Introduction to High-TG PCB
High-Tg PCB, or high glass transition temperature printed circuit board, is a type of PCB material that can withstand higher temperatures compared to standard FR-4 PCBs. The glass transition temperature (Tg) refers to the temperature at which the PCB material transitions from a rigid, glassy state to a more flexible, rubbery state. High-Tg PCBs typically have a Tg value of 170°C or higher, while standard FR-4 PCBs have a Tg around 130-140°C.
The higher temperature resistance of High-Tg PCBs makes them suitable for applications that involve exposure to elevated temperatures, such as:
- Automotive electronics
- Aerospace systems
- Industrial control systems
- Power electronics
- LED lighting
Advantages of High-Tg PCBs
High-Tg PCBs offer several advantages over standard FR-4 PCBs:
-
Improved thermal stability: The higher glass transition temperature allows High-Tg PCBs to maintain their mechanical and electrical properties at elevated temperatures, reducing the risk of warping, delamination, or other temperature-related failures.
-
Reduced thermal expansion: High-Tg PCBs have a lower coefficient of thermal expansion (CTE), which means they expand and contract less when subjected to temperature changes. This reduces stress on the PCB and its components, improving reliability and longevity.
-
Better signal integrity: The higher Tg value and lower CTE of High-Tg PCBs contribute to better signal integrity, especially at high frequencies. This is because the PCB material is less likely to deform or change its dielectric properties under thermal stress, maintaining consistent impedance and reducing signal distortion.
-
Increased durability: The improved thermal stability and reduced thermal expansion of High-Tg PCBs make them more durable and resistant to thermal cycling, vibration, and other mechanical stresses.
Disadvantages of High-Tg PCBs
Despite their benefits, High-Tg PCBs also have some drawbacks:
-
Higher cost: The specialized materials and manufacturing processes required for High-Tg PCBs make them more expensive than standard FR-4 PCBs. This can impact the overall cost of the end product.
-
Limited availability: Not all PCB manufacturers offer High-Tg PCBs, as they require specific expertise and equipment. This can lead to longer lead times and reduced sourcing options.
-
Increased weight: High-Tg PCBs are often made with heavier, more dense materials to achieve their thermal properties. This can result in a slightly higher overall weight compared to standard FR-4 PCBs.
High-Tg PCB Materials
Several materials are used to manufacture High-Tg PCBs, each with its own set of properties and advantages. Some common High-Tg PCB materials include:
FR-4 High Tg
FR-4 High Tg is an enhanced version of the standard FR-4 material, with a higher glass transition temperature. It is made by modifying the epoxy resin system used in the laminate. FR-4 High Tg typically has a Tg value of 170-180°C and offers a cost-effective option for applications that require improved thermal performance over standard FR-4.
Polyimide
Polyimide is a high-performance polymer known for its excellent thermal stability, chemical resistance, and mechanical strength. Polyimide-based PCBs can have a Tg value of 250°C or higher, making them suitable for the most demanding high-temperature applications. However, polyimide is more expensive and harder to process than other High-Tg materials.
High Tg Multifunctional Epoxy
High Tg multifunctional epoxy is a type of epoxy resin system that combines the benefits of high thermal stability with improved mechanical properties and chemical resistance. PCBs made with this material typically have a Tg value of 180-200°C and offer a balance of performance and cost for many high-temperature applications.
Comparison of High-Tg PCB Materials
Material | Tg (°C) | Advantages | Disadvantages |
---|---|---|---|
FR-4 High Tg | 170-180 | Cost-effective, easy to process, good thermal performance | Limited high-temperature range |
Polyimide | 250+ | Excellent thermal stability, chemical resistance, strength | Expensive, difficult to process |
High Tg Multifunctional Epoxy | 180-200 | Good balance of thermal, mechanical, and chemical properties | Higher cost than FR-4 High Tg |
High-Tg PCB Manufacturing Process
The manufacturing process for High-Tg PCBs is similar to that of standard FR-4 PCBs, with some additional considerations to account for the unique properties of the High-Tg materials.
Material Selection and Preparation
The first step in manufacturing High-Tg PCBs is selecting the appropriate material based on the application requirements, such as the expected operating temperature range, mechanical stresses, and chemical exposure. The chosen material is then prepared for the lamination process by cutting it to the desired size and shape.
Lamination
During lamination, the prepared High-Tg material is combined with copper foil and other layers, such as prepreg and core materials, to form the PCB stackup. The stackup is then subjected to high temperature and pressure in a lamination press, causing the layers to bond together and form a solid, cohesive board.
Drilling and Plating
After lamination, the PCB is drilled to create holes for vias and component leads. The holes are then plated with copper to establish electrical connections between layers. High-Tg materials may require specialized drilling and plating processes to ensure proper hole quality and copper adhesion.
