Introduction
PCB (printed circuit board) fabrication is the process of designing, manufacturing, and assembling printed circuit boards. It involves creating the physical circuit board that will hold and connect various electronic components. The end goal of PCB fabrication is to produce completed circuit boards that are fully functional and ready to be integrated into electronic devices.
In this comprehensive guide, we will explore everything you need to know about PCB fabrication including:
- The PCB fabrication process step-by-step
- Different types of PCBs
- Materials used in PCBs
- PCB design and layout considerations
- Manufacturing and assembly methods
- Quality control and testing
- Cost factors
- Applications of PCBs
Understanding the ins and outs of PCB fabrication will help you produce high-quality boards tailored for your specific project requirements. Let’s get started!
Overview of the PCB Fabrication Process
The main steps involved in creating a fully assembled PCB are:
1. Design and Layout
This involves creating the circuit schematic showing connections between components, and the board layout showing physical placement. PCB design is done using CAD (computer-aided design) software.
2. Prototyping
Initial prototype PCBs are produced to test the design before full production. This helps catch any errors.
3. Pre-production
Pre-production validation testing is done to confirm the design meets requirements before mass production.
4. Production
Multiple circuit boards are mass produced using the validated design files. Automated machinery is used for high volume.
5. Assembly
Electronic components are soldered onto the fabricated boards manually or by pick-and-place machines.
6. Testing and Quality Control
Finished boards undergo electrical, visual, and functional testing to catch any defects. Boards that pass are sent to the customer.
7. Delivery
The completed and tested boards are shipped to the customer for integration into products.
We’ll now look at each of these PCB fabrication stages in greater detail.
PCB Design and Layout
The first step is schematic capture and board layout. This is done with electronic design automation (EDA) or PCB CAD software. Some popular options are Altium, Eagle, OrCAD, and KiCad.
Schematic Capture
This involves creating a circuit schematic showing the logical connections between components. Symbols are used to represent each component. Lines show how they connect. The schematic is like the circuit blueprint. It is used to generate the board layout.
Board Layout
The physical board layout is designed, showing the positioning of components, copper traces, and drill holes. Layout considers factors like signal routing, noise, heat dissipation, manufacturability, and cost.
Here are some key layout considerations:
- Component placement: Position components logically for optimal signal flow and heat dissipation. Follow manufacturability rules.
- Trace routing: Route paths between component pins that maintain signal integrity. Avoid crosstalk. Match trace widths to current.
- Stackup: For multilayer boards, plan internal layer stacking order. Balance signal layers and plane layers.
- Via design: Include plated through hole vias for connections between layers. Minimize via counts where possible.
- Keepouts: Leave sufficient spacing around components to allow soldering and rework access.
- Silkscreen: Add component outlines, labels, assembly markings to help production.
- Dimensions: Size the board according to manufacturing requirements and target enclosure.
- Radii and chamfers: Use rounded pad corners and chamfered edges to aid manufacturability.
Proper board layout is critical for reliable PCB operation. Simulation and analysis can help verify the design prior to fabrication.
PCB Prototyping
Before moving to full production, initial prototype PCBs are fabricated to test out the design. Evaluating prototypes helps catch any errors and make improvements early on.
Prototyping is an iterative process. Multiple revisions are produced to refine the design. Early prototypes may use a simplified fabrication process without all final production details.
Common prototype techniques include:
Breadboarding
Using solderless breadboards for initial circuit construction and testing. Allows quick changes.
Wire-wrap
Soldering components to a wire-wrap board and using wire wrap connections between points. Reversible.
Stripboard
Soldering components on copper stripboards. Similar to perfboard without pre-formed holes.
CNC milling
Using a CNC milling machine to directly mill circuit traces on a PCB blank. Fast and inexpensive.
3D printing
Additively printing conductive traces onto plastic 3D printed boards. Low volume option.
Evaluating PCB prototypes before launching full production helps verify the design, avoids mistakes flowing downline, and ultimately saves time and cost.
PCB Pre-Production
Before mass fabrication, pre-production validation testing is performed. This confirms the design meets all requirements and specs before high volume manufacturing proceeds.
Typical pre-production testing includes:
- Design rule checks: Validate all design rules and manufacturing requirements are met. Check for errors.
