What is an Outer Annular Ring?
An Outer Annular Ring is a circular component that forms the outer part of a bearing assembly. It is typically made from high-quality materials such as steel, stainless steel, or ceramics, depending on the specific application and operating conditions. The OAR is designed to provide a smooth, precise, and wear-resistant surface for the rolling elements (balls or rollers) to rotate against, while also serving as a structural support for the bearing.
Key characteristics of an Outer Annular Ring
-
Geometry: OARs have a circular shape with a precise inner diameter that matches the outer diameter of the rolling elements. The outer diameter of the OAR is designed to fit snugly within the housing or bore of the machine component.
-
Material properties: The material chosen for an OAR must possess high hardness, strength, and wear resistance to withstand the loads and stresses imposed during operation. Common materials include bearing steels (e.g., 52100, 440C), stainless steels (e.g., 316, 440), and ceramics (e.g., silicon nitride, zirconia).
-
Surface finish: The inner surface of the OAR is precision-ground and polished to achieve a smooth, low-friction surface that minimizes wear on the rolling elements and ensures efficient rotation.
Functions of an Outer Annular Ring
The Outer Annular Ring serves several critical functions within a bearing assembly:
-
Load support: The OAR acts as a load-bearing surface, transferring the radial and axial loads from the rotating shaft to the bearing housing. It must be strong enough to withstand these loads without deformation or failure.
-
Guiding rolling elements: The inner surface of the OAR provides a smooth, precise track for the rolling elements to rotate against. This ensures that the rolling elements maintain proper alignment and do not skew or skid during operation, which could lead to increased friction and wear.
-
Sealing and lubrication: In some bearing designs, the OAR may incorporate features such as grooves, holes, or lips that facilitate sealing and lubrication. These features help to retain lubricants within the bearing and prevent contamination from external debris or moisture.
Manufacturing Processes for Outer Annular Rings
The production of Outer Annular Rings involves several key manufacturing processes:
-
Forging or casting: The initial shape of the OAR is typically formed through forging or casting, depending on the material and size of the component. Forging involves shaping the metal through compressive forces, while casting involves pouring molten metal into a mold.
-
Machining: After forging or casting, the OAR undergoes various machining operations to achieve its final dimensions and shape. This may include turning, grinding, and honing to create the precise inner and outer diameters, as well as any features such as grooves or holes.
-
Heat treatment: To achieve the desired material properties, the OAR may undergo heat treatment processes such as quenching and tempering. These processes help to increase the hardness, strength, and wear resistance of the material.
-
Surface finishing: The final step in the manufacturing process is surface finishing, which involves grinding and polishing the inner surface of the OAR to achieve a smooth, low-friction finish. This is critical for ensuring the efficient and reliable operation of the bearing.
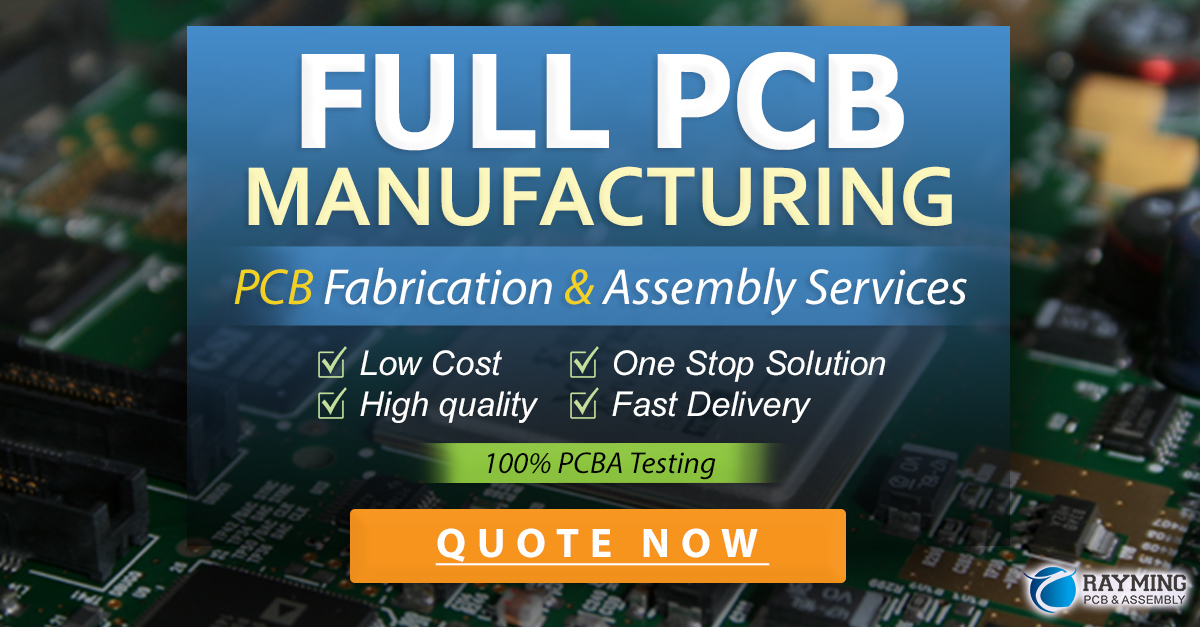
Materials used for Outer Annular Rings
The choice of material for an Outer Annular Ring depends on several factors, including the intended application, operating conditions, and required performance characteristics. Some common materials used for OARs include:
-
Bearing steels: These steels, such as 52100 and 440C, are widely used in bearing applications due to their high hardness, strength, and wear resistance. They are often heat-treated to achieve optimal performance.