Patterning and Etching
The copper layers of the PCB are patterned using photolithography and then etched to remove the unwanted copper, leaving only the desired circuit traces. High-Tg materials may require adjustments to the photolithography and etching processes to account for their different chemical and mechanical properties compared to standard FR-4.
Solder Mask and Silkscreen
A solder mask is applied to the PCB to protect the copper traces from oxidation and prevent solder bridges during assembly. A silkscreen layer is then added to provide component labels and other markings. High-Tg materials may require specialized solder mask and silkscreen inks to ensure proper adhesion and durability at elevated temperatures.
Surface Finish
Finally, a surface finish is applied to the exposed copper areas of the PCB to protect them from oxidation and enhance solderability. Common surface finishes for High-Tg PCBs include:
- ENIG (Electroless Nickel Immersion Gold)
- ENEPIG (Electroless Nickel Electroless Palladium Immersion Gold)
- OSP (Organic Solderability Preservative)
- Immersion Silver
The choice of surface finish depends on the specific application requirements, such as the expected operating temperature, shelf life, and compatibility with the chosen solder alloy.
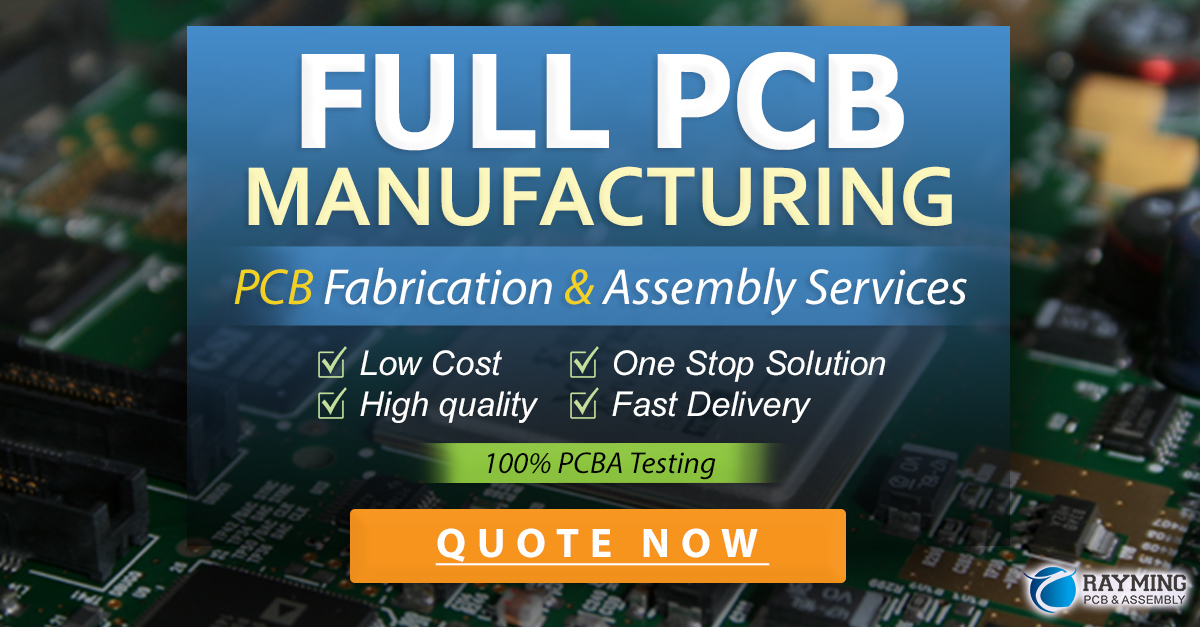
High-Tg PCB Design Considerations
Designing High-Tg PCBs involves several considerations to ensure optimal performance and reliability in high-temperature environments.
Thermal Management
Proper thermal management is crucial for High-Tg PCBs to prevent overheating and ensure reliable operation. This can be achieved through several techniques:
-
Thermal vias: Adding thermal vias to the PCB design helps to conduct heat away from hot components and spread it more evenly across the board. Thermal vias can be placed under or near high-power components, such as processors, FPGAs, or power regulators.
-
Copper pours: Using large copper pours on the PCB Layers helps to distribute heat more effectively and provides a low-impedance path for heat to flow to the board edges or other heat-dissipating structures.
-
Component placement: Strategic component placement can minimize heat buildup and improve thermal performance. High-power components should be placed away from each other and near the board edges to facilitate heat dissipation. Components with similar thermal profiles should be grouped together to minimize local hot spots.
Signal Integrity
Maintaining good signal integrity is essential for High-Tg PCBs, especially at high frequencies. Some key considerations for signal integrity include:
-
Impedance control: Ensuring consistent impedance throughout the signal paths helps to minimize reflections and signal distortion. This can be achieved by carefully designing the trace widths, spacings, and layer stackup to match the desired characteristic impedance.
