Introduction
In printed circuit board (PCB) design, you may come across an odd looking cutout pattern called a “mouse bite” along the edges of boards and panels. This is not a random design element but rather an important fabrication feature.
Mouse bites help facilitate the depanelization process which separates individual PCBs from the larger panel. By understanding when and where to use mouse bites, you can optimize your boards for manufacturing.
This article will cover what mouse bites are, why they are used, different mouse bite patterns, and guidelines on incorporating them into your PCB designs. Let’s dive in!
What Are Mouse Bites?
Mouse bites are small semicircular indentations made along the edges of PCB boards and panels. They create a perforated edge that is easy to snap and break.
The term “mouse bite” comes from the characteristic curved shape that resembles a mouse nibbling along the board outline. These curved cutouts are made during fabrication by the same router bits and drills used for other PCB features.
Mouse bites serve as predetermined breaking points or weak spots during depanelization. This is the process of separating individual boards from the larger panel they were fabricated on for ease of manufacturing.
Without mouse bites, depanelization would require manually sawing or routing the entire perimeter of each board. Mouse bites allow the panels to be quickly broken apart by hand or with pliers.
Why Use Mouse Bites?
There are several key reasons mouse bites are widely used in PCB fabrication:
Simpler Depanelization – Mouse bites greatly simplify depanelization compared to sawing or routing. Operators can quickly snap boards out in just seconds.
Reduced Stresses – Breaking at the mouse bites produces less mechanical stress on components compared to sawing. This helps prevent pad lifting or fracturing traces.
Lower Cost – Mouse bites minimize depanelization time and equipment needed. This reduces manufacturing costs.
No Debris – Snapping produces no sawing debris or particles that could contaminate boards compared to sawing or routing.
No Damage – Mouse bites prevent potential damage to sensitive board edges from vibration and heating during sawing.
Precision – The mouse bites can be precisely positioned to avoid interfering with board features. Sawing cannot always cleanly follow intricate board outlines.
Mouse Bite Patterns and Configurations
There are different mouse bite arrangements used depending on factors like board shape, quantity, and separation process. Common patterns include:
Single Row – A single row of mouse bites running along the board perimeter. Used for basic rectangular PCB shapes.
Double Row – Two staggered rows of mouse bites provide extra holding strength while panelized. Critical for thin or dense boards.
Quad Row – Four rows of mouse bites spaced evenly across panelized boards. Reduces stress concentrations during separation.
Castellated – Mouse bites placed at regular intervals along parallel board sides to create a castellated edge. Allows cleaner separation when dense boards tile a panel.
Non-Rectangular – Custom mouse bite designs following traces along non-rectangular board outlines. Provides break points when sawing would be difficult.
Fiducials – Mouse bites canreplace fiducial marks for alignment. This saves space when panelizing small boards.
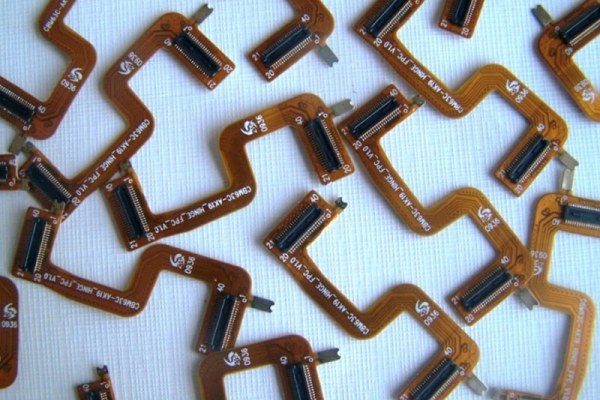
Mouse Bite Design Guidelines
Follow these guidelines when incorporating mouse bites in your PCB designs:
- Place mouse bites at least 0.2” from component pads and traces. Avoid overlapping internal features.
- Include at least 3-5 mouse bites per board edge spaced 0.2” to 0.4” apart. More for longer edges.
- Mouse bite diameter is typically 20 to 30 mils larger than finished slot width.
- Match mouse bite diameter to drill/slot width used for scoring if present.
- Use mouse bite slots on panels between arrayed boards for stress relief during separation.
