Why is an Extra Press Cycle Necessary?
There are several reasons why manufacturers may choose to incorporate an extra press cycle into their production process:
1. Achieving Tighter Tolerances
In some cases, a single press cycle may not be sufficient to achieve the required dimensional accuracy or tolerances. By applying an extra press cycle, manufacturers can ensure that the component meets the desired specifications, reducing the likelihood of product rejections or failures.
2. Improving Surface Finish
An extra press cycle can help improve the surface finish of a component by smoothing out any irregularities or imperfections that may have occurred during the initial pressing. This is particularly important for parts that require a high-quality appearance or need to meet specific aesthetic standards.
3. Correcting Defects
If a component exhibits any defects after the initial press cycle, such as warping, cracking, or incomplete forming, an extra press cycle can be used to correct these issues. By re-pressing the part, manufacturers can salvage components that would otherwise be discarded, reducing waste and improving overall production efficiency.
The Extra Press Cycle Process
The extra press cycle process typically involves the following steps:
-
Inspection: After the initial press cycle, components are inspected for any defects, dimensional inaccuracies, or surface imperfections. This step helps determine whether an extra press cycle is necessary.
-
Re-pressing: If an extra press cycle is deemed necessary, the component is placed back into the press tool and subjected to another round of pressing. The press parameters, such as pressure, temperature, and dwell time, may be adjusted to achieve the desired results.
-
Post-press Operations: Following the extra press cycle, the component may undergo additional post-press operations, such as trimming, punching, or cleaning, to remove any excess material or prepare the part for the next stage of the manufacturing process.
-
Final Inspection: After completing the extra press cycle and any post-press operations, the component undergoes a final inspection to ensure that it meets the required specifications and quality standards.
Advantages of an Extra Press Cycle
Implementing an extra press cycle offers several advantages to manufacturers:
-
Improved Product Quality: By achieving tighter tolerances, better surface finishes, and correcting defects, an extra press cycle contributes to the overall improvement of product quality, leading to higher customer satisfaction and fewer warranty claims.
-
Reduced Waste: An extra press cycle allows manufacturers to salvage components that may otherwise be discarded due to defects or non-conformance, reducing material waste and associated costs.
-
Enhanced Production Efficiency: By minimizing product rejections and rework, an extra press cycle can help streamline the production process, resulting in improved efficiency and reduced cycle times.
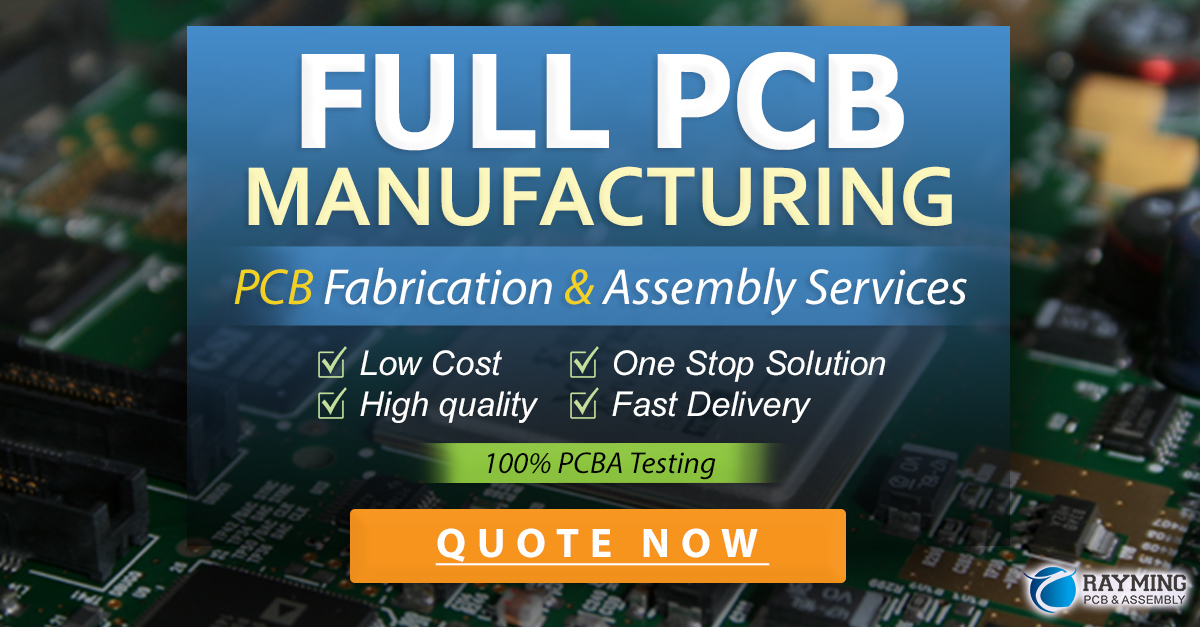
Challenges Associated with an Extra Press Cycle
While an extra press cycle offers numerous benefits, there are also some challenges that manufacturers must consider:
-
Increased Production Time: Adding an extra press cycle to the manufacturing process inevitably increases the overall production time per component. This can impact production schedules and throughput, particularly in high-volume manufacturing environments.
