Introduction to Buildup PCBs
Printed Circuit Boards (PCBs) have revolutionized the electronics industry by providing a reliable and efficient way to connect electronic components. As technology advances, the demand for more complex and high-density PCBs has increased. This is where Buildup PCBs come into play. Buildup PCBs, also known as High-Density Interconnect (HDI) PCBs, are a type of PCB that allows for higher interconnect density and better signal integrity compared to traditional PCBs.
What is a Buildup PCB?
A Buildup PCB is a type of printed circuit board that uses a layered construction technique to achieve higher interconnect density and better signal integrity. Unlike traditional PCBs, which have a single layer of copper traces, Buildup PCBs have multiple layers of copper traces separated by insulating layers. This allows for more connections to be made in a smaller area, making Buildup PCBs ideal for high-density applications.
Advantages of Buildup PCBs
Buildup PCBs offer several advantages over traditional PCBs, including:
- Higher interconnect density: Buildup PCBs allow for more connections to be made in a smaller area, making them ideal for high-density applications.
- Better signal integrity: The layered construction of Buildup PCBs reduces crosstalk and signal interference, resulting in better signal integrity.
- Improved thermal management: Buildup PCBs have better thermal management capabilities due to their layered construction, which allows for better heat dissipation.
- Reduced size and weight: Buildup PCBs can be made smaller and lighter than traditional PCBs, making them ideal for applications where size and weight are critical factors.
The Buildup Process
The Buildup process is a manufacturing technique used to create Buildup PCBs. It involves the sequential layering of conductive and insulating materials to create a multi-layer PCB. The process begins with a core layer, which is typically made of a glass-reinforced epoxy laminate. The core layer is then coated with a layer of copper, which is patterned to create the desired circuit pattern.
Step 1: Core Layer Preparation
The first step in the Buildup process is to prepare the core layer. The core layer is typically made of a glass-reinforced epoxy laminate, which provides a stable base for the subsequent layers. The core layer is drilled and plated to create the necessary vias and through-holes.
Step 2: Copper Deposition
Once the core layer is prepared, a layer of copper is deposited onto the surface using a process called electroless copper plating. This process involves immersing the core layer in a solution containing copper ions, which are then deposited onto the surface of the core layer.
Step 3: Patterning
After the copper layer is deposited, it is patterned to create the desired circuit pattern. This is typically done using a photolithographic process, which involves coating the copper layer with a light-sensitive material called photoresist. The photoresist is then exposed to light through a mask, which hardens the exposed areas. The unexposed areas are then removed using a chemical developer, leaving behind the desired circuit pattern.
Step 4: Insulation Layer Deposition
Once the copper layer is patterned, an insulation layer is deposited onto the surface. This layer is typically made of a polymer material, such as polyimide or epoxy. The insulation layer serves to separate the copper layers and prevent short circuits.
Step 5: Via Formation
After the insulation layer is deposited, vias are formed to connect the different layers of the PCB. Vias are small holes that are drilled through the insulation layer and filled with a conductive material, such as copper. This allows signals to pass between the different layers of the PCB.
Step 6: Repeating the Process
The Buildup process is repeated for each additional layer of the PCB. The number of layers in a Buildup PCB can vary depending on the application, but typically ranges from 4 to 16 layers.
Types of Buildup PCBs
There are several types of Buildup PCBs, each with its own unique characteristics and applications. The most common types of Buildup PCBs are:
1. Any Layer HDI PCBs
Any Layer HDI PCBs are a type of Buildup PCB that allows for the placement of vias on any layer of the PCB. This provides greater flexibility in the design of the PCB and allows for higher interconnect density. Any Layer HDI PCBs are typically used in high-density applications, such as smartphones and wearable devices.
2. Staggered Via HDI PCBs
Staggered Via HDI PCBs are a type of Buildup PCB that uses staggered vias to connect the different layers of the PCB. Staggered vias are offset from each other, which allows for higher interconnect density and better signal integrity. Staggered Via HDI PCBs are typically used in high-speed applications, such as 5G networks and data centers.
3. Buried Via HDI PCBs
Buried Via HDI PCBs are a type of Buildup PCB that uses buried vias to connect the different layers of the PCB. Buried vias are completely enclosed within the PCB and do not extend to the surface. This allows for higher interconnect density and better signal integrity, as well as improved thermal management. Buried Via HDI PCBs are typically used in high-reliability applications, such as aerospace and medical devices.