- Radii for mouse bite semicircles ranges from 15 to 25 mils typically.
- Stagger multiple rows of mouse bites for uniform holding strength while panelized.
- Discuss preferred mouse bite configurations with your board manufacturer early in the design process.
Pros and Cons of Mouse Bites
Mouse bites offer substantial benefits but also have some downsides:
Pros
- Fast, simple, low cost depanelization.
- Reduced mechanical stress on boards during separation.
- Avoids debris, heat, and vibration damage from sawing.
- Allows precision break points not possible with sawing.
Cons
- Requires additional board edge space for mouse bite cutouts.
- Can leave an uneven cosmetic edge profile on consumer boards.
- Exposes additional copper edges susceptible to oxidation and dendrite growth if unprotected.
- Can produce small hairline cracks in glass reinforced laminates.
Alternatives to Mouse Bites
For applications where mouse bites are undesirable, some alternatives for depanelization include:
Scoring/Routing – Partial depth cuts made along board perimeters facilitate separation but produces debris.
Breakaway Tabs – Unpopulated sections hold boards together until manually snapped but take up space.
Perf Board – Boards are fabricated as panels on special perforated substrates that snap apart.
Depanelization Shear – A hydraulic press shears boards apart along hardened tooling rails with no dust or debris.
However, mouse bites remain the most common solution balancing cost, ease of use, and efficiency.
Summary
In summary, mouse bites are a key PCB fabrication feature that enables easy separation of boards from panels while avoiding the downsides of other depanelization methods.
The characteristic curved nibbles along board outlines create perforations that serve as predefined break points during manufacturing. Using proper mouse bite patterns and designs allows you to optimize boards for fabrication.
By understanding when and where to use mouse bites, you can ensure your PCBs can be quickly and safely broken out of panels while minimizing stresses. This allows you to balance production efficiencies without affecting board performance.
Frequently Asked Questions
What are some best practices for positioning mouse bites in a PCB design?
Some best practices include:
- Place mouse bites at least 0.2″ away from any components, pads, or traces.
- Stagger multiple rows of mouse bites for uniform separation forces across the panel.
- Put mouse bites on non-functional board areas whenever possible.
- Align mouse bites vertically on parallel board edges for easier breaking.
- Use mouse bites sized for the depanelization method – punch, router bit, etc.
- Place fiducials adjacent to mouse bites in unused space to serve dual purposes.
- Discuss preferred mouse bite configurations with your PCB manufacturer early in the design process.
When should scoring/routing be used instead of mouse bites?
Scoring may be better for:
- Very dense boards with little edge space for mouse bites.
- Consumer products where cosmetics are important.
- Low volume complex shapes where precision sawing is practical.
- Thick metal-core boards requiring deep perforations.
- High layer count multilayer boards needing reduced separation stresses.
How can mouse bites be designed for irregular board shapes?
For irregular shapes:
- Follow the board outline contours with smaller mouse bites.
- Use mouse bites only where sawing would be impractical.
- Supplement mouse bites with perforated tabs for fragmented edges.
- Rotate mouse bite orientation for angled edges.
- Place mouse bites adjacent to drilled tooling holes used for fixturing during depanelization.
Should mouse bites overlap routed slots in panels?
It’s generally best to avoid overlapping mouse bites with routed slots between boards to prevent cracks from propagating across the panel.
If overlap is unavoidable, the mouse bites should intersect slots at 90 degree angles rather than terminating directly at a slot end. This reduces stress concentration points during separation.
Can solder mask be applied over mouse bite openings?
Solder mask should not be coated over mouse bite openings. This would interfere with the perforations needed for separation.
Mouse bite openings should remain clear through the entire PCB fabrication process. Any solder mask or other coatings blocking them should be cleared by additional routing after application if needed.
What steps can reduce oxidation of exposed copper at mouse bite edges?
To reduce oxidation:
- Apply OSP or immersion silver plating to exposed mouse bite copper edges after depanelization.
- Cover mouse bite openings with resist or tape during unfinished board storage and handling.
- Minimize time between depanelization and conformal coating application.
- Use nickel/gold plating at mouse bite edges for corrosion resistance.
- Avoid designs with mouse bites on exposed high voltage planes if possible.
Leave a Reply