Purpose and Function of Soldermask
The main functions of soldermask are:
- Solder resist: Prevents solder from adhering to areas of the PCB where it is not intended, thus preventing short circuits.
- Protection: Shields the copper traces from oxidation, corrosion, and other environmental factors that could degrade the performance of the PCB over time.
- Insulation: Acts as an insulating layer between the copper traces and components, improving the overall reliability of the PCB.
- Aesthetics: Provides a uniform and professional appearance to the PCB. Soldermask is available in various colors, with green being the most common.
How Soldermask Works
Soldermask is typically applied to the PCB using a silkscreen printing process. The soldermask material is a photo-imageable polymer that is sensitive to ultraviolet (UV) light. The process involves the following steps:
- The soldermask material is applied to the entire surface of the PCB.
- A photomask, which contains the negative image of the desired soldermask pattern, is placed on top of the PCB.
- The PCB is exposed to UV light, which cures the soldermask material in the areas not covered by the photomask.
- The uncured soldermask is then removed using a developer solution, leaving behind the desired soldermask pattern.
After the soldermask is applied, the PCB undergoes a final curing process to ensure that the soldermask is fully hardened and adhered to the board.
Types of Soldermask
There are two main types of soldermask: liquid photoimageable (LPI) and dry film soldermask (DFSM).
Liquid Photoimageable (LPI) Soldermask
LPI soldermask is the most common type used in PCB manufacturing. It is applied to the PCB as a liquid and then exposed to UV light through a photomask to cure the desired areas. LPI soldermask offers several advantages:
- High resolution and accuracy
- Excellent adhesion to the PCB surface
- Good thermal and chemical resistance
- Available in a wide range of colors
Dry Film Soldermask (DFSM)
DFSM is a solid film that is laminated onto the PCB surface using heat and pressure. It is then exposed to UV light through a photomask and developed to remove the uncured areas. DFSM offers some advantages over LPI soldermask:
- Faster application process
- More uniform thickness
- Better suited for high-volume production
However, DFSM has some limitations compared to LPI soldermask:
- Lower resolution and accuracy
- Limited color options
- Higher cost
Soldermask Colors and Their Significance
Soldermask is available in a variety of colors, with each color serving a specific purpose or indicating a particular characteristic of the PCB. The most common soldermask colors and their significance are:
Color | Significance |
---|---|
Green | Most common color, provides good contrast with copper traces |
Blue | High-end PCBs, often used in military and aerospace applications |
Red | High-Voltage PCBs or warning indicator for critical areas |
Yellow | Used for PCBs in high-temperature environments |
Black | Used for aesthetic purposes or to reduce light reflection |
White | Used for LED lighting applications to reflect light |
The choice of soldermask color depends on the specific application, industry standards, and customer preferences.
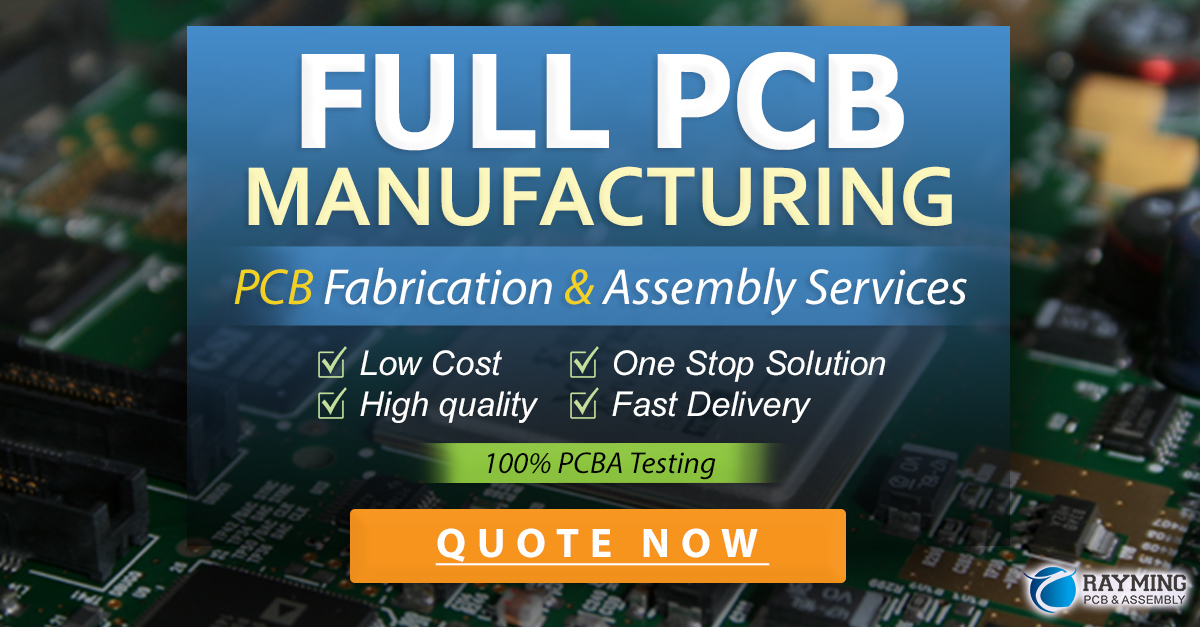
Soldermask Application Process
The soldermask application process involves several steps to ensure a high-quality finish and reliable performance of the PCB. The main steps in the soldermask application process are:
- Surface Preparation: The PCB surface is cleaned to remove any contaminants or debris that could affect the adhesion of the soldermask.
