Printed circuit board (PCB) engineering is the design process of creating the layout of electronic circuits on a printed circuit board (PCB). It involves designing schematics, laying out PCBs, selecting components, testing prototypes, and manufacturing the final PCB design. PCB engineering bridges the gap between circuit design and PCB fabrication.
PCB engineering combines knowledge of electrical engineering, electronics, physics, and manufacturing to take an electronic design from a breadboard prototype to a mass-produced PCB. PCB engineers need to have strong technical knowledge as well as skills in CAD software, simulation, signal integrity, manufacturability, and debugging. The end goal is to create a PCB that faithfully implements the intended circuit design.
The PCB Engineering Process
Schematic Capture
The first step in PCB engineering is schematic capture. This involves drawing a schematic diagram showing all the electronic components and their interconnectivity. Schematics are the basis for PCB layout as they provide the electrical connectivity map.
Schematics are drawn using CAD software like Altium Designer, Cadence Allegro, Mentor Graphics PADS, or KiCad. Common schematic symbols are used to represent components like resistors, capacitors, integrated circuits, connectors, etc. Each component is given a unique reference designator label like R1, R2, C1, U1, J1 etc. Lines between symbols show how components are connected in the circuit.
Component Selection
With the schematic complete, the next step is selecting real-world components to populate the PCB. Component parameters like voltage rating, power rating, package size, and cost are considered. Components must be chosen that closely match the specifications in the schematic.
For integrated circuits, the exact chips need to be chosen. Other components like resistors, capacitors, transistors etc. involve choosing optimal values and packages. Component libraries provide PCB footprints to represent real components. Decisions need to be made on through-hole vs. surface-mount parts.
PCB Layout
PCB layout is the process of arranging components and routing connections on a PCB. It takes the schematic and transforms it into the physical 2D layout that will be fabricated as a PCB. This layout is made in CAD software using the component footprints selected earlier.
The goal is to arrange components in an optimal way and route traces between them. Considerations include signal integrity, electrical noise, heat dissipation, manufacturability, cost, and board space. Engineers strive to route traces efficiently between components following best layout practices.
Multiple PCB layers are used as needed for complex designs. Power and ground planes provide low impedance supply distribution. High-speed signals need impedance controlled traces. Spacing and clearance rules must be followed to prevent shorts. The finished layout goes through design rule checking to verify no errors.
PCB Prototyping
Once the PCB layout and design files are complete, prototypes PCBs are fabricated and assembled. This is an iterative stage of testing PCBs, finding issues, and refining the design. Engineers inspect the PCB for errors, assemble components, and test circuit functionality.
Errors found could be incorrectly chosen components, PCB traces spaced too close, signals interfering, wrong footprints, or other issues. Engineers then rework the design and get new prototypes made until the PCB implementation matches the schematic design. Virtual simulation and analysis during layout also helps reduce prototyping iterations.
PCB Fabrication and Assembly
After prototypes validate the design, the PCB moves to full manufacturing. Fabrication companies produce bare PCBs from the layout files using processes like photolithography or CNC machining. PCB assembly companies then stuff and solder components onto the bare boards using pick-and-place machines and reflow ovens.
Engineers work closely with fabricators and assemblers to smoothly transition designs to production. Volume pricing is negotiated, solder masks and finishes are specified, testing procedures established, and other details coordinated. For large production runs, fabrication and assembly are often handled in separate dedicated facilities.
Bring-Up and Debugging
Once assembled PCBs are received, they undergo bring-up testing. This involves powering up the board, loading firmware, and validating functionality. Engineers debug any issues by checking power, signals, connections, firmware, and components. Diagnostic tests are run to identify defects.
Debugging problems is an essential PCB engineering skill. Troubleshooting techniques like voltage measurements, signal injection, and continuity checking are used to isolate faults. Design or assembly errors may require hardware modifications or file corrections. The goal is getting the manufactured PCBs working correctly.
Documentation
Documentation is vital throughout the PCB engineering process. Schematics, datasheets, layout drawings, assembly instructions, BOMs, prototyping results, and other information is documented. This data serves as a record of the design and how it was developed and can be referenced during debugging or future revisions.
Good documentation enables others to understand the PCB design and provides information needed for manufacturing, assembly, testing, inventory management, servicing, and board upgrades. Keeping thorough, well-organized documentation is a sign of professional and thoughtful PCB engineering.
PCB Design Software
PCB engineering relies heavily on electronic design automation (EDA) software. Different programs are used for schematic capture, PCB layout, component management, simulation and analysis, documentation, and other tasks. Common PCB design software includes:
- Altium Designer – All-in-one EDA tool for schematics, PCB layout, embedded systems, and FPGA design. Provides unified design environment.
- Cadence Allegro – Suite of tools for PCB design with advanced layout features. Used for high-speed, high-complexity boards.
