Table of Contents
- CNC“>Introduction to CNC
- History of CNC
- Components of a CNC Machine
- Types of CNC Machines
- Advantages of CNC Machining
- Applications of CNC Technology
- CNC Programming
- CNC Software
- CNC Machining Process
- CNC Maintenance and Troubleshooting
- Future of CNC Technology
- Frequently Asked Questions (FAQ)
- Conclusion
Introduction to CNC
CNC is a computer-controlled manufacturing process that utilizes pre-programmed software to dictate the movement of factory machinery and tools. This technology enables the automation of 3D cutting tasks, reducing the need for manual input and increasing production efficiency. CNC machines can perform a wide range of operations, including drilling, milling, turning, and grinding, with unparalleled accuracy and consistency.
History of CNC
The history of CNC dates back to the 1940s when the first numerically controlled (NC) machines were developed. These early machines utilized punched tape to store and execute machining instructions. In the 1960s, computer technology advanced, leading to the development of CNC machines. The first CNC machine, the Cincinnati Milacron Hydrotel, was introduced in 1952. Since then, CNC technology has continued to evolve, incorporating more advanced features and capabilities.
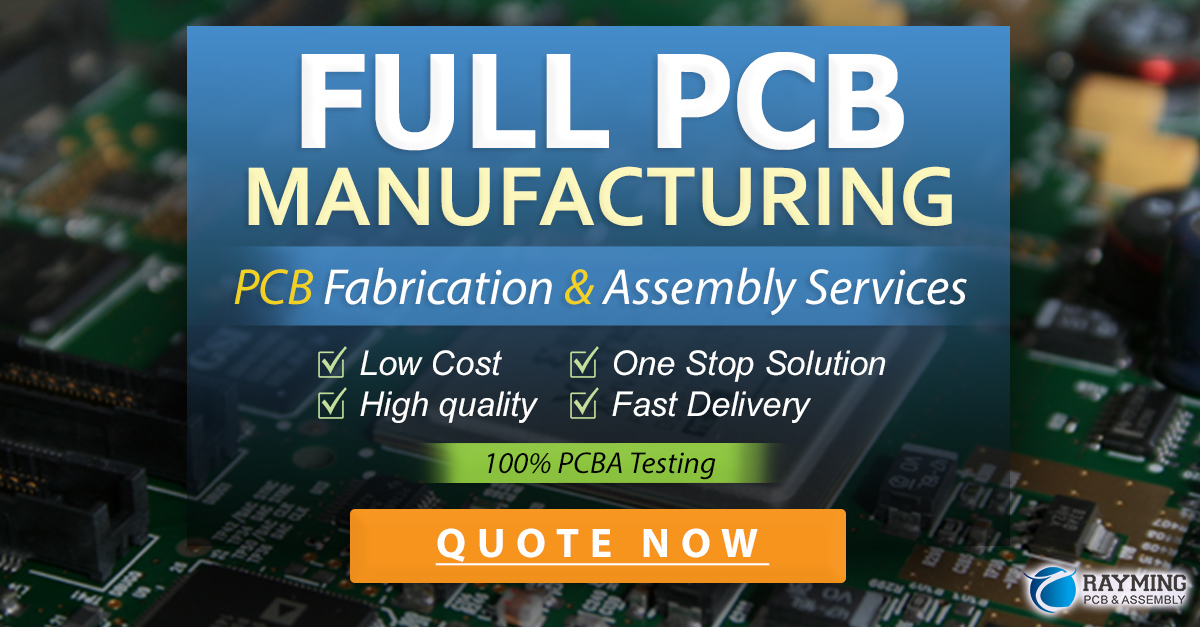
Components of a CNC Machine
A typical CNC machine consists of several key components that work together to perform precise machining operations. These components include:
-
Control System: The control system is the brain of the CNC machine. It consists of a computer that runs the CNC software, interprets the G-code, and sends commands to the machine’s motors and other components.
-
Machine Bed: The machine bed is the foundation of the CNC machine. It provides a stable and rigid platform for the workpiece and the cutting tools.
-
Spindle: The spindle is the rotating axis of the CNC machine that holds the cutting tool. It is responsible for providing the cutting force and speed necessary for machining operations.
-
Axes: CNC machines typically have three or more axes of motion, denoted as X, Y, and Z. These axes allow the cutting tool to move in different directions and angles relative to the workpiece.
-
Motors: CNC machines use servo or stepper motors to control the movement of the axes and the spindle. These motors provide precise and accurate motion control.