-
Crosstalk reduction: Minimizing crosstalk between adjacent signal traces is important to prevent signal interference and maintain data integrity. This can be done by providing adequate spacing between traces, using guard traces or ground planes, and employing differential signaling techniques.
-
Length matching: Matching the lengths of related signal traces, such as those in a bus or differential pair, helps to ensure that signals arrive at their destinations simultaneously, reducing skew and improving timing margins.
Mechanical Stress Management
High-Tg PCBs must be designed to withstand the mechanical stresses associated with high-temperature environments, such as thermal expansion and contraction. Some strategies for managing mechanical stress include:
-
Flexible interconnects: Using flexible interconnects, such as ribbon cables or flex circuits, can help to decouple the PCB from mechanical stresses caused by thermal expansion mismatches between the board and its enclosure or other components.
-
Strain relief: Incorporating strain relief features, such as slots or cutouts, near connectors or other mechanical interfaces can help to distribute stress and prevent cracking or delamination of the PCB.
-
Component selection: Choosing components with compatible thermal expansion characteristics and using underfill or other reinforcing materials can help to minimize stress on solder joints and improve reliability.
High-Tg PCB Testing and Qualification
To ensure that High-Tg PCBs meet the required performance and reliability standards, they must undergo thorough testing and qualification processes. Some common tests for High-Tg PCBs include:
Thermal Cycling
Thermal cycling tests expose the PCB to repeated cycles of high and low temperatures to simulate the expected operating conditions and verify that the board can withstand thermal stress without failure. The number of cycles, temperature range, and dwell times are determined based on the specific application requirements.
Thermal Shock
Thermal shock tests subject the PCB to rapid changes in temperature, typically by moving it quickly between hot and cold chambers. This test verifies the PCB’s ability to withstand sudden temperature changes without cracking, delamination, or other failures.
Interconnect Stress Test (IST)
The Interconnect Stress Test (IST) evaluates the reliability of the PCB’s interconnects, such as vias and plated through-holes, under thermal stress. The test involves applying a high current to specific interconnects while subjecting the board to elevated temperatures, then measuring the resistance change to detect any failures.
Time-Domain Reflectometry (TDR)
Time-Domain Reflectometry (TDR) is a technique used to characterize the impedance of the PCB’s signal paths and detect any discontinuities or defects. TDR measurements are performed before and after thermal stress testing to verify that the PCB’s electrical properties remain stable.
Microsectioning
Microsectioning involves cross-sectioning the PCB and examining the internal structure using microscopy to detect any manufacturing defects, such as voids, delamination, or poor copper plating. This destructive test is typically performed on a sample of boards from each manufacturing lot to ensure consistent quality.
FAQ
What is the difference between High-Tg PCB and standard FR-4 PCB?
The main difference between High-Tg PCB and standard FR-4 PCB is the glass transition temperature (Tg). High-Tg PCBs have a Tg value of 170°C or higher, while standard FR-4 PCBs have a Tg around 130-140°C. This higher Tg value allows High-Tg PCBs to maintain their mechanical and electrical properties at elevated temperatures, making them suitable for high-temperature applications.
Can High-Tg PCBs be used in all applications?
While High-Tg PCBs offer superior thermal performance and reliability compared to standard FR-4 PCBs, they may not be necessary or cost-effective for all applications. High-Tg PCBs are typically used in applications that involve exposure to elevated temperatures, such as automotive electronics, aerospace systems, industrial control systems, power electronics, and LED lighting. For applications with lower temperature requirements, standard FR-4 PCBs may be sufficient.
Are High-Tg PCBs more expensive than standard FR-4 PCBs?
Yes, High-Tg PCBs are generally more expensive than standard FR-4 PCBs due to the specialized materials and manufacturing processes required. The higher cost of High-Tg PCBs can impact the overall cost of the end product, so it is important to carefully consider the specific application requirements and balance performance with cost.
What is the typical lead time for High-Tg PCBs?
The lead time for High-Tg PCBs can vary depending on the specific material, complexity of the design, and the manufacturer’s capacity. In general, High-Tg PCBs may have slightly longer lead times compared to standard FR-4 PCBs, as fewer manufacturers offer High-Tg PCB services and the specialized materials may not be as readily available. It is important to plan accordingly and communicate with the PCB manufacturer to ensure timely delivery of the boards.
Can High-Tg PCBs be reworked or repaired?
Reworking or repairing High-Tg PCBs can be more challenging compared to standard FR-4 PCBs due to the higher temperature resistance of the materials. Special care must be taken during rework or repair processes to avoid damaging the PCB or its components. It is important to follow the manufacturer’s guidelines and use appropriate tools and techniques when attempting to rework or repair High-Tg PCBs. In some cases, it may be more cost-effective to replace the entire board rather than attempting a repair.
Leave a Reply