- Mentor Graphics Xpedition – Tools for layout, high-speed design, system modeling, thermal analysis, and design for manufacturability.
- OrCAD – Affordable PCB design solution including schematic capture, layout, and simulation tools.
- KiCad – Free, open source EDA software with schematic capture and PCB layout. Active development community.
- Autodesk Eagle – Low cost PCB design toolset optimized for smaller boards and makers. Limited capability.
- Zuken CR-8000 – PCB layout-centric tool with design for manufacturing and fabrication capabilities.
- Pulsonix – Full-featured, low-cost PCB design software with intuitive UI. Has enterprise deployment options.
- Siemens Saturn PCB – Part of the Siemens digital industry software suite, focused on high-speed design.
Advanced tools for signal and power integrity, thermal analysis, 3D modeling, design rule checking, and simulation help engineers thoroughly validate designs digitally before manufacturing PCBs.
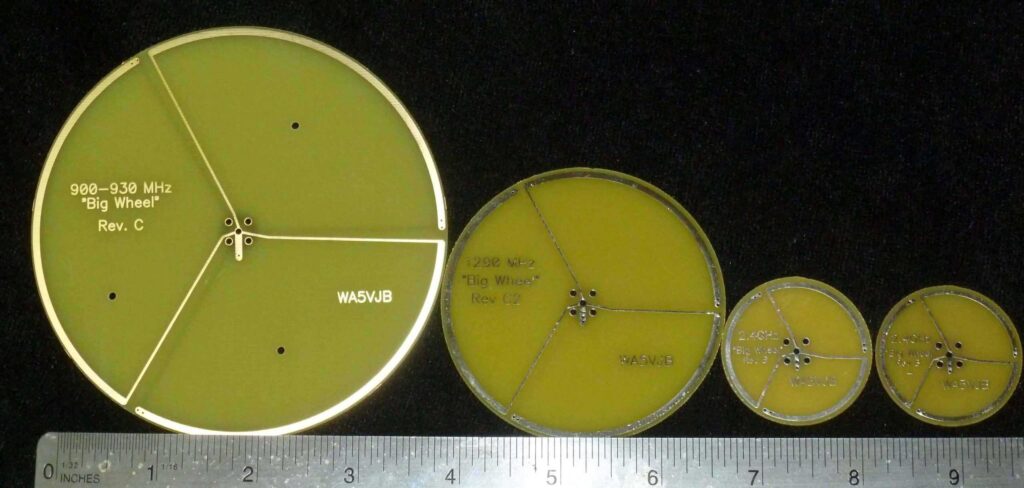
Skills and Knowledge
PCB engineering requires diverse skills and knowledge. Key areas PCB engineers need expertise include:
- Schematic design – Ability to design functional schematics showing electronic components and connectivity
- Circuit simulation – Using SPICE or other tools to simulate circuit operation before prototyping
- PCB layout – Skilled at layout design, routing traces, managing signal layers, and component placement
- EMI and noise – Understanding of electromagnetic interference, capacitive coupling, and mitigation
- Signal integrity – Expertise in controlled impedance traces, terminations, and high-speed signals
- Power integrity – Designing proper power and ground planes for clean, stable supply delivery
- Manufacturing – Knowledge of PCB fab and assembly processes, DFM, tolerances, and limitations
- CAD software – Proficiency with PCB design automation and analysis tools
- Prototyping – Skills in breadboarding, debugging, rework, and validation testing
- Documentation – Discipline to thoroughly document designs, revisions, and learnings
- Teamwork – Ability to work cross-functionally with electrical engineers, technicians, assemblers
- Standards – Familiarity with PCB design standards like IPC-2221 and manufacturing capabilities
PCB engineering draws on a diverse set of engineering disciplines. Success requires both strong technical expertise as well as broad hands-on experience designing, prototyping, and debugging PCBs.
Applications of PCB Engineering
Printed circuit boards are ubiquitous across practically all electronic devices. PCB engineering is involved in products like:
- Consumer electronics – Smartphones, tablets, computers, TVs, home appliances
- Industrial – Programmable logic controllers, test equipment, process control systems
- Automotive – Engine control units, dashboards, infotainment, assisted driving components
- Medical – Imaging systems, patient monitors, analyzers, prosthetics
- Aerospace/defense – Avionics, radar and sensor systems, communications
- IoT devices – Smart home products, wearables, sensors, embedded devices
- Infrastructure – Telecom switches, data centers, utility equipment
From small commodity boards to complex multilayer boards for mission-critical systems, PCB engineering is key to implementing electronic system functionality, reliability and performance. PCBs translate circuit designs into functional real-world products.
