Understanding CPL and BoM
In the world of manufacturing and supply chain management, two important terms often come up: CPL (Customer Parts List) and BoM (Bill of Materials). While both are essential for managing the production process, they serve different purposes and contain different types of information. In this article, we will delve into the differences between CPL and BoM, their roles in the manufacturing process, and how they work together to ensure efficient production and inventory management.
What is a Customer Parts List (CPL)?
A Customer Parts List, or CPL, is a document that lists all the parts or components that a customer requires for their specific product. It is essentially a list of all the items that the customer wants to be included in their final product. The CPL is usually provided by the customer to the manufacturer and serves as a reference for the production process.
Key features of a CPL:
- Lists all parts required by the customer
- Includes part numbers, descriptions, and quantities
- May include customer-specific requirements or specifications
- Used as a reference for the manufacturer to create the BoM
What is a Bill of Materials (BoM)?
A Bill of Materials, or BoM, is a comprehensive list of all the raw materials, sub-assemblies, intermediate assemblies, sub-components, parts, and the quantities of each needed to manufacture a product. It is a hierarchical document that shows the relationship between a finished product and its components. The BoM is created by the manufacturer based on the CPL provided by the customer and is used to guide the production process.
Key features of a BoM:
- Lists all components and materials required to produce a product
- Includes part numbers, descriptions, quantities, and unit of measure
- Shows the hierarchical relationship between components and assemblies
- Used to plan production, purchase materials, and manage inventory
Differences between CPL and BoM
While CPL and BoM are both important documents in the manufacturing process, they have distinct differences in terms of their purpose, content, and usage.
Aspect | CPL | BoM |
---|---|---|
Purpose | Lists customer requirements | Guides manufacturing process |
Content | Parts required by customer | All components and materials needed for production |
Creation | Provided by customer | Created by manufacturer based on CPL |
Level of Detail | May not include all components | Includes all components and their relationships |
Usage | Reference for manufacturer | Used for production planning, purchasing, and inventory management |
Purpose
The primary purpose of a CPL is to communicate the customer’s requirements to the manufacturer. It serves as a reference for the manufacturer to understand what parts or components the customer needs in their final product. On the other hand, the purpose of a BoM is to guide the manufacturing process. It provides a detailed list of all the components and materials needed to produce the final product, along with their quantities and relationships.
Content
A CPL typically includes only the parts or components that the customer specifically requires. It may not include all the sub-components or raw materials that are needed to produce those parts. In contrast, a BoM is a comprehensive list that includes all the components, sub-assemblies, and raw materials required to manufacture the final product. It provides a complete picture of everything that goes into the production process.
Creation
The CPL is usually provided by the customer to the manufacturer. It is the customer’s responsibility to specify their requirements and provide the necessary information about the parts they need. The manufacturer then uses the CPL as a reference to create the BoM. The BoM is created by the manufacturer based on their understanding of the production process and the components needed to fulfill the customer’s requirements.
Level of Detail
A CPL may not always include all the details about the components or parts. It may only specify the high-level parts that the customer requires without going into the specifics of each sub-component. On the other hand, a BoM is a highly detailed document that includes all the components, sub-assemblies, and raw materials needed for production. It shows the hierarchical relationship between these elements and provides a complete picture of the product structure.
Usage
The CPL is primarily used as a reference by the manufacturer to understand the customer’s requirements. It helps the manufacturer to identify the parts they need to produce or procure to fulfill the customer’s order. The BoM, however, has a wider range of usage in the manufacturing process. It is used for production planning, materials purchasing, inventory management, and cost analysis. The BoM serves as a central document that various departments within the manufacturing organization refer to throughout the production lifecycle.
How CPL and BoM Work Together
While CPL and BoM serve different purposes, they are closely related and work together to ensure smooth and efficient manufacturing processes.
- The customer provides the CPL to the manufacturer, specifying their requirements for the final product.
- The manufacturer reviews the CPL and uses it as a reference to create the BoM.
- The BoM is created by breaking down the customer’s requirements into specific components, sub-assemblies, and raw materials needed for production.
- The manufacturer uses the BoM to plan production, purchase materials, and manage inventory.
- As the product goes through the manufacturing process, the BoM is referred to ensure that all the necessary components are available and assembled correctly.
- Once the final product is manufactured, it is checked against the CPL to ensure that it meets the customer’s requirements.
By working together, the CPL and BoM help to ensure that the manufacturing process is efficient, accurate, and meets the customer’s expectations.
