Introduction to PCB Tg
In the world of printed circuit boards (PCBs), one critical parameter that designers and manufacturers must consider is the glass transition temperature, commonly known as Tg. PCB Tg refers to the temperature at which a PCB substrate material transitions from a rigid, glassy state to a more pliable, rubbery state. This transition significantly impacts the PCB’s mechanical and electrical properties, making it a crucial factor in determining the reliability and performance of electronic devices.
What is Glass Transition Temperature (Tg)?
Glass transition temperature (Tg) is a characteristic property of amorphous and semi-crystalline materials, including polymers used in PCB substrates. At temperatures below Tg, the polymer molecules have limited mobility, resulting in a rigid and brittle material. However, as the temperature increases and surpasses Tg, the polymer molecules gain sufficient energy to move more freely, leading to a softer and more flexible state.
Importance of PCB Tg
Understanding and considering PCB Tg is essential for several reasons:
-
Reliability: PCBs exposed to temperatures above their Tg may experience deformation, warping, or layering issues, compromising the board’s structural integrity and reliability.
-
Electrical Performance: As PCBs approach or exceed their Tg, the dielectric constant and loss tangent of the substrate material can change, affecting the board’s electrical performance and signal integrity.
-
Application Suitability: The choice of PCB substrate material and its corresponding Tg must align with the operating temperature range and environmental conditions of the intended application.
Common PCB Substrate Materials and Their Tg Values
Several materials are commonly used for PCB substrates, each with its own set of properties and Tg values. Some of the most popular options include:
FR-4
FR-4 is the most widely used PCB substrate material, consisting of a woven fiberglass cloth impregnated with an epoxy resin. It offers a good balance of mechanical, electrical, and thermal properties at a relatively low cost. The standard Tg for FR-4 is 130°C, although high-Tg variants (170°C) are available for more demanding applications.
Grade | Tg (°C) | Applications |
---|---|---|
Standard FR-4 | 130 | General-purpose electronics |
High Tg FR-4 | 170 | Automotive, aerospace, military |
Polyimide
Polyimide is a high-performance polymer known for its excellent thermal stability, chemical resistance, and mechanical strength. PCBs made with polyimide substrates can withstand higher temperatures and harsher environments compared to FR-4. The Tg of polyimide is typically around 250°C, making it suitable for applications that require continuous operation at elevated temperatures.
Material | Tg (°C) | Applications |
---|---|---|
Kapton | 360-410 | Aerospace, defense, high-temperature electronics |
Upilex | 290 | Flexible PCBs, high-frequency applications |
High-Frequency Laminates
For high-frequency and high-speed applications, specialized substrate materials with low dielectric constant and loss tangent are used to minimize signal loss and distortion. These materials often have higher Tg values to maintain their electrical properties over a wide temperature range. Examples include Rogers RO4000 series (Tg: 280°C) and Isola I-Tera MT40 (Tg: 200°C).
Material | Tg (°C) | Dielectric Constant | Applications |
---|---|---|---|
Rogers RO4350B | 280 | 3.48 @ 10 GHz | Automotive radar, aerospace, defense |
Isola I-Tera MT40 | 200 | 3.38 @ 10 GHz | 5G, automotive, high-speed digital |
Factors Affecting PCB Tg
Several factors can influence the glass transition temperature of a PCB substrate material:
Resin Chemistry
The chemical composition of the polymer resin used in the substrate material plays a significant role in determining its Tg. Different resin systems, such as epoxy, polyimide, or cyanate ester, have varying molecular structures and crosslink densities, resulting in different Tg values.
Filler Content
PCB substrate materials often incorporate fillers, such as woven fiberglass or ceramic particles, to enhance their mechanical and thermal properties. The type, size, and distribution of these fillers can impact the overall Tg of the composite material.
Manufacturing Process
The manufacturing process, including the curing temperature and duration, can affect the degree of crosslinking in the polymer resin, influencing its Tg. Higher curing temperatures and longer curing times generally lead to a higher crosslink density and, consequently, a higher Tg.
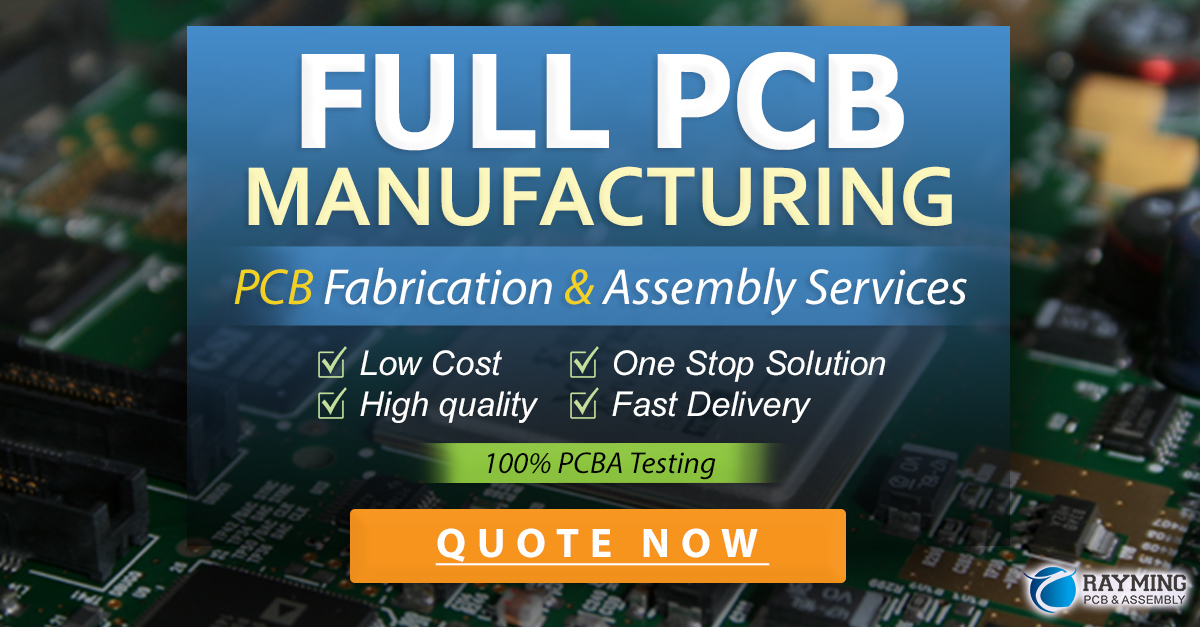
Tg Measurement Techniques
Several techniques are used to measure the glass transition temperature of PCB substrate materials:
Differential Scanning Calorimetry (DSC)
DSC is a thermal analysis technique that measures the heat flow into or out of a sample as a function of temperature. It can detect the glass transition by monitoring changes in the sample’s heat capacity. DSC is widely used for Tg measurement due to its accuracy and ease of sample preparation.