Evolution of PCB Engineering
PCB engineering has evolved enormously over the decades:
- 1950s – Manual tape-and-pad layouts with through hole components
- 1960s – Transition to printed circuit boards with planar copper traces
- 1970s – Surface mount components and early CAD tools adopted
- 1980s – Automated assembly and DFM become standard practice
- 1990s – High density boards with surface mount lead to complex multilayer PCBs
- 2000s – Very dense BGAs, HDI, and miniaturization drive advanced PCBs
- 2010s – High-speed signals above 5 Gbps push PCB technology
Each decade has advanced PCB density, precision, reliability and capability. State-of-the-art PCBs now integrate hundreds of components on multilayer boards with high density interconnects. Engineers must master more sophisticated design automation tools to handle rising complexity.
PCB Engineering Education and Training
There are multiple education paths to becoming a PCB engineer:
- Electrical engineering degree – BSEE or CE degree provides foundation in circuits, signals, electronics and design
- On-the-job training – Start as drafter or technician and gain experience under senior engineers
- Trade school – Programs focused specifically on EDA software and PCB design skills
- Certifications – Testing offered by IPC, ETA and GIAC in PCB standards and design tools
- Continuing education – Short courses, seminars and conferences help build capabilities
Engineers generally need an electrical engineering academic background. This is combined with hands-on experience under the mentorship of veteran PCB designers. Continuing education helps hone expertise in specific tools and advanced techniques.
Career Outlook for PCB Engineers
The job outlook for PCB engineers is very strong:
- Increasing electronics – More smart products means more PCBs needing engineered
- Hardware for AI – New AI applications require advanced specialty PCBs
- Next-gen wireless – 5G infrastructure and devices use high frequency PCBs
- Market growth – Electronics manufacturing continues expanding globally
- Aging workforce – Many current PCB engineers nearing retirement age
There is accelerating demand for qualified PCB engineers familiar with doing complex, dense, reliable boards. Automotive, telecom, industrial, and consumer sectors particularly need this expertise. The aging engineering workforce is also driving openings. There are abundant well-paying career opportunities in PCB engineering.
Major PCB Engineering Companies
Some well-known companies that employ large numbers of PCB engineers include:
- Apple – Cutting-edge consumer devices like iPhone and Macbooks
- Samsung – Mobile devices, semiconductors, displays
- General Electric – Appliances, industrial controls and medical equipment
- Huawei – Telecom infrastructure equipment and consumer electronics
- Bosch – Automotive components and industrial technology
- Texas Instruments – Semiconductors and embedded processors
- Cisco – Enterprise and telecom networking hardware
- Lockheed Martin – Defense and aerospace systems
- Intel – Semiconductors and computer processors
- Tesla – Electric vehicles subsystems and autonomy hardware
Both established tech giants and innovative startups need strong PCB engineering talent on their hardware teams. There are abundant global job opportunities at companies leading the electronics industry.
FQA about PCB Engineering
Here are answers to some frequently asked questions about PCB engineering:
Q: What is the typical workflow of PCB engineering?
A: The typical workflow is:
- Create schematic for circuit design
- Select real-world components
- Layout PCB traces and position components
- Fabricate and assemble prototype boards
- Test and debug prototypes
- Repeat process iteratively
- Finalize fabrication and assembly files
- Manufacture full production run
- Test product with PCBs installed for functionality
Q: What are some common problems faced in PCB engineering?
A: Some common issues are:
- Poor signal integrity due to uncontrolled impedance
- Excessive EMI noise coupling between traces
- Power supply noise or unclean ground
- Crosstalk causing signal interference
- Improper component footprints or pinouts
- Traces spaced too close together causing shorts
- Inefficient component placement and routing
- Lack of design for manufacturing considerations
Q: What are the essential skills for a PCB engineer?
A: Key skills include:
- Strong grasp of electrical engineering fundamentals
- Proficiency with EDA design software tools
- Understanding of signal and power integrity
- Knowledge of PCB manufacturing processes
- Ability to read schematics and datasheets
- Attention to detail and organizational skills
- Simulation, prototyping and debugging competence
- Teamwork and communication abilities
Q: How long does it take to design the layout for a complex PCB?
A: For a high density multilayer PCB, layout can take:
- 2-4 weeks for initial placement and routing
- 4-8 weeks for optimization, tweaking, tuned routing
- 6-12 weeks total for final layout signoff
The more complex the board, the longer layout takes. Time is needed for meticulous layout to avoid errors and iterate improvements.
Q: What are good ways to build skills in PCB engineering?
A: Recommended ways to build expertise include:
- Formal electrical engineering university studies
- On-the-job experience under senior PCB designers
- Working through tutorials and documentation for EDA tools
- Online courses focused on specific PCB design subjects
- Attending industry conferences and seminars
- Participating in PCB design challenges and contests
- Contributing to open source PCB projects
- Reading books and articles on latest techniques
- Experimenting with designs using DIY prototyping skills
Leave a Reply