Introduction to PCB Layer Stackup
A printed circuit board (PCB) is made up of multiple layers of conductive copper and insulating substrate materials laminated together into a single board. The layer stackup refers to the arrangement and order of these layers.
A typical PCB will have at least two layers – the top and bottom layers where components are placed and routed. More complex designs will have additional inner layers in between the top and bottom. These Inner PCB Layers allow for more dense routing and are essential for high-speed and high-frequency designs.
The number of layers needed depends on the complexity of the circuit, the component density, and the signal integrity and EMC requirements. Here is an overview of common PCB layer stackups:
Layers | Stackup | Typical Applications |
---|---|---|
1 | Single layer | Very simple circuits |
2 | Double sided | Most common for simple to moderate designs |
4 | Double sided + 2 internal planes | Moderately complex, single power/ground plane |
6 | Double sided + 4 internal planes | Complex, multiple power/ground planes |
8+ | Double sided + 6+ internal planes | Very complex, high speed, controlled impedance |
In this article, we’ll focus on the properties, manufacturing, and design considerations for the inner layers of the PCB.
Properties of PCB Inner Layers
Copper Weight
The amount of copper on the inner layers is typically specified in ounces per square foot (oz/ft^2). The most common copper weights are:
- 0.5 oz/ft^2 (17 μm thick)
- 1 oz/ft^2 (34 μm thick) – most common
- 2 oz/ft^2 (70 μm thick)
- 3 oz/ft^2 (105 μm thick)
Heavier copper weights allow for higher current carrying capacity but are more expensive and limit the minimum trace width and spacing.
Dielectric Constant (Dk)
The dielectric constant (Dk) is a measure of a material’s ability to store electrostatic energy. In PCBs, it refers to the insulating substrate material between the copper layers. A lower Dk value means faster signal propagation speed.
Common PCB dielectric materials include:
Material | Dk | Advantages | Disadvantages |
---|---|---|---|
FR-4 | 4.2 | Low cost, good mechanical properties | Higher loss at high frequencies |
Rogers | 2-10 | Low loss, stable Dk over frequency | Expensive |
Polyimide | 3.5 | High heat resistance, good stability | Brittle, moisture absorption |
PTFE | 2.1 | Lowest loss and Dk | Very expensive, poor mechanical properties |
The choice of dielectric material depends on the design requirements and cost constraints. FR-4 is the most common choice for general purpose PCBs up to a few GHz.
Controlled Impedance
For high-speed designs, it’s important to control the characteristic impedance of the transmission lines on the PCB. This is done by adjusting the trace width, dielectric thickness, and Dk value.
Common controlled impedance values are:
- 50 ohms for single-ended traces
- 100 ohms for differential pairs
Achieving controlled impedance requires careful stackup design and precise manufacturing control. The PCB fabricator will need to adjust the dielectric thickness and trace width to meet the specified impedance targets.
Manufacturing Process of PCB Inner Layers
The inner layers of a PCB are fabricated using a multi-step process:
-
Cleaning: The Copper Clad laminate is cleaned to remove any contaminants.
-
Photoresist application: A light-sensitive photoresist is applied to both sides of the laminate.
-
Exposure: The photoresist is exposed to UV light through a photomask, hardening the exposed areas.
-
Developing: The unexposed photoresist is dissolved in a chemical developer, leaving only the hardened areas.
-
Etching: The exposed copper is etched away in a chemical bath, leaving only the desired traces and pads.
-
Stripping: The remaining photoresist is stripped away, leaving the bare copper traces.
-
Inspection: The inner layers are inspected for defects and measured to ensure they meet specifications.
-
Oxide treatment: A black or brown oxide treatment is applied to the copper to improve adhesion to the prepreg.
The finished inner layers are then laminated together with prepreg (pre-impregnated fiberglass) sheets in between each layer. The stack is placed in a hydraulic press at high temperature and pressure to cure the prepreg resin and bond the layers together.
After lamination, holes are drilled through the board and plated with copper to interconnect the layers. The outer layers are then etched using a similar process as the inner layers. Finally, soldermask and silkscreen are applied, and the boards are routed out of the panel.
