Introduction to ViaInPad
ViaInPad is a revolutionary technology that has transformed the world of printed circuit board (PCB) design and manufacturing. It is a process that involves creating electrical connections between different layers of a PCB using tiny holes called vias. These vias are filled with conductive material, allowing signals to pass through the layers of the board, enabling more complex and compact circuit designs.
What are Vias?
Vias are small holes drilled through a PCB that allow electrical connections to be made between different layers of the board. They are essential for creating multi-layer PCBs, which are used in a wide range of electronic devices, from smartphones and laptops to medical equipment and aerospace systems.
There are several types of vias, including:
- Through-hole vias: These vias go through all layers of the PCB and are typically used for mounting through-hole components.
- Blind vias: These vias start on an outer layer and end on an inner layer, but do not go through the entire board.
- Buried vias: These vias are located entirely within the inner layers of the PCB and do not appear on the outer layers.
The Importance of ViaInPad Technology
ViaInPad technology has become increasingly important in PCB Design and manufacturing due to the growing demand for smaller, more complex electronic devices. By allowing electrical connections to be made between layers of the board, ViaInPad enables designers to create more compact and efficient layouts, reducing the overall size and weight of the finished product.
Some of the key benefits of ViaInPad technology include:
- Increased circuit density: ViaInPad allows for more components and traces to be placed on a single board, enabling more complex designs in a smaller footprint.
- Improved signal integrity: By reducing the length of electrical paths, ViaInPad can help minimize signal loss and interference, resulting in better overall performance.
- Enhanced reliability: ViaInPad can help improve the mechanical strength and thermal performance of a PCB, making it more resistant to stress and temperature fluctuations.
The ViaInPad Manufacturing Process
The ViaInPad manufacturing process involves several key steps, each of which must be carefully controlled to ensure the quality and reliability of the finished product.
Step 1: PCB Design
The first step in the ViaInPad manufacturing process is to design the PCB Layout using specialized software. This involves determining the placement of components, traces, and vias on each layer of the board. The design must take into account factors such as signal integrity, power distribution, and thermal management to ensure optimal performance.
Step 2: Drilling
Once the PCB design is finalized, the next step is to drill the vias into the board. This is typically done using a computer-controlled drilling machine that can create holes with a diameter as small as 0.1mm. The machine must be carefully calibrated to ensure that the holes are drilled in the correct locations and to the correct depth.
Step 3: Plating
After the vias have been drilled, the next step is to plate them with a conductive material, typically copper. This is done using a process called electroplating, which involves immersing the board in a chemical bath and applying an electrical current to attract the copper ions to the surface of the vias.
Step 4: Filling
Once the vias have been plated, they must be filled with a non-conductive material to provide mechanical support and prevent short circuits. This is typically done using a specialized paste that is applied using a screen printing process. The paste is then cured using heat or ultraviolet light to harden it.
Step 5: Lamination
The final step in the ViaInPad manufacturing process is to laminate the layers of the PCB together using heat and pressure. This fuses the layers together and ensures that the vias are securely bonded to the board.
Advantages of ViaInPad Technology
ViaInPad technology offers several key advantages over traditional PCB manufacturing methods, including:
Increased Reliability
By filling the vias with a non-conductive material, ViaInPad helps to prevent short circuits and improve the mechanical strength of the board. This can help to reduce the risk of failure in harsh environments or under high stress conditions.
Improved Signal Integrity
ViaInPad can help to improve signal integrity by reducing the length of electrical paths and minimizing the risk of signal loss or interference. This is particularly important in high-speed applications where even small amounts of signal degradation can have a significant impact on performance.
Reduced Manufacturing Costs
ViaInPad technology can help to reduce manufacturing costs by enabling more complex designs to be produced on a smaller board. This can help to reduce material costs and simplify the assembly process, resulting in lower overall production costs.
Faster Time-to-Market
By enabling more complex designs to be produced quickly and efficiently, ViaInPad can help to reduce development times and speed up time-to-market for new products. This can be a significant advantage in fast-paced industries where being first to market can make all the difference.
