and electrical insulation and protects paper from moisture and aging.
Fillers – inert fillers like clay, silica, talc, calcium carbonate are often added to improve thermal conductivity, coefficient of thermal expansion and other properties.
CEI Grade Paper Laminates
Similarly, CEI grade circuit boards use cellulose paper bonded with thermoset adhesive as core:
Cellulose Paper – paper forms the supporting foundation reinforced by resin impregnation. Low density paper around 250-400 g/m^2 is typically used.
Thermoset adhesive – adhesive options include melamine, phenolic, or polyester/epoxy blends specially formulated to penetrate paper. Heat cures adhesive into crosslinked polymer imparting mechanical and dielectric strength. Flame retardants are added to meet safety standards.
Reinforcement Fabric Plies – CEI grades may also incorporate thin fiberglass fabric plies on exterior surfaces for enhanced structural and environmental integrity at low material cost.
GETEK – Cotton Paper & Epoxy
GETEK laminates use cotton paper base with epoxy resin binder infused for economy PCBs.
Cotton Paper – cotton linters provide the core foundation. It offers some cost savings over pricier synthetic papers.
Epoxy Resin – epoxy saturates and encapsulates the paper to give mechanical strength and moisture protection. Brominated formulations improve flame retardancy.
Fillers & Reinforcements – fillers like clay and silica may be used as extenders. Reinforcing fabric is sometimes bonded to surfaces for extra support on outer layers.
PTFE / Teflon Composition
Polytetrafluoroethylene or PTFE Teflon consists of long chain synthetic fluorocarbon polymers with carbon and fluorine composition:
(C2F4)n
Its makeup provides a highly stable, heat and chemical resistant structure. Specifically:
Carbon Backbone – carbon atoms link together the molecular chains with strong interatomic bonds allowing tight packing and crystallization imparting chemical and thermal stability.
Fluorine Atoms – fluorine tightly bonds to carbon providing strong electronegativity, lipophobicity and shielding effect against other chemical interactions. This produces excellent electrical insulation and low friction properties.
Tight Packed Crystals – the heavily packed crystals of linear PTFE chains account for its high melting point around 327°C and wide useful working range up to 260°C for circuit boards.
Fillers like mica, silica, graphite or fiberglass strengthen the pure PTFE and reduce the high costs of unfilled resin.
Polyimide Structure & Components
Polyimides contain aromatic heterocyclic imide groups as part of the polymer backbone unit connected by aromatic rings.
The polyimide used may be one of several related heterocyclic polymers, including:
Poly(4,4′-oxydiphenylenepyromellitimide)
Poly(4,4′-biphenylenepyromellitimide) (BPDA-PDA)
Poly(4,4′-benzophenone-tetracarboxylic dianhydride-oxydianiline) (BTDA-ODA)
They are characterized by imide rings attached to aromatic benzene structures. These rigid planar chains pack together tightly, requiring extremely high temperatures (~400-500°C) to mobilize and melt the crystallites. This accounts for their exceptional thermal and mechanical performance.
Common product names like Kapton and Vespel refer specifically to DuPont manufactured polyimide film or resin formulations. Additives like graphite or glass fiber bolster mechanical strength. Polyimide laminates offer top range electrical and physical properties for electronics exposed to high heat, stress and chemical environments.
Conclusion
This covers the main constituent ingredients comprising typical PCB substrate materials. While subtle variations in composition exist across manufacturer product lines, understanding the fundamental building blocks of core papers, fiber cloths, thermoset resins, and reinforcements provides insight into the origins of the materials’ attributes. The combination and relative fraction of components offer tradeoffs of electrical performance, mechanical specs, thermal ratings, moisture absorption, ease of processing, and product cost. Continuous innovation refines PCB laminates to achieve new functionality supporting cutting-edge electronics demand.
Frequently Asked Questions
What is the most common material for making PCBs?
The most ubiquitous PCB material used today is FR-4 glass epoxy. This consists of thick woven fiberglass cloth bonded with flame retardant epoxy resin. The fiberglass reinforcement gives good strength while the epoxy protects against environmental exposure. FR-4 offers an ideal balance of electrical performance, mechanical specs, heat resistance and cost.
What’s the difference between FR-4 and normal PCBs?
There is no specific “normal” PCB material, but this typically refers to comparison with basic phenolic paper or polyester laminates lacking flame retardants. FR-4 has fiberglass for much greater structural integrity and specially formulated epoxy resin to achieve UL flammability classification. It has higher heat ratings and superior electrical and mechanical characteristics over basic consumer-grade phenolic boards.
Can you use cotton paper as PCB substrate?
Yes, cotton paper like kraft or linter fiber paper can be utilized as the core substrate for low cost PCB laminate materials. Cotton paper offers some price advantage over synthetic papers for less demanding circuit board applications. The paper fibers are permeated with thermoset resin like epoxy to reinforce it as a composite material achieving solid dielectric and mechanical performance for printed wiring demands.
Why don’t PCBs melt under high temperature?
Most PCB materials like FR-4 use thermoset resin systems, like epoxy or polyimide, which crosslink into occupied 3D network structures. This produces solid materials that do not thermally flow or melt like thermoplastics. While the resins will char and degrade at temperature extremes, the high initial melt or glass transition temperatures – typically over 300°C for common PCB substrates – support robust thermal performance. Materials like PTFE maintain integrity above soldering temps.
Can you 3D print circuit boards?
Yes, additive manufacturing processes for printed circuit boards are emerging using specialized conductive and dielectric inks and base resins to construct layered wiring traces and boards. But traditional subtractive PCB fabrication currently remains far higher performance, higher reliability and lower cost than fledgling 3D printing methods. The bulk of rigid circuit board demands still utilize traditional lamination of pressed thermoset copper clad laminates sheets.
Leave a Reply