Introduction to IC Packages
Integrated Circuit (IC) packages are protective casings that contain semiconductor devices like microprocessors, memories, transceivers, etc. The IC package provides an electrical interface between the internal delicate components and the external system via pins or pads. It also offers mechanical support, protects the chip from the environment, and enables heat dissipation.
Some of the most common types of surface mount IC packages used today include:
– Ball Grid Array (BGA)
– Quad Flat No-Lead (QFN)
– Land Grid Array (LGA)
While these packages serve similar purposes, they have distinct characteristics that make them suitable for different applications. Understanding the differences between BGA, QFN, and LGA packages is crucial for electronics designers and manufacturers when selecting the appropriate package for their products.
Ball Grid Array (BGA) Packages
What is a BGA Package?
A Ball Grid Array (BGA) is a surface-mount package that uses an array of solder balls underneath the package to provide electrical connections to the PCB. The solder balls are arranged in a grid pattern, allowing for a high density of interconnects in a small footprint.
BGA Package Construction
BGA packages consist of the following main components:
1. Substrate: A laminated material, usually made of BT (Bismaleimide Triazine) or FR-4, that provides a platform for mounting the die and routing the electrical connections.
2. Die: The semiconductor chip that contains the integrated circuit.
3. Wire Bonds: Thin gold or copper wires that connect the die to the substrate.
4. Encapsulant: A protective material, typically epoxy resin, that covers the die and wire bonds.
5. Solder Balls: Spherical balls of solder alloy that are attached to the bottom of the substrate, providing electrical connections to the PCB.
Advantages of BGA Packages
- High interconnect density due to the grid array of solder balls
- Excellent electrical and thermal performance
- Reduced package size compared to peripheral-pin packages
- Improved signal integrity and reduced inductance
- Suitable for high-speed and high-frequency applications
Disadvantages of BGA Packages
- Difficult to inspect solder joints visually
- Requires specialized equipment for assembly and rework
- Limited ability to probe individual connections for testing
- Thermal mismatch between package and PCB can cause reliability issues
Applications of BGA Packages
BGA packages are widely used in various applications, including:
– High-performance processors (CPUs, GPUs, etc.)
– Memory devices (DRAM, FLASH, etc.)
– Field-Programmable Gate Arrays (FPGAs)
– Application-Specific Integrated Circuits (ASICs)
– Chipsets and controllers
Quad Flat No-Lead (QFN) Packages
What is a QFN Package?
A Quad Flat No-Lead (QFN) package is a surface-mount package with a leadless design. It has a square or rectangular body with exposed pads on the bottom surface for electrical connections. QFN packages are known for their small size, low profile, and good thermal performance.
QFN Package Construction
QFN packages consist of the following main components:
1. Lead Frame: A metal frame, usually made of copper alloy, that supports the die and provides electrical connections.
2. Die: The semiconductor chip that contains the integrated circuit.
3. Wire Bonds: Thin gold or copper wires that connect the die to the lead frame.
4. Encapsulant: A protective material, typically epoxy resin, that covers the die and wire bonds.
5. Exposed Pad: A large metal pad on the bottom of the package that is exposed for better thermal dissipation and electrical grounding.
Advantages of QFN Packages
- Small package size and low profile
- Good thermal performance due to the exposed pad
- Reduced lead inductance and improved electrical performance
- Lower cost compared to BGA packages
- Easier visual inspection of solder joints compared to BGA
Disadvantages of QFN Packages
- Limited number of I/O connections compared to BGA
- Requires precise PCB Land Pattern Design and assembly
- Potential for thermal mismatch between package and PCB
- Difficult to rework or replace individual packages
Applications of QFN Packages
QFN packages are commonly used in applications that require small size, low cost, and good thermal performance, such as:
– Power management ICs
– RF and wireless communication devices
– Sensors and MEMS
– Automotive electronics
– Consumer electronics
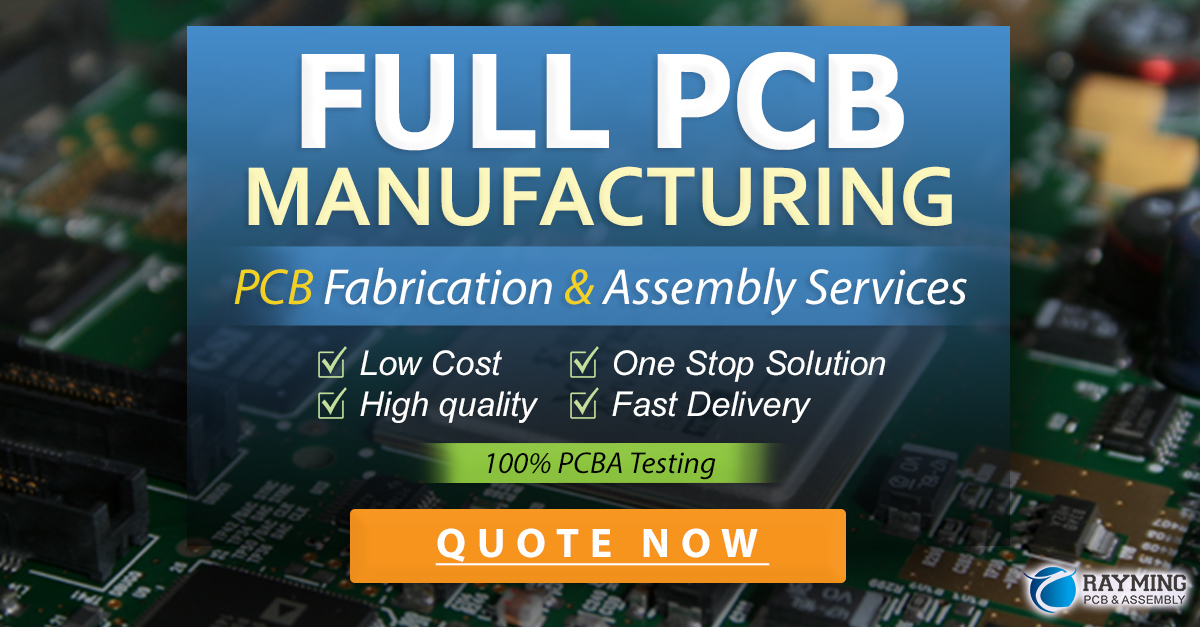
Land Grid Array (LGA) Packages
What is an LGA Package?