-
Cutting Tools: CNC machines utilize a variety of cutting tools, such as end mills, drill bits, and turning tools, to perform machining operations on the workpiece.
-
Coolant System: Many CNC machines incorporate a coolant system to lubricate and cool the cutting tools during machining operations. This helps to extend tool life and improve surface finish.
Types of CNC Machines
There are several types of CNC machines, each designed for specific machining operations and applications. Some of the most common types include:
-
CNC Mills: CNC mills are used for milling operations, which involve using rotary cutters to remove material from a workpiece. They can perform a wide range of operations, including face milling, profile milling, and drilling.
-
CNC Lathes: CNC lathes are used for turning operations, which involve rotating the workpiece while a cutting tool removes material from its surface. They are commonly used for producing cylindrical parts, such as shafts and bushings.
-
CNC Routers: CNC routers are used for cutting and shaping various materials, such as wood, plastics, and composites. They are often used in the woodworking and sign-making industries.
-
CNC Plasma Cutters: CNC plasma cutters use a high-velocity jet of ionized gas to cut through electrically conductive materials, such as metals. They are commonly used in the metal fabrication industry.
-
CNC Laser Cutters: CNC laser cutters use a high-powered laser beam to cut and engrave various materials, such as wood, acrylic, and metal. They are often used for precision cutting and engraving applications.
Type of CNC Machine | Primary Function | Common Applications |
---|---|---|
CNC Mill | Milling | Aerospace, automotive, medical devices |
CNC Lathe | Turning | Shafts, bushings, cylindrical parts |
CNC Router | Cutting/Shaping | Woodworking, sign-making |
CNC Plasma Cutter | Cutting | Metal fabrication |
CNC Laser Cutter | Cutting/Engraving | Precision cutting, engraving |
Advantages of CNC Machining
CNC machining offers several advantages over traditional manual machining methods. These advantages include:
-
Increased Productivity: CNC machines can operate continuously, 24 hours a day, 7 days a week, without the need for breaks or shift changes. This leads to increased productivity and faster production times.
-
Improved Accuracy: CNC machines are programmed to follow precise instructions, resulting in high levels of accuracy and consistency. This is particularly important in industries where tight tolerances are required, such as aerospace and medical device manufacturing.
-
Reduced Labor Costs: CNC machines can perform complex machining operations with minimal human intervention, reducing the need for skilled labor and associated costs.
-
Enhanced Flexibility: CNC machines can be quickly reprogrammed to produce different parts or products, allowing for greater flexibility in manufacturing processes.
-
Reduced Waste: CNC machines optimize material usage and minimize waste, as they can be programmed to make precise cuts and avoid unnecessary material removal.
Applications of CNC Technology
CNC technology has a wide range of applications across various industries. Some of the most common applications include:
-
Aerospace: CNC machines are used to produce complex aircraft components, such as engine parts, landing gear, and structural components.
-
Automotive: CNC technology is extensively used in the automotive industry for manufacturing engine components, transmission parts, and body panels.
-
Medical Devices: CNC machines are used to produce high-precision medical devices, such as implants, surgical instruments, and prosthetics.
-
Electronics: CNC technology is used in the production of electronic components, such as printed circuit boards (PCBs) and enclosures.
-
Woodworking: CNC routers are widely used in the woodworking industry for cutting, drilling, and shaping various wood products, such as furniture, cabinetry, and musical instruments.
CNC Programming
CNC programming involves creating a set of instructions that tell the CNC machine how to perform a specific machining operation. These instructions are written in a programming language called G-code. G-code consists of a series of commands that control the movement of the machine’s axes, spindle speed, and other parameters.
CNC programming can be done manually, using a text editor or specialized CNC programming software. However, many modern CNC machines are equipped with computer-aided manufacturing (CAM) software that can automatically generate G-code from 3D CAD models.
CNC Software
CNC software is an essential component of the CNC machining process. It includes both CAD (computer-aided design) and CAM (computer-aided manufacturing) software.
-
CAD Software: CAD software is used to create 3D models of the parts or products to be machined. Popular CAD software includes AutoCAD, SolidWorks, and Fusion 360.
-
CAM Software: CAM software takes the 3D CAD model and generates the G-code necessary for the CNC machine to perform the machining operations. Some popular CAM software include Mastercam, HSMWorks, and SprutCAM.
