What is a High-Voltage PCB?
A high-voltage PCB is a specialized type of printed circuit board designed to handle voltages higher than the standard level, typically above 50 volts. These PCBs are used in applications that require the management and distribution of high-voltage signals or power. High-voltage PCBs differ from standard PCBs in terms of their material selection, design rules, and manufacturing processes to ensure proper insulation, creepage, and clearance distances.
Key Considerations for High-Voltage PCB Design
When designing high-voltage PCBs, several critical factors must be taken into account to ensure optimal performance and safety. These factors include:
1. Material Selection
The choice of materials for high-voltage PCBs is crucial to ensure proper insulation and heat dissipation. Some commonly used materials for high-voltage applications include:
- FR-4: A flame-retardant glass-reinforced epoxy laminate with good electrical and mechanical properties.
- Polyimide: A high-temperature resistant material with excellent electrical insulation properties.
- Ceramic: A thermally conductive and electrically insulating material suitable for high-power applications.
The following table compares the properties of these materials:
Material | Dielectric Strength (kV/mm) | Thermal Conductivity (W/mK) | Maximum Operating Temperature (°C) |
---|---|---|---|
FR-4 | 20-30 | 0.3-0.4 | 130-140 |
Polyimide | 60-100 | 0.1-0.2 | 250-300 |
Ceramic | 10-20 | 20-30 | 500-1000 |
2. Creepage and Clearance Distances
Creepage and clearance distances are critical design parameters in high-voltage PCBs. Creepage distance refers to the shortest path between two conductive parts along the surface of the insulating material, while clearance distance is the shortest distance through air between two conductive parts.
The required creepage and clearance distances depend on factors such as the voltage level, pollution degree, and material group. The IPC-2221 standard provides guidelines for determining these distances based on the application requirements.
3. Trace Width and Spacing
The width and spacing of traces on a high-voltage PCB must be carefully designed to prevent electrical arcing and ensure proper current carrying capacity. The trace width should be sufficient to handle the expected current without excessive heating, while the spacing between traces should be adequate to prevent voltage breakdown.
The IPC-2152 standard provides guidelines for determining the minimum trace width and spacing based on the current rating and voltage level.
4. Shielding and Grounding
Effective shielding and grounding techniques are essential in high-voltage PCB design to minimize electromagnetic interference (EMI) and ensure proper operation. Some common shielding and grounding techniques include:
- Ground planes: A continuous copper layer on one or both sides of the PCB that acts as a low-impedance return path for high-frequency signals.
- Faraday cages: A conductive enclosure that surrounds sensitive components to shield them from external electromagnetic fields.
- Grounding vias: Plated through-holes that connect ground planes on different layers of the PCB to provide a low-impedance path for return currents.
5. Component Selection and Placement
The selection and placement of components on a high-voltage PCB should be done carefully to ensure proper functionality and safety. High-voltage components such as capacitors, resistors, and transformers should be rated for the expected voltage and power levels.
The placement of components should also consider the creepage and clearance distances, as well as the thermal management requirements. High-power components should be placed away from sensitive circuits and provided with adequate cooling to prevent overheating.
High-Voltage PCB Manufacturing Process
The manufacturing process for high-voltage PCBs involves several specialized techniques to ensure proper insulation and reliability. Some key steps in the manufacturing process include:
1. Lamination
The lamination process involves bonding the copper layers and insulating materials together under high pressure and temperature. For high-voltage PCBs, special attention is given to the selection of laminate materials and the control of the lamination process parameters to ensure proper bonding and minimize voids or delamination.
2. Drilling and Plating
The drilling process creates holes in the PCB for component mounting and interconnection. For high-voltage PCBs, the drilling process must be precisely controlled to ensure proper hole size and position, as well as to minimize mechanical stress on the board.
After drilling, the holes are plated with copper to provide electrical connectivity between layers. The plating process must be carefully controlled to ensure uniform coverage and avoid any voids or discontinuities that could lead to electrical failures.
3. Solder Mask and Silkscreen
The solder mask is a protective coating applied to the PCB surface to prevent accidental short circuits and protect against environmental factors such as moisture and contaminants. For high-voltage PCBs, the solder mask must have high dielectric strength and good adhesion to the board surface.
The silkscreen is a printed layer that provides component identification and assembly information. The silkscreen ink must be compatible with the high-voltage environment and resistant to fading or peeling over time.
4. Electrical Testing
Thorough electrical testing is essential for high-voltage PCBs to ensure proper functionality and safety. Some common electrical tests include:
- Hipot testing: Applies a high voltage between isolated conductors to test for insulation breakdown.
- Continuity testing: Verifies the electrical continuity of traces and connections.
- Resistance testing: Measures the resistance of traces and components to ensure proper values.
Electrical testing should be performed at various stages of the manufacturing process and on the final assembled board to catch any defects or issues early on.