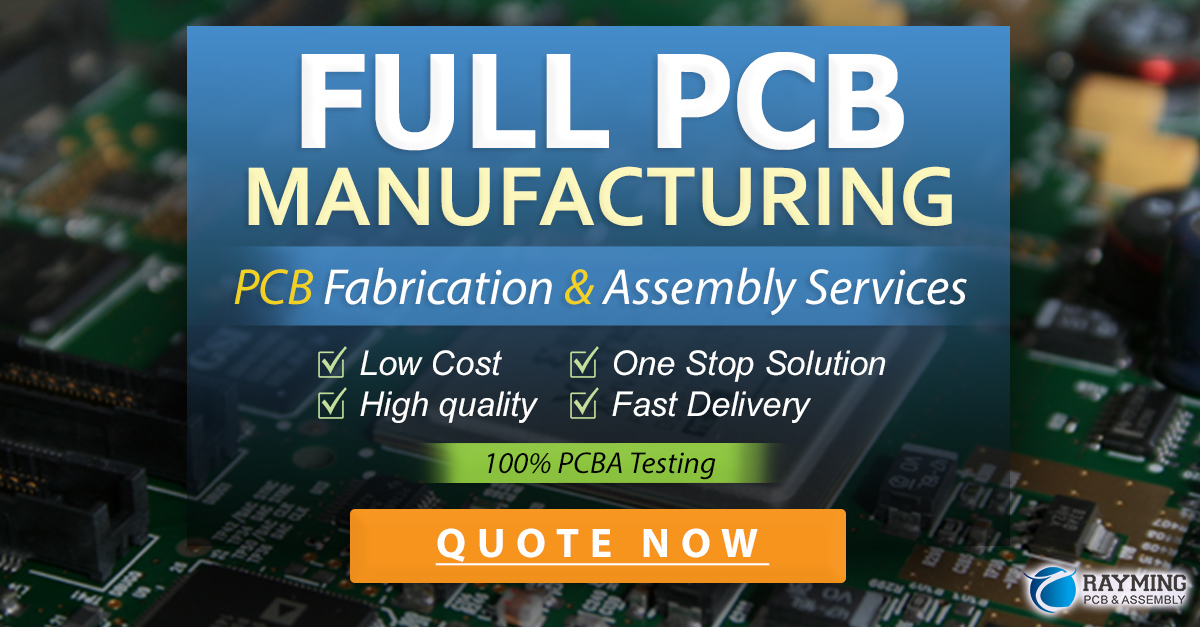
Designing with Inner Layers
Signal Integrity
Proper stackup design is critical for maintaining signal integrity on high-speed PCBs. Here are some best practices:
- Route critical signals on inner layers between power and ground planes for shielding
- Avoid crossing split planes with signals to prevent discontinuities
- Use enough ground vias near connectors to provide a low-impedance return path
- Minimize stubs and unterminated traces that can cause reflections
- Follow length matching and symmetry rules for differential pairs
EMC
Electromagnetic compatibility (EMC) is the ability of a device to operate without causing or being susceptible to electromagnetic interference. Proper use of inner layers can help meet EMC requirements:
- Use solid power and ground planes to provide low-impedance supply and return paths
- Stitch multiple ground planes together with many vias to prevent resonances
- Isolate noisy and sensitive circuits on separate layers
- Provide shielding for critical signals using via fences or copper pours
- Filter signals entering or leaving the board using capacitors, ferrites, or common mode chokes
DFM
Design for manufacturing (DFM) rules ensure that the PCB can be fabricated reliably and cost-effectively. Some key considerations for inner layers:
- Use standard trace width and spacing for the desired copper weight and layer count
- Avoid acute angles and long parallel traces that can cause acid traps during etching
- Provide enough clearance around drilled holes and vias for Annular rings
- Follow the fabricator’s guidelines for minimum hole size, aspect ratio, and plating thickness
- Panelize boards efficiently to maximize material usage and minimize waste
FAQ
What is the purpose of inner layers in a PCB?
Inner layers provide additional routing space and allow for more complex designs. They also provide shielding and reference planes for improved signal integrity and EMC.
How many inner layers are typical in a PCB?
The number of inner layers depends on the complexity of the design. Simple boards may have no inner layers, while complex high-speed designs can have 8 or more. 4-6 layers is common for moderately complex designs.
What is the difference between core and prepreg layers?
Core layers are the rigid fiberglass sheets that make up the bulk of the PCB. Prepreg layers are the partially cured resin sheets used to bond the core layers together during lamination. Prepreg is also used to insulate between copper layers on the same core.
Can you have different copper weights on different layers?
Yes, it’s possible to have different copper weights on different layers, such as 1 oz on the outer layers and 0.5 oz on the inner layers. However, this can add complexity and cost to the manufacturing process. It’s more common to use the same copper weight on all layers.
How do you specify controlled impedance on inner layers?
To specify controlled impedance, you need to provide the PCB fabricator with the desired impedance value, trace width, dielectric thickness, and Dk value. The fabricator will then adjust the dielectric thickness and trace width to meet the impedance target. It’s important to work closely with the fabricator to ensure the stackup is designed correctly for controlled impedance.
Conclusion
The inner layers of a PCB play a critical role in the performance and reliability of the finished board. By understanding the properties, manufacturing process, and design considerations for inner layers, engineers can create stackups that meet the signal integrity, EMC, and manufacturability requirements of their designs.
Proper use of inner layers allows for more complex routing, improved shielding and reference planes, and better control of impedance and crosstalk. However, it also requires careful planning and attention to detail in the design and manufacturing process.
As PCB designs continue to push the boundaries of speed and density, the importance of inner layers will only continue to grow. By staying up to date with the latest materials, processes, and design techniques, engineers can ensure their boards are ready to meet the demands of the future.
Leave a Reply