Introduction to PCB Microsections
PCB microsections are a crucial technique used in the analysis and quality control of printed circuit boards (PCBs). This process involves cutting a small, representative sample of a PCB and examining it under a microscope to assess the quality of the board’s construction, identify potential defects, and ensure compliance with industry standards. By utilizing PCB microsections, manufacturers can improve the reliability and performance of their products, ultimately leading to better customer satisfaction and reduced costs associated with failures and repairs.
The Importance of PCB Microsections
PCB microsections play a vital role in the electronics industry for several reasons:
-
Quality control: Microsections allow manufacturers to identify and address issues in the PCB manufacturing process, ensuring that the final product meets the required specifications and standards.
-
Failure analysis: In the event of a PCB failure, microsections can help determine the root cause of the problem, enabling manufacturers to implement corrective actions and prevent future occurrences.
-
Product improvement: By analyzing PCB microsections, manufacturers can identify areas for improvement in their designs and manufacturing processes, leading to the development of more reliable and efficient products.
-
Compliance: Microsections are used to verify that PCBs comply with industry standards, such as IPC (Association Connecting Electronics Industries) specifications, ensuring the consistency and reliability of the final product.
The PCB Microsectioning Process
The PCB microsectioning process typically involves the following steps:
1. Sample Selection and Preparation
The first step in the microsectioning process is to select a representative sample of the PCB. This sample should be chosen from a critical area of the board, such as a high-stress region or an area with suspected defects. The sample is then carefully removed from the PCB using specialized cutting tools, such as diamond-tipped blades or precision saws, to minimize damage to the sample and ensure a clean, accurate cut.
2. Mounting and Encapsulation
Once the sample has been removed, it is mounted and encapsulated in a clear resin or epoxy material. This process helps to protect the sample during the subsequent grinding and polishing stages and ensures that the sample maintains its integrity for accurate analysis. The encapsulation material is carefully chosen to provide the necessary support and clarity for microscopic examination.
3. Grinding and Polishing
After the sample has been mounted and encapsulated, it undergoes a series of grinding and polishing steps to reveal the internal structure of the PCB. This process typically involves using progressively finer abrasive materials, such as silicon carbide papers and diamond suspensions, to remove material from the sample’s surface gradually. The goal is to create a smooth, flat surface that clearly reveals the PCB’s layers, traces, and components.
4. Etching and Staining
In some cases, additional etching and staining techniques may be used to enhance the contrast and visibility of specific features within the PCB microsection. For example, chemical etchants can be applied to the sample to selectively remove certain materials, such as copper, and reveal the underlying structure. Staining techniques, such as the use of dyes or polarized light, can also be employed to highlight specific features or defects within the sample.
5. Microscopic Examination and Analysis
Once the sample has been prepared, it is examined under a microscope to assess the quality of the PCB’s construction and identify any potential defects or issues. This process typically involves using a high-magnification optical microscope or a scanning electron microscope (SEM) to capture detailed images of the sample’s internal structure. These images are then analyzed by skilled technicians or engineers to evaluate the PCB’s conformance to industry standards and identify any areas of concern.
Common PCB Defects Identified Through Microsections
PCB microsections can reveal a wide range of potential defects and issues that can impact the performance and reliability of the final product. Some of the most common defects identified through microsections include:
1. Voids and Inclusions
Voids and inclusions are small gaps or pockets of air, moisture, or other contaminants that can become trapped within the PCB during the manufacturing process. These defects can weaken the structural integrity of the board, leading to reduced reliability and an increased risk of failure. Microsections can help to identify the presence and location of voids and inclusions, enabling manufacturers to take corrective action and improve their processes.
2. Delamination and Separation
Delamination and separation occur when the layers of the PCB begin to pull apart or separate from one another. This can be caused by a variety of factors, such as poor adhesion between layers, excessive stress, or exposure to harsh environmental conditions. Delamination and separation can lead to reduced electrical performance, increased risk of short circuits, and premature failure of the PCB. Microsections can help to identify the extent and location of delamination and separation, allowing manufacturers to address the issue and improve the overall quality of their products.
3. Plating Defects
Plating defects refer to issues with the conductive copper layers that are deposited onto the PCB during the manufacturing process. These defects can include thin or uneven plating, nodules, and voids, which can impact the electrical performance and reliability of the board. Microsections can reveal the presence and severity of plating defects, enabling manufacturers to optimize their plating processes and ensure the consistency and quality of their products.
