Introduction
In the world of electronics manufacturing, ensuring the proper functionality and reliability of printed circuit boards (PCBs) is crucial. PCBs are the backbone of countless electronic devices, and their performance can significantly impact the overall quality and success of a product. To thoroughly test and validate PCBs, manufacturers rely on specialized equipment known as PCB test fixtures. These fixtures play a vital role in the testing process, enabling comprehensive evaluation and verification of PCB designs before they are integrated into final products.
Definition of a PCB Test Fixture
A PCB test fixture is a specialized mechanical and electrical interface designed to hold and connect a PCB securely while enabling various tests and measurements. It serves as a bridge between the PCB and the test equipment, providing a controlled environment for accurate and repeatable testing. PCB test fixtures are essential tools in the manufacturing process, ensuring that each PCB meets the required specifications and performs as intended.
Purpose and Importance of PCB Test Fixtures
PCB test fixtures serve several crucial purposes in the electronics manufacturing process:
- Functional Testing: PCB test fixtures allow for the thorough testing of a PCB’s functionality by providing access to all necessary test points and interfaces. This includes verifying the correct operation of individual components, circuits, and interconnections.
- Electrical Testing: Test fixtures enable various electrical tests, such as continuity testing, insulation resistance testing, and high-potential testing, to ensure the integrity of the PCB’s electrical connections and isolation.
- Signal Integrity Testing: For high-speed and high-frequency applications, PCB test fixtures facilitate signal integrity testing, including measurements of signal quality, crosstalk, and electromagnetic compatibility (EMC).
- Environmental Testing: Some PCB test fixtures are designed to simulate various environmental conditions, such as temperature, humidity, or vibration, to evaluate the PCB’s performance and reliability under different operating conditions.
- Quality Control: By providing a consistent and controlled testing environment, PCB test fixtures contribute to effective quality control measures, helping to identify and eliminate defective PCBs before they are assembled into final products.
- Cost Savings: Thorough testing and verification of PCBs using test fixtures can help prevent costly product failures and recalls, ultimately saving manufacturers significant financial resources.
The importance of PCB test fixtures cannot be overstated, as they play a crucial role in ensuring the reliability, performance, and quality of electronic products.
Types of PCB Test Fixtures
PCB test fixtures come in various types and configurations, each designed to meet specific testing requirements and accommodate different PCB form factors and complexities. Here are some common types of PCB test fixtures:
- Bed-of-Nails Fixtures: Also known as “nail beds,” these fixtures feature an array of spring-loaded pins or “nails” that make electrical contact with the test points on the PCB. Bed-of-nails fixtures are widely used for functional testing and are suitable for various PCB designs.
- Vacuum Fixtures: These fixtures use vacuum suction to securely hold the PCB in place during testing. Vacuum fixtures are often used for testing flexible or irregularly shaped PCBs, as well as for high-frequency and high-speed applications where precise positioning is critical.
- Electromagnetic Compatibility (EMC) Fixtures: EMC fixtures are designed to test a PCB’s compliance with electromagnetic compatibility standards. They typically feature shielding enclosures and specialized interfaces for measuring and analyzing electromagnetic emissions and susceptibility.
- Environmental Fixtures: These fixtures are designed to subject PCBs to various environmental conditions, such as temperature cycling, humidity, vibration, or altitude simulation. They are used to evaluate the PCB’s performance and reliability under extreme or specific operating conditions.
- Customized Fixtures: For unique or complex PCB designs, manufacturers may require customized test fixtures tailored to their specific requirements. These fixtures are designed and manufactured to accommodate the specific form factor, test points, and testing needs of the PCB.
The choice of PCB test fixture type depends on factors such as the PCB design, testing requirements, production volumes, and available resources.
Design Considerations for PCB Test Fixtures
Designing an effective and reliable PCB test fixture requires careful consideration of various factors to ensure accurate and repeatable testing results. Here are some key design considerations:
- PCB Interface: The fixture should provide a secure and stable interface for the PCB, minimizing the risk of misalignment or movement during testing. This may involve the use of precisely machined housing, alignment pins, or clamping mechanisms.
- Test Point Access: The fixture must provide easy access to all necessary test points on the PCB, including surface-mounted components, through-hole components, and edge connectors. This may require the use of customized pin configurations or probe adapters.
- Signal Integrity: For high-speed and high-frequency applications, the fixture design should minimize signal distortion, crosstalk, and parasitic effects. This may involve the use of specialized materials, shielding, and controlled impedance paths.