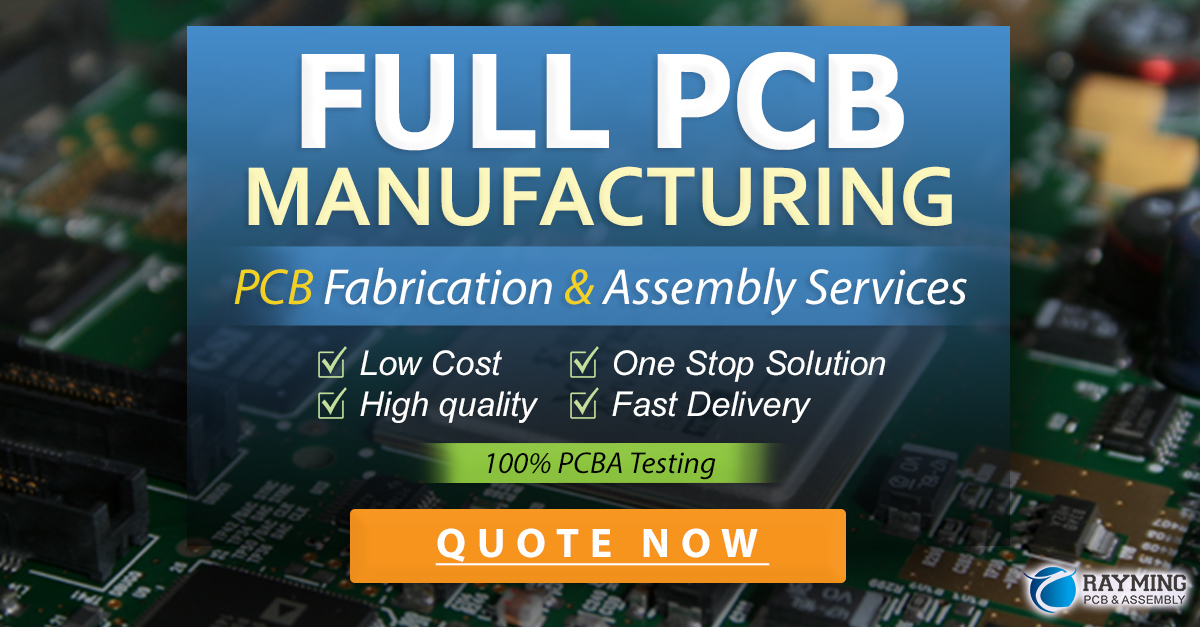
Applications of ViaInPad Technology
ViaInPad technology is used in a wide range of applications, from consumer electronics to aerospace and defense. Some of the most common applications include:
Smartphones and Tablets
ViaInPad is widely used in the production of smartphones and tablets, where the demand for smaller, more powerful devices has driven the need for more complex PCB designs. By enabling more components to be packed onto a single board, ViaInPad has helped to enable the development of ever-more sophisticated mobile devices.
Wearable Technology
ViaInPad is also increasingly being used in the production of wearable technology, such as smartwatches and fitness trackers. These devices require extremely compact and lightweight PCBs that can be easily integrated into the device housing, making ViaInPad an ideal solution.
Medical Devices
ViaInPad is used in the production of a wide range of medical devices, from diagnostic equipment to implantable devices such as pacemakers and insulin pumps. In these applications, reliability and signal integrity are critical, making ViaInPad an essential technology.
Aerospace and Defense
ViaInPad is also widely used in the aerospace and defense industries, where the demand for high-performance, reliable electronics is paramount. By enabling more complex designs to be produced in a smaller footprint, ViaInPad has helped to enable the development of advanced avionics, communication systems, and other critical technologies.
Challenges and Future Developments
Despite the many advantages of ViaInPad technology, there are still some challenges that must be overcome to fully realize its potential. One of the biggest challenges is the need for even smaller vias to enable even more complex designs. This requires advances in drilling and plating technologies, as well as new materials that can provide the necessary electrical and mechanical properties.
Another challenge is the need for better modeling and simulation tools to help designers optimize their layouts for signal integrity and thermal performance. As PCBs become more complex, the risk of signal degradation and thermal issues increases, making it essential to have accurate models that can predict and prevent these problems.
Despite these challenges, the future of ViaInPad technology looks bright. As the demand for smaller, more powerful electronic devices continues to grow, the need for advanced PCB manufacturing technologies will only increase. By enabling more complex designs to be produced quickly and efficiently, ViaInPad is poised to play a key role in shaping the future of the electronics industry.
Frequently Asked Questions (FAQ)
1. What is the minimum via size that can be achieved with ViaInPad technology?
The minimum via size that can be achieved with ViaInPad technology depends on the specific manufacturing process and equipment being used. However, most modern ViaInPad processes can achieve via sizes as small as 0.1mm in diameter.
2. How does ViaInPad compare to traditional through-hole vias in terms of reliability?
ViaInPad can offer improved reliability compared to traditional through-hole vias, particularly in harsh environments or under high stress conditions. This is because the filled vias provide better mechanical support and are less prone to cracking or delamination.
3. Can ViaInPad be used with any type of PCB material?
ViaInPad can be used with a wide range of PCB Materials, including standard FR-4, high-frequency laminates, and flexible substrates. However, the specific material and manufacturing process must be carefully selected to ensure optimal performance and reliability.
4. How much does ViaInPad technology add to the cost of PCB manufacturing?
The cost of ViaInPad technology varies depending on the specific manufacturing process and the complexity of the design. In general, ViaInPad can add a small premium to the cost of PCB manufacturing, but this is often offset by the benefits in terms of reliability, signal integrity, and design flexibility.
5. What are some of the key challenges in implementing ViaInPad technology?
Some of the key challenges in implementing ViaInPad technology include the need for advanced drilling and plating equipment, the development of new materials and processes to support smaller via sizes, and the need for better modeling and simulation tools to optimize designs for signal integrity and thermal performance. However, with ongoing research and development, these challenges are being addressed, paving the way for even more advanced ViaInPad solutions in the future.
Conclusion
ViaInPad technology has revolutionized the world of PCB design and manufacturing, enabling more complex and compact designs to be produced quickly and efficiently. By allowing electrical connections to be made between layers of the board, ViaInPad has opened up new possibilities for electronic devices, from smartphones and wearables to medical devices and aerospace systems.
While there are still challenges to be overcome, the future of ViaInPad technology looks bright. As the demand for smaller, more powerful devices continues to grow, the need for advanced PCB manufacturing technologies will only increase. With ongoing research and development, ViaInPad is poised to play a key role in shaping the future of the electronics industry, enabling even more advanced and innovative designs in the years to come.
Leave a Reply