CNC Machining Process
The CNC machining process involves several steps, from design to final production. A typical CNC machining process includes the following stages:
-
Design: The part or product is designed using CAD software, creating a 3D model that specifies the geometry, dimensions, and tolerances.
-
CAM Programming: The 3D CAD model is imported into CAM software, where the machining operations and toolpaths are defined. The CAM software generates the G-code for the CNC machine.
-
Setup: The CNC machine is set up for the specific machining operation, including installing the appropriate cutting tools, fixturing the workpiece, and loading the G-code into the machine’s control system.
-
Machining: The CNC machine executes the G-code, performing the programmed machining operations on the workpiece. This may include milling, turning, drilling, or other operations.
-
Inspection: After machining, the finished part is inspected to ensure that it meets the required specifications and tolerances. This may involve using measuring instruments, such as calipers, micrometers, or coordinate measuring machines (CMMs).
-
Post-processing: Depending on the application, the machined part may require additional post-processing, such as surface finishing, heat treatment, or assembly.
CNC Maintenance and Troubleshooting
Regular maintenance and troubleshooting are essential for ensuring the optimal performance and longevity of CNC machines. Some key maintenance and troubleshooting tasks include:
-
Lubrication: Regular lubrication of the machine’s moving parts, such as bearings and ball screws, helps to reduce friction and wear.
-
Coolant Management: Monitoring and maintaining the coolant system, including regular cleaning and replacement of coolant, helps to ensure effective cooling and lubrication during machining operations.
-
Tool Management: Regularly inspecting and replacing worn or damaged cutting tools helps to maintain machining accuracy and prevent tool breakage.
-
Calibration: Periodically calibrating the machine’s axes and spindle ensures that the machine maintains its accuracy and precision over time.
-
Error Diagnostics: When errors or issues arise, it is important to diagnose the problem using the machine’s error codes and troubleshooting guides. Common issues may include tool breakage, programming errors, or machine component failures.
Future of CNC Technology
The future of CNC technology is promising, with ongoing advancements in automation, robotics, and artificial intelligence. Some of the trends and developments shaping the future of CNC include:
-
Industry 4.0: The integration of CNC machines with the Internet of Things (IoT), big data analytics, and cloud computing is enabling more connected, intelligent, and adaptive manufacturing systems.
-
Additive Manufacturing: The combination of CNC machining with additive manufacturing technologies, such as 3D printing, is opening up new possibilities for hybrid manufacturing and the production of complex geometries.
-
Robotic Integration: The integration of CNC machines with industrial robots is enabling more flexible and automated manufacturing processes, such as robotic part loading and unloading.
-
AI and Machine Learning: The application of artificial intelligence and machine learning algorithms to CNC machining is enabling predictive maintenance, process optimization, and autonomous decision-making.
Frequently Asked Questions (FAQ)
-
What is the difference between CNC and traditional machining?
CNC machining is a computer-controlled process that automates the movement of machine tools based on pre-programmed instructions. Traditional machining, on the other hand, relies on manual control and the skill of the machine operator. -
What materials can be machined using CNC technology?
CNC machines can process a wide range of materials, including metals (such as aluminum, steel, and titanium), plastics, composites, and wood. -
How long does it take to program a CNC machine?
The time required to program a CNC machine varies depending on the complexity of the part and the experience of the programmer. Simple parts may take a few hours to program, while more complex parts can take several days. -
What is the accuracy of CNC machining?
CNC machines are capable of achieving very high levels of accuracy, with tolerances as tight as ±0.001 inches (±0.025 mm) or better, depending on the machine and the application. -
How much does a CNC machine cost?
The cost of a CNC machine varies widely depending on the type, size, and capabilities of the machine. Entry-level CNC machines can cost around $10,000, while high-end, industrial-grade machines can cost several hundred thousand dollars or more.
Conclusion
CNC technology has revolutionized the manufacturing industry, enabling the precise and efficient production of a wide range of products. From its origins in the 1940s to its current state-of-the-art applications, CNC machining has continually evolved to meet the demands of modern manufacturing.
With its ability to automate complex machining tasks, improve accuracy, and reduce labor costs, CNC technology has become an essential tool for industries ranging from aerospace and automotive to medical devices and electronics. As the technology continues to advance, incorporating developments in automation, robotics, and artificial intelligence, the future of CNC machining looks brighter than ever.
By understanding the fundamentals of CNC technology, including its components, programming, and applications, manufacturers can harness the power of this innovative technology to streamline their operations, improve product quality, and stay competitive in an ever-evolving market.
Leave a Reply