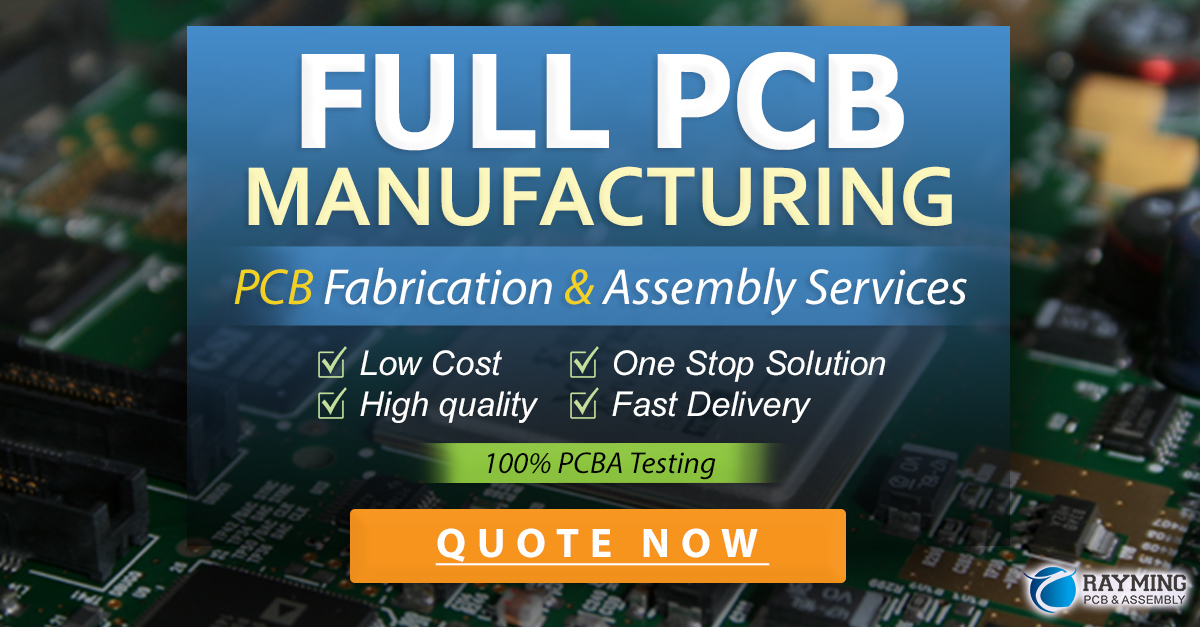
Benefits of Using CPL and BoM
Using CPL and BoM in the manufacturing process offers several benefits for both the customer and the manufacturer.
Benefits for the Customer:
- Ensures that their specific requirements are clearly communicated to the manufacturer
- Helps to avoid misunderstandings or miscommunications about the desired product
- Provides a reference for verifying that the final product meets their expectations
Benefits for the Manufacturer:
- Provides a clear understanding of the customer’s requirements
- Enables efficient production planning and materials procurement
- Helps to reduce waste and minimize inventory holding costs
- Facilitates accurate cost estimation and pricing
- Supports effective communication between different departments involved in the production process
By leveraging the CPL and BoM, manufacturers can streamline their operations, reduce errors, and improve overall productivity.
Challenges and Best Practices
While CPL and BoM are essential tools for manufacturing, there are some challenges and best practices to keep in mind.
Challenges:
- Ensuring accuracy and completeness of the CPL and BoM
- Managing changes and revisions to the CPL and BoM throughout the product lifecycle
- Maintaining consistency between the CPL and BoM
- Integrating CPL and BoM with other systems, such as ERP or PLM software
Best Practices:
- Establish clear communication channels between the customer and manufacturer
- Use standardized templates and formats for CPL and BoM
- Implement version control and change management processes
- Regularly review and update the CPL and BoM to ensure accuracy
- Leverage technology, such as PLM or ERP systems, to manage and integrate CPL and BoM data
By addressing these challenges and following best practices, manufacturers can effectively utilize CPL and BoM to optimize their production processes and deliver high-quality products to their customers.
Frequently Asked Questions (FAQ)
-
Q: Can a CPL and BoM be used interchangeably?
A: No, a CPL and BoM serve different purposes and contain different levels of detail. A CPL lists the customer’s requirements, while a BoM lists all the components and materials needed for production. -
Q: Who is responsible for creating the CPL?
A: The customer is typically responsible for providing the CPL to the manufacturer. The CPL should specify the customer’s requirements for the final product. -
Q: How does a manufacturer create the BoM?
A: The manufacturer creates the BoM based on the CPL provided by the customer. They break down the customer’s requirements into specific components, sub-assemblies, and raw materials needed for production. -
Q: What happens if there are changes to the CPL or BoM during the production process?
A: Changes to the CPL or BoM should be managed through a formal change management process. This ensures that all stakeholders are aware of the changes and that the production process is adjusted accordingly. -
Q: How can technology help in managing CPL and BoM?
A: Technologies such as Product Lifecycle Management (PLM) or Enterprise Resource Planning (ERP) systems can help in managing and integrating CPL and BoM data. These systems provide a centralized platform for storing, updating, and sharing CPL and BoM information across different departments and stakeholders.
Conclusion
In conclusion, CPL and BoM are two critical documents in the manufacturing process that serve different purposes but work together to ensure efficient production and delivery of high-quality products. The CPL represents the customer’s requirements, while the BoM provides a detailed list of all the components and materials needed to produce the final product.
By understanding the differences between CPL and BoM, manufacturers can effectively utilize these tools to streamline their operations, reduce errors, and improve customer satisfaction. Effective communication, standardization, and the use of technology can help overcome challenges and ensure the smooth integration of CPL and BoM in the manufacturing process.
As the manufacturing landscape continues to evolve, the importance of CPL and BoM will only grow. By staying up-to-date with best practices and leveraging these essential tools, manufacturers can remain competitive and deliver products that meet and exceed customer expectations.
Leave a Reply