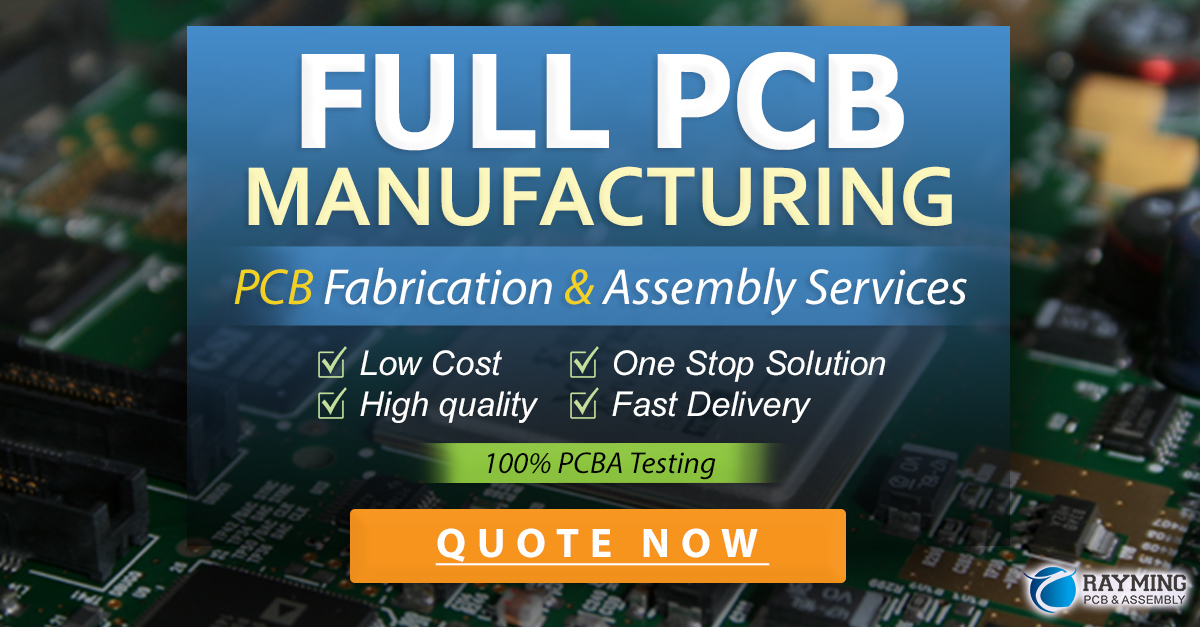
Applications of Buildup PCBs
Buildup PCBs are used in a wide range of applications, from consumer electronics to industrial automation. Some of the most common applications of Buildup PCBs include:
1. Smartphones and Wearable Devices
Buildup PCBs are widely used in smartphones and wearable devices due to their high interconnect density and small form factor. Any Layer HDI PCBs are particularly well-suited for these applications, as they allow for the placement of vias on any layer of the PCB.
2. 5G Networks and Data Centers
Buildup PCBs are also used in 5G networks and data centers due to their high-speed capabilities and better signal integrity. Staggered Via HDI PCBs are particularly well-suited for these applications, as they allow for higher interconnect density and better signal integrity.
3. Aerospace and Defense
Buildup PCBs are used in aerospace and defense applications due to their high reliability and improved thermal management capabilities. Buried Via HDI PCBs are particularly well-suited for these applications, as they allow for higher interconnect density and better signal integrity, as well as improved thermal management.
4. Medical Devices
Buildup PCBs are used in medical devices due to their high reliability and small form factor. Any Layer HDI PCBs are particularly well-suited for these applications, as they allow for the placement of vias on any layer of the PCB.
Challenges and Limitations of Buildup PCBs
While Buildup PCBs offer many advantages over traditional PCBs, they also present some challenges and limitations. Some of the most common challenges and limitations of Buildup PCBs include:
1. Higher Cost
Buildup PCBs are typically more expensive than traditional PCBs due to the additional materials and processing steps required. This can make them cost-prohibitive for some applications.
2. Limited Flexibility
Buildup PCBs are typically less flexible than traditional PCBs due to their layered construction. This can make them more difficult to use in applications where flexibility is required, such as wearable devices.
3. Limited Repairability
Buildup PCBs are typically more difficult to repair than traditional PCBs due to their layered construction. This can make them less suitable for applications where repairability is a critical factor.
Future of Buildup PCBs
Despite the challenges and limitations of Buildup PCBs, they are expected to play an increasingly important role in the electronics industry in the coming years. Some of the key trends and developments in the future of Buildup PCBs include:
1. Increased Adoption in 5G Networks
As 5G networks continue to roll out around the world, the demand for high-speed, high-density PCBs is expected to increase. Buildup PCBs, particularly Staggered Via HDI PCBs, are well-suited for these applications and are expected to see increased adoption in the coming years.
2. Growing Use in Wearable Devices
Wearable devices, such as smartwatches and fitness trackers, are becoming increasingly popular. Buildup PCBs, particularly Any Layer HDI PCBs, are well-suited for these applications due to their small form factor and high interconnect density. As the demand for wearable devices continues to grow, the use of Buildup PCBs in these applications is expected to increase.
3. Advancements in Materials and Processing
As the demand for Buildup PCBs continues to grow, advancements in materials and processing are expected to drive further improvements in performance and cost. For example, the use of advanced materials, such as low-loss dielectrics and high-performance laminates, is expected to improve signal integrity and reduce signal loss. Additionally, advancements in processing techniques, such as laser drilling and plasma etching, are expected to improve the precision and reliability of Buildup PCBs.
Conclusion
Buildup PCBs are a critical technology for the electronics industry, providing a reliable and efficient way to connect electronic components in high-density applications. With their layered construction, Buildup PCBs offer higher interconnect density, better signal integrity, and improved thermal management compared to traditional PCBs.
As technology continues to advance, the demand for Buildup PCBs is expected to grow, particularly in applications such as 5G networks, wearable devices, and aerospace and defense. While Buildup PCBs present some challenges and limitations, advancements in materials and processing are expected to drive further improvements in performance and cost in the coming years.
Frequently Asked Questions (FAQ)
-
What is the difference between Buildup PCBs and traditional PCBs?
Buildup PCBs have multiple layers of copper traces separated by insulating layers, allowing for higher interconnect density and better signal integrity compared to traditional PCBs, which have a single layer of copper traces. -
What are the advantages of Buildup PCBs?
Buildup PCBs offer several advantages, including higher interconnect density, better signal integrity, improved thermal management, and reduced size and weight. -
What are the different types of Buildup PCBs?
The most common types of Buildup PCBs are Any Layer HDI PCBs, Staggered Via HDI PCBs, and Buried Via HDI PCBs. -
What are some common applications of Buildup PCBs?
Buildup PCBs are commonly used in smartphones and wearable devices, 5G networks and data centers, aerospace and defense, and medical devices. -
What are some challenges and limitations of Buildup PCBs?
Buildup PCBs can be more expensive than traditional PCBs, have limited flexibility, and are more difficult to repair due to their layered construction.
Leave a Reply