-
Stainless steels: Stainless steels, such as 316 and 440, are used in applications where corrosion resistance is a key requirement. They offer good strength and hardness, as well as excellent resistance to oxidation and chemical attack.
-
Ceramics: Ceramic materials, such as silicon nitride and zirconia, are increasingly used in high-performance bearing applications. They offer superior hardness, wear resistance, and thermal stability compared to traditional bearing steels, making them suitable for extreme operating conditions.
Material | Hardness (HRC) | Thermal Expansion Coefficient (10^-6/°C) | Maximum Operating Temperature (°C) |
---|---|---|---|
52100 Steel | 60-64 | 11.9 | 120 |
440C Stainless Steel | 58-60 | 10.2 | 260 |
316 Stainless Steel | 25-39 | 16.0 | 870 |
Silicon Nitride | 75-80 | 3.2 | 1000 |
Zirconia | 75-80 | 10.0 | 2400 |
Applications of Outer Annular Rings
Outer Annular Rings are used in a wide range of bearing applications across various industries:
-
Aerospace: OARs are used in aircraft engines, landing gear, and control systems, where high reliability and performance under extreme conditions are critical.
-
Automotive: In the automotive industry, OARs are found in wheel bearings, transmissions, and steering systems, where they must withstand high loads and speeds.
-
Industrial machinery: OARs are used in a variety of industrial machines, such as pumps, compressors, and turbines, where they support rotational movements and help to reduce friction and wear.
-
Medical devices: In medical applications, OARs are used in devices such as centrifuges, dental drills, and X-ray machines, where precision and reliability are paramount.
-
Wind turbines: OARs play a crucial role in the main shaft and gearbox bearings of wind turbines, supporting the heavy loads and rotational forces generated by the turbine blades.
Frequently Asked Questions (FAQ)
- What is the difference between an Outer Annular Ring and an Inner Annular Ring?
-
An Outer Annular Ring forms the outer part of a bearing assembly and provides a surface for the rolling elements to rotate against, while an Inner Annular Ring is the inner part of the bearing that fits onto the rotating shaft.
-
Can Outer Annular Rings be replaced if they become worn or damaged?
-
In most cases, worn or damaged OARs cannot be replaced individually, as they are typically part of a larger bearing assembly. The entire bearing unit would need to be replaced to ensure proper fit and function.
-
How does the material of an Outer Annular Ring affect its performance?
-
The material of an OAR directly influences its hardness, strength, wear resistance, and thermal properties. Choosing the appropriate material based on the application and operating conditions is crucial for ensuring optimal bearing performance and longevity.
-
What is the importance of surface finish on an Outer Annular Ring?
-
The surface finish of an OAR is critical for reducing friction and wear on the rolling elements. A smooth, polished surface minimizes surface irregularities and ensures efficient rotation, while a rough or uneven surface can lead to increased friction, heat generation, and premature failure.
-
How do Outer Annular Rings contribute to the overall efficiency of a bearing system?
- OARs play a vital role in the efficiency of a bearing system by providing a smooth, precise surface for the rolling elements to rotate against. By minimizing friction and ensuring proper alignment, OARs help to reduce energy losses, extend bearing life, and improve overall system performance.
Conclusion
The Outer Annular Ring is a critical component in bearing assemblies, serving essential functions such as load support, guiding rolling elements, and facilitating sealing and lubrication. The precise geometry, material properties, and surface finish of an OAR directly influence the performance and longevity of the bearing system. By understanding the characteristics, manufacturing processes, and applications of Outer Annular Rings, engineers and designers can select the most suitable components for their specific needs, ensuring optimal system performance and reliability.
As technology advances and new materials emerge, the design and manufacture of Outer Annular Rings will continue to evolve, pushing the boundaries of bearing performance in increasingly demanding applications. From aerospace and automotive to industrial machinery and renewable energy, the humble Outer Annular Ring will remain a crucial element in the smooth operation of countless mechanical systems, playing a vital role in driving innovation and efficiency across a wide range of industries.
Leave a Reply