- Simulations: Perform thermal, power, and signal integrity simulations to verify performance.
- Test assembly: Build a small test batch with all components assembled, to confirm fit and function.
- Quality testing: Put assemblies through environmental stress testing, lifetime testing, and qualification testing.
Pre-production testing provides the final verification before moving to mass production. It ensures a high yield and prevents problems in fabrication. Crossing this checkpoint means the design is ready for volume PCB manufacturing.
PCB Fabrication Techniques
There are a variety of methods used for volume PCB fabrication and production. The main steps include:
1. Multilayer Lamination
Inner layers are stacked together under heat and pressure to form a multilayer board blank. Layers alternate between copper and insulating dielectric.
2. Through Hole Drilling
Holes are drilled through the entire board to form vias and component lead holes. High precision NC drill machines are used.
3. Copper Plating
The entire board is electroplated with a thin copper layer. Plating coats the drilled holes to form a conductive connection between layers.
4. Photolithography
Photoresist is applied and selectively exposed under a mask. Exposed areas are etched away to form the conductive copper traces.
5. Soldermask Application
A solder resist coating is applied to protect copper traces. Openings in the mask define solderable regions.
6. Silkscreen Printing
Silkscreen labels, markings, and component outlines are printed onto the board for identification.
7. Surface Finishing
Finishing processes like immersion silver or ENIG are applied to protect exposed copper surfaces on pads.
This sequence of steps is followed for mass PCB production. Let’s look at the most common fabrication techniques.
Subtractive Process
Also known as the etching process, this chemically etches away unwanted copper to leave only the desired traces on the laminated base material. A typical sequence is:
- Start with a copper clad laminate base
- Apply photoresist and expose via lithography
- Etch away unmasked copper regions
- Strip off remaining photoresist
Widely used due to lower cost. However, generates more waste compared to additive processes.
Additive Process
Rather than etching away copper, this electroplates copper only where traces are needed. The steps are:
- Start with a bare laminate with no copper
- Apply a thin seed layer of copper
- Apply photoresist and expose via lithography
- Electroplate copper in unmasked areas
- Strip off photoresist
More eco-friendly but higher cost. Provides finer trace resolution.
Semi-Additive Process
Combines aspects of subtractive and additive. A common SAP sequence is:
- Start with thin copper clad laminate
- Apply photoresist and expose via lithography
- Electroplate more copper thickness in unmasked areas
- Etch away all original thin copper cladding
- Strip off photoresist
Improves resolution while using less copper than full additive process.
Maskless Fabrication
Eliminates the use of photoresists. Direct laser or mechanical milling removes copper from a clad laminate according to the digital layout patterns. Simplified process but lower resolution traces.
Multi-Layer Boards
Boards with more than 2 layers involve bonding together individually fabricated double-sided boards under heat and pressure. Layers are interconnected through plated through-hole vias. Allows increased routing density.
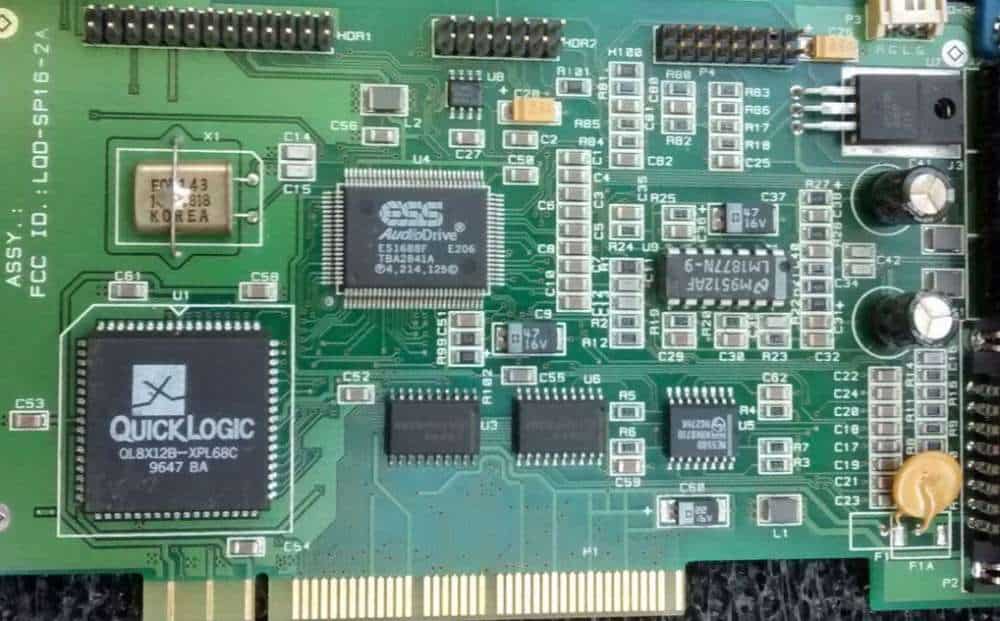
PCB Assembly and Component Soldering
Once the bare boards are fabricated, electronic components must be assembled and soldered on. Some ways to attach components include:
- Through-hole parts: Leaded components are inserted into holes and soldered to pads on the opposite side.