- Soldermask Application: The soldermask material is applied to the PCB surface using either the LPI or DFSM method, as described earlier.
- UV Exposure: The PCB with the applied soldermask is exposed to UV light through a photomask to cure the desired areas of the soldermask.
- Developing: The uncured soldermask is removed using a developer solution, leaving behind the desired soldermask pattern.
- Curing: The PCB undergoes a final curing process to fully harden the soldermask and ensure its adhesion to the board.
- Inspection: The PCB is inspected for any defects or irregularities in the soldermask, such as voids, bubbles, or inconsistent thickness.
Factors Affecting Soldermask Quality
Several factors can impact the quality of the soldermask application, including:
- Surface cleanliness: Any contaminants or residues on the PCB surface can prevent proper adhesion of the soldermask.
- Soldermask material quality: The quality and consistency of the soldermask material can affect its performance and durability.
- UV exposure time and intensity: Insufficient or excessive UV exposure can result in incomplete curing or over-curing of the soldermask.
- Developing process: Improper developing can lead to incomplete removal of uncured soldermask or damage to the cured soldermask.
- Curing temperature and time: Incorrect curing temperature or insufficient curing time can affect the hardness and adhesion of the soldermask.
Proper control and monitoring of these factors are essential to ensure a high-quality soldermask application and reliable PCB performance.
Soldermask Design Considerations
When designing a PCB, several factors must be considered to ensure optimal soldermask performance and manufacturability. These include:
Soldermask Clearance
Soldermask clearance refers to the distance between the edge of the soldermask opening and the edge of the copper pad or trace. Adequate soldermask clearance is necessary to ensure proper solder joint formation and to prevent solder bridging. The minimum soldermask clearance depends on the PCB manufacturing capabilities and the specific design requirements.
Soldermask Sliver
A soldermask sliver is a thin strip of soldermask between two closely spaced copper features. Soldermask slivers can be difficult to manufacture consistently and may lead to soldermask adhesion issues or solder bridging. To avoid soldermask slivers, designers should maintain sufficient spacing between copper features or consider alternative layout options.
Soldermask Registration
Soldermask registration refers to the alignment of the soldermask openings with the underlying copper features. Poor soldermask registration can result in partially covered pads or exposed copper traces, leading to soldering issues or reduced protection. Designers should work closely with the PCB manufacturer to ensure proper soldermask registration and accommodate any necessary adjustments.
Via Tenting
Via tenting is the process of covering drilled holes (vias) with soldermask to prevent solder from flowing into the holes during the assembly process. Tented vias can improve the PCB’s structural integrity and protect against contamination. However, via tenting can also increase the difficulty of soldering and may not be suitable for all applications.
Soldermask Specifications and Standards
Several industry standards and specifications govern the quality and performance of soldermask materials and their application in PCB manufacturing. Some of the key standards include:
- IPC-SM-840E: Qualification and Performance Specification of Permanent Solder Mask
- IPC-4552: Specification for Electroless Nickel/Immersion Gold (ENIG) Plating for Printed Circuit Boards
- MIL-PRF-31032: Performance Specification for Printed Circuit Board Assemblies
- UL 94: Standard for Safety of Flammability of Plastic Materials for Parts in Devices and Appliances
These standards provide guidelines for soldermask material properties, application processes, and testing methods to ensure consistent quality and reliability of PCBs.
Frequently Asked Questions (FAQ)
-
What is the difference between soldermask and silkscreen?
Soldermask is a protective layer applied to the copper traces on a PCB to prevent solder bridging and provide insulation. Silkscreen, on the other hand, is a printed layer on top of the soldermask that contains text, logos, and component outlines for assembly and identification purposes. -
Can soldermask be removed from a PCB?
Yes, soldermask can be removed from a PCB using specialized chemicals or mechanical abrasion. However, removing soldermask can expose the underlying copper traces to oxidation and contamination, compromising the PCB’s performance and reliability. Soldermask removal should only be done when necessary and with proper precautions. -
What is the typical thickness of soldermask?
The typical thickness of soldermask ranges from 0.0005 to 0.003 inches (0.0127 to 0.0762 mm). The actual thickness depends on the specific soldermask material, application method, and PCB design requirements. -
Can soldermask be applied to flexible PCBs?
Yes, soldermask can be applied to flexible PCBs, but the choice of soldermask material and application process may differ from rigid PCBs. Flexible soldermask materials, such as polyimide or acrylic-based soldermask, are specifically designed to withstand the bending and flexing of the PCB without cracking or delaminating. -
How does soldermask affect PCB Assembly?
Soldermask plays a crucial role in PCB assembly by preventing solder from adhering to unintended areas and causing short circuits. Properly applied soldermask ensures that solder only flows onto the exposed pads and creates reliable solder joints. Additionally, soldermask helps to protect the PCB from damage during the assembly process and provides a surface for labeling and identification.
In conclusion, soldermask is an essential component of PCB manufacturing that serves multiple purposes, including solder resist, protection, insulation, and aesthetics. Understanding the types, colors, application process, design considerations, and industry standards related to soldermask is crucial for designing and manufacturing high-quality, reliable PCBs.
Leave a Reply