- Thermal Management: Depending on the testing requirements, the fixture may need to incorporate thermal management features, such as heating or cooling elements, to maintain the PCB at specific temperature ranges during testing.
- Ease of Use: The fixture should be designed with user-friendliness in mind, allowing for easy loading and unloading of PCBs, as well as clear visual indicators and intuitive controls.
- Scalability and Modularity: For high-volume production or diverse product lines, the fixture design should consider scalability and modularity, allowing for easy reconfiguration or adaptation to different PCB variants.
- Maintenance and Serviceability: PCB test fixtures are subject to wear and tear, especially in high-volume production environments. The design should consider ease of maintenance, repair, and replacement of critical components, such as spring-loaded pins or vacuum seals.
- Safety and Compliance: The fixture design must comply with relevant safety standards and regulations, including electrical safety, mechanical safety, and environmental considerations.
Collaboration between PCB designers, test engineers, and fixture manufacturers is crucial to ensure that the PCB test fixture meets all necessary requirements and provides reliable and accurate testing results.
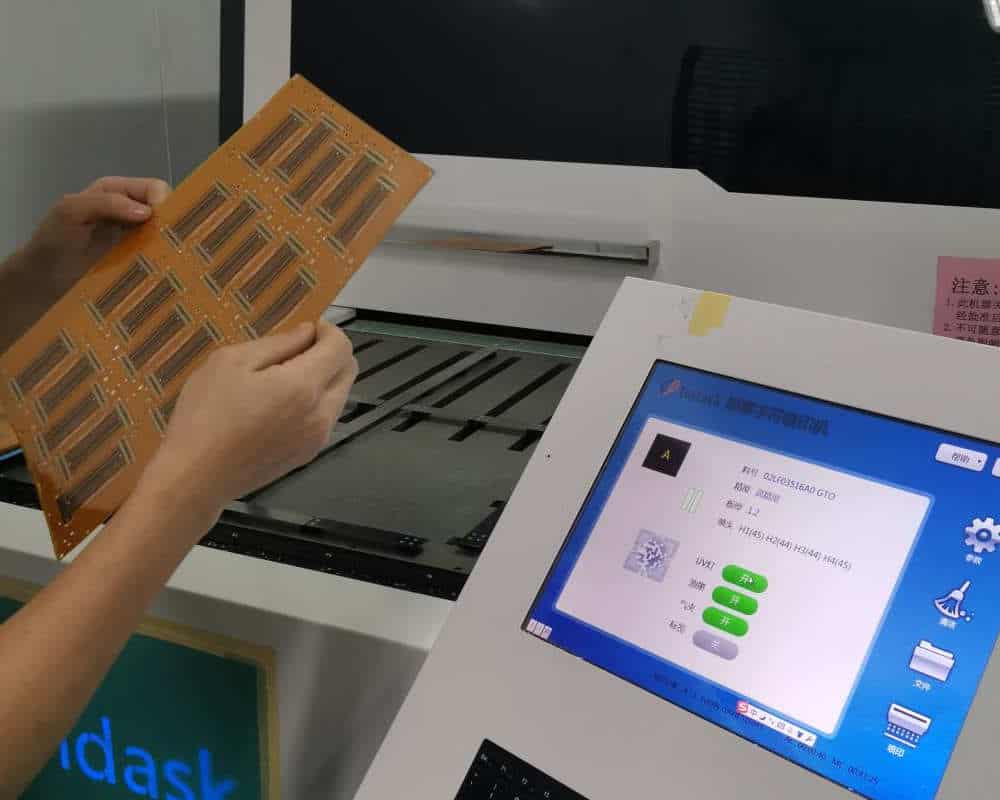
PCB Test Fixture Manufacturing Process
The manufacturing process for PCB test fixtures typically involves several stages, each contributing to the overall quality and performance of the fixture. Here is a general overview of the PCB test fixture manufacturing process:
- Design and Simulation: The process begins with the design phase, where the PCB layout, test requirements, and fixture specifications are analyzed. Computer-aided design (CAD) tools and simulation software may be used to optimize the fixture design and validate its performance before physical manufacturing.
- Material Selection: Based on the design requirements, appropriate materials are selected for the fixture components. Common materials used include plastics, metals, and specialized conductive materials for electrical interfaces.