-
Additional Tooling Wear: Subjecting press tools to an extra press cycle can lead to increased wear and tear, potentially reducing tool life and increasing maintenance requirements.
-
Higher Energy Consumption: An extra press cycle consumes additional energy, which can contribute to higher production costs and environmental impact.
Optimizing the Extra Press Cycle
To mitigate the challenges associated with an extra press cycle and maximize its benefits, manufacturers can employ several strategies:
-
Process Simulation: By using advanced simulation tools, manufacturers can optimize press parameters and predict the outcome of an extra press cycle before physically running the process. This helps minimize trial and error, reducing development time and costs.
-
Tool Design Optimization: Designing press tools with the extra press cycle in mind can help minimize tooling wear and improve overall process efficiency. This may involve incorporating harder, more wear-resistant materials or optimizing tool geometry to reduce stress concentrations.
-
Automation: Implementing automated handling systems and press controls can help streamline the extra press cycle process, reducing manual intervention and minimizing the risk of errors or inconsistencies.
Real-World Applications
Extra press cycles are employed in various industries to manufacture a wide range of products. Some examples include:
Automotive Industry
In the automotive industry, extra press cycles are commonly used to produce body panels, structural components, and interior trim parts. For instance, a car door inner panel may undergo an extra press cycle to achieve the required dimensional accuracy and surface finish, ensuring proper fit and appearance.
Aerospace Industry
The aerospace industry relies on extra press cycles to manufacture high-precision components, such as turbine blades, compressor discs, and structural parts. These components often require tight tolerances and exceptional surface finishes to meet the stringent performance and safety standards of the industry.
Consumer Goods
Extra press cycles are also used in the production of consumer goods, such as household appliances, electronic devices, and sporting equipment. For example, a stainless steel kitchen sink may undergo an extra press cycle to achieve a uniform surface finish and eliminate any imperfections, enhancing its aesthetic appeal and durability.
The Future of Extra Press Cycles
As manufacturing technologies continue to advance, the role of extra press cycles in the production process is likely to evolve. Some potential developments include:
-
Additive Manufacturing Integration: The integration of additive manufacturing techniques, such as 3D printing, with traditional pressing processes may enable the production of more complex geometries and reduce the need for extra press cycles in certain applications.
-
Smart Press Tools: The development of smart press tools equipped with sensors and data analytics capabilities could help optimize the extra press cycle process in real-time, minimizing the need for manual adjustments and improving overall efficiency.
-
Alternative Materials: The adoption of new, advanced materials with improved formability and dimensional stability may reduce the need for extra press cycles in some applications, leading to faster production times and reduced energy consumption.
Frequently Asked Questions (FAQ)
-
Q: How does an extra press cycle differ from a standard press cycle?
A: An extra press cycle is an additional pressing operation performed after the initial press cycle to achieve desired specifications, improve surface finish, or correct defects. In contrast, a standard press cycle refers to the initial pressing operation used to form the component. -
Q: Is an extra press cycle always necessary?
A: No, an extra press cycle is not always necessary. It is typically employed when the initial press cycle fails to achieve the required dimensional accuracy, surface finish, or when defects are present in the component. -
Q: Can an extra press cycle be automated?
A: Yes, an extra press cycle can be automated using advanced handling systems and press controls. Automation helps streamline the process, reduce manual intervention, and minimize the risk of errors or inconsistencies. -
Q: How does an extra press cycle impact production time and costs?
A: An extra press cycle increases the overall production time per component, which can impact production schedules and throughput. Additionally, it consumes more energy and may lead to increased tooling wear, potentially contributing to higher production costs. -
Q: Are extra press cycles used in industries other than automotive, aerospace, and consumer goods?
A: Yes, extra press cycles can be employed in various other industries, such as medical device manufacturing, electrical equipment production, and metal packaging, wherever there is a need to achieve tight tolerances, superior surface finishes, or correct defects in pressed components.
In conclusion, an extra press cycle is a valuable tool for manufacturers looking to improve product quality, reduce waste, and enhance production efficiency. By understanding the process, its advantages, and the challenges associated with it, manufacturers can make informed decisions about incorporating extra press cycles into their production processes. As manufacturing technologies continue to evolve, the role of extra press cycles may adapt, but their importance in achieving high-quality, precise components is likely to remain significant.
Leave a Reply