- Surface-mount parts: Parts are placed onto surface pads and reflow soldered in an oven.
- Press-fit parts: Pins press tightly into plated through-holes for friction hold. No soldering needed.
- Connector headers: Long pin headers are soldered in while mating connectors are removable.
There are two main assembly methods:
Manual Assembly
Components are placed and soldered by hand. Lower volumes only. Requires skilled operators.
Automated Assembly
Pick-and-place machines position components precisely onto boards. Reflow ovens melt solder to attach parts. Higher throughput.
For high volume production, automated assembly provides faster speed, accuracy, and repeatability. Hand assembly may be used for quick-turn prototypes. Some boards may use a combination of both techniques.
In-Circuit Test
After assembly, boards should undergo in-circuit testing. This checks for correct component placement, soldering defects, and electrical faults. Issues can be detected and corrected before further integration.
PCB Quality Control and Testing
Verifying the quality of completed PCBs through testing is essential to ensure reliable functioning. Different tests help confirm the design and check for potential defects.
Visual Inspection
Boards are visually examined to check for flaws in the fabrication quality and assembly. Example defects:
- Missing or damaged components
- Incorrect part placement
- Poor soldering joints
- Copper defects, nicks, or scratches
- Solder bridges, shorts
- Foreign object debris (FOD)
- Board damage
Inspection may be manual under a microscope or use automated optical inspection (AOI).
Netlist Testing
Netlist testing compares layout connections against schematic connections to identify mismatch errors. This verifies all nets are properly connected.
In-Circuit Testing
Electrically tests assembled boards for proper connections between components, and identifies faults.
Flying Probe Testing
Tests electrical connectivity and function using movable probes without fixture boards. Checks nets, traces, and detects opens, shorts.
Functional Testing
Applies actual electrical inputs and environments to validate proper functional operation of the board. Confirms it meets all design requirements.
Environmental Stress Testing
Subjects boards to stresses like temperature, vibration, shock, humidity to check operation and reliability under harsh conditions. Accelerated lifetime testing.
Thorough testing at various PCB fabrication stages provides quality control to meet design requirements consistently across production volumes.
Factors Affecting PCB Cost
Several factors determine the fabrication cost of printed circuit boards. These include:
- Board size – Overall dimensions of the PCB. Larger boards cost more.
- Board layers – Additional inner layers increase costs due to lamination. 4-6 layer is typical.
- Board thickness – Standard 1.6mm. Thicker boards are pricier.
- Materials – Base laminate material type affects cost. FR-4 glass epoxy is common.
- Trace density – More tightly spaced fine line traces require additional steps.
- Hole counts – Each drill hole adds cost. Minimizing holes optimizes cost.
- Tolerances – Tighter fabrication and assembly tolerances are pricier.
- Surface finishes – Immersion silver, hard gold, ENIG add cost for anti-tarnishing.
- Solder mask – Additional solder mask colors (black, red, etc) add cost versus standard green.
- Volume – High volume production has lower cost per board versus low volumes.
- Lead time – Faster turnaround times increase costs. Standard is 3-4 weeks.
- Testing – Additional testing like ICT, functional adds cost.
- Certifications – Some industries require UL, IPC certifications that increase cost.