- Fabrication: The fixture components are fabricated using various manufacturing techniques, such as computer numerical control (CNC) machining, 3D printing, injection molding, or metal forming processes. Precision and accuracy are critical during this stage to ensure proper alignment and fit.
- Assembly and Integration: The fabricated components are assembled and integrated into the final fixture assembly. This may involve mechanical assembly, electrical wiring, and the installation of specialized components like spring-loaded pins, vacuum seals, or thermal management elements.
- Testing and Calibration: Once assembled, the PCB test fixture undergoes rigorous testing and calibration processes to ensure its functionality, accuracy, and compliance with specifications. This may involve electrical testing, mechanical testing, and environmental simulations.
- Documentation and Quality Control: Comprehensive documentation, including assembly instructions, test procedures, and calibration records, is created for the PCB test fixture. Quality control measures are implemented to ensure consistency and traceability throughout the manufacturing process.
- Delivery and Installation: The completed PCB test fixture is then delivered to the customer’s facility, where it is installed and integrated into the testing infrastructure. On-site training and support may be provided to ensure proper usage and maintenance.
Throughout the manufacturing process, strict quality control measures and adherence to industry standards are crucial to ensure the reliability and accuracy of the PCB test fixtures.
Applications of PCB Test Fixtures
PCB test fixtures find applications across various industries and sectors, serving as essential tools for ensuring the quality and performance of electronic products. Here are some common applications of PCB test fixtures:
- Consumer Electronics: PCB test fixtures are widely used in the manufacturing of consumer electronics, such as smartphones, tablets, laptops, and home appliances, to verify the functionality and reliability of PCBs before final assembly.
- Automotive Electronics: The automotive industry relies heavily on PCB test fixtures to test and validate electronic control units (ECUs), sensors, and other critical automotive electronics components.
- Aerospace and Defense: In the aerospace and defense sectors, PCB test fixtures are essential for ensuring the reliability and performance of avionics, radar systems, and other mission-critical electronic systems.
- Telecommunications: Test fixtures play a crucial role in the manufacturing of telecommunication equipment, such as routers, switches, and base stations, enabling thorough testing of high-speed and high-frequency PCBs.
- Medical Devices: The medical device industry utilizes PCB test fixtures to verify the functionality and safety of electronic components in medical equipment, ensuring compliance with stringent regulations and standards.
- Industrial Automation: PCB test fixtures are used in the manufacturing of industrial automation systems, robotics, and control systems, where reliability and performance are critical for safe and efficient operation.
- Research and Development: In research and development environments, PCB test fixtures are employed for prototype testing, design validation, and experimentation with new electronic technologies and materials.
As electronics continue to permeate various aspects of our lives, the demand for reliable and high-quality PCBs will continue to grow, further emphasizing the importance of PCB test fixtures in the manufacturing process.
Frequently Asked Questions (FAQs)
- What is the difference between a PCB test fixture and a bed-of-nails fixture? A bed-of-nails fixture is a specific type of PCB test fixture that features an array of spring-loaded pins or “nails” that make electrical contact with the test points on the PCB. While all bed-of-nails fixtures are PCB test fixtures, not all PCB test fixtures are bed-of-nails fixtures.
- Why is signal integrity important in the design of PCB test fixtures? Signal integrity is crucial in the design of PCB test fixtures, especially for high-speed and high-frequency applications. Poor signal integrity can lead to signal distortion, crosstalk, and inaccurate test results, compromising the reliability and performance of the PCB under test.
- Can PCB test fixtures be used for environmental testing? Yes, there are specialized PCB test fixtures designed for environmental testing, such as temperature cycling, humidity testing, vibration testing, and altitude simulation. These fixtures provide a controlled environment to evaluate the PCB’s performance and reliability under various operating conditions.
- How often do PCB test fixtures need to be maintained or calibrated? The frequency of maintenance and calibration for PCB test fixtures depends on various factors, such as the fixture type, usage intensity, and the specific testing requirements. Generally, regular maintenance and calibration schedules are recommended to ensure accurate and repeatable testing results.
- Can PCB test fixtures be customized for specific PCB designs? Yes, customized PCB test fixtures can be designed and manufactured to accommodate unique or complex PCB designs. These fixtures are tailored to the specific form factor, test points, and testing requirements of the PCB, ensuring proper interfacing and reliable testing.
By understanding the critical role of PCB test fixtures in the electronics manufacturing process, manufacturers can ensure the quality, reliability, and performance of their products, ultimately delivering superior electronic devices to consumers.
Leave a Reply