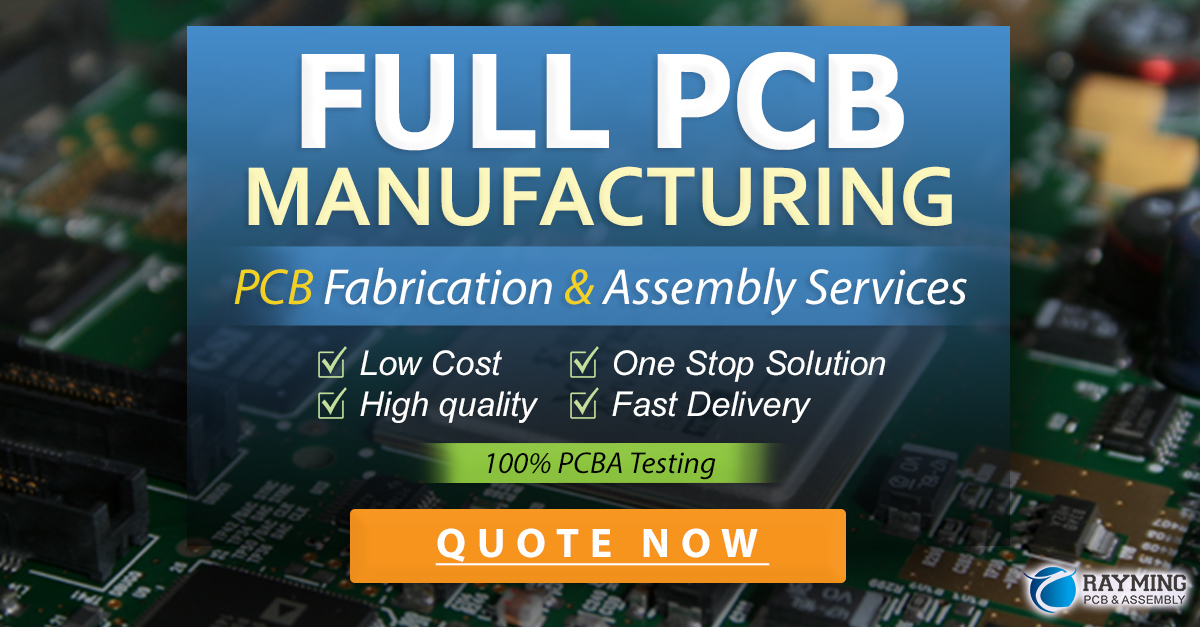
Frequently Asked Questions (FAQ)
1. What is the difference between creepage and clearance distance?
Creepage distance is the shortest path between two conductive parts along the surface of an insulating material, while clearance distance is the shortest distance through air between two conductive parts. Both are important design parameters in high-voltage PCBs to prevent electrical breakdown and ensure proper insulation.
2. How do I determine the required trace width and spacing for my high-voltage PCB?
The required trace width and spacing depend on factors such as the expected current level, voltage rating, and the IPC class of the PCB. The IPC-2152 standard provides guidelines for determining the minimum trace width and spacing based on these factors. It is recommended to consult the standard or work with an experienced PCB design engineer to determine the appropriate values for your specific application.
3. What materials are commonly used for high-voltage PCB substrates?
Common materials used for high-voltage PCB substrates include FR-4, polyimide, and ceramic. FR-4 is a flame-retardant glass-reinforced epoxy laminate with good electrical and mechanical properties. Polyimide is a high-temperature resistant material with excellent electrical insulation properties. Ceramic is a thermally conductive and electrically insulating material suitable for high-power applications.
4. How can I minimize electromagnetic interference (EMI) in my high-voltage PCB design?
To minimize EMI in high-voltage PCB design, you can employ techniques such as:
- Using ground planes to provide a low-impedance return path for high-frequency signals.
- Implementing Faraday cages to shield sensitive components from external electromagnetic fields.
- Placing high-power components away from sensitive circuits and providing adequate shielding.
- Using grounding vias to connect ground planes on different layers of the PCB.
- Following proper layout and routing guidelines to minimize loop areas and crosstalk.
5. What are some common electrical tests performed on high-voltage PCBs?
Common electrical tests performed on high-voltage PCBs include:
- Hipot testing: Applies a high voltage between isolated conductors to test for insulation breakdown.
- Continuity testing: Verifies the electrical continuity of traces and connections.
- Resistance testing: Measures the resistance of traces and components to ensure proper values.
- Dielectric withstanding voltage (DWV) testing: Tests the ability of the insulation to withstand a specified high voltage without breakdown.
- Insulation resistance (IR) testing: Measures the resistance of the insulation between conductors.
These tests are performed at various stages of the manufacturing process and on the final assembled board to ensure proper functionality and safety.
Conclusion
Designing high-voltage PCBs requires careful consideration of various factors, including material selection, creepage and clearance distances, trace width and spacing, shielding and grounding, and component selection and placement. By understanding these key aspects and following industry standards and best practices, you can create high-voltage PCBs that meet your specific requirements and deliver optimal performance and reliability.
When working on high-voltage PCB projects, it is essential to collaborate with experienced design engineers and manufacturing partners who have expertise in this specialized field. They can provide valuable insights and guidance throughout the design and manufacturing process, helping you navigate the complexities and challenges involved in high-voltage PCB technology.
By keeping the information presented in this article in mind and working with skilled professionals, you can confidently design and manufacture high-voltage PCBs that not only meet your technical specifications but also leave you satisfied with the end product. With the right approach and attention to detail, high-voltage PCB technology can be leveraged to create innovative and reliable solutions for a wide range of industries and applications.
Leave a Reply