- Location – Local production versus overseas adds cost, but allows better supply chain control.
By optimizing these factors, PCB costs can be managed for a particular application need and budget.
PCB Design and Fabrication Considerations
Here is a summary of key considerations when designing boards destined for fabrication:
- Design for manufacturing (DFM): Follow fabrication and assembly rules to avoid unmanufacturable designs.
- Supplier capabilities: Verify capabilities of the PCB manufacturer early for the feature set needed.
- Standard thicknesses: Use standard 1.6 mm or 0.8 mm board thicknesses when possible. Other values cost more.
- FIN size requirements: Account for any matched impedance trace needs with suitable laminate materials.
- High speed design: Carefully route traces and tune loads for high frequency signals to limit noise. Provide guard traces, ground planes, or spacing between channels.
- Controlled impedances: Match trace widths and adjacent layer dielectric materials to achieve controlled impedance transmission lines, when needed.
- Bypass capacitors: Use sufficient bypass/decoupling capacitors close to ICs to stabilize power.
- Thermal design: Ensure components are properly positioned and board has sufficient thermal vias/ground planes to dissipate heat.
- EMI/EMC considerations: Include grounding structures, filtering, and shielding methods to reduce electromagnetic interference.
- Test points: Allow for test points to facilitate troubleshooting, programming, and quality control testing.
- Component selection: Choose component packages and lead styles suitable for PCB assembly processes. Prefer surface mount over through hole.
- ** tolerances** Tight tolerances increase costs. Allow reasonable fab tolerances.
Early planning considering these design for manufacturing guidelines will facilitate the fabrication process and help prevent potential issues.
Typical Applications of PCBs
Printed circuit boards enable countless electronic devices by providing the supporting base for components and interconnections. Some examples of PCB applications across different industries include:
- Consumer electronics (tablets, smartphones, TVs, gaming systems)
- Computer motherboards, graphics cards, and peripherals
- Automotive electronics (engine control units, infotainment, GPS)
- Industrial control systems (PLCs, HMI panels, sensors)
- Medical devices (patient monitors, analyzers, prosthetics)
- Instrumentation (oscilloscopes, spectrum analyzers, signal generators)
- Communications infrastructure (routers, switches, base stations)
- Military and aerospace avionics
- IoT and wearable tech products
Continued technology advancements allow printed circuit boards to provide the foundation for modern electronic innovation across nearly every product category.
Conclusion
In summary, PCB fabrication is the comprehensive process of taking an electronic circuit design and turning it into a physical, functional board ready for components. This multi-step sequence involves CAD layout, prototyping, volume manufacturing, assembly, and testing. When executed properly, the result is a high quality PCB ready for integration into diverse products and applications.
From material selection to trace routing to quality control, every aspect must be considered to produce a board that matches the design requirements. By understanding the PCB fabrication principles covered here, you???ll be prepared to successfully develop the next generation of electronic hardware.
Frequently Asked Questions
What are the different types of PCBs?
Some common PCB types include:
- Single-sided: Copper traces on one side only
- Double-sided: Copper on both sides
- Multilayer: Multiple copper inner layers laminated together
- Flexible/rigid-flex: Bendable boards using flexible base materials
- HDI: Boards with higher density interconnects
- Metal core: Insulated metal base laminate for thermal dissipation
How accurate are PCB fabrication tolerances?
Typical fabrication tolerances are:
- Line width and spacing: ±10%
- Hole diameter: ±12.5%
- Hole location: ±50 μm
- Board thickness: ±10%
Higher precision tolerances are possible but increase cost.
What surface finishes are used for PCBs?
Common surface finishes include:
- HASL: Hot air solder leveling, for leaded soldering
- ENIG: Electroless nickel immersion gold, for corrosion protection
- Immersion silver: Anti-tarnish silver plating
- Immersion tin: Solderable tin plating
- OSP: Organic surface protectant coating
How are multilayer PCBs fabricated?
Multilayer boards sandwich laminated dielectric core layers together under high pressure and temperature. Copper layers on each core form the signal layers interconnected by plated through holes.
What is HDI technology for PCBs?
HDI or high-density interconnect provides finer trace pitches, smaller vias, tighter tolerances, and higher component density. Enables more compact PCB designs.
Leave a Reply