4. Trace and Pad Issues
Trace and pad issues refer to defects or irregularities in the conductive pathways and connection points on the PCB. These can include trace width variations, pad lifting, and poor alignment, which can lead to signal integrity issues, increased resistance, and reduced reliability. Microsections can help to identify trace and pad issues, allowing manufacturers to make necessary adjustments to their design and manufacturing processes.
5. Solder Joint Defects
Solder joint defects are issues that can occur during the soldering process, such as insufficient or excessive solder, poor wetting, and voids within the solder joint. These defects can lead to reduced electrical and mechanical performance, as well as an increased risk of failure. Microsections can reveal the presence and nature of solder joint defects, enabling manufacturers to optimize their soldering processes and improve the overall quality of their products.
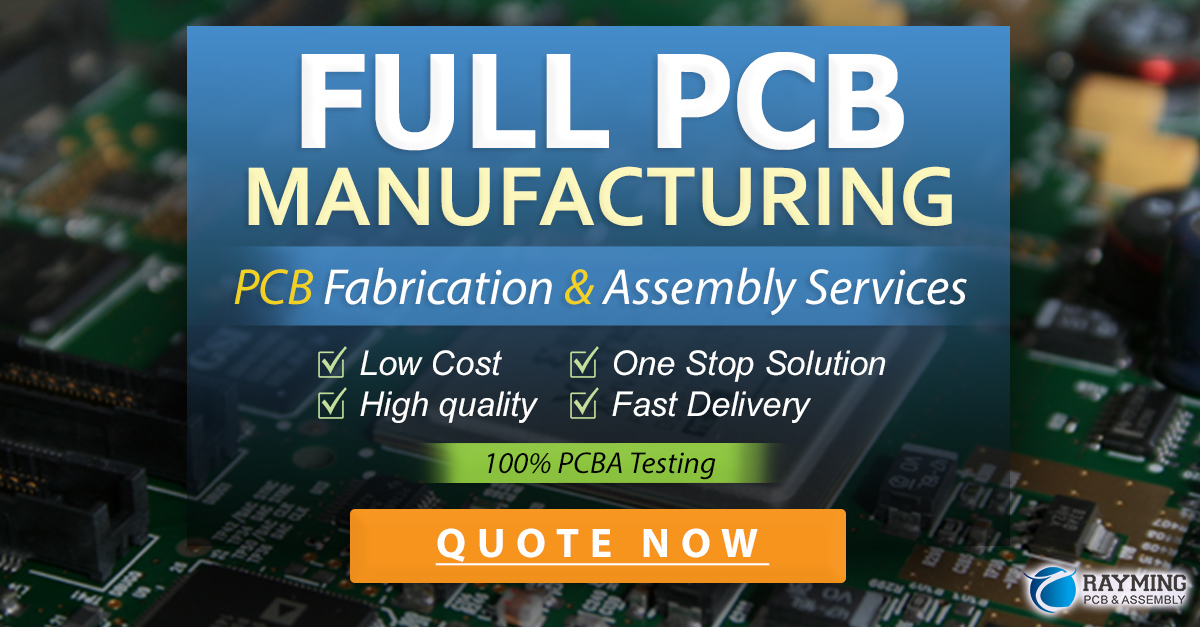
Benefits of PCB Microsections
Implementing PCB microsections as part of a comprehensive quality control and analysis process offers numerous benefits for manufacturers and end-users alike:
1. Improved Reliability
By identifying and addressing potential defects and issues early in the manufacturing process, PCB microsections help to improve the overall reliability of the final product. This leads to fewer field failures, reduced warranty claims, and increased customer satisfaction.
2. Cost Savings
Detecting and correcting issues early in the manufacturing process through PCB microsections can help to minimize the costs associated with scrap, rework, and repairs. By identifying and addressing problems before they escalate, manufacturers can save significant amounts of time and money.
3. Enhanced Quality Control
PCB microsections provide a powerful tool for monitoring and controlling the quality of the manufacturing process. By regularly analyzing microsections, manufacturers can identify trends, make data-driven decisions, and continuously improve their processes to ensure the highest levels of quality and consistency.
4. Faster Time-to-Market
By streamlining the quality control and failure analysis processes, PCB microsections can help manufacturers to bring their products to market faster. This can provide a competitive advantage and enable companies to respond more quickly to changing market demands and customer needs.