A Land Grid Array (LGA) package is a surface-mount package that uses a grid of exposed metal pads on the bottom surface for electrical connections. Unlike BGA packages, LGA packages do not have solder balls attached to the pads. Instead, the pads are directly soldered to the PCB.
LGA Package Construction
LGA packages consist of the following main components:
1. Substrate: A laminated material, usually made of BT or FR-4, that provides a platform for mounting the die and routing the electrical connections.
2. Die: The semiconductor chip that contains the integrated circuit.
3. Wire Bonds: Thin gold or copper wires that connect the die to the substrate.
4. Encapsulant: A protective material, typically epoxy resin, that covers the die and wire bonds.
5. Contact Pads: Exposed metal pads on the bottom of the substrate that provide electrical connections to the PCB.
Advantages of LGA Packages
- High interconnect density due to the grid array of contact pads
- Excellent electrical performance with low inductance
- Reduced package height compared to BGA packages
- Improved thermal performance due to direct contact between pads and PCB
- Lower cost compared to BGA packages
Disadvantages of LGA Packages
- Requires precise alignment between package and PCB during assembly
- Potential for solder joint reliability issues due to CTE mismatch
- Limited ability to inspect solder joints visually
- Difficult to rework or replace individual packages
Applications of LGA Packages
LGA packages are often used in applications that require high interconnect density, low profile, and good electrical performance, such as:
– Microprocessors and chipsets
– High-speed memory interfaces
– Network processors and ASICs
– Mobile and handheld devices
– High-performance computing systems
Comparison Table: BGA vs. QFN vs. LGA
Feature | BGA | QFN | LGA |
---|---|---|---|
Interconnect Type | Solder Balls | Exposed Pads | Contact Pads |
I/O Density | High | Medium | High |
Package Height | Medium | Low | Low |
Thermal Performance | Good | Very Good | Excellent |
Electrical Performance | Excellent | Good | Excellent |
Assembly Complexity | High | Medium | High |
Rework Difficulty | High | Medium | High |
Cost | High | Low | Medium |
Frequently Asked Questions (FAQ)
1. Which package type is best for my application?
The choice of package type depends on various factors such as the required I/O count, thermal performance, electrical performance, package size constraints, and cost. Consider the specific requirements of your application and consult with package and PCB design experts to determine the most suitable package type.
2. Can I replace a BGA package with a QFN or LGA package?
In most cases, directly replacing a BGA package with a QFN or LGA package is not possible due to differences in package dimensions, pin assignments, and PCB layout requirements. A redesign of the PCB and potentially the system would be necessary to accommodate a different package type.
3. How do I ensure reliable solder joints for BGA, QFN, and LGA packages?
To ensure reliable solder joints, consider the following:
– Follow the manufacturer’s guidelines for PCB land pattern design and package soldering profiles.
– Use appropriate solder paste and stencil thickness for the specific package type.
– Implement proper PCB surface finish and solder mask design.
– Control the assembly process parameters, such as reflow temperature profile, to minimize thermal stress.
– Perform post-assembly inspection using X-ray or other suitable methods to detect solder joint defects.
4. What are the challenges in reworking BGA, QFN, and LGA packages?
Reworking these package types can be challenging due to the following reasons:
– Difficulty in accessing and heating individual solder joints without affecting adjacent components.
– Risk of damaging the package or PCB during the rework process.
– Potential for solder bridging or open connections after rework.
– Need for specialized rework equipment and skilled operators.
It is essential to follow established rework procedures and use appropriate tools to minimize the risks associated with reworking these package types.
5. How do I select the appropriate solder paste for my package type?
When selecting solder paste for BGA, QFN, or LGA packages, consider the following factors:
– Solder alloy composition (e.g., SAC305, SAC405) that matches the package and PCB finish.
– Solder paste particle size and distribution that is compatible with the package pitch and PCB land pattern.
– Solder paste rheology (e.g., viscosity, slump resistance) that ensures proper printing and reflow behavior.
– Flux activity level that provides adequate wetting and minimizes solder defects.
Consult with solder paste manufacturers and perform compatibility testing to determine the most suitable solder paste for your specific package type and assembly process.
Conclusion
Understanding the differences between BGA, QFN, and LGA packages is crucial for selecting the appropriate package type for your electronic products. Each package type has its unique advantages and disadvantages in terms of interconnect density, thermal performance, electrical performance, assembly complexity, and cost.
BGA packages offer high interconnect density and excellent electrical performance, making them suitable for high-speed and high-frequency applications. QFN packages provide a small form factor, good thermal performance, and lower cost, making them ideal for power management and wireless communication devices. LGA packages combine high interconnect density, low profile, and excellent electrical performance, making them suitable for microprocessors, high-speed memory interfaces, and mobile devices.
When choosing the package type for your application, consider the specific requirements, consult with package and PCB design experts, and follow best practices for assembly and rework to ensure reliable and high-quality electronic products.
Leave a Reply