Dynamic Mechanical Analysis (DMA)
DMA measures the mechanical properties of a material, such as storage modulus and loss modulus, as a function of temperature. The glass transition is indicated by a sharp drop in the storage modulus and a peak in the loss modulus. DMA provides additional information about the material’s viscoelastic behavior compared to DSC.
Thermomechanical Analysis (TMA)
TMA measures the dimensional changes of a sample as a function of temperature. The glass transition is associated with a change in the coefficient of thermal expansion (CTE) of the material. TMA is useful for evaluating the thermal stability and CTE mismatch of PCB substrate materials.
Designing with PCB Tg in Mind
When designing PCBs, it is crucial to consider the glass transition temperature of the substrate material and ensure that it is suitable for the intended application and operating environment. Some key aspects to keep in mind include:
-
Operating Temperature Range: Choose a substrate material with a Tg well above the maximum expected operating temperature to maintain the PCB’s structural integrity and reliability.
-
Environmental Conditions: Consider the environmental factors the PCB will be exposed to, such as humidity, chemicals, or mechanical stress, and select a substrate material with appropriate resistance and stability.
-
Thermal Management: Evaluate the heat generation and dissipation requirements of the PCB and choose a substrate material with suitable thermal conductivity and CTE to minimize thermal stresses and warpage.
-
High-Frequency Performance: For high-frequency applications, select substrate materials with low dielectric constant and loss tangent, and consider the impact of temperature on these properties.
-
Cost and Availability: Balance the performance requirements with the cost and availability of the substrate material, considering the volume and production timeline of the project.
FAQ
1. What is the difference between Tg and Td for PCB substrate materials?
Tg (glass transition temperature) refers to the temperature at which a material transitions from a rigid, glassy state to a more pliable, rubbery state. Td (decomposition temperature) is the temperature at which a material begins to break down and lose its structural integrity. Tg is more relevant for the operational temperature range of a PCB, while Td determines the upper limit for processing and manufacturing.
2. Can PCBs be used above their Tg?
While PCBs can be exposed to temperatures above their Tg for short periods, prolonged exposure can lead to deformation, warping, and layering issues. It is generally recommended to choose a substrate material with a Tg well above the maximum expected operating temperature to ensure the PCB’s reliability and performance.
3. How does PCB Tg affect the assembly process?
The assembly process, including soldering and reflow, subjects PCBs to elevated temperatures. It is essential to choose a substrate material with a Tg higher than the maximum temperature encountered during assembly to prevent deformation or damage to the board.
4. Can high-Tg PCB materials be combined with standard FR-4?
Yes, high-Tg materials can be used in combination with standard FR-4 in a multi-layer PCB Stack-up. This approach allows for the strategic placement of high-performance materials in critical layers while using cost-effective FR-4 for less demanding layers.
5. How does the choice of PCB Tg impact the overall cost of the PCB?
Higher Tg materials, such as polyimide or high-frequency laminates, are generally more expensive than standard FR-4. The choice of PCB Tg should be based on a careful consideration of the performance requirements and the overall project budget. In some cases, the added cost of a high-Tg material may be justified by the improved reliability and performance of the end product.
Conclusion
PCB Tg, or the glass transition temperature of printed circuit board substrate materials, is a critical parameter that influences the reliability, performance, and suitability of PCBs for various applications. Understanding the concept of Tg, common substrate materials and their Tg values, factors affecting Tg, and measurement techniques is essential for designing and manufacturing high-quality PCBs.
When selecting a PCB substrate material, designers must consider the operating temperature range, environmental conditions, thermal management, high-frequency performance, and cost. By choosing a substrate material with an appropriate Tg and other properties, designers can ensure the optimal performance and longevity of their electronic devices.
As technology advances and new applications emerge, the development of PCB substrate materials with improved thermal stability, electrical properties, and processing characteristics will continue to be a focus for the electronics industry. Staying informed about the latest advancements in PCB materials and their glass transition temperatures will help designers and manufacturers stay ahead of the curve in delivering cutting-edge, reliable electronic products.
Leave a Reply