5. Compliance with Industry Standards
PCB microsections are an essential tool for ensuring compliance with industry standards and specifications, such as those set by IPC. By regularly analyzing microsections and comparing them to established standards, manufacturers can demonstrate their commitment to quality and reliability, enhancing their reputation and marketability.
FAQs
1. How often should PCB microsections be performed?
The frequency of PCB microsections depends on various factors, such as the complexity of the product, the criticality of the application, and the volume of production. In general, it is recommended to perform microsections at regular intervals throughout the manufacturing process, as well as whenever there are changes to the design, materials, or processes. A typical frequency might be once per shift, per day, or per batch, depending on the specific requirements and risk factors involved.
2. What equipment is needed for PCB microsectioning?
To perform PCB microsections, manufacturers typically need the following equipment:
- Precision cutting tools, such as diamond-tipped blades or saws
- Mounting and encapsulation materials, such as resins or epoxies
- Grinding and polishing equipment, including abrasive papers and diamond suspensions
- Etching and staining solutions and equipment
- High-magnification optical microscopes or scanning electron microscopes (SEMs)
- Image capture and analysis software
3. How long does the PCB microsectioning process take?
The duration of the PCB microsectioning process can vary depending on the complexity of the sample, the number of steps involved, and the level of analysis required. In general, the entire process, from sample selection to final analysis, can take anywhere from a few hours to several days. However, with the use of automated equipment and streamlined processes, many manufacturers are able to complete microsections in a matter of hours, enabling faster turnaround times and more efficient quality control.
4. Can PCB microsections be performed on assembled boards?
Yes, PCB microsections can be performed on fully assembled boards, including those with components and solder joints. In fact, analyzing assembled boards can provide valuable insights into the quality and reliability of the final product, as it allows manufacturers to assess the interaction between the PCB and its components under real-world conditions. However, microsectioning assembled boards can be more challenging and time-consuming than analyzing bare boards, as it requires careful sample preparation and specialized techniques to avoid damaging the components or altering the solder joints.
5. Are there any limitations to PCB microsections?
While PCB microsections are a powerful tool for quality control and failure analysis, there are some limitations to the technique:
- Destructive nature: Microsections require the physical removal and destruction of a portion of the PCB, which can be problematic for high-value or low-volume products.
- Limited sample size: Microsections provide a detailed view of a small, localized area of the PCB, which may not be representative of the entire board or production run.
- Skill and expertise: Performing and analyzing PCB microsections requires specialized knowledge and experience, which can be costly and time-consuming to develop and maintain.
- Interpretation challenges: Analyzing microsection images and data can be subjective and open to interpretation, requiring skilled technicians and engineers to ensure accurate and consistent results.
Despite these limitations, PCB microsections remain an essential tool for ensuring the quality, reliability, and performance of modern electronics products.
Conclusion
PCB microsections are a critical technique for analyzing and optimizing the quality and reliability of printed circuit boards. By providing detailed insights into the internal structure and potential defects of PCBs, microsections enable manufacturers to identify and address issues early in the production process, leading to improved product performance, reduced costs, and enhanced customer satisfaction. As the electronics industry continues to evolve and demand ever-higher levels of quality and reliability, the use of PCB microsections will remain an essential tool for manufacturers seeking to stay ahead of the curve and deliver the best possible products to their customers.
Defect Type | Description | Impact | Detection Method |
---|---|---|---|
Voids and Inclusions | Small gaps or pockets of air, moisture, or contaminants trapped within the PCB | Reduced structural integrity, increased risk of failure | Optical microscopy, SEM |
Delamination and Separation | Layers of the PCB pulling apart or separating from one another | Reduced electrical performance, increased risk of short circuits, premature failure | Optical microscopy, SEM |
Plating Defects | Issues with conductive copper layers, such as thin or uneven plating, nodules, and voids | Impacted electrical performance and reliability | Optical microscopy, SEM |
Trace and Pad Issues | Defects or irregularities in conductive pathways and connection points, such as trace width variations, pad lifting, and poor alignment | Signal integrity issues, increased resistance, reduced reliability | Optical microscopy, SEM |
Solder Joint Defects | Issues during soldering, such as insufficient or excessive solder, poor wetting, and voids within the solder joint | Reduced electrical and mechanical performance, increased risk of failure | Optical microscopy, SEM, X-ray |
Leave a Reply